Mines and batteries: a perfect match?
Finnish company Terrafame has received a permit from local authorities to build a battery chemicals plant at its Sotkamo mine. The benefits of integrating battery chemical production into a mine’s refining operations are obvious, but can it be done in a sustainable way? Molly Lempriere finds out
Scroll down to read the article
Sotkamo, in the north east of Finland, has given the go ahead for a building permit for state-owned Terrafame to build a battery chemical plant. It will form part of the nickel and zinc mine in the area, should the environmental impact assessment, which is currently underway, prove successful.
“We aim to increase the added value of our operations,” says Terrafame CEO Joni Lukkaroinen. “Our nickel-cobalt product is today partly sold to customers refining it to battery grade nickel and cobalt sulphate. The product properties are well suited for such refining process. We have seen that the market is developing very fast in the battery applications and we want to be one of the big companies offering solutions for battery application customers.”
However, the Sotkamo mine has a history of environmental damage under its previous owner Talvivaara Mining. Earlier this year, in the climax of a three-year lawsuit, the original director was prosecuted following extensive contamination of the nearby area.
The battery market is growing worldwide, and the development of such a large battery chemicals plant could give Finland a leg-up – but only if it can be done in a sustainable and environmentally sensitive way.
The benefits of an onsite battery plant
The battery chemical plant will add an extra level of processing to the metal refining already undertaken at the Sotkamo mine. This will allow Terrafame to produce battery-grade nickel sulphate and battery-grade cobalt sulphate, both intrinsic aspects of lithium-ion battery technologies.
The chemical plant has only recently become an economically viable possibility, as the market for batteries, and therefore demand, has grown. The International Energy Agency now predicts that there will be 70 million electric vehicles around the world by 2025. Additionally, the amount of nickel used in batteries is increasing; by 2020, 80% of NCA and NMC cathodes popular in batteries such as those used in Tesla cars will be made of nickel, compared with just 33.3% now.
This has created a huge market for battery chemicals, a key factor in Terrafame’s decision to pursue the process plant.
“The big challenge for our project is to predict the market development,” says Lukkaroinen. “This year our nickel production will be close to 30,000 tonnes, and we are planning to convert the whole production in the future into battery chemicals. This will make our plant the biggest nickel-sulphate production plant in the world when it's finished.
“In order for this to be sensible, we need the market to grow. We can see the need for nickel is going up and the share of nickel used in lithium-ion batteries is increasing, so I think we have all the reasons to believe the market is booming, but I do think it is critical for us to be successful.”
The International Energy Agency now predicts that there will be 70 million electric vehicles around the world by 2025
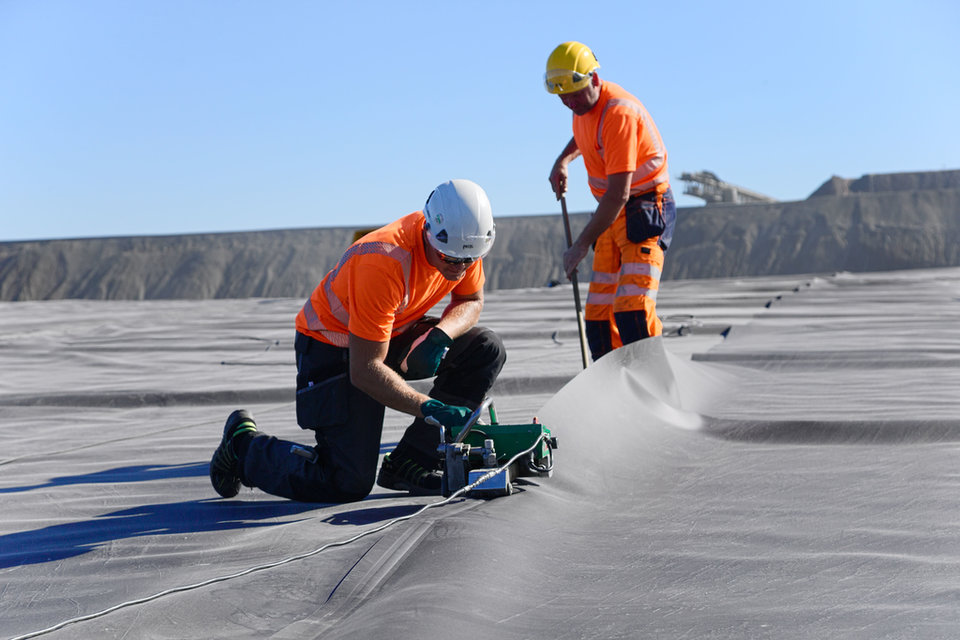
Construction of secondary leaching area.
Credit: Terrafame
By limiting transportation, the chemicals can be produced without the need for heavily polluting vehicles
Reducing emissions and limiting waste
Along with contributing to the battery revolution, building a battery chemical plant onsite should reduce carbon emissions.
“There are a few benefits, one of which is that there is of course less need for transporting the product. Instead of transporting it from our site to the refiner and then further to customers, we are planning to do the further processing ourselves,” says Lukkaroinen.
By limiting transportation, the chemicals can be produced without the need for heavily polluting vehicles.
Furthermore, it ensures that the cleanest possible techniques are used when producing nickel-sulphide and cobalt-sulphide. “Our current production here in Sotkamo is based on bioleaching technology,” Lukkaroinen continues. “In this technology [the] carbon footprint is very good compared with the traditional process for producing nickel. And when we are able to produce the nickel sulphate at the site in the same way, the carbon footprint will be clearly one of the best compared with any production unit globally making those products. We believe that, in particular for the battery chain, this is valuable.”
Onsite processing can also decrease the amount of waste at a plant, ensuring that all the possible elements are extracted and utilised.
“The other thing is then we can make the most of the by-products, the ‘impurities’, and sell them in the future like, for example, zinc and copper today,” he says.
Credit: Terrafame
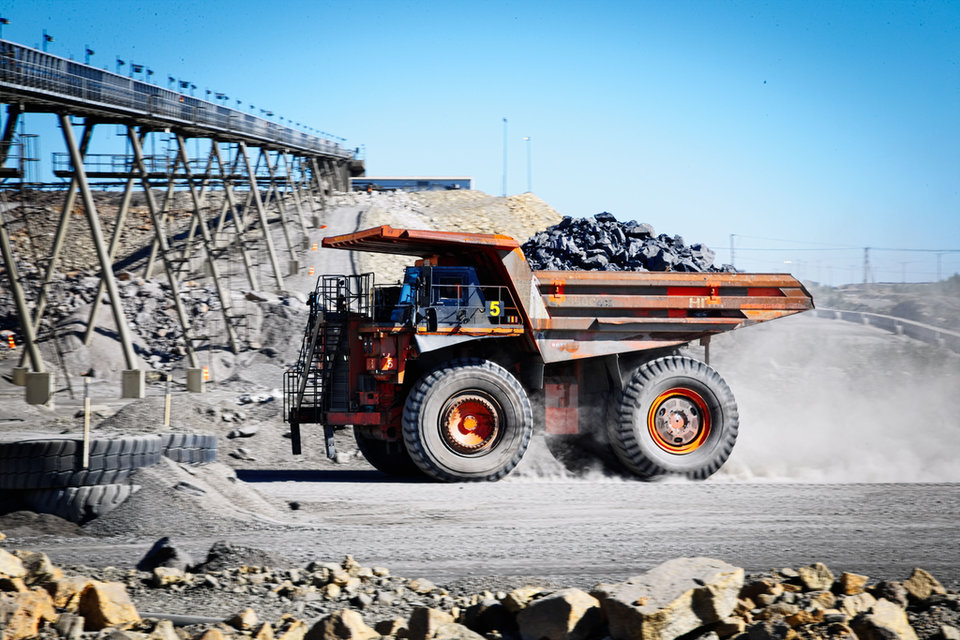
Keeping it environmental
The Sotkamo mine has a history of environmental oversight that could cause concerns. Talvivaara Mining, which owned the mine from 2008, mismanaged waste on the site. Waste reservoirs overfilled due to rainwater, and leaked in 2008, 2010, 2012 and 2013. This led to two nearby lakes becoming badly contaminated and turning into salt water, according to researchers from Helsinki University.
In March 2018, Pekka Perä, founder and original director of Talvivaara Mining, was sentenced to six months in prison on probation for severe environmental damage. Two further company executives were also fined in what is thought to be the most significant environmental lawsuit in Finland.
However, since Terrafame took over the plant in 2015, there have been no further environmental damages.
“We've been operating for three years, and during Terrafame's time there hasn't been any environmental deviations or any concerns,” reassures Lukkaroinen.
“We've worked to build a good safety culture at the site, we have been able to get rid of the excess water and we have taken into use reliable water purification systems among many other things. Thanks to this development work, we haven't had any environmental problems.”
The environmental impact assessment is hoped to be complete by the end of 2018, allowing Terrafame to apply for an environmental permit in 2019.
Going forward, environmental safety will remain a top priority for the site, ensuring that the battery revolution doesn’t leave a trail of damage.
“Of course, environmental safety is a key issue, and it's always analysed in detail when making any investment,” says Lukkaroinen.
Environmental safety will remain a top priority for the site, ensuring that the battery revolution doesn’t leave a trail of damage