Company Insight
Sponsored by CCG Cable Terminations
Ultraweld: The key to superior exothermic connections
Standfirst...
Main image credit:
When electrical conductivity, durability, and reliability are paramount, the quality of connections between conductors can make all the difference. Exothermic welding has long been recognised as a superior method for creating molecular-level bonds that ensure longevity and efficiency. CCG Cable Terminations exclusively imports Ultraweld Exothermic Earthing, providing an innovative approach to exothermic welding that makes the process more accessible and dependable.
Whether you work in grounding, lightning protection, cathodic protection, or rail applications, mastering the Ultraweld process is essential to achieving the best results. By following best practices in preparation, execution, and inspection, you can ensure high-quality connections that exceed mechanical or pressure-based alternatives.
Why Ultraweld?
Ultraweld utilises a time-tested chemical reaction to fuse conductors at a molecular level. The process involves reducing copper oxide with aluminium, generating extreme heat that melts copper and forms a bond stronger than the original conductors themselves.
Encapsulated in a graphite mould, this method ensures portability and cost-effectiveness without compromising performance.
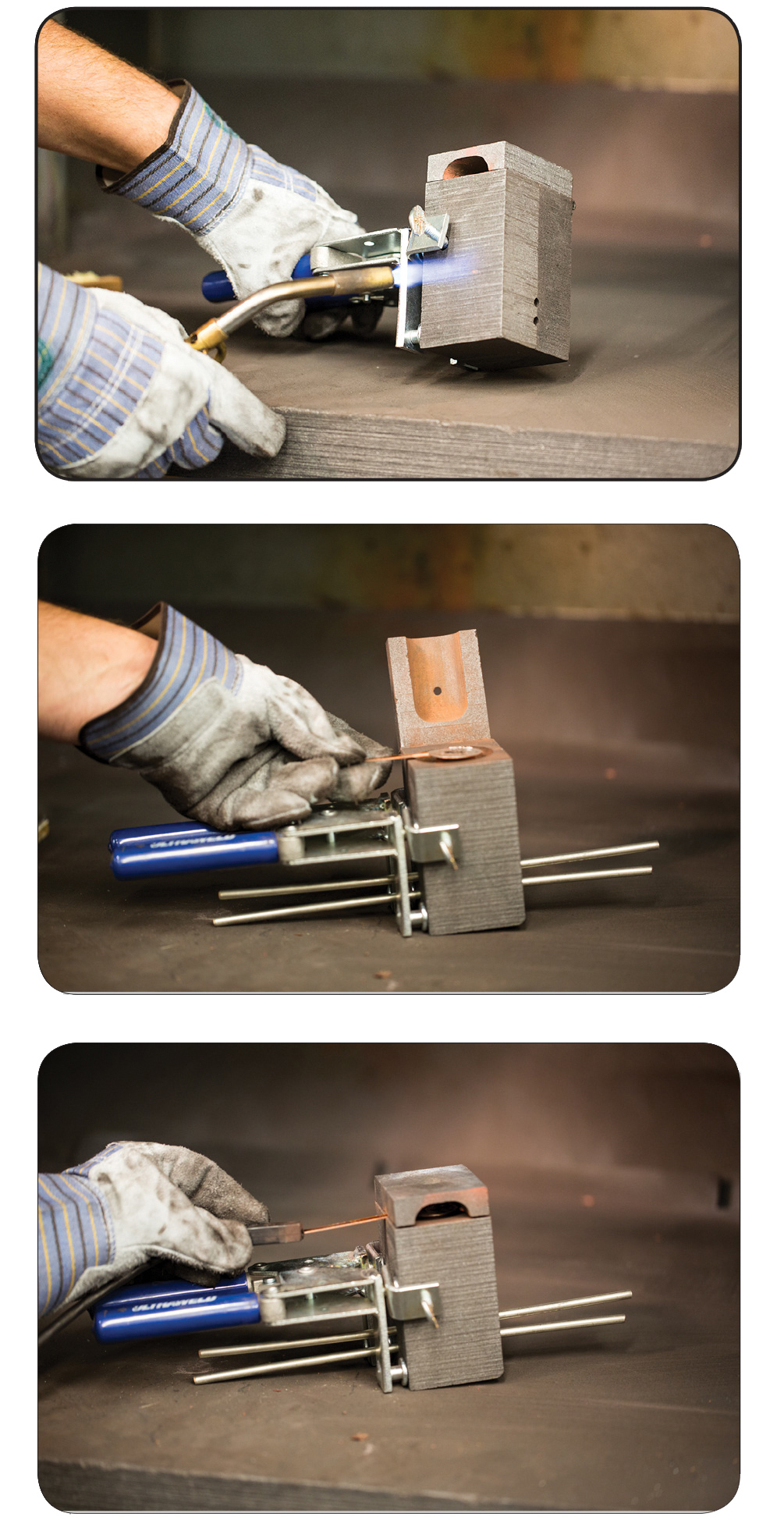
The advantages of Ultraweld connections include:
- Permanent, non-loosening bonds
- Current carrying capacity exceeding that of the conductors
- Resistance to corrosion and environmental degradation
- No increase in resistance over time
- Straightforward, low-cost materials with minimal training required
- Simple non-destructive inspection methods
Achieving high-quality ultraweld connections
As with any precision process, careful attention to detail ensures consistently high-quality results. Following these key preparation steps will optimise your Ultraweld connections:
1. Mould preparation:
- Before each use, dry the graphite mould with a torch to remove any moisture, ensuring a temperature above 104°C.
- Clean the mould using a natural bristle brush – avoid metal or plastic brushes that could damage its surface.
- Inspect the mould for wear, particularly around conductor openings and weld cavities.
2. Conductor preparation:
- Conductors must be clean and dry, with all oxidation and coatings removed down to bright metal.
- Ensure conductors fit snugly within the mould, preventing leakage of molten weld metal.
3. Positioning and handling:
- The mould must be kept stable in a vertical position during the weld, as the process is gravity-fed.
- Ensure handles close tightly and lock properly to maintain a sealed reaction chamber.
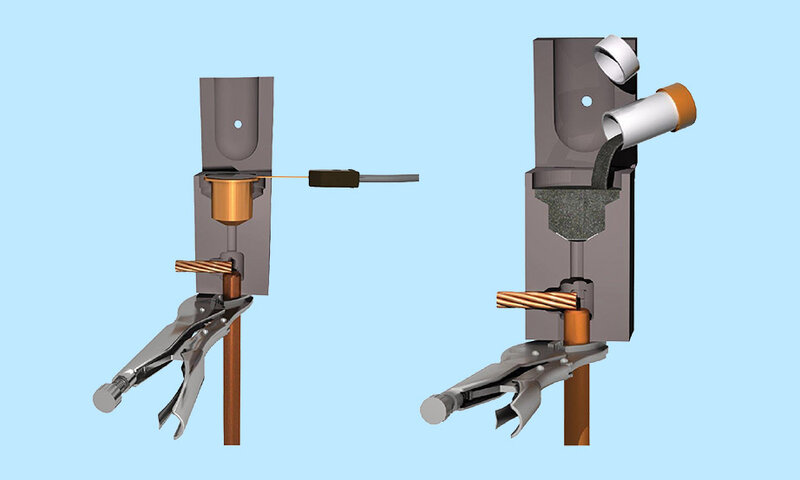
Ultraweld processes (NUWTube and UltraShot) use a graphite mould to facilitate an exothermic reaction, reducing copper oxide and producing molten copper for a durable, molecular-level electrical connection.
The Ultraweld process: UltraShot vs NUWTube
Ultraweld offers two primary connection methods, each with distinct advantages.
UltraShot®: Simple and efficient
The UltraShot system enhances traditional exothermic welding by encapsulating the weld metal in a cartridge, eliminating the need for manually handling powders. This modern approach increases efficiency, reduces waste, and prolongs the lifespan of the graphite mould.
Key Steps:
- Dry and clean the mould and conductors.
- Insert conductors and UltraShot cartridge into the mould.
- Close the lid and attach the DRONE cord to the UltraShot igniter.
- Simultaneously press and hold both igniter buttons.
- Open the mould, remove the connection, clear away slag, and clean the mould before the next weld.
NUWTube®: Traditional Pour-In Method
NUWTube follows a conventional exothermic welding approach, offering a flexible and cost-effective alternative.
Key Steps:
- Torch-dry the mould before the first connection.
- Clean and dry conductors, insert them into the mould, and secure the handle clamp.
- Place a protective disk inside the mould.
- Remove the clear plastic cap and pour NUWTube weld metal into the mould.
- Close the lid, remove the orange cap from the starting powder chamber, and sprinkle powder near the ignition hole.
- Ignite using a flint igniter.
- Once the reaction completes, remove the connection, clear slag, and clean the mould.
Inspection: Ensuring a perfect weld
Regular inspection is crucial to maintaining weld integrity. A well-made Ultraweld connection should feature:
- A solid weld body with a cross-section greater than the conductors.
- Complete sleeves for mechanical strength.
- Minimal slag contamination in the weld.
- A riser height above the highest conductor.
Signs of a poor weld and causes
Excess slag: May compromise electrical resistance; often caused by improper disk placement or a leaking mould.
- Underfilled weld: Weld body too low, affecting conductivity. This can result from using the wrong weld metal or a mould leak.
- Gas pockets or voids: Appear as a lighter weld colour with a high riser. Often caused by contaminants in the mould, conductors, or weld metal.
- Leaking weld: Typically, due to a worn or improperly closed mould.
For added assurance, a simple hammer test can identify weak connections – a well-made weld should withstand a controlled tap without dislodging.
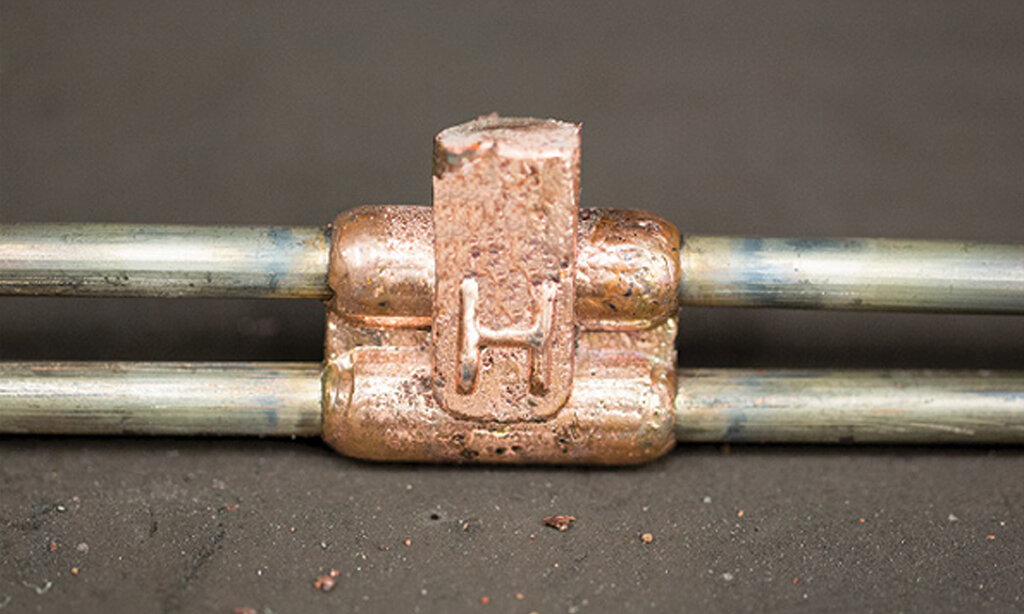
Caption. Credit:
Optimise your work with Ultraweld
Exothermic welding remains the gold standard for permanent electrical connections, and the Ultraweld system offers an efficient, reliable solution. By selecting the right method—whether the streamlined UltraShot or the traditional NUWTube—you can achieve superior electrical connections that stand the test of time.
For more information, contact CCG Cable Terminations, the exclusive importer of Ultraweld Exothermic Earthing.