INFRASTRUCTURE
Electricity infrastructure for mines of the future
In the Pilbara region, Western Australia, Rio Tinto is constructing what will be the most technologically advanced iron ore mine in its portfolio, and a new industry benchmark. Barry Menzies, managing director at M&I Materials, explains what this means for the mines of the future.
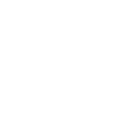
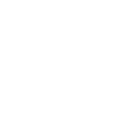
Along with a new 220kV transmission line and 39 transformers, Rio Tinto’s new site in Pilbara will also need 166km of railway, an airport, and a camp and road access to support its operation.
Koodaideri forms a flagship part of Rio Tinto’s Mine of the Future programme, using the latest in mining technology including autonomous trucks, trains and drills, digital twins and advanced data analytics. With significant levels of electrification, a new approach to transformer safety was required on site.
More than half of the country’s coal mines are managed by pro-Russian separatist militia.Credit: DmyTo/Shutterstock.
More than half of the country’s coal mines are managed by pro-Russian separatist militia.
Credit: DmyTo/Shutterstock.
The boardroom discussion
This is nothing short of a major milestone for mining. The past decade has seen record high and low mining commodity prices, and this has presented challenges across the industry in terms of securing and allocating for the capital upgrades that drive innovation. Yet digitalisation is increasingly a boardroom discussion across the minerals, metals and resources industry. The substantial safety, uptime and efficiency benefits that it can bestow are beginning to speak for themselves. And it may also be in part because the demand for rare earth minerals for mobile devices and electric vehicles grows year on year, creating something of a race to meet demand in the most efficient way.
Equally, the role for digitalisation has found a way into more unlikely conversations such as the discussion around onsite energy infrastructure, both for new mines and for existing mines that need to make critical investments in order to continue or expand production.
“Siemens Transmissions Products CEO Beatrix Natter offers that digitalisation will become a “mandatory element of the functionality customers expect” from products.”
Transformers, as an example, are no longer assets that simply step up or down voltage, thanks to digitalisation. Being able to access data via a cloud-based platform will provide mine operators with an unprecedented and real-time view of the assets supplying its site. This level of transparency and control helps operators to significantly reduce costly, unplanned downtime as well as increasing productivity, while minimising stress from overloading. While these types of technologies are still very much the purview of the ‘Mine of the Future’, Siemens Transmissions Products CEO Beatrix Natter offers that digitalisation will become a “mandatory element of the functionality customers expect” from products.
Yet, while innovation and digitalisation are increasingly used interchangeably, there is still bandwidth for analogue innovations, particularly in materials, to make an impact.
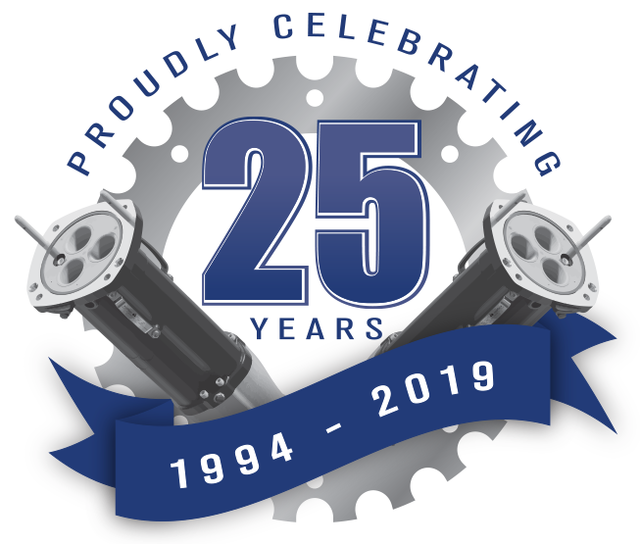
AusProof is celebrating 25 years of business in Australia in 2019.
The Pilbara 39
Delivering much of this new vision for mining will require a significant level of electrification, and a substantial amount of power onsite. Driven in part by the Mine of the Future’s guiding principles to reduce environmental impact and improve safety, Rio Tinto’s 39 newly constructed transformers at Pilbara will be inspiring examples of how small changes in materials can lead to industry-leading improvements that are widely applicable.
“Despite their remote locations, space on mining sites often comes at a premium.”
Providing power to mining operations offers up some unique challenges. Contrary to what you might think, despite their remote locations, space on mining sites often comes at a premium. In traditional setups, transformers needed to be built a minimum distance from neighbouring buildings and facilities and needed to be blast and fireproof. As you can imagine, a mine would be about the last place on earth you’d want to experience a fire, or an unintended blast.
In that respect, one simple innovation in transformer fluid has made all the difference.
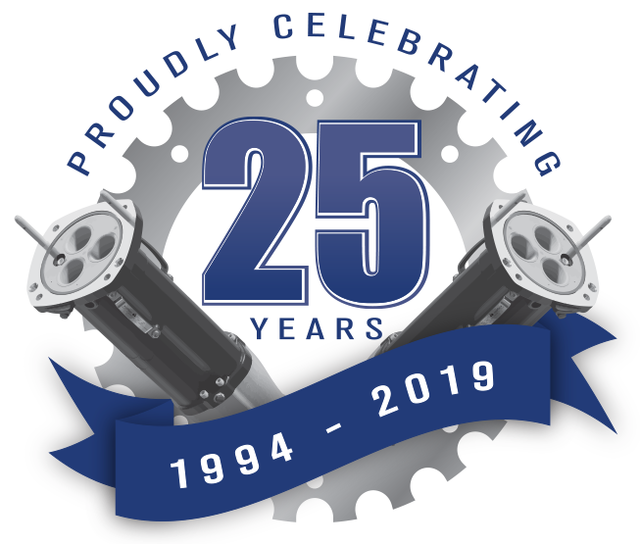
AusProof is celebrating 25 years of business in Australia in 2019.
Small changes, big improvements
Traditionally, transformers have been filled with a potentially flammable mineral oil as an insulator and to provide cooling. But should that mineral oil ignite, the resulting transformer fire will be notoriously unforgiving, with the ability to cause massive damage in a short space of time. Accordingly, the necessary fire suppression equipment (and/or civil works) to mitigate the risk (in mines, tonnes and tonnes of poured concrete) can run into the millions of dollars at remote sites and add a significant amount of space to the installation footprint.
Instead, the Koodaideri project has specified the use of MIDEL 7131 – a biodegradable, synthetic ester transformer fluid which is fire safe up to 316˚C; a vast improvement on mineral oil’s fire point of 170 ˚C. Consequently, the mine’s transformers require a smaller footprint, don’t require fire walls and allow simplified bunding. They also provide the added bonus of being environmentally friendly. As well as saving millions of dollars, this simple innovation has set a new standard in the way power is supplied to projects, shutting the door on oversized projects with supersized budgets.
This is a real success story for Rio Tinto, and its step-change in decision making has made a marked difference elsewhere too. Just last year, Rio Tinto earned a Safety and Health Resources Sector Award nomination from the Government of Western Australia for the implementation of on-line partial discharge screening and condition monitoring on a fleet of more than 1,000 switchgear panels. The regime has significantly improved substation safety culture and asset reliability across 25 mining sites.
“As well as saving millions of dollars, this simple innovation has set a new standard in the way power is supplied to projects.”
Mining plant operators
The Australian Resources and Energy Group (AMMA) predicts that of the 20,767 employees needed in Australia’s mining sector by 2024, mining plant operators will see the most demand, with a total of 8,660 operators required across the country’s 57 total projects.
Western Australia (WA) accounts for more than 50% of this demand, with AMMA expecting that 4,464 mining plant operators will be needed in the region.
WA contains eight of Australia’s nine new lithium mining projects, which has ensured the country remains one of the world’s largest producers of this critical mineral.
With demand for this metal increasing with the development of electric vehicles, these mining operators will be an important part of Australia’s future energy mix as well as the country’s presence in global energy markets.
In the report, AMMA CEO Steve Knott said: “There is no escaping that the mining industry, a significant driver of national wealth and prosperity, can be highly cyclical. While the industry has always been a key pillar of the Australian economy, the period of 2005-2012 saw unprecedented levels of project and workforce growth.
“The number of direct employees in Australia’s mining industry jumped from 113,000 to 274,000 – a 162% increase in seven years. On average, the workforce demand grew by one-fifth every 12 months.
“Australia’s mining industry is facing new workforce demand at levels not seen since the previous investment and construction ‘boom’. Securing the pipeline of skills to support mining project growth is a significant challenge that must be met head-on, collaboratively, by industry and government.”
But Rio Tinto isn’t the only operator giving serious thought to what mines of the future should look like.
Glencore’s Mount Isa Mines, the largest underground network of mines in the world, recently awarded the Wilson Transformer Company a contract to supply electricity infrastructure to the 32,000-hectare site. The order includes three 132 kV/25MVA above-ground transformers. The transformers were originally to be filled with mineral oil, but after learning of the benefits of synthetic esters at the TechCon Aus-NZ 2019 conference, the superintendent for above ground high-voltage was moved to specify synthetic ester fluids instead.
The ability to mitigate the risk from fire and smoke, and to reduce the burden of transformer maintenance all in one go was an undeniable draw. This is also made possible by upgrading existing mineral oil transformers by ‘retrofilling’ them with synthetic ester, as opposed to specifying costly new transformers with a much longer lead time.
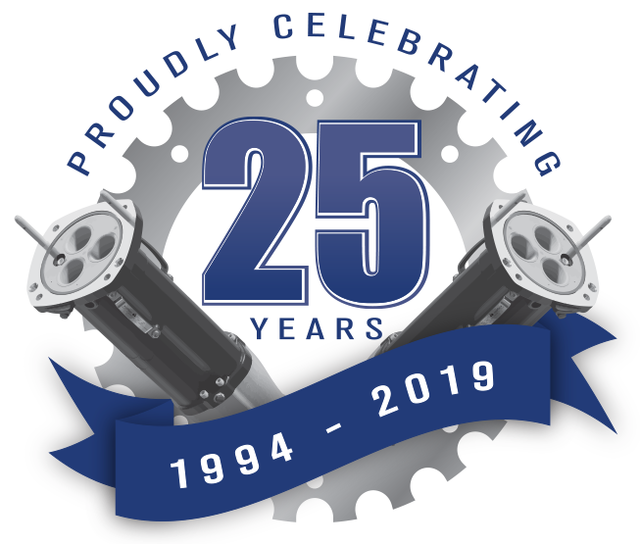
AusProof is celebrating 25 years of business in Australia in 2019.
What’s next for mines of the future? Small changes, big improvements
Fast forward five or ten years and where might we expect to be? Well, many mine operators are already quietly gearing up for subsea exploration – purported to be the ‘next frontier of mining’. This will bring a whole new set of unique challenges, particularly around reliability and environmental impact, where the infrastructure will very much come into its own. But for now, there are thousands of sites that would benefit from taking a fresh look at their infrastructure. After all, it can often be the smallest changes that make the biggest impact when it comes to environment and safety.
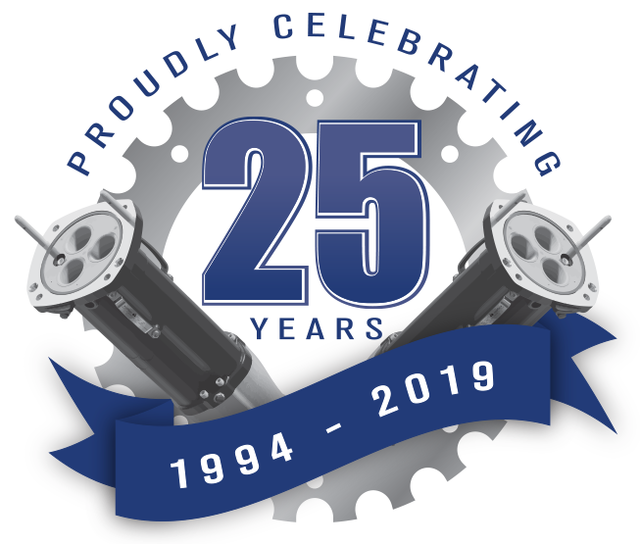
AusProof is celebrating 25 years of business in Australia in 2019.