During December 2019, in an active mine in the Antofagasta region in Chile, our teams programmed and fired 185 DaveyTronic® detonators with 2-way wireless capabilities: a world premiere! We speak with Aymeric Denuelle, Product Marketing Manager for Davey Bickford Enaex, who has been working with the research and development teams in France to create the system.
The system is very exciting, what can you tell the customers about its capabilities?
The DaveyTronic®Edge product is a new electronic detonator system with wireless capabilities. It will be offered as an option of our current DaveyTronic®. It is the first electronic detonator that enables the removal of surface harness wires while keeping two-way communication, which is a crucial safety feature in our industry. This means that, from programming up until firing time, you can communicate back and forth with the detonator. This feature provides information on the detonator location, identify potential misfires, but more importantly report on the detonator status on each stage of the blasting process.
How is it different from a regular electronic detonator?
DaveyTronic®Edge is equipped with a surface module that provides energy and two-way communication capabilities to the detonator. Equipped with a down line, the system development aims to eliminate all the surface wires and all the electrical network which could be troublesome and even hazardous. Two-way communication is a key enabler to always get closer to ensure zero misfire as it is the only way to know everything works fine up until the firing order. You can decide whether you want to proceed or not and potentially cancel the blast. A misfire will mean exposing people to danger afterwards in the digging phase which can result in serious damages and even casualties. Therefore, it is absolutely crucial to keep a way to detect it, which the DaveyTronic® range is able to do while offering two-way communication.
Safety seems to be a big benefit of this product, is this how you identified the need for it?
It is part of our global strategy, as the Enaex group, to humanize mining. Removing people from hazardous situations is a priority for us, as we seek a minimum exposition to danger. For example, reducing the time spent on the bench contributes to humanize mining as it is a hazardous situation with explosives around and potential harsh environmental conditions. Humanize mining also means a more suitable job for the miner with less effort required while on the bench. The proposed technology makes complete sense because we ease the handling; it is easier to use than a regular electronic detonator. In addition, the programming operation will be faster by removing the clipping process and the deployment of the cables on surface, also contributing to remove hazard and exposure, especially knowing that regions where mines are located might be subject to extreme temperatures. This new technology also paves the way for automation, in our efforts to keep the teams on-site away from dangers and extreme conditions.
What has been the biggest challenge you have faced so far?
With this technology, when compared to wired networks of electronic detonators, the main difference is the removal of surface wires. Instead of having an electrical network where everything is connected, we go to a radio network of hundreds of modules. A clear benefit of electronic initiation is the timing accuracy. In our case, synchronisation applies to a wireless network of hundreds of independent detonators. The key challenge for the R&D teams was to guarantee the synchronization between modules. Currently the product is at a prototype stage so the next challenge is to define the lead to its industrialisation.
Are you using two-way communication in other areas of your business?
Two-way communication is part of most electronic initiation systems today as a means to enable communication between a remote firing point and the on-bench equipment. What is new in our approach is, instead of having only two-way wireless communication between the firing point and the bench, now we have two-way wireless communication from the firing point to the bench but also over bench, with all the detonators reporting wirelessly to the on-bench blasting machine.
How does drone technology help with DaveyTronic®Edge system and other projects in general?
Today, drones are mainly used during the blast to make video records, or post blast to enable analysis of the blast output and measure the volume of the muck pile for instance. We are the first company to use a drone before the blast as a step of the initiation process. It is a key enabler for this technology with multiple benefits. Using a drone allows taking full advantage of the contactless programming offered by DaveyTronic®Edge which results in increased safety, operational efficiency and greater productivity. Using drone technology and more generally steering towards automation will also help to remove human errors from the process. With its geo-localisation capability, a drone knows exactly where it is and thus can assign the right timing to each detonator. One could think that automated operations may not be as flexible as ones performed by humans in case of modifications during the drilling process. However, based on its available positioning data, and the integration of engineering information, the drone could adapt the timing to the real situation based on the designed blast pattern.
What is key for customers to understand about DaveyTronic®Edge?
This technology can be handled by any regular blast crews so someone who knows how to implement electronic detonators will be able to use our DaveyTronic®Edge with little to no extra training. They will require training on the system, but not at an expert level. This technology represents the future of wired electronic initiation. For a mining company, it will be easy to switch from a regular product to the DaveyTronic®Edge because it will be simpler to use. For the operator their life will be eased because it is faster so they will spend less time on the bench. There will be no more last-minute surprises for the operator to deal with. Our product will pave the way to automation with all the benefits in safety, accuracy, reliability and cost saving for the mining company. The blasting process will be faster which means that customers will stop operations for a shorter time.
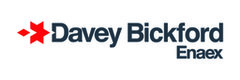
A world premiere: Innovating for a safer & more productive blasting
wireless enabled electronic system with 2 way communication capabilities
read interview
During December 2019, in an active mine in the Antofagasta region in Chile, our teams programmed and fired 185 DaveyTronic® detonators with 2-way wireless capabilities: a world premiere! We speak with Aymeric Denuelle, Product Marketing Manager for Davey Bickford Enaex, who has been working with the research and development teams in France to create the system.
The system is very exciting, what can you tell the customers about its capabilities?
The DaveyTronic®Edge product is a new electronic detonator system with wireless capabilities. It will be offered as an option of our current DaveyTronic®. It is the first electronic detonator that enables the removal of surface harness wires while keeping two-way communication, which is a crucial safety feature in our industry. This means that, from programming up until firing time, you can communicate back and forth with the detonator. This feature provides information on the detonator location, identify potential misfires, but more importantly report on the detonator status on each stage of the blasting process.
How is it different from a regular electronic detonator?
DaveyTronic®Edge is equipped with a surface module that provides energy and two-way communication capabilities to the detonator. Equipped with a down line, the system development aims to eliminate all the surface wires and all the electrical network which could be troublesome and even hazardous. Two-way communication is a key enabler to always get closer to ensure zero misfire as it is the only way to know everything works fine up until the firing order. You can decide whether you want to proceed or not and potentially cancel the blast. A misfire will mean exposing people to danger afterwards in the digging phase which can result in serious damages and even casualties. Therefore it is absolutely crucial to keep a way to detect it, which the DaveyTronic® range is able to do while offering two-way communication.
Safety seems to be a big benefit of this product, is this how you identified the need for it?
It is part of our global strategy, as the Enaex group, to humanize mining. Removing people from hazardous situations is a priority for us, as we seek a minimum exposition to danger. For example, reducing the time spent on the bench contributes to humanizing mining as it is a hazardous situation with explosives around and potential harsh environmental conditions. Humanizing mining also means a more suitable job for the miner with less effort required while on the bench The proposed technology makes complete sense because we ease the handling; it’s easier to use than a regular electronic detonator. In addition, the programming operation will be faster by removing the clipping process and the deployment of the cables on surface, also contributing to remove hazard and exposure, especially knowing that regions where mines are located might be subject to extreme temperatures. This new technology also paves the way for automation, in our efforts to keep the teams on-site away from dangers and extreme conditions.
What has been the biggest challenge you have faced so far?
With this technology, when compared to wired networks of electronic detonators, the main difference is the removal of surface wires. Instead of having an electrical network where everything is connected, we go to a radio network of hundreds of modules. A clear benefit of electronic initiation is the timing accuracy. In our case, synchronisation applies to a wireless network of hundreds of independent detonators. The key challenge for the R&D teams was to guarantee the synchronization between modules. Currently the product is at a prototype stage so the next challenge is to define the lead to its industrialisation.
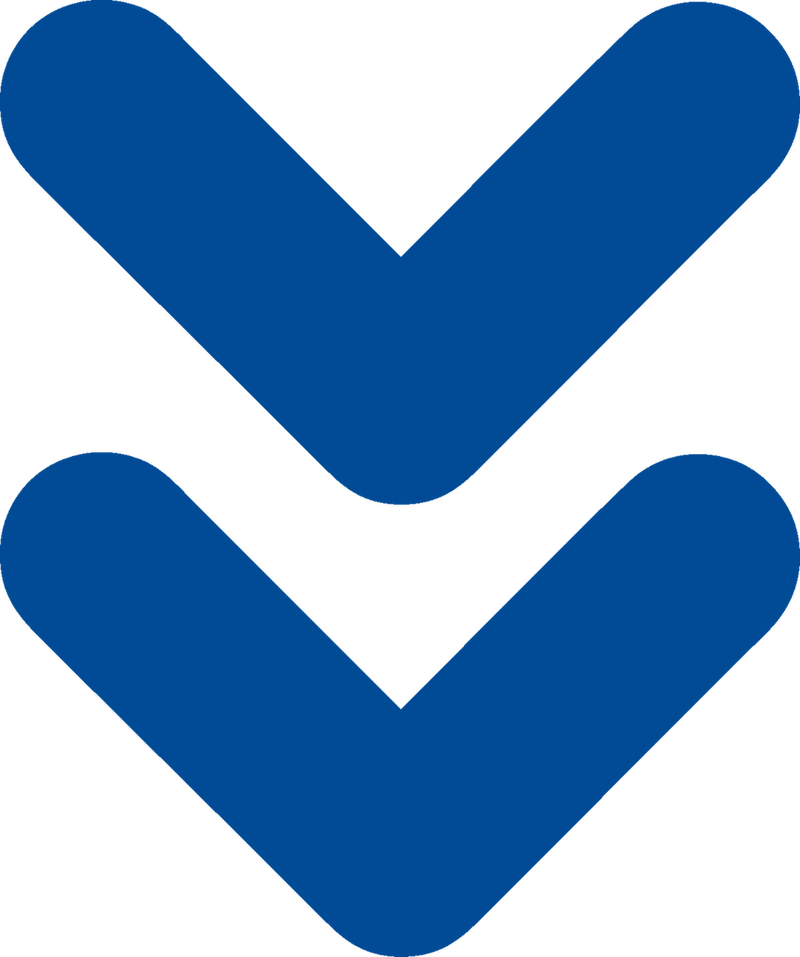
Are you using two-way communication in other areas of your business?
Two-way communication is part of most electronic initiation systems today as a means to enable communication between a remote firing point and the on-bench equipment What is new in our approach is, instead of having only two-way wireless communication between the firing point and the bench, now we have two-way wireless communication from the firing point to the bench but also over bench, with all the detonators reporting wirelessly to the on-bench blasting machine.
How does drone technology help with DaveyTronic®Edge system and other projects in general?
Today, drones are mainly used during the blast to make video records, or post blast to enable analysis of the blast output and measure the volume of the muck pile for instance. We are the first company to use a drone before the blast as a step of the initiation process It is a key enabler for this technology with multiple benefits. Using a drone allows taking full advantage of the contactless programming offered by DaveyTronic®Edge which results in increased safety, operational efficiency and greater productivity. Using drone technology and more generally steering towards automation will also help to remove human errors from the process. With its geo-localisation capability, a drone knows exactly where it is and thus can assign the right timing to each detonator. One could think that automated operations may not be as flexible as ones performed by humans in case of modifications during the drilling process. However, based on its available positioning data, and the integration of engineering information, the drone could adapt the timing to the real situation based on the designed blast pattern.
What is key for customers to understand about DaveyTronic®Edge?
This technology can be handled by any regular blast crews so someone who knows how to implement electronic detonators will be able to use our DaveyTronic®Edge with little to no extra training. They will require training on the system, but not at an expert level. This technology needs represents the future of wired electronic initiation. For a mining company, it will be easy to switch from a regular product to the DaveyTronic®Edge because it will be simpler to use. For the operator their life will be eased because it is faster so they will spend less time on the bench. There will be no more last-minute surprises for the operator to deal with. Our product will pave the way to automation with all the benefits in safety, accuracy, reliability and cost saving for the mining company. The blasting process will be faster which means that customers will stop operations for a shorter time.
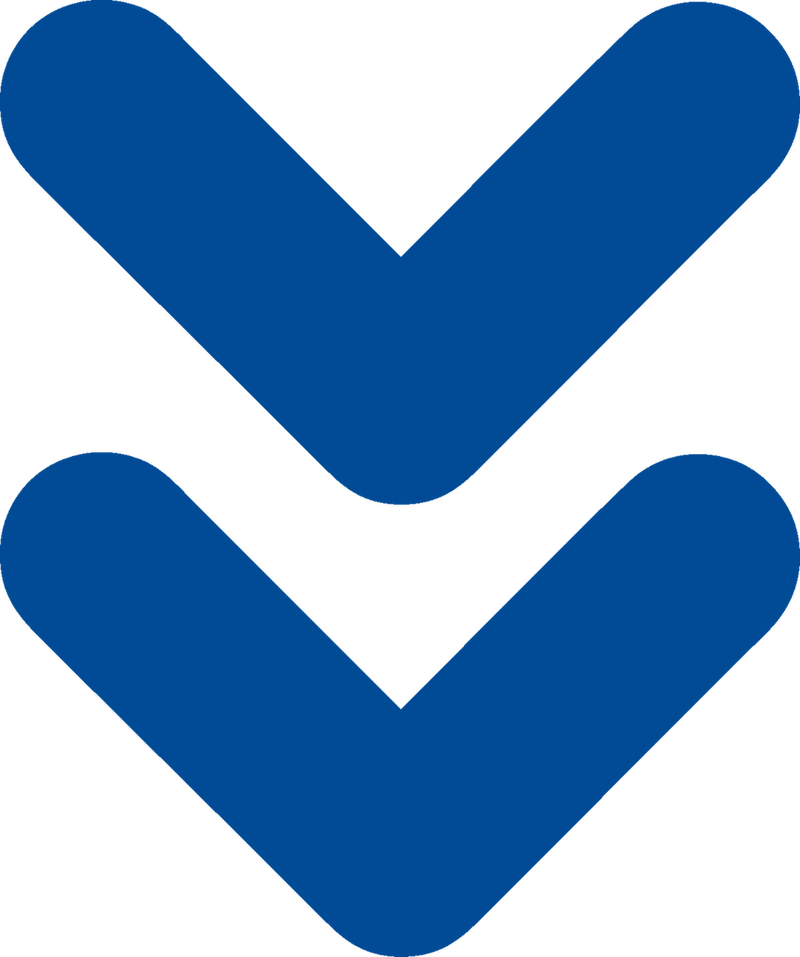