Feature
On the rails: around Western Australia’s massive mining rail network
The Pilbara produced over 800 billion tonnes of iron ore in 2020-21, a massive amount requiring an equally massive rail network. JP Casey investigates.
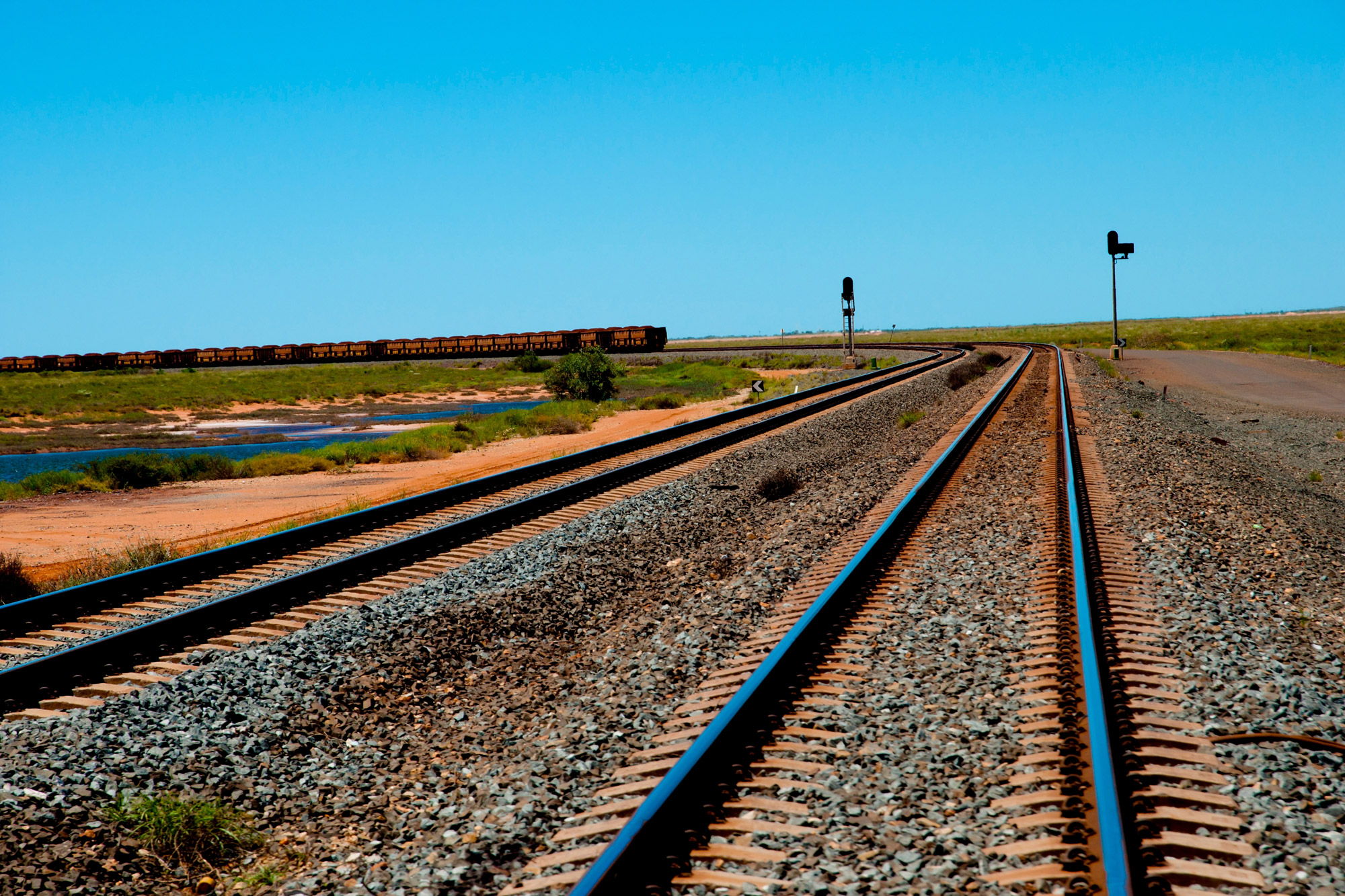
Railway in Western Australia. Credit: Adwo via Shutterstock
The Pilbara is Australia’s, and perhaps the world’s, mining heartland, dominating in both national and global production of a number of minerals. The region was the world’s second-largest producer of bauxite and third-largest of gold in the 2020-21 financial year, and these commodities delivered close to $15bn (A$23bn) in value for the Australian economy.
However, iron ore is the jewel in the region’s crown of commodities. Pilbara miners produced over 800 billion tonnes of iron ore in the 2020-21 financial year, with Western Australia accounting for 98% of the country’s total iron ore reserves. These products included over $100bn (A$150bn) worth of iron ore exports, and generated $103.3bn (A$154bn) in sales, up from $42.7bn (A$64bn) in 2016-17.
Massive business, but a sector of this size requires equally sizable infrastructure, both literally and financially. In the case of the Pilbara, a number of vast rail lines, built specifically to transport iron ore from mine to port cross the countryside, all but carrying stacks of cash from one end of Western Australia to another.
The state’s four primary rail lines – owned and operated by mining giants including BHP and Rio Tinto – account for over 3,800km of track. These connect mines in the Pilbara to ports at Dampier and Port Hedland, bringing Pilbara iron ore to the world. With newfound interest in Australian mineral exports, particularly from China, this rail infrastructure could be more important than ever as Western Australia looks to keep up its production.
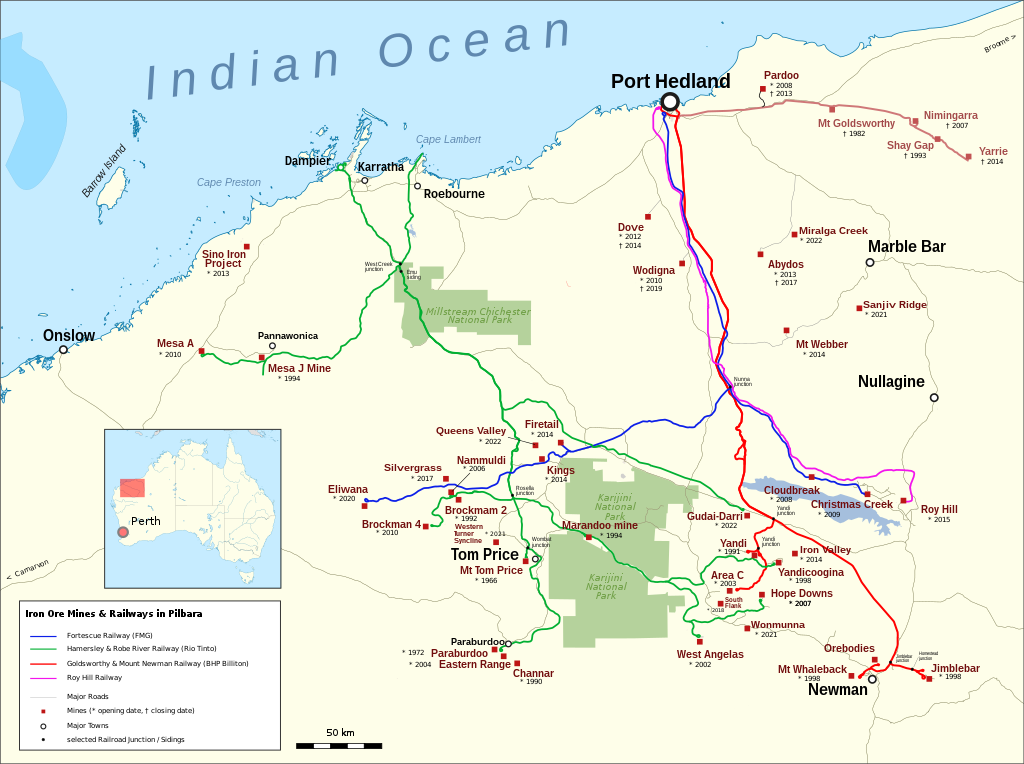
Credit: Peter Christener via Wikimedia
Fortescue Railway
Fortescue’s rail lines connect a total of five projects – four functional iron ore projects and one currently under development – and bring the company’s iron to Herb Elliott Port at Port Hedland. The miner has recently invested in its iron ore production, committing $1.3bn to the Eliwana project in 2018, and bringing its new Western Hub into its rail network, as the company looks to protect its place as the third-largest producer of iron ore, as of the 2020-21 financial year. Considering the scale of these operations, the miner has taken steps to reduce its carbon footprint.
Last year, Fortescue Metals Group chairman Andrew Forrest announced plans to develop an “infinity train,” a form of locomotive that captures the energy given off as the train’s wheels create friction with the track, and converts this into electricity. This electricity is then stored in batteries stored on the train, and used to power the vehicle as it moves up hills. This would cut its need for fuels such as oil, improving the environmental performance of the entire project.
While the technology is nothing new, its use in heavy industry, particularly on trains so massive that vast reserves of energy are needed to power them, presents an engineering challenge. Fortescue has already acquired Williams Advanced Engineering for $221m, bringing on board an engineering partner for the project, and announced that it plans to deploy its infinity train as early as next year.
Hamersley and Robe River railways
The Hamersley and Robe River railways have been cornerstones of Pilbara mining for decades, with the two lines first starting to ferry rail cars in 1964 and 1970 respectively. The lines were merged into a single entity, operating under the banner of Pilbara Rail, by Rio Tinto in 2001. Four years later, the miner announced that the move had saved the company around $10.7m (A$16m).
Rio Tinto has gone on to invest significantly in the rail network, most recently with the construction of an additional 166km of track in August 2022. This pushed the total length of the network to over 1,800km, the longest network operated by a single company in the region. This is the latest development in the company’s hugely impressive “AutoHaul” project, which has brought autonomous haulage to the length and breadth of its Pilbara rail network.
The AutoHaul project is significant both on its own merits, and its role as something of a proof of concept for large-scale driverless mineral transportation. The network builds on Rio Tinto’s 2018 delivery of iron ore by an autonomous train in the Pilbara, then a world’s first. It today consists of 220 trains, which themselves operate entirely autonomously, overseen by human operators in Perth.
The vast scale of both the network and its potential implications for working habits – Rio Tinto claims that the project will remove the need to transport drivers 1.5 million kilometres each year – as well as the success with which the network has been managed, means this could be a blueprint for other autonomous rail lines in the future.
Goldsworthy and Mount Newman railways
The Goldsworthy and Mount Newman railways both began work in the 1960s, but their function as part of the BHP rail network has drawn headlines for decades. In 2001, one of the miner’s trains operating on the network broke a world record for the longest train in the world, at 4.5 miles. The company also produced 253 million tonnes of iron ore in 2022, 145 million of which came from the South Flank and Mining Area C projects, both in the Pilbara.
However, the line has drawn considerable attention for less productive reasons. In 2011, the railways were the subject of a bid by Fortescue, which sought to gain access to BHP’s networks, arguing that the alternative, building its own rail lines, would be prohibitively expensive. While both a federal court and the Australian High Court ruled against Fortescue, and overturned an earlier decision made in favour of the appeal, the episode drew attention to the challenges that can arise when a select few companies own significant transport infrastructure across such a large area.
More recently, one of BHP’s trains in the Pilbara travelled without a driver for close to 100km, before being forcibly derailed. While no-one was injured in the crash, the Australian Transport Safety Bureau called the damage to the train itself “substantial”, and the loss of ore and resulting transport suspensions are thought to have cost BHP over $200m (A$300m).
Roy Hill railway
The Roy Hill railway transports iron ore from Australia’s largest iron mine, which shares a name with the rail line. Both facilities are owned by Hancock Prospecting, and have received significant investment, in both time and money. The mine is a $6.7bn (A$10bn) project with an annual production of 60 million tonnes, and connects the mine to Port Hedland via a 344km stretch of track.
The scale of the mine and its infrastructure have helped deliver consistently impressive financial results for Hancock, which saw its revenue increase from $5.6bn (A$8.4bn) in 2019 to a high of $11.1bn (A$16.6bn) in 2021, before falling slightly to $9.8bn (A$14.6bn) last year. The Roy Hill mine alone delivered profit after tax of $2.2bn (A$3.2bn) in the 2021-22 financial year, a significant return in pure profit for a single project.
However, questions remain as to the future of the project. When permission was first granted for the railway in 2011, ahead of the first train travelling in 2015, Hancock concluded that the line would remain in operation for “20+” years. With the halfway point of the rail’s minimum lifespan approaching, Hancock has made much of its plans to export its iron ore to East Asian buyers, notably in South Korea. With the long-term future of the rail line uncertain, it is unclear how the company plans to deliver ore to these consumers in the 2030s and 2040s.