Company Insight
Sponsored by Diacon Australia
The innovative leaders in Conveyor guard safety
The original Australian-owned & Australian-built plastic guarding system
Diacon Australia is a leader in the design and manufacturing of plastic conveyor guarding. Since 2010, Diacon has been delivering safe and durable solutions that significantly improve conveyor productivity and safety, machinery guarding, work area demarcation and fall protection.
Originating in Mackay, Queensland, Diacon’s unique range of plastic guarding can now be found in sites across Australia, as well as overseas in Papua New Guinea, Indonesia, New Caledonia, and the UK.
The specialised custom-made range of products encompass a wealth of features that comply with Australian standards, including Diacon® Conveyor Guards, Diacon® Hungry Boards, and Diacon® Safety Panels.
Identifying industry risks
History has shown that there are numerous risks associated with working in and around conveyors. Such as:
- Rotating parts or pinch points
- Confinement or assembly areas
- Electrical or fire hazards
- Falling hazards
- Items falling or expelling from belt
When considering the size, power and speed of conveyors, the lost time injury (LTI) frequency rate from incidences is higher and more complex. While an isolated incident is often viewed as the result of a single action, conveyor incidences present several more layers of concern, including at-risk behaviours, procedures, safety measures, and equipment faults.

State-of-the-art methodologies
Diacon was initially established to service the Queensland sugar industry, however ongoing site analyses and research revealed a considerable gap in the market for potential high risk mining incidences – leading to an expansion into the mining sector.
Guided by a clear ethical standard of operations, Diacon has combined maximum growth and sustainability with safety, as the fundamental foundation for product development.
With the aim of zero harm and to implement long-term protective measures, the unique range of Diacon products are customisable, CNC manufactured, corrosion-free and built to handle extreme weather conditions. Every safety consideration has been given to the design, including the inclusion of a slide-lock mechanism captive within the Diacon Guard to avoid mishaps.
Their team of specialised professionals, fabricators and installers complete a series of risk assessments, utilising state-of-the-art methodologies, and product testing phases to create innovative industrial plastic products.

Innovation from the ground up
Diacon has approached the market with innovative features that directly respond to onsite industry safety concerns, by reducing operational disruptions, maintenance and repairs, workplace hazards, and employee risks. The use of industrial plastic ensures products are lightweight, resistant to extreme conditions and have a superior corrosion resistance to other steel and aluminium alternatives; the key differences being the design and performance that can withstand tough Australian conditions and reduce risks during installation, maintenance, and operations.
Diacon is challenging the industry standard of guarding, by inventing products that deliver a sustainable solution with ease-of-application and cost-efficiencies – particularly in large-scale conveyor builds.
The long-term economic benefits are identified when considering the following:
- Requirement for design drafting of each guard – reconciled internally by Diacon.
- Higher-than-normal labour rates in Australian-made guards – reduced through manufacturing automation.
- Cost of modifying non-conforming or ill-fitting steel guards – allowance made in the design for simple, onsite modification.
- Avoidance of double handling of Diacon guards during manufacturing.
- Painting is not required of Diacon guards.
Notably, Diacon has the only guarding system on the market with the inclusion of in-built hook and hang’ system features, a reinforced frame and a UV stabiliser guarantee of 15 years.
The inclusion of an additional ‘hook and hang’ feature is an important safety measure to remove guarding from walkways and reduce trip hazards for workers during maintenance, further reinforcing the unwavering commitment to workplace health and safety.
The lightweight construction ensures that maintenance can be undertaken by one person, instead of two, due to the 16kg weight limit. This compares favourably against traditional 30kg steel mesh guards.
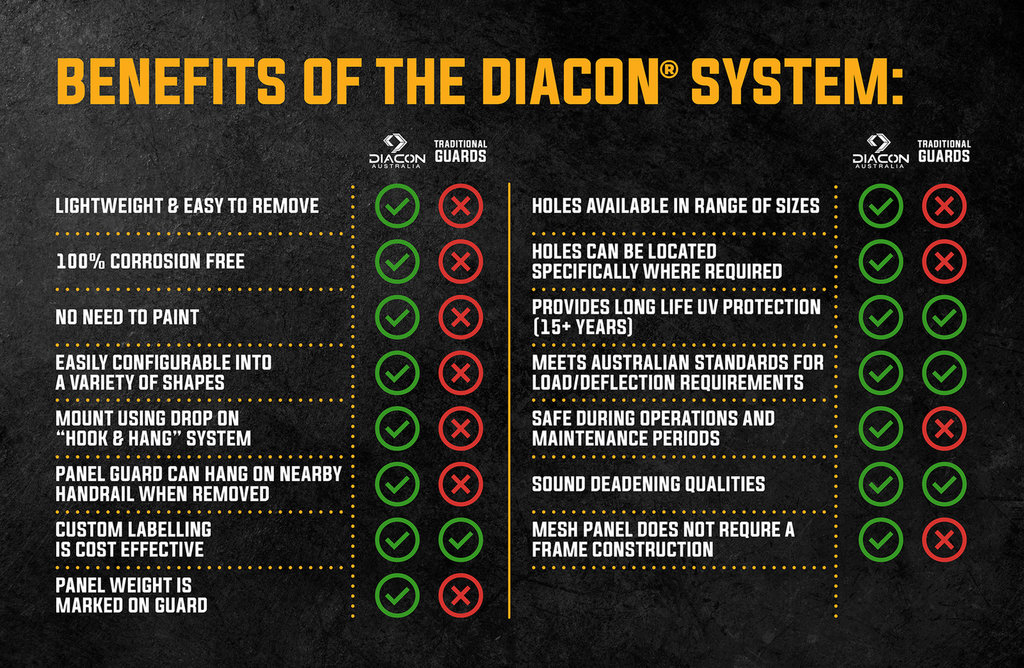
A focus on evolution
Diacon is positioned as a leader in safety prevention and forward-thinking, due to their proactive response to industry risks. Their commitment to effective engineering techniques and continuous improvement has enabled them to offer a custom site-specific application that is adaptive to the needs of customers.
Upon manufacturing the plastic mesh guarding, Diacon team members conduct on-site installation, or alternatively guide customers through completing their own installation to provide a level of education that supports safe practices.
Diacon’s focus on product refinement is evident with the current trial of a new product range at a mine site in the Bowen Basin and in a sugar mill in Mackay. Expected to be released soon, the new high-visibility conveyor belt guard utilises stainless steel mesh to improve visibility for cleaning and inspections for areas, like tail ends and gravity take-up units. The result of customer feedback and requests, the new product will be positioned alongside their existing range.
While the existing Diacon HDPE guarding has good visibility through, the optional extra high-visibility stainless steel mesh will give workers a clearer view where lighting is inadequate or where build-up of dust and mud is a problem.
Contact information
Diacon Australia
Tel.: 1800 342 266
Email: sales@diaconaust.com.au
Web: www.diaconaust.com.au