Company Insight
Sponsored by Martin Engineering
Tackling Dust Head-On: The Importance of Quality Skirting
Standfirst
It’s a persistent and often an overwhelming challenge facing bustling world of material handling: dust.
As materials transition from one conveyor belt or hopper to another, they are subjected to crushing forces and airflow, forming an ideal environment for creating dust particles. This seemingly innocuous byproduct poses significant risks, ranging from health hazards for workers to environmental concerns and regulatory scrutiny.
Central to the matter is a misunderstanding that solely relying on dust suppression and collection is adequate to tackle the problem. Although these measures provide advantages, they fall short in addressing the root cause. True dust control begins at the source of its creation – the transfer point.
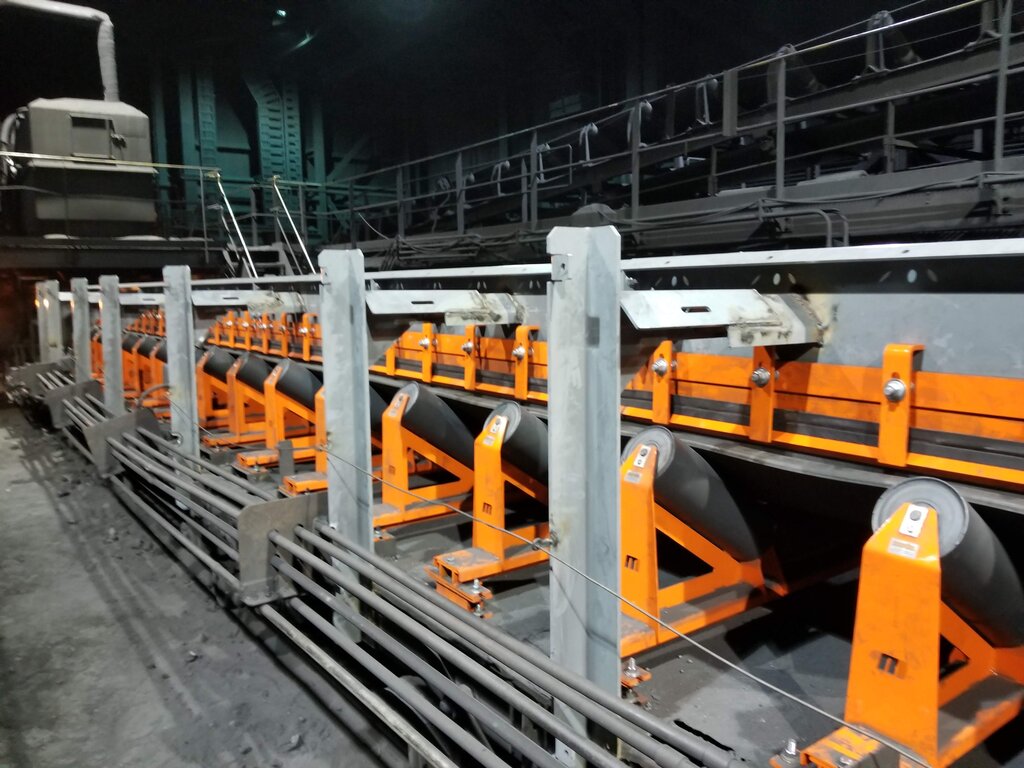
Caption. Credit:
Causes and Best Practices
The root causes of dust at transfer points in material handling operations stem from various factors inherent in the process. Understanding these underlying issues is crucial for implementing effective dust control measures. Here are the primary root causes:
- Influx of Air: As material loads into the transfer point, it brings along a rush of air, exacerbating dust dispersion.
- Material Degradation: The crushing action during transfer leads to the generation of fine particles, intensifying dust production.
- Poor Transfer Point Design: Outdated or inadequate transfer point designs struggle to meet the demands of modern production, resulting in heightened dust emissions.
Implementing best practices to solve dust problems at transfer points in material handling operations requires a comprehensive approach that addresses the root causes of dust generation. By combining engineering solutions, effective maintenance practices, and proactive measures, facilities can significantly reduce dust emissions and create a safer and more sustainable working environment.
Here are some key best practices:
- Comprehensive Support: Ensure the conveyor belt is fully supported along the entire length of the chute wall to prevent sagging and maintain a tight seal.
- Abrasion Resistance: Protect rubber skirting with durable steel wear liners to withstand the abrasive forces encountered in material handling operations.
- Effective Sealing: Install belt skirting to create a barrier that seals off airflow, thereby containing dust at the source.
- Sequential Approach: Prioritize dust containment measures before implementing suppression and collection techniques to maximize effectiveness.
- Velocity Control: Employ dust curtains or other means to reduce exiting air velocity to under 200 feet per minute (FPM), minimizing dust dispersion.
By adhering to these best practices, facilities can achieve comprehensive dust containment, mitigating risks to both personnel and the environment.
Furthermore, embracing a proactive approach to dust management not only enhances workplace safety but also fosters regulatory compliance and community goodwill.
Martin Engineering can help you out!
Martin® specializes in providing innovative sealing solutions designed to address dust and material containment challenges. With a focus on engineering excellence and customer satisfaction, Martin® offers a range of sealing systems tailored to specific applications and operational requirements.
Their sealing solutions, including the ApronSeal™ and BOCO Skirting, are renowned for their durability, versatility, and effectiveness in preventing material spillage and dust emissions.
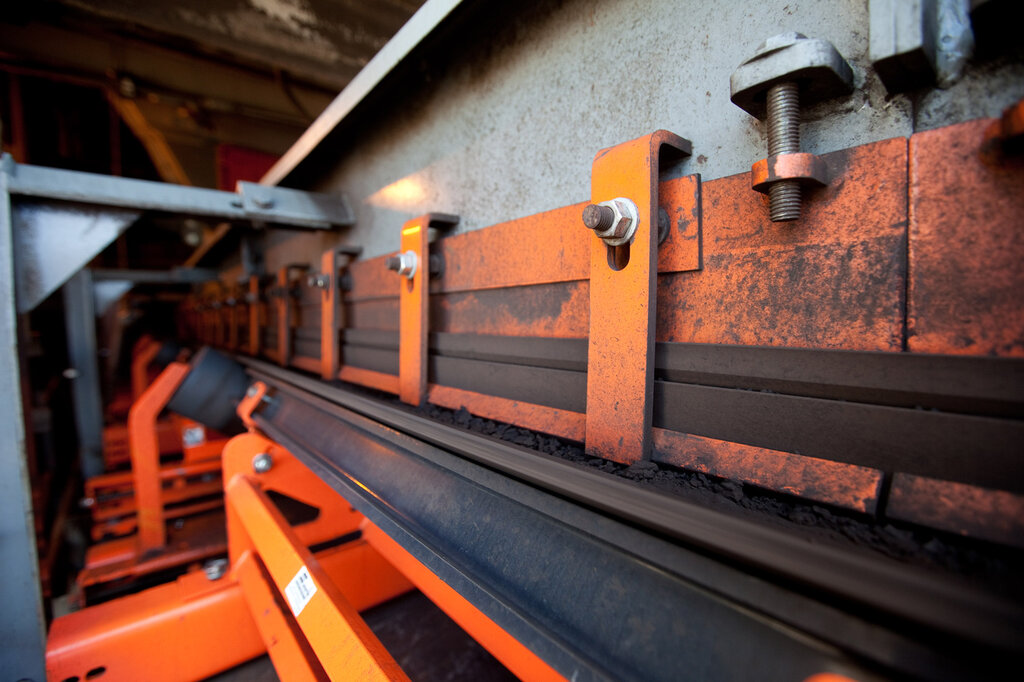
Caption. Credit:
By collaborating closely with clients and leveraging their extensive expertise in bulk material handling, Martin® ensures that each sealing solution is meticulously engineered to deliver optimal performance and long-term reliability.
With a commitment to sustainability and operational efficiency, Martin Engineering's sealing solutions play a crucial role in enhancing workplace safety, environmental stewardship, and overall productivity in diverse industries worldwide.
Contact information
Martin Engineering Australia
www.martin-eng.com.au
mea@martin-eng.com
1300 627 364