Cover Story
‘Fatigue kills people all the time’ – but monitoring is making strides
Fatigue monitoring and management remains a nascent discipline in mining, but technology and industry understanding are progressing, as Stu Robarts finds out.
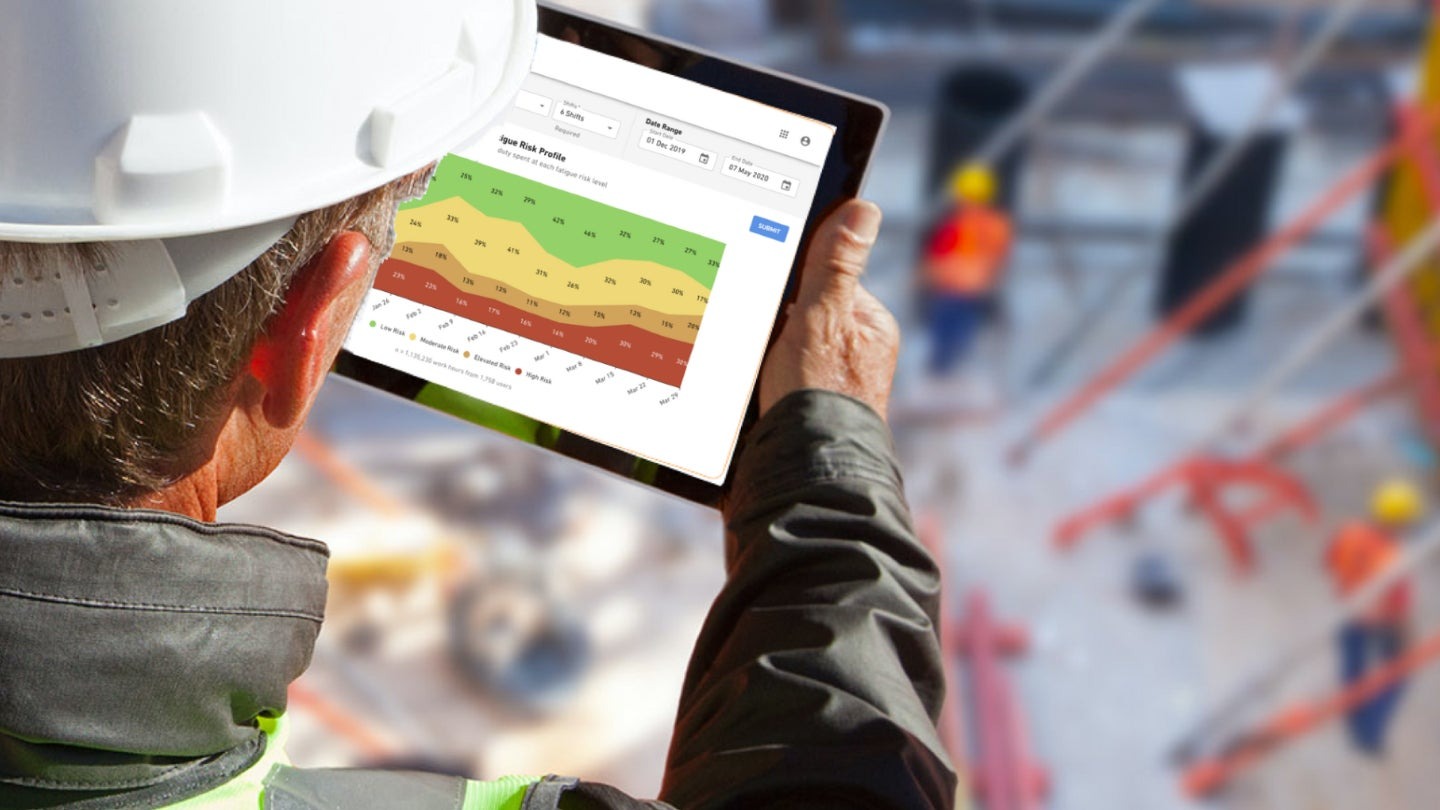
Fatigue Science uses leading indicators to predict the fatigue levels of operators. Credit: Fatigue Science
In October, First Quantum Minerals (FQM) launched a Fatigue Crib Station at one of its sites in Africa. Described by FQM as a first of its kind in the region, the rest area is “specifically designed to combat fatigue among dump truck operators”, according to the Canadian mining and metals company.
Per FQM, the station is ergonomically designed for rest and has amenities for relaxation, flexible scheduling to minimise operational impact and technology for monitoring and optimisation. Its aim is to reduce the risk of accidents.
As to how the station will contribute to this goal, Daniel Kutontonkanya, superintendent of health and safety management systems at FQM, said it would be used for “staggered fatigue breaks that will be guided by ReadiWatch [sleep tracking] technology from a company called Fatigue Science.
“When the operator’s ReadiScore [fatigue rating] drops below a determined threshold, he is called in for a hot-seat change out. The truck is then operated by a standby operator. The expected outcomes are a lower fatigue event count and lower truck downtime.”
This sort of attention to fatigue monitoring and management is a world away from where the mining industry was even ten years ago – due in large parts to a lack of understanding then about the role fatigue plays in accidents and the cost implications it has for mining companies.
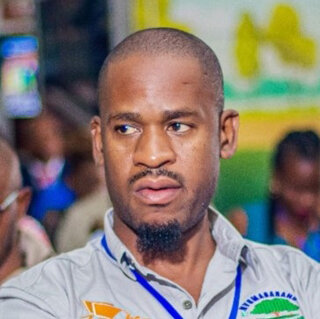
Tobias Zulu, occupational health and safety manager, Barrick Gold
“When you review accidents and near misses within industries that work around the clock most are caused by human error not equipment failure,” David Edwards, worldwide market manager for safety solutions at Caterpillar, tells MINE. “And industry data shows that most human error accidents are related to human fatigue or inattention. When humans become fatigued, decision making is slower and it’s frequently observed that people more often make procedural errors, including those related to jobsite safety. Humans are simply not designed to be at peak alertness at every time of every day.”
Of the impacts this can have, Tobias Zulu, occupational health and safety manager at Barrick Gold, tells MINE: “Incidents are a cost to the company not only in the form of production loss due to reduced efficiencies – a fatigued worker is a slow operator – but also indirect costs such as replacing manpower, medical costs, compensation, increased insurance costs and the poor reputation of a company.”
But Zulu adds that the most important impact of fatigue monitoring and management is ensuring that “every employee goes home safe and healthy every day”, and boiling down the significance of fatigue, Bryden Waggott, vice president for product at FQM’s ReadiWatch supplier Fatigue Science, tells MINE simply that: “Fatigue kills people all the time.”
He says too that dealing with it is challenging “because at any given moment it’s hard to tell whether someone is fatigued. It’s a major problem, not necessarily for injuries but for lack of productivity and mistakes.”
Understanding fatigue
The growing recognition within the mining industry of the need to monitor and manage fatigue was reflected in a survey carried out by MINE’s parent company GlobalData earlier this year. It found that fatigue detection was among the technologies in which there have been the highest increases in relative investment within the industry in the past few years.
Outlining the survey results in its Global Mine-Site Technology Adoption Survey, 2024 report, GlobalData said companies are increasingly investing in fatigue detection to help improve uptime and prevent accidents.
Of the companies surveyed, 42.3% had either fully implemented fatigue detection technology or invested considerably in it, while a further 36.8% had made moderate investment, minor initial investment or trialled the technology. Over a third (37%) were expecting to invest in fatigue detection technology in the next two years.
The fatigue monitoring systems have evolved from merely alert systems that depended on alarms to more advance systems that can actually physically intervene when there is a fatigue event – such as with seat vibration.
Tobias Zulu, occupational health and safety manager at Barrick Gold
The advancement of monitoring and management within the industry is evidenced anecdotally too. Drawing on his decade-plus of experience in mining health and safety, Zulu says: “I have seen fatigue management programmes develop from being education- and awareness-based to taking a more scientific approach, where systems have been introduced to monitor fatigue through wearing gadgets and devices to alert operators when they are fatigued.
“The fatigue monitoring systems have evolved from merely alert systems that depended on alarms to more advance systems that can actually physically intervene when there is a fatigue event – such as with seat vibration.
“In the past few years, we have seen a rise in more proactive systems which predict fatigue as opposed to intervening during the fatigue even. These systems predict when an operator or worker is likely to be fatigued, allowing supervisors to take action even prior to workers starting their shifts or during any period of the shift.
“I’ve also seen companies trying to balance fatigue management programmes to include scientific monitoring systems incorporating education, diet, exercise, scheduling of rosters and shifts, sleep management and hydration.”
One company that has invested heavily in fatigue management is metals and mining giant Rio Tinto. It employs a layered approach that takes into account human behaviour, job design and fatigue indicator tracking. This includes pre-employment screenings and ongoing medical checks to detect and address sleep disorders, fatigue checklists, even-time work rosters, commute and journey management plans and in-vehicle fatigue tracking technology.
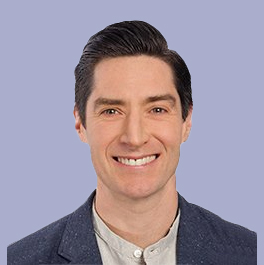
Bryden Waggott, vice president for product, Fatigue Science
“At Rio Tinto, the health and safety of our workers is our highest priority, and we recognise fatigue is a critical risk in our day-to-day operations,” a company spokesperson tells MINE. “We have seen considerable development in the technology available to the industry to detect, manage and understand fatigue. There is a greater understanding that fatigue is complex and managing this risk requires a multifactor approach beyond the design of shifts and rosters.”
Of this progress within the industry, Waggott says: “We’re just as a workforce getting a better understanding of productivity and fatigue. The understanding that you cannot overcome fatigue, that it always wins, is something of step change. In the last 20 years, there’s been an understanding, there’s been acceptance, and then there’s been some mitigation.”
Despite that, he notes that fatigue monitoring and management as a discipline with mining is “still nascent” – a view shared by Adrian Heieis, product manager at digital reality company Hexagon, whose Operator Alertness System was purpose-built for the mining industry.
“Fatigue monitoring is a relatively new technology in mining,” Heieis tells MINE. “Compared with technologies like fleet management and mine planning software, which have been around since the 1980s, monitoring for operator fatigue and alertness did not become popular in mining until the 2010s.
“Technology has evolved greatly since then, with many alternative technologies being tested, but real-time, vision-based PERCLOS (percentage of eyelid closure) monitoring remains the most effective solution. Today, there is an opportunity to significantly increase the accuracy of these solutions thanks to recent advancements of AI and machine learning technologies.”
Monitoring and management
As Heieis explains, there are various means by which fatigue can be monitored, such as by eye blinks and by brainwaves (via EEG), but the PERCLOS monitoring favoured by Hexagon has been found by studies to be one of the most reliable approaches. It is not a solution in itself, though, and the company employs it in concert with other technologies including collision avoidance, obstacle detection, personnel detection and vehicle intervention.
“One cannot just install a fatigue management system and expect it to be fully impactful,” adds Heieis’ colleague Josh Savitt, principal advisor at Hexagon. “Both the long-term and short-term success are dependent on the quality of change management and education. This is how the solution truly becomes a solution.”
Monitoring operators in real-time is a crucial part of combatting potential risks to do with fatigue, but it is inherently reactive. So-called ‘lagging’ indicators like PERCLOS can be complemented by more predictive ‘leading’ indicators.
“You need to manage both,” says Waggott. “You can’t avoid lagging indicators. You can try and mitigate them with leading indicators.”
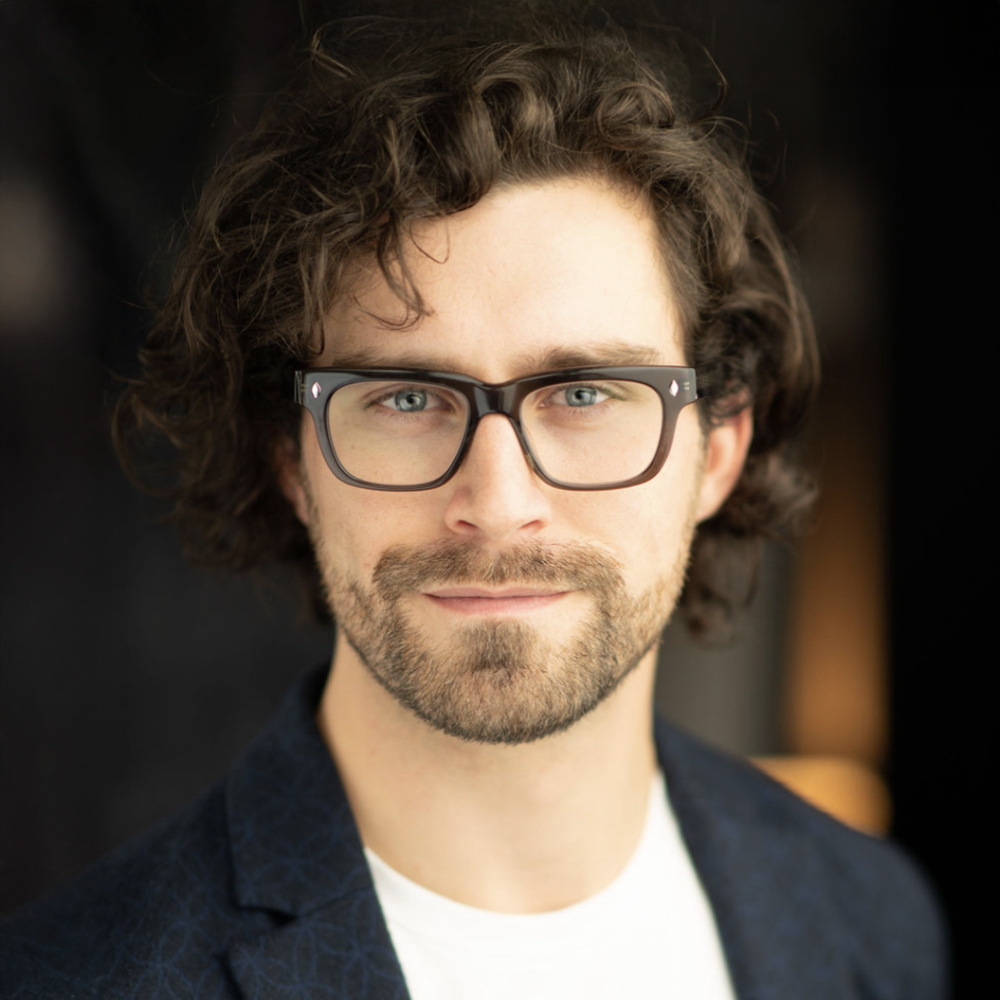
Adrian Heieis, product manager, Hexagon
Waggott explains that most current fatigue management technology focuses on lagging indicators, typically using cameras in the cabs of trucks to monitor operators.
“The camera tech is amazing these days. If someone closes their eyes for a fraction of a second longer than normal in a blink, immediate alarm. The trouble with lagging indicators and alarms like that is it’s super disruptive. If I close my eyes for a little bit because they’re irritated by the dust, that’s an alarm.
“Stop the truck, come out, check this person, see if they’re asleep or impaired. There’s a tonne of these sort of false flag indicators that disrupt productivity.”
Fatigue Science focuses on leading indicators, using a combination of AI and biomathematical modelling to analyse data like work schedules and sleep patterns to predict fatigue levels. The approach was developed by the US military to help understand where the limits with fatigue are and how it impacts critical work.
Waggott explains: “The two primary inputs right now are, how much you have slept in the last ten days – what’s your sleep reservoir? And how much have you worked and when have you worked?
“Someone who’s worked nine to five with a low amount of sleep for the last five days, they’re not going to be great. But someone who’s worked 7pm to 7am with a low amount of sleep, and that sleep is during the day, is going to be much, much worse.”
One system that takes into account both leading and lagging indicators is Caterpillar’s MineStar DSS, which monitors for signs of driver fatigue and distraction alongside the use of predictive data.
“It is the multi-layered approach of instant in-cab feedback, monitoring centre review and communication combined with consistently applied on-site process reinforcement that fosters lasting behaviour improvement and organisational trust with MineStar DSS,” says Edwards. “When organisations fail to reinforce in-cab detections with on-site communications and believe technology alone solves the problem, results are often short-lived.”
Challenges and impacts
Waggott credits much of the growing interest in fatigue management within the mining industry to companies’ bottom lines.
“Mining specifically is really interesting,” he says. “Almost any heavy industry, high-hazard industry – oil and gas, mining, heavy manufacturing, petrochem – fatigue has a very big impact on them. With mining, however, everything is bigger … So, the impact of a fatigued person, the impact on productivity, the impact on personal safety is much, much greater in the mining industry.”
Heieis adds: “Operating mining equipment is hard. One of the challenges in mining is that fatigue is not just about what happens on site but also about the lifestyle and personal choice of operators. This is why education and change management are so important, and it is also why miners should consider fatigue management to be for operators – to help them and not just to monitor them.”
Like Waggott, Heieis notes that there is also a productivity benefit to having operators who are more alert. “But, at the end of the day, it’s about saving lives,” he says.
By putting in place fatigue management programmes and technologies, miners can greatly reduce the risk on-site, bring down their incident frequency, and, as a byproduct, improve productivity.
Bryden Waggott, vice president for product at Fatigue Science
“The operation of heavy and light mobile equipment is one of the biggest risks to people on mine sites, and fatigue is one of the main contributing factors. By putting in place fatigue management programmes and technologies, miners can greatly reduce the risk on-site, bring down their incident frequency, and, as a byproduct, improve productivity.”
These points are echoed by mining companies themselves, for which the safety, cost and reputation implications are stark.
“Managing fatigue risk is a critically important part of our day-to-day operations given our large number of shift workers,” the Rio Tinto spokesperson says, adding: “Some of the work activities our people do is physically and mentally demanding and fatigue increases the chances of injury, even when people are not at work.”
The future of fatigue
Given its size and resources at hand, it’s unsurprising that Rio Tinto’s monitoring and management efforts are advanced, with the company noting that it has “consulted with a wide variety of scientific and operationally based organisations to determine the key elements of a system to monitor and mitigate fatigue risk.”
With this in mind and looking to the future, its spokesperson tells MINE: “Rio Tinto expects there will be greater use of biomathematical modelling across the mining industry to design roster schedules that maximise workers’ alertness and performance to reduce risk. This technology is commonly used in high-risk shiftwork industries including aviation and rail.
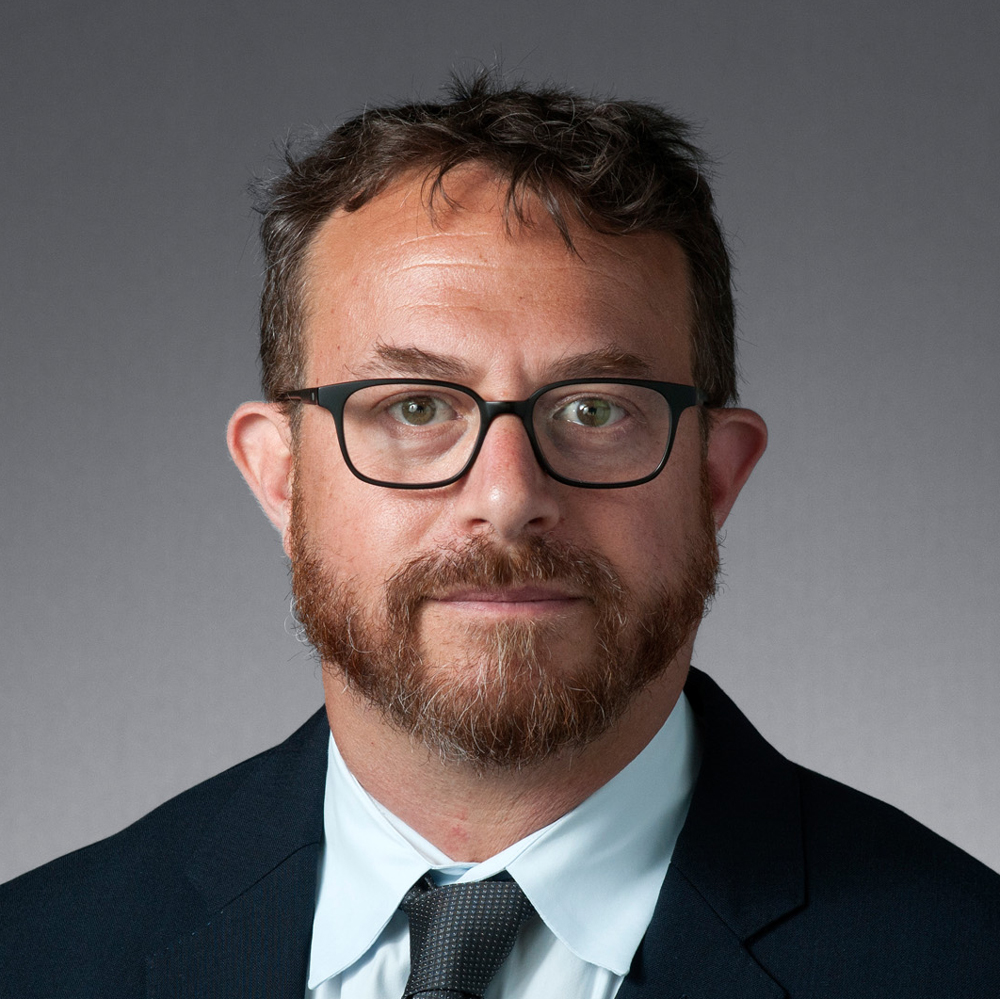
Josh Savitt, principal advisor, Hexagon
“As the understanding of the bi-directional relationship between mental health and fatigue continues to improve, we expect to see even more effective measures put in place to support workers.”
From the perspective of Fatigue Science, the predictive fatigue management of which is based on that biomathematical modelling, Waggott believes artificial intelligence will begin to play a much bigger role.
“I’m talking about really big data tools that can pull out information and also look at other operational systems to provide prescriptive tools. There’s going to be a combination of these fatigue tools into more operational and safety systems. That’s just a given. That’s got to happen because they’re so closely tied to it, and my expectation is that there’s going to be a real better understanding of productivity and how it relates to fatigue.”
That is a view shared by Barrick’s Zulu, whose company uses both CAT and Hexagon technology. He expects a combination of predictive and reactive fatigue monitoring systems to be increasingly used, commenting: “I think there will be a lot of emphasis on roster and shift scheduling to mitigate fatigue-related incidents. Companies that find this balance of technological, educational and roster/shift management will be on top of the game with regards to fatigue management.”
Of the technology underpinning fatigue detection, meanwhile, Edwards concludes: “Significant improvements are being made in sensor technology and how that information is analysed to allow a deeper insight into a driver’s ability to operate safely. Solutions are better able to discern different stages and types of fatigue, levels of alertness and vigilance, including how engaged a driver is with their driving task. These enhancements allow us to provide drivers with better feedback about their driving condition earlier to help keep them engaged and productive.”