Interview
Ore processing innovation: Rockburst sets out to cut energy use by up to 50%
Rockburst Technologies CEO Oscar Malpica tells Andrew Tunnicliffe about the company’s CO2-based ore processing technology, which has gained interest from mining majors.
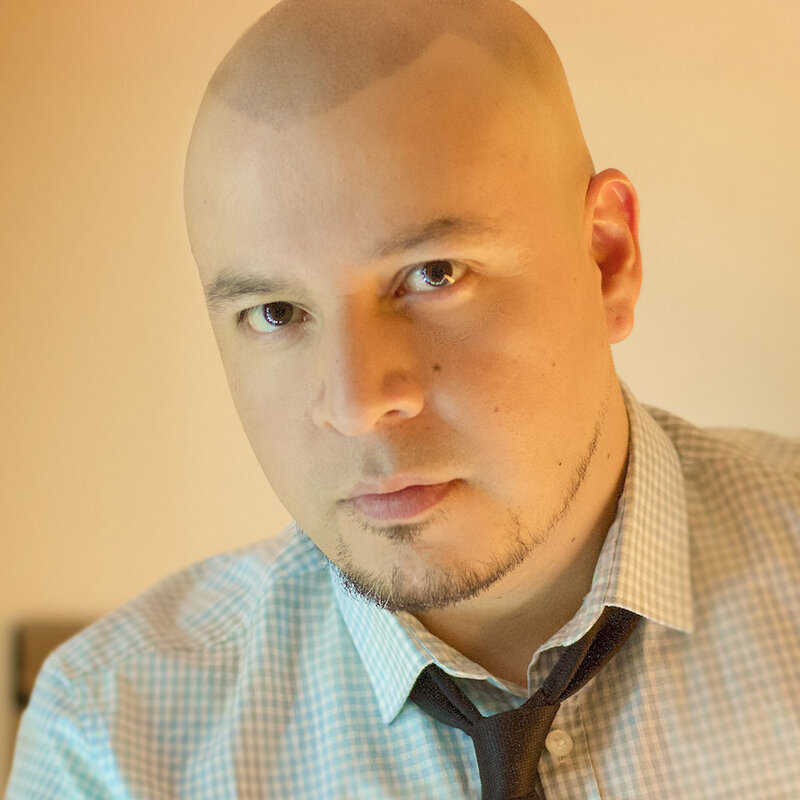
CEO Oscar Malpica co-founded Rockburst in 2020. Credit: Rockburst Technologies
It is a proposition that is almost literally out of this world. Quite simply, Rockburst’s CO2 Pulverization technology breaks rock with CO2, cutting the need for consumable media in the grinding process, and offering potential hardware cost savings.
However, says Rockburst, the savings don’t stop there. It has the potential to significantly reduce energy consumption, cut and even repurpose greenhouse gas (GHG) emissions, and requires no water, improving mines’ sustainability credentials.
The Canada-based company says it is committed to using its technology to “make a positive impact on the world around us, whether on Earth or beyond”. With the grinding process in mining globally equating to as much as 4% of energy consumption, Rockburst CEO Oscar Malpica and his team have set out to innovate and transform ore processing. Here, he tells us about CO2 Pulverization, the company’s work with BHP and other mining majors, and the road to commercialisation.
Andrew Tunnicliffe: Can you tell us a little about Rockburst?
Oscar Malpica: We started in 2020 with the objective of developing a new technology for the mining industry, a technology that would consume up to 50% less energy to break rock and liberate valuable minerals. So far, we have validated that technology in the lab and are now working with top mining companies; we are also hoping to raise capital to bring our CO2 Pulverization into the field for real-world operations.
Andrew Tunnicliffe: What is CO2 Pulverization?
Oscar Malpica: The mining industry primarily uses compression techniques for breaking ore in a process called comminution, which accounts for around 4% of global energy consumption – a significant problem. Our technology uses CO2 to promote tension within the ore, not compression, meaning we break the rock using considerably lower energy. We take advantage of the fact that rocks are ten to 30 times weaker under tension than compression.
Ore is put into a vessel, then CO2 is introduced and set to a temperature and pressure where it coexists in both gas and liquid states – known as the supercritical state of CO2. At this moment, CO2 is able to penetrate inside the pores of the ore. Then we very rapidly decompress the system and as CO2 expands and tries to escape, it breaks the rock down from within.
Andrew Tunnicliffe: What does it offer that current technologies don't?
Oscar Malpica: There are four key differences. First there is less energy consumed, so right off the bat you are getting some sort of cost reduction, and typically fewer GHG emissions. Then an important aspect is that we use CO2, which is prone to be sequestered after it has been used in this process. This means that in the future we could potentially use the CO2 from waste gas from other industries – or even from the air with direct air capture (DAC) systems – and then sequester that CO2, and lock in the carbon forever in the tailings of our process. Finally, this is a dry process by default; we don't use water and this is an increasingly important aspect all around the world. All this is on the back of the absolutely staggering demand for critical minerals that the world will need towards 2050.
Andrew Tunnicliffe: If you are successful and this comes to market, what new infrastructure will it require?
Oscar Malpica: The infrastructure needed would be different but not uncommon. The pressure and temperature ranges in our process are very industry friendly, roughly 70 bar (atmospheres) and 30°C. This translates into a system with just two consumables: electricity and CO2.
Our system would use the existing mine’s electrical infrastructure. As for the supply of CO2, as this technology progresses to commercialisation we expect a larger adoption in the mining industry of CO2 capture systems for their own emissions, and even DAC systems, which could be synergistically used in a process like this.
Also, because CO2 Pulverization is technically a ‘grindless’ process, it does away with grinding media used in today’s equipment, which is extremely expensive and needs to be replaced every six to eight months.
Andrew Tunnicliffe: You are currently involved in a few partnerships – what can you tell us about them?
Oscar Malpica: Our biggest partner is BHP, as we are now part of their technology development programme called Think & Act Differently. Having the expertise of actual miners, and their feedback, as part of the development of this technology is absolutely invaluable. Other large mining companies that we have worked in the past include Anglo American, Teck and Copper Mountain.
On the research side, we have worked with a number of universities that have proposed applications of our technology that extend beyond mining, such as cement and electronic waste recycling.
Andrew Tunnicliffe: There has been some talk about your technology going into space?
Oscar Malpica: This is an area we didn't really think about, space mining and recycling. This is something we were made aware of during a last-minute meeting we had arranged with the guys from the Thomas Space Research Centre in Adelaide, Australia.
They said: “Wait a minute, your technology uses gas, therefore there is no gravity needed to operate your machinery?” We said “no it doesn’t need gravity, what are you thinking?” We then talked about the possibility – and this is in the future – of looking at how to recycle and reutilise stuff that is brought in space missions.
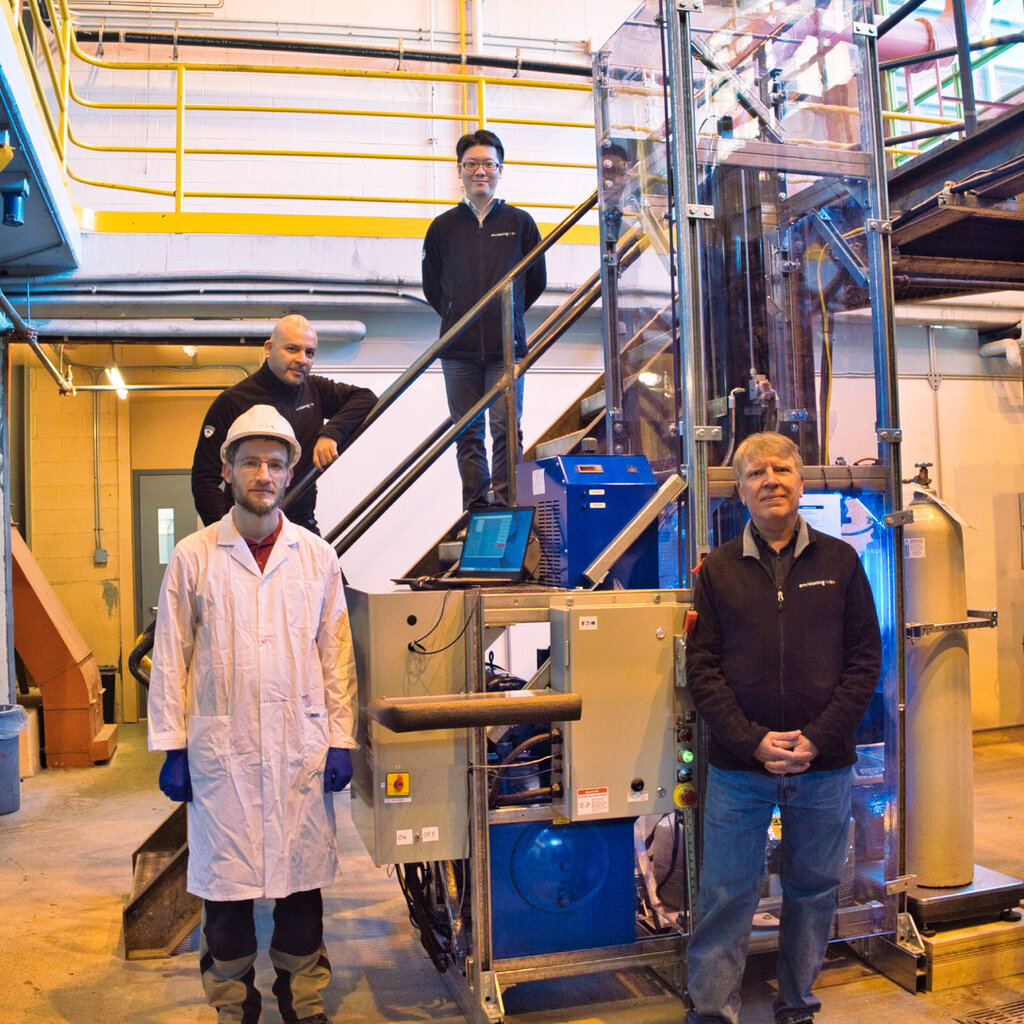
The Rockburst team. Front (left to right): Max Hesse, Cliff Edwards; back (left to right): Oscar Malpica, Chuck Lee. Credit: Rockburst Technologies
Our technology could potentially be used to disassemble full electronic devices down to its constituent parts, and these parts could then be reused for other purposes. There is also the aspect of space mining, particularly for water as the number one thing we will need to secure in all space missions. Again, these are long-term conversations.
Andrew Tunnicliffe: Although still at prototype stage, how is the industry receiving the concept – those that might use it and others it might compete with?
Oscar Malpica: Miners are definitely very interested in it. There are four areas they really want: less energy use, fewer emissions, potential for decarbonisation and that it is a waterless technology.
However, there is another aspect I have not yet mentioned: we are seeing early evidence of breakage along grain boundaries, the weakest points of union between two or three elements or mineral assets in the ore. If this is confirmed it would make the separation of different mineral species easier, and that would translate into less reagents and less energy needed to maximise the yield of minerals mined.
We are actually running a mineral liberation study, starting in July, to confirm this hypothesis with up to ten miners. I would say we have definitely piqued interest in the industry to the point where some of the majors – BHP and Anglo American, for example – are already supporting us with certain studies and certain aspects of technology.
Andrew Tunnicliffe: How has the project been financed?
Oscar Malpica: The initial support came from Natural Resources Canada after we were awarded as one of the six finalists in a national innovation contest to decrease energy in the mining industry. Since then we have raised private investment, secured additional government grants and landed service contracts with mining companies. At this moment we are looking for C$1.5m ($1.09m) as seed investment to design the first pilot unit that will eventually be deployed at a customer site.
Andrew Tunnicliffe: Where do you hope to be in five years’ time?
Oscar Malpica: Because our technology really doesn't distinguish what to break, we are currently working with BHP to determine where it could fit to provide the most bang for our buck. This is critical, especially at the beginning for a pilot because you do not want to build a massive machine. We are working with them to figure out the low-hanging fruit applications that we could tackle in three years’ time.
In the next couple of months we will be working to define where exactly that inflection point is. We are going to start small, a niche application where processing volume is not an issue, and where we could offer something no other technology can achieve.
Rockburst Technologies is keen to seek industry input and support, both financially and technically. If you are interested in discussing this technology or any other element of collaboration with them, visit www.rockburst.tech for more information.