Cover Story
How to build a fully electric mine
In Norway, an ambitious electrification project is underway. Andrew Tunnicliffe hears from Norge Mineraler and ABB about how they are designing a new mine to be fully electric.
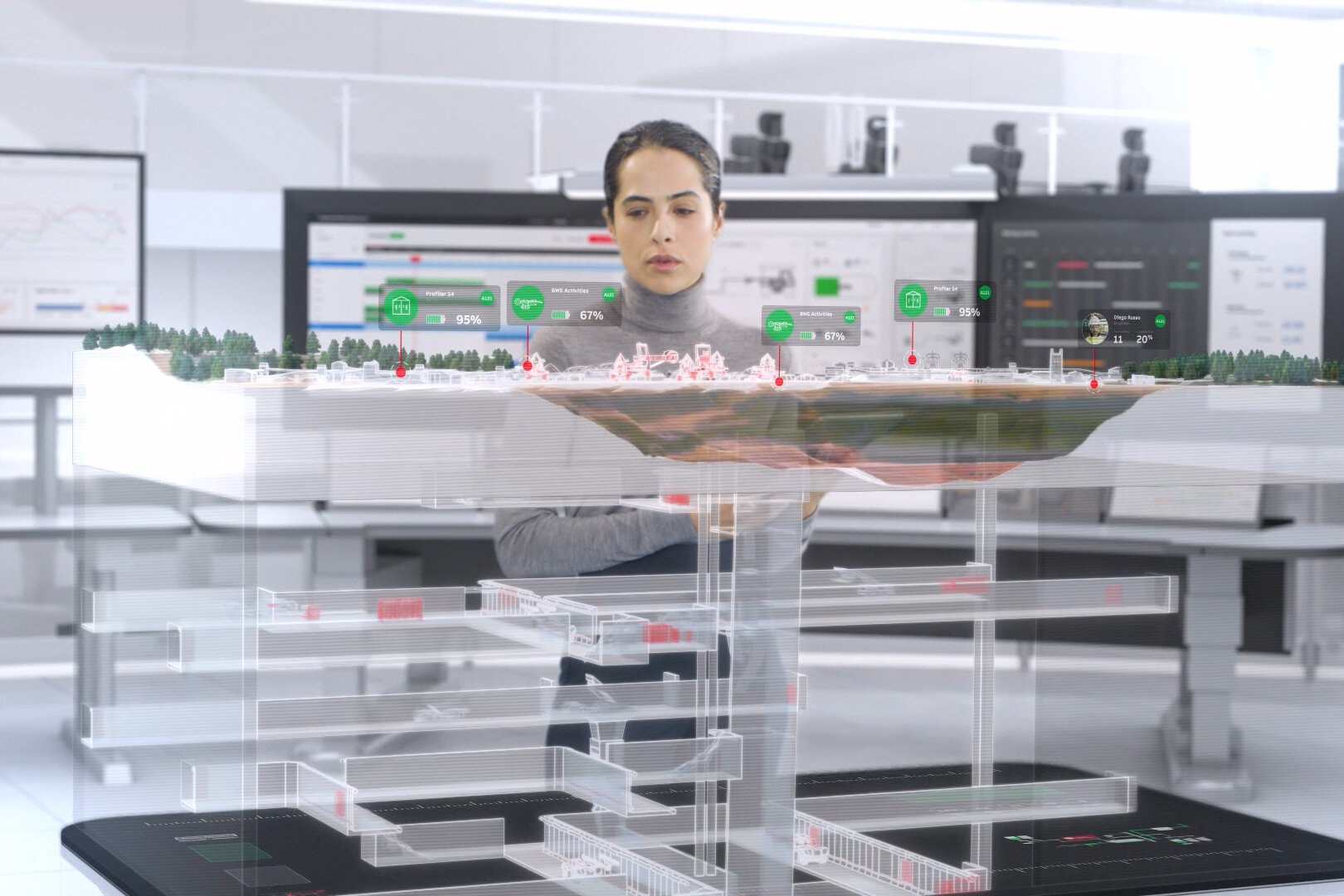
ABB and Norge Mineraler are exploring the full electrification of mining and downstream operations. Credit: ABB
“Electrification creates enormous opportunities for operational cost savings, innovative mine designs and resilience against uncertainty,” says the Electric Mine Consortium (EMC).
The group of more than a dozen mining companies and suppliers is collaborating to expediate the realisation of a fully electrified, zero-carbon and particulates-free mine. Such mines, it adds, will cut scope 1 and 2 carbon emissions completely while increasing mine productivity and helping “unlock deeper and more remote ore bodies”.
Last autumn, Norway’s Norge Mineraler announced it may have discovered one such vast yet untapped resource. It presented three updated Joint Ore Reserve Committee-compliant mineral resource statements totalling 3.4 billion tonnes of igneous rock.
Located in the Bjerkreim–Sokndal intrusion in south-western Norway, the find could potentially secure the supply of critical raw materials – including phosphate, titanium, vanadium and subsequently phosphorus – for 50 years, according to calculations by geologists based on already known data.
The announcement was boosted by news that Norge was collaborating with ABB to design the mine to be fully electric, once operational later this decade.
Integrating electrification at the mine design stage
This, Norge’s engineering manager and technical leader Hercules Sandenbergh says, is exactly the time a project team looking to electrify a mine should start planning. Speaking specifically of this project, he says very quickly there was a realisation that if you don't plan upfront, the options for electrification might be severely limited.
“I would just like to give an example of the benefits [of planning]” he says, speaking of an area of specific interest for Norge’s work with ABB – electric trucks and trolley systems. “You are able to put more power into trolley assisted mine trucks than diesel, meaning they can travel up greater inclines. For me, that is a great example of where you actually get a performance enhancement. But if you don't plan… you will not be able to put the trolley system in as a retrofit and won’t see such great benefits because your mine is just not designed in that way.”
That, of course, is one example, but it is a view echoed more broadly by ABB Process Industries’ Anton Venter, who says: “An electric mine looks different to a traditional mine, and the design of an all-electric mine needs to consider future developments, too.”
The feasibility study is addressing electrification, automation and digitalisation for maximum sustainability, cost-efficiency and productivity, from the outset and for the long term.
Nine months into the project, Venter explains, work to complete the feasibility and design stage is ongoing, before moving into front-end engineering and design (FEED). “We started with the feasibility study, looking at the site to see what is possible from a design perspective. As part of the study, we have to look at process design; once process design is finished, we can start looking into the electrical design.”
The FEED stage typically lasts one to three months and helps prepare for execution, aiming to enhance efficiency and productivity targets and capabilities defined in the feasibility study. Summing up ABB’s involvement thus far, Venter says: “The [feasibility] study is addressing electrification, automation and digitalisation for maximum sustainability, cost-efficiency and productivity, from the outset and for the long term.”
Mine design with a view to future innovation
Speaking of the ABB collaboration, Norge founder Michael Wurmser said the “transformative” partnership would mark a new era for more sustainable, resource-efficient mining. However, Sandenbergh explains, while some of those technologies are already established, others are still in development, adding that the speed of innovation today means that will likely always be the case – a factor that should be considered when designing and future-proofing a site.
For this reason, when designing next-generation mines it is critical to build with a view to advance further at later stages. For example, the trolley assist Sandenbergh spoke of is already available, but other elements of mining fleets are also suitable for electrification – excavators, for example.
“So, we need to bring those things into the planning and work in what would fit into the mine design,” he says, explaining that not all elements would be electrified to the same degree. “We would have some parts that would be very advanced, and others that would really be just at the start. This would give us a lot of space for improvement as we go on.”
When designing next-generation mines it is critical to build with a view to advance further at later stages.
This is where the partnership with ABB is crucial. Sandenbergh says: “For us it is important to be aware of innovations and advancements. ABB have their finger on the pulse in terms of where developments are going. We can work that into our mine to put in the best available technology in – but also, through our design, we can keep the option to implement electric technologies as they mature, reducing our environmental footprint and improving our efficiencies, reliability and throughput.”
Venter is also looking to future possibilities. “We hope to continue our collaboration into the execution stage to bring this next-generation mine to life,” he says, adding that recommendations as a result of the work being undertaken now will focus on low energy consumption, and optimising capital expenditure whilst lowing operational costs with lower-maintenance and higher-efficiency solutions.
Integrated electrification and digital systems
Technology is already helping to do that, including ABB’s eMine, which, as global eMine solutions manager Nic Beutler explains, is “a framework of solutions that aims to remove the CO₂ emissions from mine operations and ultimately support the energy transition in mining, progressing mining operations from the use of fossil fuels to electricity”.
It is an “ecosystem” – covering everything from mine to port – that makes the all-electric mine a reality through integrated electrification and digital systems. ABB hopes to introduce it to this project.
Beutler adds: “eMine is a natural extension of mining operations, with new electric or battery electric vehicles being introduced into the mine operation, as well as electrified trolley systems.” Launched in 2021, it not only covers physical assets – mine electrification and the automation of fleets – but also helps oversee a mine’s operations, providing real-time actionable insights to increase efficiency and reduce emissions.
We will no doubt see more convergence with automation and digital, with supportive operation management and energy management systems which interact with the assets according to the energy requirements and availability.
But, Beutler cautions, electrification is only as smart as the automation and digital components complementing the infrastructure.
“In the future, we will no doubt see more convergence with automation and digital, with supportive operation management and energy management systems which interact with the assets according to the energy requirements and availability,” he adds.
Although this is already an area ABB is working in, it says developing the capabilities of automation and digitalisation will only become even more sophisticated and crucial.
Managing energy demand in fleets and equipment
Globally, there are only a handful of mines classified, by their owners at least, as all electric, largely due to completely replacing diesel fleets with battery or trolley-assist vehicles.
It is not just fleets, however. Other types of equipment currently powered by diesel have the potential to transition, with OEMs working hard to help make that switch. A byproduct of this change is advances in ventilation and the systems used. The removal of diesel particulates from the environment means ventilations systems can do less in the first instance but are also able to run on electricity.
However, one challenge lies in reducing the overall energy consumption of the operation. Sandenbergh says the first and most important thing to consider is energy usage. His advice: look at what you are likely going to use and channel the design to reduce that consumption.
For his project, however, he accepts the site is uniquely positioned: “If we look at the area we operate in Norway, it has a large amount of renewables. There is wind and hydropower. That is where I think our project is, in particular, well suited to renewable electrification.”
He adds the region also has a strong electricity grid and accepts this isn’t the case for all mines, although others may have an abundance of other renewables such as solar.
As we look to the future of eMine, the next logical step is to include more renewables in the plan – to unburden the grid and avoid costly investments into large grid solutions.
Power demand is an area ABB is taking seriously, too. “Mines are becoming more remote... As we look to the future of eMine, the next logical step is to include more renewables in the plan – to unburden the grid and avoid costly investments into large grid solutions,” Beutler says, adding that this is where eMine is well suited.
“From integration of renewables into the grid design, right up to the point of energy dispatch, including the use of electric vehicles in a stationary or dynamic form of energy transfer, our portfolio of eMine solutions covers all.”
It seems change is coming to mining with many of the world’s leading companies having committed to reducing, even eliminating, carbon emissions by the middle of the century. Electrification, supported by innovative battery and renewable technologies, will no doubt be the single biggest contributor to achieving this goal.
However, electrification isn’t just about cutting emissions, as Sandenbergh explains, echoing the sentiment of the EMC. “It is talked about quite a lot in the media in terms of reduced carbon emissions and reduced environmental impact, but I think what gets missed is that this is not a zero-sum game," he says. "There are performance enhancements that we can get with electrification, and I think that is what we really need to focus on in the project.”
According to GlobalData, Norway currently only has one mine at which electrification – by way of vehicles – has taken place. All eyes are now on Norge and ABB as the country takes its next transformative step to cleaner, more efficient mining operations.