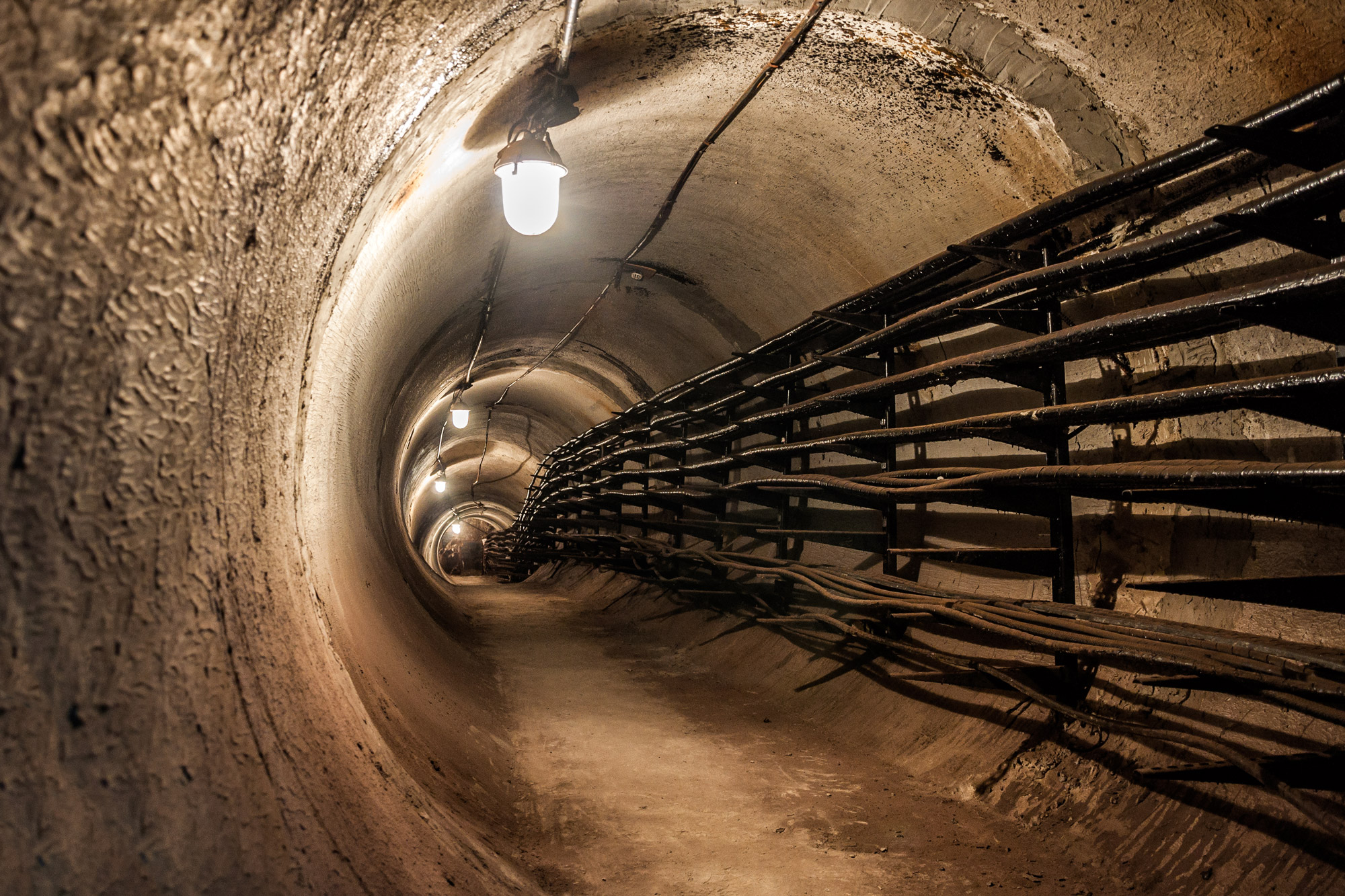
Communications
Voices in the deep: the value of underground communication collaboration
Giles Crosse investigates Swedish telecoms giant Ericsson’s cross-industry team of Ambra Solutions and Nutrien, which aims to deliver new radio systems to the Rocanville potash mine.
Some 95% of potash is used in the global fertiliser to support plant growth, increase crop yield and disease resistance and enhance water preservation, vital components to human development that renders potash mining one of the more influential mining processes, with regard to impact on human life.
Self-evidently, radio networks offer a number of benefits to potash production, particularly in underground environments where communication can be challenging. These include more functional operations kilometres beneath the surface of the Earth, and better futureproofed hardware.
For both miners and mining companies, safety, operational efficiency, downtime and morale are all elements which benefit, in addition of course to essential profit.
With this in mind, Swedish telecoms giant Ericsson has unveiled a cross-company approach that could set a precedent for technological innovation in some of the more specialised parts of the mining sector. Announced in November 2022, and in partnership with Ambra Solutions and Nutrien, the project could enhance communication and collaboration at the Rocanville potash mine in Canada, which has become something of a proving ground for the technology.
Talking matters
Difficulties in underground communications, in both potash and more general mining, have always affected the minerals industry. Ericsson says that in standard scenarios, with only a handful of Wi-Fi access points, workers could be required to travel several kilometres through tunnels just to get connected.
This has big implications in terms of convenience, the ability to talk should emergencies occur and practicalities for production and communicating challenges as and when they hit. But very deep communications are possible; Agnico Eagle has previously partnered with Ambra Solutions and Ericsson to design and deploy a private 4G LTE network some 3.2km beneath the Earth’s surface.
As a result, the companies improved both safety and the work experience for miners, enabling them to stay connected with colleagues and family above ground. The solution tracks the precise location of people, vehicles and machinery to prevent dangerous situations too.
Each mine can cover up to 500km2, with dozens of tunnels running across the length and width, around one kilometre underground.
Nutrien’s most recent potash case study explains how it operates some of the largest potash mines in the world, and demonstrates how the technology honed by Agnico could now be deployed on a larger scale. Each mine can cover up to 500km2, with dozens of tunnels running across the length and width, around one kilometre underground. The sheer scale of many of these projects makes the logistics involved in their management tricky for companies.
Of course, running those mine operations efficiently is the key to boosting production and keeping workers safe. Justin Stade, Nutrien’s director of NPK digital transformation, explains that: “[When] having a mine that is essentially the size of a city, communication is essential to know where people and equipment are at all times to ensure safety.”
Eric L'Heureux, Ambra’s president and CEO, adds: “It is very challenging to propagate a radio signal in a low-ceiling tunnel made of soft rock like potash,” drawing attention to some of the specific challenges faced by potash miners.
“Adding to the challenge, power is only available at tunnel intersections in a few parts of the mine. We had to perform a number of experiments in the field and use our propagation model to find the best locations for the radio antennas.”
Ease of use
For the mining worker, better underground communications offer practical benefits, which are in line with many of the time-saving advantages of modern communications technology more broadly. Workers can open up a manual or standard operating procedure for a piece of equipment on their smartphones. If a problem arises with such equipment, workers can simply take a smartphone picture and send it instantly to maintenance, rather than getting in a vehicle and driving hours to report the issue.
Through new mobile apps, voice communication with supervisors or the control room can be instantaneous from anywhere in the mine, again saving hours getting to the nearest phone.
Nutrien is beginning to deploy internet of things sensors on vehicles, equipment and systems like ventilation.
There’s more to like; Nutrien is beginning to deploy internet of things sensors on vehicles, equipment and systems like ventilation. Combining sensor data with analytics and machine learning, the company will be able to obtain predictive maintenance intelligence to match human efficiencies.
With sensors on its mine ventilation fans, for example, Nutrien can now receive real-time data on air flow and how much particulate matter is being emitted into the mine atmosphere. This will enable managers in the control room to make more-informed decisions on how to reduce those emissions and ensure a healthy working environment for the people underground.
What’s more, those very people can call managers instantly, letting them know how the conditions feel to work in and offering valuable feedback to match the automated data.
Challenges beyond the mine
It is worth noting that the advances in underground radio networking come as the globe faces up to big challenges on potash, and indeed other mining production. The BBC writes that Svein Tore Holsether, from fertiliser firm Yara, said countries needed to cut their reliance on Russia after its invasion of Ukraine hit global food supplies, supply and prices.
His warning echoes concerns from the International Monetary Fund (IMF). Also speaking to the BBC, its managing director Kristalina Georgieva said the world should move attention today to fertilisers, because this is where we see particular threats for food production and therefore food prices in 2023.
She added: “Fertiliser prices remain very high. Production of ammonia [which is used to make fertiliser] in the EU, for example, shrank dramatically. All of this is connected, of course, to the impact of Russia's war on gas prices and gas availability.”
Production of ammonia [which is used to make fertiliser] in the EU, for example, shrank dramatically. All of this is connected, of course, to the impact of Russia's war on gas prices and gas availability.
There are big challenges ahead. The IMF says in response to the inflation of food, fuel and fertiliser prices, countries have spent over US$710bn for social protection measures covering one billion people, including approximately US$380bn for subsidies.
The World Bank Group’s $6bn IFC Global Food Security Platform supports farmers to access fertilisers and other critical supplies, while helping private companies make longer-term investments, focusing on improving the resilience of agri-food systems and fertiliser use efficiency.
This kind of support is useful, but clearly the potash and the fertiliser production has to be there in the first place. As a result, advances in this field in particular have never been more urgent.
// Main image: Cables in a tunnel. Credit: Alina Filatova via Shutterstock