Not simply ‘plug and play’: new battery electric risks for mine operations
Marcello Sanchez, mining global sales manager at Dafo Vehicle Fire Protection, explores how the global shift towards battery electric vehicles isn’t free from fire risks, and discusses how operators can minimise these effectively.
Battery electric vehicle (BEV) technology is continually evolving, and mining companies need to go back to basics to ensure workers, supervisors and management fully understand the new technology, safeguarding site operations and vehicle maintenance.
Mobile equipment fires are all too common in the mining and resources industry, and there are several key factors to consider to improve the understanding and application of fire prevention and mitigation controls across the sectors.
In general, mobile equipment fires present significant risks for operators, maintainers and emergency responders; can be catastrophic in underground operations; create wider operational and commercial issues for earthmoving equipment owners and operators; and require mandatory statutory reporting in most mining jurisdictions.
Yet these dangers remain extensively analysed, with regulators now expecting that mine operators will improve their mobile equipment fire management performance.
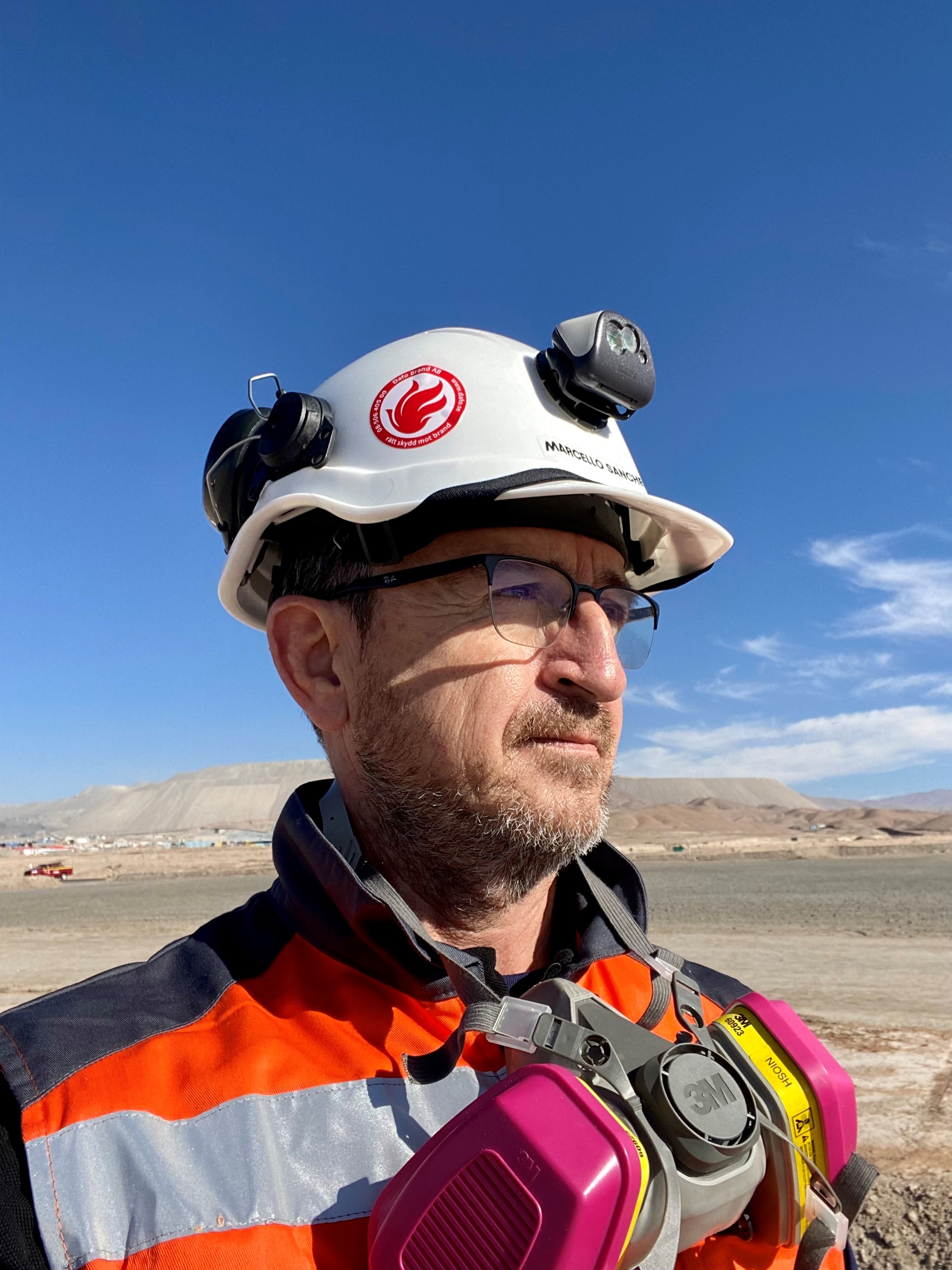
Credit: Dafo Vehicle Fire Protection
Emergency response and battery chemistry
Within a battery, heat is generated by the current flow and temperature management is influenced by the battery management system (BMS). The BMS monitors the mean temperature of the battery pack, temperatures of individual cells, as well as the intake and output coolant temperatures if coolant is used.
Typically, a high-temperature condition is the result of an external heat source, or the voltage and/or current being out of the operating range.
High internal temperatures can cause separator failure, leading to internal short-circuiting. For some chemistries, this can lead to a process called thermal runaway, which can ultimately cause venting of hazardous gases and flames and potential explosion of the battery assembly.
In thermal runaway, a battery also has the ability to produce its own source of oxygen, propagating the flames from within and self-sustaining the fire. This makes suppression using traditional measures particularly challenging, and addressing it effectively often requires a unique solution.
The key is to detect a potential battery failure, at the earliest possible stage, and take immediate action by cooling, using wet chemical suppression agent, for example. This will effectively stop, or delay, a potentially hazardous situation, preventing the fire from developing further.
As there is no current standardisation for batteries in BEVs, battery chemistries can vary, and special consideration is required when the vehicle is involved in an incident that structurally damages its battery or causes fire on the vehicle.
Facilitating low-carbon mines
In line with global sustainability targets, the mining industry is continually searching for eco-friendly alternatives to the combustion engine vehicles and diesel-powered machinery commonly used to fulfil intense work schedules.
The benefits of BEVs are arguably greater for underground mining than any other industry, as emissions, noise and heat generated from diesel engines can negatively affect the underground work environment.
Many mining businesses are now looking to BEVs as a sustainable alternative for onsite equipment, from production equipment – such as load hall dump machines and drilling rigs – to utility support equipment, such as scissor trucks, boom trucks and personal and service carriers.
The electrification of vehicles for underground mines presents a critical opportunity to reduce costs and enhance safety, reducing the need for expensive ventilation measures and improving the mine’s air quality for workers.
Minimising risks
Alongside the general best practice fire prevention measures implemented in mines, there are some key steps operators can take to minimise fire risk, including thorough risk assessment and effective fire suppression.
Regarding risk assessment, BEV equipment manufacturers should incorporate certain control measures into the design of electric vehicle batteries to enable the vehicles’ safe operation, minimising fire risk. They should also provide sufficient information to end-users, so they’re able to implement the appropriate emergency management strategies in the event of a fire.
Mine operators should also ensure any new process or equipment are firstly subject to a full risk assessment before integration into the site’s operations. This goes beyond looking at the vehicles or machines in isolation and towards considering the operating environment in its entirety.
This will give deeper insight surrounding the risks particularly pertinent in the specific context. This assessment should also consider the risks posed by the battery chemistry, covering all aspects of the battery lifecycle.
Regarding fire suppression, mine operators should ensure that risks can be effectively managed through the implementation of additional control measures to ensure maximum safety. Fire suppression solutions should be adapted and tailored for your individual site and its risks.
BEVs should have a fire suppression system that is appropriate for the vehicle type, according to the battery chemistry. Automatic systems should also be capable of manual activation by the BEV operator. Local mining regulations or site level risk assessments may also require an automatically activated system.
Fire-fighting information to train operators, mechanical and electrical personnel, and first responders should be provided by the equipment manufacturer.
For these manufacturers, effective fire suppression systems can be integrated into the manufacturing process, ensuring BEVs are protected, and relevant site regulations are met, from the outset. For operators, fire suppression systems can also be retrofitted to existing vehicles and machinery for operations and maintenance safety.
COMMENT