Boosting safety and productivity
in underground mines
wireless enabled electronic system with 2 way
communication capabilities
read interview
With many mine operations underground and in confined spaces, high safety standards are essential. Enaex offers a range of solutions to improve efficiency and safety in underground mining. The company is focused on automating mining to deliver value to clients and enable blasting with precision. MiNE Magazine spoke to underground director Danko Morales and key account manager Javier Alcaino about the services Enaex provides and how clients quickly see results.
Block caving mines can be particularly dangerous. What techniques are you using to create safe environments for workers?
DM: Within our company values, our priority is life. Our aim is always to increase safety in our processes, always with productivity in mind. Block caving undercut is a zone where the working conditions are complex, so we have our UBEX ONE truck with remote-operated arm. This enables us to reduce the amount of hours that teams spend in hazardous areas.
JA: We are always trying to reduce safety hazards inside mines. By understanding the customer’s needs and providing tailor-made solutions, we can improve both productivity and safety at the same time. The focus is always on safety, especially in the undercut level. And with the production blasting in a block caving mine, there's always this huge risk of rocks falling. That's why we developed this equipment, which you can operate remotely. The remote-operated arm can charge the drill holes from a safe distance – up to 10m away – so you don't have to be right next to the blasting front.
What would you describe as the main benefits of your Underground operations?
JA: We are able to deliver an increase in productivity in mines. As we understand the old way of doing things and are continuously generating improvements. In a block caving mine, when you do the undercut you first have to load the blast holes and you would get around 80% in efficiency for each blast. That means you remove 80% of the rock you wanted to. But with our emulsion, you can get up to 95% efficiency.. That's because we use the UBEX ONE and bulk emulsion in the blast holes.
What makes your Duoblast emulsion different to other products out there?
DM: It’s used both horizontally and vertically. The main benefit is that Duoblast is a high-viscosity emulsion, and this enables it to adhere to the blast hole walls. And the second benefit would be that gasification time - it's quite quick in comparison.
How does your underground booster improve blast efficiency?
DM: We developed this booster to initiate a blast underground. It works well with UBEX ONE specifically because it adapts easily to the blast holes. Also, it has a ballistic form, which allows the booster to arrive at the bottom of the blast hole, enabling a more efficient blast. It also has a safe-lock system, which avoids the initiation system inside the booster detaching during the blast. This eliminates the risk of misfires, i.e. when the blast doesn't happen.
JA: Through charging emulsion and using this booster, we can save up to a 40% in operational time and the efficiency is better.. The equipment is safer than manual operation, the emulsion gives you the efficiency, and it takes almost half the time.
Can you give some specific examples of where your products have been successful?
DM: We are currently servicing two of the biggest block caving mines in the world, located in Chile. We are using our technology on ascending shots, but also with horizontal development. In this case, we've developed 3,400m in block caving in mines, which is double what we have in the market in this area. And in this particular development, we've increased productivity, achieving 95% in blasting efficiency where the standard is generally 80%-82%. Also, we have decreased blast hole loading time by 30%. And the number of blast holes we needed to drill has also been reduced by 15%. We have been working at these sites for over two years. The teams were surprised by the results. In the undercut processes, we have worked at a new block caving mine site and when they first started operations, the engineering concluded that they would achieve around 4,500m2 per month, more than the 3,000m2 per month considered as a standard rate, so achieving 6,000m2 for them was much better than expected. Recently, we have achieved a production rate over 9,000m2 and blasted 21 drawbells in one month, which is a huge record for underground mining.
Are there any other factors that have contributed to these results? Has automation helped?
DM: We are going from manual to more automated operations, that’s a key benefit factor. Before, we required confirmation on walls safety and We needed to make sure that a lot of operations were safe because the people were working closer and operations were not automated. Now, operations times have been reduced by one third thanks to our technology, with UBEX ONE, underground booster, and the Duoblast emulsions. Another key success factor has been our agile approach for both projects and operations, which allows us to address our customer’s specific pains with operational and engineering teams on-site, in a quick and efficient way.
JA: The automation processes have improved safety and reduced operation times. And it’s not just safety in the blasting process, but also when you have to fortify the mine and check that everything's safe for people and equipment. All of this has been made easier now that we have this equipment. You can have really good equipment, you can have a lot of resources, but that does not ensure succes. Besides our products and technology, we were able to implement both projects and operations successfully because we had close supervision onsite and were always in communication with the customer. That was a key factor to improve the process and achieve this undercut record. It was a mix of service and products.
What are your future plans to improve safety and productivity?
DM: Our company’s purpose is to contribute to humanize mining through R&D, and avoiding our teams being exposed to high risk areas is vital. At the moment, we are working with remote-operated equipment. And the idea is to keep workers at a distance as much as possible. In the future, we are thinking of automation to ensure working in even safer environments. We are already working in better conditions with UBEX ONE truck remote-operated arm; using Duolex emulsion - which is a higher quality solution for horizontal or ascending blast shots. Additionally, DaveyTronic UG electronic initiation system has been designed for our underground requirements. On top of this, there are robotics developments All these different elements come together, giving us these positive results. And we are developing new tools, products and technologies to continue increasing productivity.
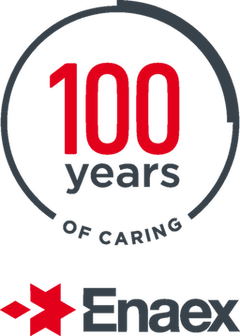
Boosting safety and productivity in underground mines
wireless enabled electronic system with 2 way communication capabilities
read interview
With many mine operations underground and in confined spaces, high safety standards are essential. Enaex offers a range of solutions to improve efficiency and safety in underground mining. The company is focused on automating mining to deliver value to clients and enable blasting with precision. MiNE Magazine spoke to underground director Danko Morales and key account manager Javier Alcaino about the services Enaex provides and how clients quickly see results.
Block caving mines can be particularly dangerous. What techniques are you using to create safe environments for workers?
DM: Within our company values, our priority is life. Our aim is always to increase safety in our processes, always with productivity in mind. Block caving undercut is a zone where the working conditions are complex, so we have our UBEX ONE truck with remote-operated arm. This enables us to reduce the amount of hours that teams spend in hazardous areas.
JA: We are always trying to reduce safety hazards inside mines. By understanding the customer’s needs and providing tailor-made solutions, we can improve both productivity and safety at the same time. The focus is always on safety, especially in the undercut level. And with the production blasting in a block caving mine, there's always this huge risk of rocks falling. That's why we developed this equipment, which you can operate remotely. The remote-operated arm can charge the drill holes from a safe distance – up to 10m away – so you don't have to be right next to the blasting front.
What would you describe as the main benefits of your Underground operations?
JA: We are able to deliver an increase in productivity in mines. As we understand the old way of doing things and are continuously generating improvements. In a block caving mine, when you do the undercut you first have to load the blast holes and you would get around 80% in efficiency for each blast. That means you remove 80% of the rock you wanted to. But with our emulsion, you can get up to 95% efficiency.. That's because we use the UBEX ONE and bulk emulsion in the blast holes.
What makes your Duoblast emulsion different to other products out there?
DM: It’s used both horizontally and vertically. The main benefit is that Duoblast is a high-viscosity emulsion, and this enables it to adhere to the blast hole walls. And the second benefit would be that gasification time - it's quite quick in comparison.
How does your underground booster improve blast efficiency?
DM: We developed this booster to initiate a blast underground. It works well with UBEX ONE specifically because it adapts easily to the blast holes. Also, it has a ballistic form, which allows the booster to arrive at the bottom of the blast hole, enabling a more efficient blast. It also has a safe-lock system, which avoids the initiation system inside the booster detaching during the blast. This eliminates the risk of misfires, i.e. when the blast doesn't happen.
JA: Through charging emulsion and using this booster, we can save up to a 40% in operational time and the efficiency is better.. The equipment is safer than manual operation, the emulsion gives you the efficiency, and it takes almost half the time.
Can you give some specific examples of where your products have been successful?
DM: We are currently servicing two of the biggest block caving mines in the world, located in Chile. We are using our technology on ascending shots, but also with horizontal development. In this case, we've developed 3,400m in block caving in mines, which is double what we have in the market in this area. And in this particular development, we've increased productivity, achieving 95% in blasting efficiency where the standard is generally 80%-82%. Also, we have decreased blast hole loading time by 30%. And the number of blast holes we needed to drill has also been reduced by 15%. We have been working at these sites for over two years. The teams were surprised by the results. In the undercut processes, we have worked at a new block caving mine site and when they first started operations, the engineering concluded that they would achieve around 4,500m2 per month, more than the 3,000m2 per month considered as a standard rate, so achieving 6,000m2 for them was much better than expected. Recently, we have achieved a production rate over 9,000m2 and blasted 21 drawbells in one month, which is a huge record for underground mining.
Are there any other factors that have contributed to these results? Has automation helped?
DM: We are going from manual to more automated operations, that’s a key benefit factor. Before, we required confirmation on walls safety and We needed to make sure that a lot of operations were safe because the people were working closer and operations were not automated. Now, operations times have been reduced by one third thanks to our technology, with UBEX ONE, underground booster, and the Duoblast emulsions. Another key success factor has been our agile approach for both projects and operations, which allows us to address our customer’s specific pains with operational and engineering teams on-site, in a quick and efficient way.
JA: The automation processes have improved safety and reduced operation times. And it’s not just safety in the blasting process, but also when you have to fortify the mine and check that everything's safe for people and equipment. All of this has been made easier now that we have this equipment. You can have really good equipment, you can have a lot of resources, but that does not ensure succes. Besides our products and technology, we were able to implement both projects and operations successfully because we had close supervision onsite and were always in communication with the customer. That was a key factor to improve the process and achieve this undercut record. It was a mix of service and products.
What are your future plans to improve safety and productivity?
DM: Our company’s purpose is to contribute to humanize mining through R&D, and avoiding our teams being exposed to high risk areas is vital. At the moment, we are working with remote-operated equipment. And the idea is to keep workers at a distance as much as possible. In the future, we are thinking of automation to ensure working in even safer environments. We are already working in better conditions with UBEX ONE truck remote-operated arm; using Duolex emulsion - which is a higher quality solution for horizontal or ascending blast shots. Additionally, DaveyTronic UG electronic initiation system has been designed for our underground requirements. On top of this, there are robotics developments All these different elements come together, giving us these positive results. And we are developing new tools, products and technologies to continue increasing productivity.