WATER MANAGEMENT
Brine & brackish: improving the efficiency of mine water management
Existing treatment techniques for brine and brackish water at mines are very energy-intensive, and only cover around 80% of brine. But MaxH2O, a membrane-based water treatment system developed by IDE Technologies, can increase recovery by up to 98% and uses far less energy than other methods during the process. Scarlett Evans finds out more.
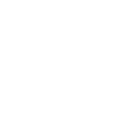
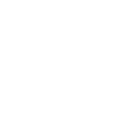
Mining’s relationship with water is a historically contentious one. Fears over high rates of water usage and possible contamination from operations means that ensuring sustainable and effective water treatment systems is often at the forefront of project planning. Such issues also arise when it comes to the processing of brine and brackish water - that is, water that has a higher concentration of salt than freshwater, but not as much as seawater.
These high levels of salt and other possible contaminants make the water both environmentally damaging and difficult to treat. Operations are barred from releasing these into the surrounding environment without first properly treating it, and these requirements are becoming increasingly stringent. In such a climate, sustainable and economical alternatives for water processing are coveted, and IDE Technologies’ believes its membrane technology is just what industry members are looking for.
More than half of the country’s coal mines are managed by pro-Russian separatist militia.Credit: DmyTo/Shutterstock.
More than half of the country’s coal mines are managed by pro-Russian separatist militia.
Credit: DmyTo/Shutterstock.
Treatment challenges
Speaking with Matan Alper, product manager at IDE Technologies, he says that regulations on water treatment are only getting tighter, with sulfates in particular deemed a significant problem for long-term water quality.
“Since regulations are becoming stricter, in recent years many jurisdictions have added low limit sulfates as a regulated parameter,” he says. “Adhering to these regulation limits when addressing typical mine impacted water (MIW) composition after high density sludge (HDS) or lime treatment, poses a major challenge for mining companies as they limit all life phases of mines: operation, closure, expansion, etc.”
Alper says that the mining industry is considered to be the fourth largest industrial user of water during daily operational activity, and its importance through every stage of a project’s life means dealing with it appropriately is both a financial and environmental necessity. Indeed, adequately processing it has globally seen increased interest in recent years.
“This regulatory challenge is bringing more and more mining operations to focus on efficient water management plans,” he says. “In many cases [the miners] present these plans to the local authorities before they can operate, expand, or even close their mine.”
“Surpassing 50% recovery is not possible without colloguing and scaling the membranes.”
When it comes to brine and brackish water, the main objective of processing is to remove dissolved sodium ions from the salt in the wastewater, with additional treatment occasionally needed to remove other contaminants such as metals and ions. While HDS has been the standard process for treating metal-containing acid rock drainage, newly introduced regulations on sulfate discharge levels mean this method is no longer practical in large-scale units.
Two main methods currently exist for removing sulfates from MIW or acid mine drainage (AMD): membrane separation through reverse osmosis, and salt or chemical precipitation. Yet Alper says that both of these methods are expensive, and only offer limited water recoveries.
“When trying to implement a conventional reverse osmosis membrane system, surpassing 50% recovery is not possible without colloguing and scaling the membranes,” he says.
Another main challenge is the buildup of gypsum (a soft sulfate mineral) on membranes, which requires a large amount of chemicals to remove and significantly reduces the membrane’s service life. IDE's MaxH2O Desalter technology works to address such challenges.
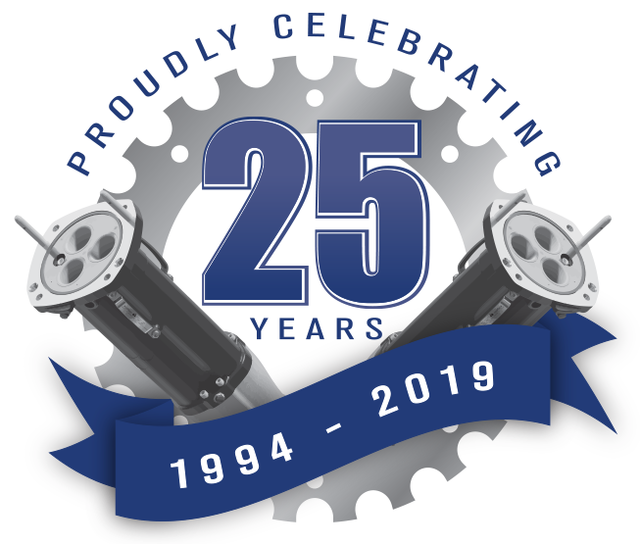
AusProof is celebrating 25 years of business in Australia in 2019.
IDE’s solution
Combining reverse osmosis membrane technology with an integrated salt precipitation unit, IDE's MaxH2O removes any unwanted impurities in the water by sifting it first through a feed tank, and then through a fluidised bed pellet reactor.
“The first stage in the MaxH2O Desalter system includes pretreatment of the MIW or AMD, which is an optional stage that depends on water quality,” says Alper. “This is designed to remove the main organic loads present in the water. Water then flows to one of two feed tanks, where one tank is always in operation while the other discharges brine from the previous cycle.”
After antiscalant has been dosed, the water flows to enter the reverse osmosis stage. Brine produced in this stage is then cycled through the fluidised bed pellet reactor.
“We can reach extremely high recoveries but at a lower energy due to the energy recovery integration.”
One benefit of this process is the lack of waste produced. While most existing methods produce sludge, which then requires further treatment, the dry pellets produced by IDE’s technology require no further chemical processing.
“The pellets are 90% dry solids so no dewatering systems and handling are required – we only use antiscalant and sometimes sodium carbonate in the system,” says Alper. “Maintenance is also quite low since the membranes are never put in a potentially high-scaling environment. The combination of these factors reduce MaxH2O's operational expenditure by two to three times compared to competing technologies.”
Another major benefit is the lack of energy used by IDE’s solution. The reverse osmosis stage can also perform with an energy recovery unit that lowers energy consumption even further, allowing the user to recover much of the brine’s energy and send it back to the reverse osmosis feed.
“We designed the system to use an energy recovery system (such as a turbocharger) which saves substantial amounts of energy, especially when reaching osmotic pressure and salinity,” says Alper. “So, we can reach extremely high recoveries but at a lower energy due to the energy recovery integration.”
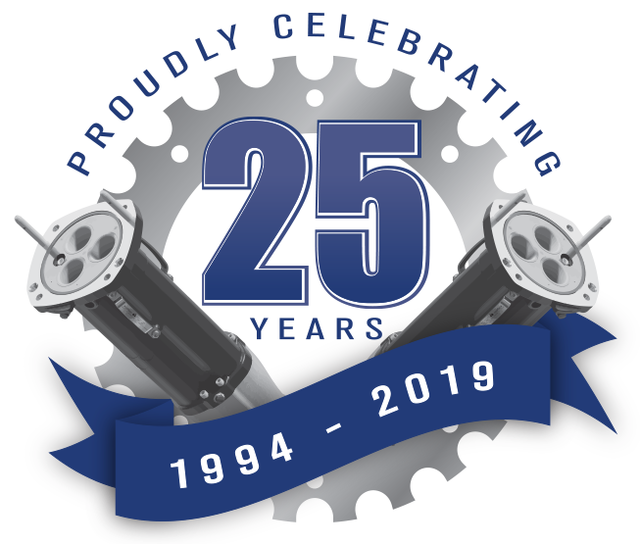
AusProof is celebrating 25 years of business in Australia in 2019.
The future of water treatment
IDE’s technology can be integrated as a standalone solution or as a downstream solution for lime neutralisation systems, and is ideally suited to treat mine impacted water, acid mine drainage, and tailing ponds challenges. Now that the technology in place, IDE is expecting the market to only become more favourable as time goes on.
“In recent years, we’re seeing that new mining projects have gradually given way to resource recovery projects, where lithium and other metals are recovered from the surface in the form of soft coal or coal waste,” Alper says. “As a result, a momentous ramp-up is expected in the widespread introduction of water treatment involving membrane technologies to the global mining sector.”
“The need for more efficient and economical water treatment is evident and more pressing than ever before.”
Alper estimates that properly implemented water management programs could allow up to 40% savings in miners’ daily freshwater intake. Depending on quality, over 90% of mining wastewater could be reused by applying advanced treatment technologies.
“As the scope of the mining industry grows, quarried substances demand is on the rise and environmental regulation is tightening,” Alper adds. “The need for more efficient and economical water treatment is evident and more pressing than ever before.”
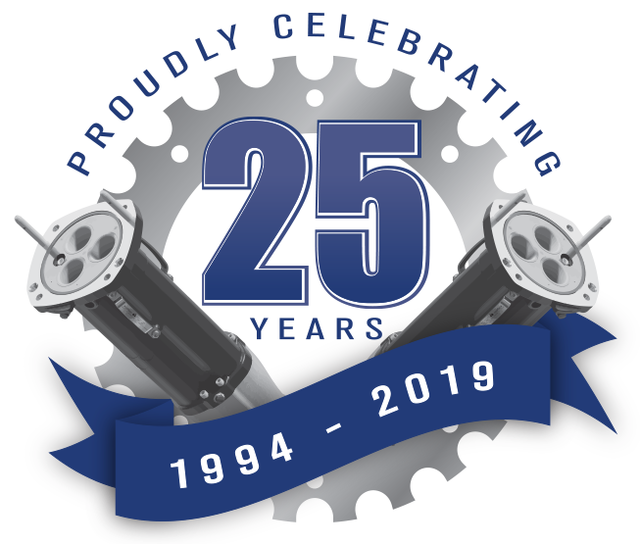
AusProof is celebrating 25 years of business in Australia in 2019.