Feature
Autonomous mining: Australia leads in adoption and safety regulation
Australia adopted autonomous mining equipment early and has taken a proactive approach to safety regulation. We look at the state of autonomous mining and what’s next.

An autonomous haul truck drives through a pit at Rio Tinto Group's West Angelas iron ore mine in Pilbara. Credit: Ian Waldie/Bloomberg via Getty Images
Australia’s miners were early adopters of autonomous technology on mine sites. In 2016, Rio Tinto’s Yandicoogina and Nammildi mines in Western Australia (WA) became the first in the world to use driverless trucks to transport iron ore.
The foundations for good policy were set early, as state regulators saw the growing technological capabilities on the horizon, and responded by publishing codes of practice and guidelines that miners and mine operators must adhere to when using autonomous technology.
In 2015, before Yandicoogina and Nammildi rolled out their first automated trucks, WA’s Department of Mines and Petroleum released the Code of practice for safe mobile autonomous mining in Western Australia, which provides guidance on mobile autonomous and semi-autonomous systems used in surface and underground mines and quarries, with a focus on developing and evaluating safe work procedures for such systems. The code of practice details their risk management approach, general hazard controls and emergency preparedness.
Other states weren’t as quick to develop their guidelines, but over time built upon the standards set by WA.
New South Wales (NSW) government agency NSW Resources Regulator published guidelines in September 2020, covering legislative requirements and risk controls of autonomous mobile mining plants.
Resources Safety & Health Queensland published the Queensland guidance note on autonomous mobile machinery & vehicles introduction & their use in coal mining in January 2022 which, similar to WA’s code of practice, covers the safety and risk management process as well as information, training, and system planning and design for hazard control and safety integrity.
Autonomous equipment in Australia’s mine sites
According to the most recent data collected by GlobalData’s mining Intelligence Centre, there are 1,962 tele-remote control or autonomous pieces of equipment worldwide, of which 907 are in Australia.
Sandvik is the leading OEM in tele-remote control and autonomous underground mining trucks and loader, haulers and dumpers (LHDs) with an estimated 67% market share, followed by Caterpillar with 18% and Epiroc with 13%.
The most popular models are Sandvik’s LH621 and LH517, according to GlobalData’s report Development of tele-remote and autonomous equipment in the underground mining sector. Caterpillar released a video campaign in December 2022 promoting its real autonomous machines on mine sites making autonomous projects a reality with an autonomised fleet.
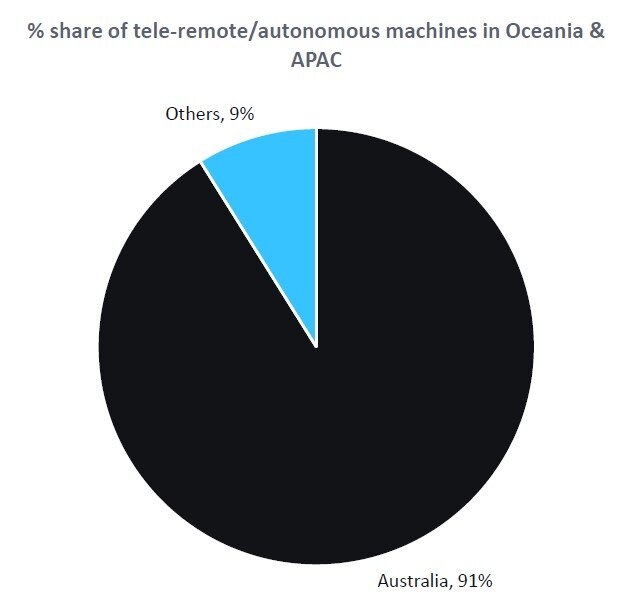
Source: Globaldata
One of the challenges to a wider rollout of autonomous equipment is related to the workforce. The industry requires upskilled workers with less need for traditional operators, and more need for specialised workers in mine planning, process engineering and automation.
Policies that govern the implementation of automation on mine sites have been followed, resulting in lower safety risks for operators by removing the hazards during man-powered operation.
Autonomous technology providers are seeing heavy adoption
GlobalData’s report reveals that Sandvik’s AutoMine autonomous system, used for single loaders or trucks, holds over 50% market share in autonomous technology.
Sandvik says this technology is particularly suitable for mining operations with challenging environments such as sub-level caving, transfer levels, or individual block caving drives. The system offers intelligence teleoperation with operating assisting automatic steering, the company says, with benefits including improvements in productivity, reduction in operating costs, increased machine utilisation and increase in total operating time.
Sandvik says it ensures the highest quality testing at its state-of-the-art test mine providing real mine conditions for rapid prototype testing and being verified in underground equipment quality assurance.
Roy Hill’s smart mine
Roy Hill, a large iron ore mining operation in Western Australia’s Pilbara region and one of the world's largest autonomous mines, transitioned its entire fleet of 96 conventional haul trucks to driverless operation starting in March 2023.
Partnering with Epiroc and ASI Mining, Roy Hill developed an autonomous haulage system that interacts around the clock within dedicated autonomous operating zones with excavators and ancillary vehicles.
The fleet includes Caterpillar and Hitachi trucks and modified ancillary vehicles. Roy Hill's success was seen as a milestone for the broader mining industry's adoption of autonomous technology. To help its workforce embrace the changes, Roy Hill has implemented re-skilling programmes for truck drivers, offering new roles within the company to adapt to automation.
Is the mining industry ready for the next stage of autonomous technology?
From promising early adoption of autonomous technology, what’s next for the industry?
Moving from level 4 autonomous technology to level 5 fully self-driving vehicles represents a major technical leap. A Level 5 vehicle must be able to act safely in any scenario in any location.
GlobalData views this as a very distant prospect, not likely before the mid-2030s at the earliest. Solving the challenges presented by level 5 autonomous vehicles may be one of the most difficult tasks in all applications of emerging AI technologies and their machine learning approach.
State regulators must build on the good examples they set in the infancy of mine automation and continue to update policies, working with accelerating technological advances to ensure ongoing productivity, and safe procedures for workers.