Company Insight
Sponsored by Kemppi
The right welding solutions can help drive quality, efficiency and productivity on mine sites
Standfirst...
On the move with the portable Kemppi MinarcMig 220 Auto.
Mining in Australian is key to the local economy and its robustness. In 2023, the mining industry accounted for around 13.6% of Australia’s GDP, and as the world economy rebounds from the impact of the COVID-19 pandemic, the outlook for the sector continues to soar.
To meet the growing international demand for Australian minerals, mining operations pursue practices that make them more efficient and productive.
In particular, high-tech mining equipment and ancillary tools such as welding machines, that can maintain and repair existing infrastructure and heavy equipment without denting the bottom line, are in demand.
Further, the right welding tools can help mining operations experience increased efficiency and productivity, and quality welds.
Kemppi is a pioneer, global designer and manufacturer of intelligent welding equipment and welding management software. Kemppi solutions meet both demanding industrial applications and ready-to-weld needs to empower professional welders to help boost productivity and quality.
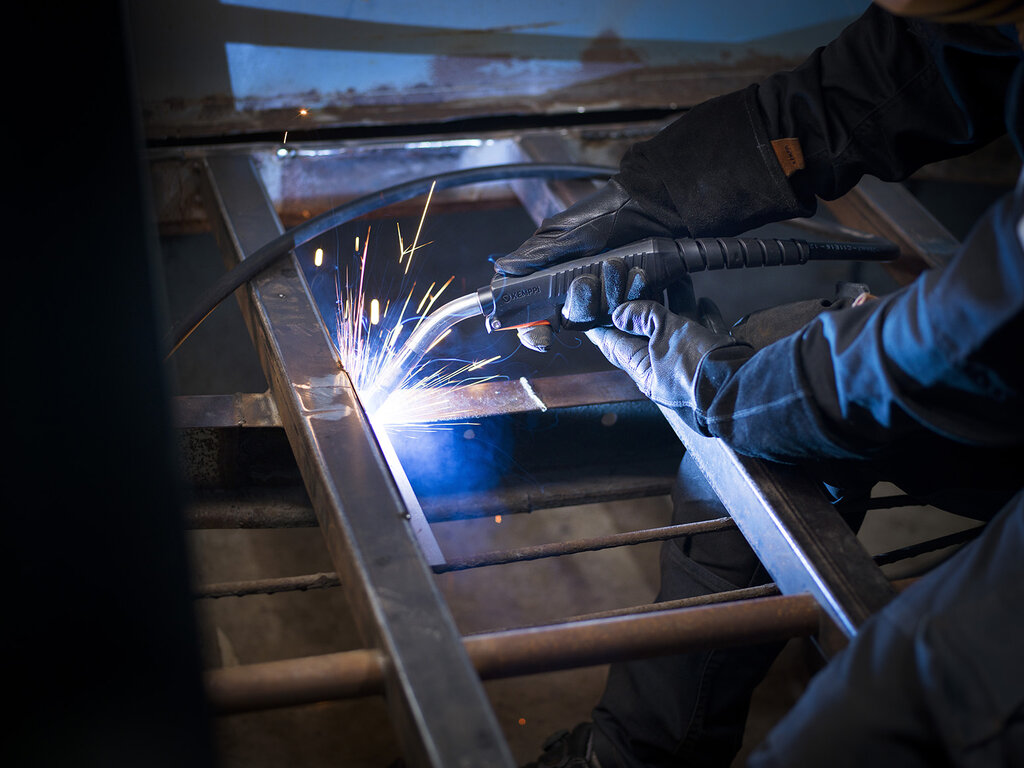
At work with the MinarcMig 190 Auto and the Flexlite GC 223 welding torch.
Introducing the Kemppi MinarcMig 190/220 Auto welding machines
Kemppi recently launched the MinarcMig 190 and 220 Auto welding machines which are ideal for the professional welder working around the mine site and/or in the mine’s maintenance workshop.
The MinarcMig 190 and 220 Auto deliver portable MIG/MAG welding power, offering 190 amps at a 35% duty cycle or 220 amps at a 20% duty cycle from a 15A, 1-phase power supply.
According to Kemppi Australia’s Sales Director, Stuart Orr, “Kemppi's MinarcMig 190/220 Auto welding machines are the epitome of compact power and precision. The new MinarcMig’s not only streamline welding tasks, but also elevate productivity and quality, ensuring every welder achieves superior results with ease.”
Key Features of the MinarcMig 190/220 Auto
Portable and lightweight
Small and lightweight, the MinarcMig 190 and 220 Auto models are fully portable so that welders can carry them anywhere and quickly move to where they need to be. Plus, the small size of the portable welders makes it easier for them to stand, squat or kneel to access and complete welding tasks.
Fast and easy set-up
Both models have been designed to be very easy to set up and operate to help boost productivity. An intuitive and user-friendly interface makes operating the machines simple. It guides welders through the process, leaving no room for guessing.
In addition, the welder can choose to use the Auto setting to simplify the welding process to help increase productivity. The welder just selects the material type and plate thickness and welds in auto mode.
Weld various metals
Robust and built to last, the MinarcMig 190 and 220 Auto models are compatible with various materials including steel, stainless steel, aluminium and CuSi brazing filler wires, so that the welder can do more with one machine.
Quality welds
Powerful and highly reliable, both models also feature an adaptive arc regulation system to ensure precise welding quality and accurate ignition. These help to minimise spatter and create high-quality welds. The need for post weld cleaning is reduced, saving time and money.
Excellent welding ergonomics
The Auto packages also help minimise downtime while increasing the welder’s arc-on time at the mine site or in the maintenance workshop. The Auto package includes the 3-metre Flexlite GC 223G welding torch, which has an ergonomic and anatomically shaped gun handle, and the improved cable is more flexible. Together, these features ensure a natural wrist position regardless of the welding position, leading to effortless, ergonomic and less muscle-loading work.
Energy efficiency and optimum welding utility
Built using PFC power source technology, both models offer the ultimate energy efficiency with a power factor of 0.99. Plus, they have been designed to be used with long power extension cables of up to 100 metres, allowing for optimum welding utility on mine sites.
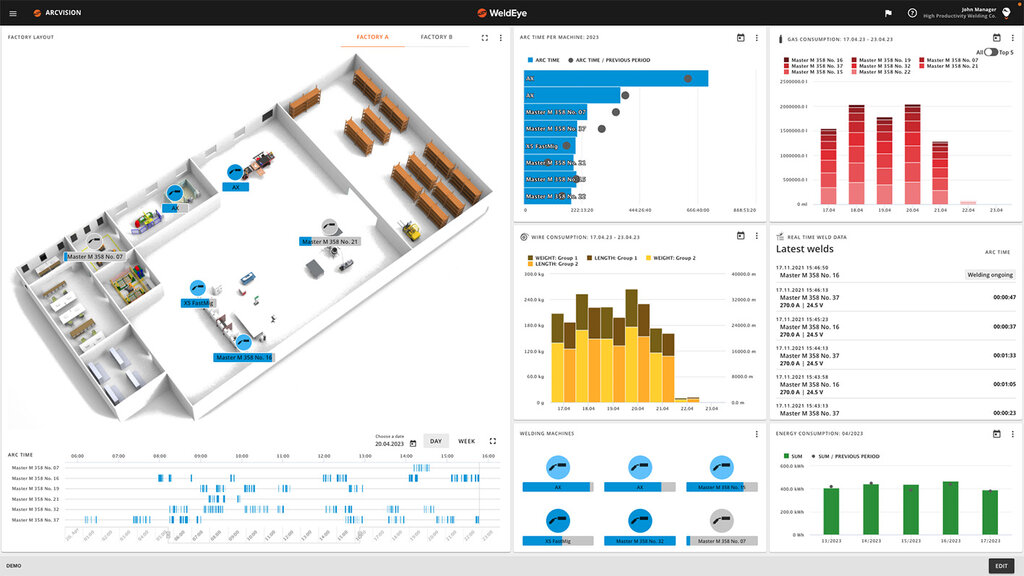
Snapshot of WeldEye.
Introducing the Kemppi WeldEye welding software solutions
In addition to world-class welding machines, Kemppi also offers a suite of leading software solutions under the WeldEye brand which optimise welding production on mine sites. WeldEye solutions let mining management analyse welding data, monitor quality, and identify areas of high performance and those for improvement.
With WeldEye, mining operators can track the performance of the welder and see who is welding where, when and how. The software also lets users trace individual welds, their quality and ensure they comply with the welding procedure specifications. Management is notified of any welding deviations for real-time rectification. In addition, WeldEye also lets welding supervisors keep track of their welder’s qualifications and whether they need updating.
This data-driven approach enables real world optimisation and quality control for improved working efficiency on mine sites. Welders and management can make informed decisions based on accurate data and reference materials to reduce errors and rework, and enhance overall welding performance, productivity and quality.
To embrace the latest in state-of-the-art welding equipment and software solutions contact Kemppi Australia.
Contact information
Kemppi Australia
2,463 Victoria Street,
Wetherill Park NSW 2164
Tel.: +61 2 8785 2000
Email: sales.au@kemppi.com
Web: www.kemppi.com