In 95% of these reliability projects, the first question is:
“How do we improve reliability?”
The second question is usually “How long is it going to take?” followed quickly by “How much is it going to cost?”
Some are hoping for a silver bullet that will solve all reliability problems, even overnight in some cases.
I tell them the truth…there is no magical checklist or a silver bullet that can improve reliability quickly and sustain it over time. There are many factors that determine how long an improvement will take.
Two of the most important factors to consider when beginning a mine reliability improvement journey are:
- Technical
- Cultural
More than half of the country’s coal mines are managed by pro-Russian separatist militia.Credit: DmyTo/Shutterstock.
More than half of the country’s coal mines are managed by pro-Russian separatist militia.
Credit: DmyTo/Shutterstock.
Technical
Improving maintenance comes down to doing two things cost-effectively, they are:
- Reducing the amount of repairs
You have to prevent failures through better essential care and condition monitoring practices. These practices include lubrication, alignment, balancing, operating procedures, quality repairs, doing root cause elimination of failures, etc.
We’ve created an 8-step video and guide to improved Preventive Maintenance – Get yours today!
Get your FREE 8-step guide to improved Preventive Maintenance
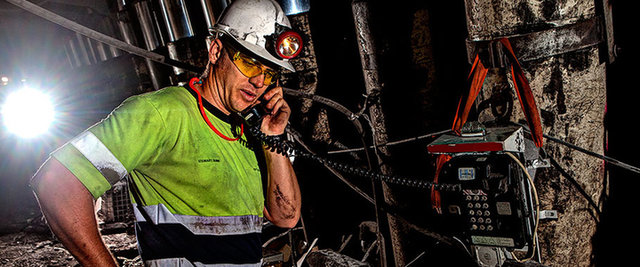
2. Effectively execute repairs
This can only be accomplished with disciplined execution of a work management process. In short, the mine needs to:
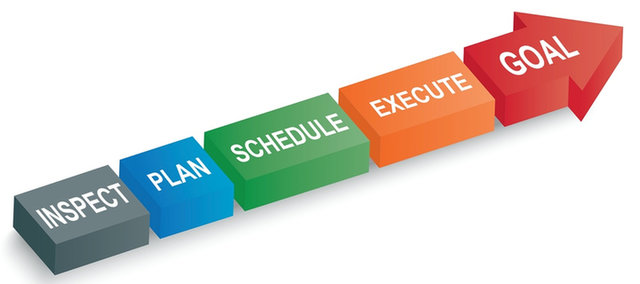
Figure 1: Effective reliability and maintenance management work must include adherence to these key elements.
Work management must come early in improving reliability for the simple reason that all maintenance work, including lubrication, repairs, improvements, will go through the work management process.
If you don’t have basic work management processes in place- start now! It will prioritize and structure all maintenance work.
Figure 2: Overall workflow for Work Management Planning and Scheduling. If your mine hasn't identified these processes, you need to do this before starting a reliability project.
Do you have workflows for all the key reliability and maintenance processes at your mine? Do they identify the activity, outcomes and who is responsible, accountable, consulted and informed (RACI)?
Need help developing or improving your workflows? Give us a call or click below to email us.
Cultural
The cultural factor is more important and often overlooked. Successful reliability and maintenance improvement projects have the following:
- A mine management team (Mine-manager, Operations manager, and maintenance manager) DRIVING the improvement of work processes forward with a constant purpose.
- A mine team that accepts the direction of leadership and implements the direction on the floor.
Maintenance improvements is 90% about people and their behavior.
People don’t mind change, but they don’t like being changed. When your mine is ready to improve your overall reliability, you must involve frontline people early in the project. You should involve them in deciding where to start the reliability improvement project.
Example: If you have buy-in to start condition monitoring, but hesitation around work management, perhaps you start with condition monitoring to get the momentum going.
Where do I suggest you start improving reliability and maintenance? If you don’t have work management or condition monitoring processes under control and working effectively, that’s where I’d begin.
One final note, if you don’t know how well your organization is performing basic reliability and maintenance processes, it’s a good idea to have an assessmentcomparing your current practices with best practices.