Feature
The role of technology in mine safety and rescue
The risk of serious injury and death is a sad reality in mining, but technology can help reduce accidents and improve emergency response. Andrew Tunnicliffe reports on innovation in mine safety and rescue.
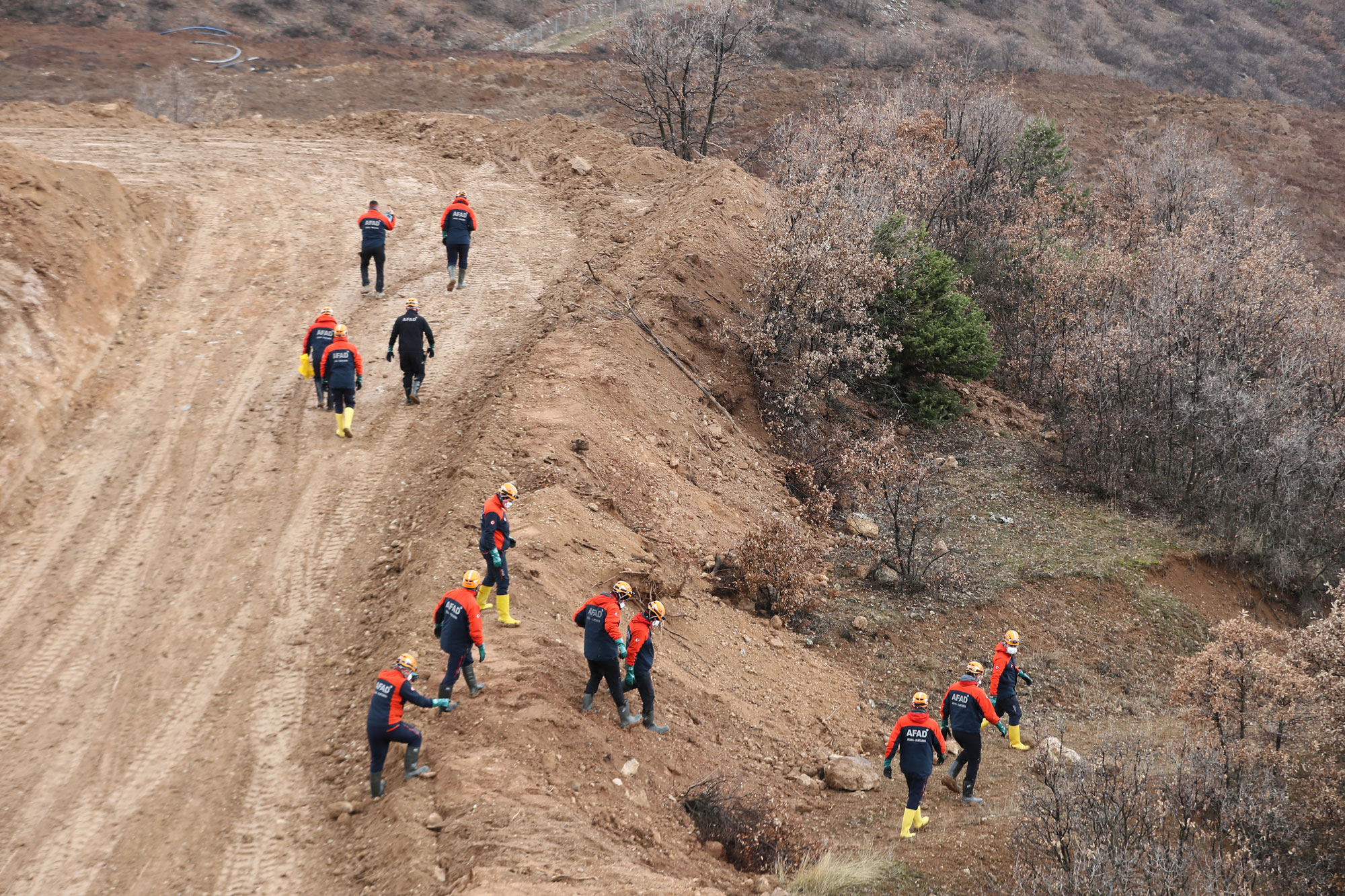
Rescue efforts in the wake of a landslide at a Turkish mine in February 2024. Credit: Turkish Disaster and Emergency Management Presidency/Handout/Anadolu via Getty Images
mining is fraught with risk. Although advances in safety, operational practices and regulation have helped to significantly lower the number of fatalities in mining over past decades, accidents – including fatal ones – remain a risk for miners around the world.
In mid-March, as rescue teams retrieved the body of a 37-year-old Australian miner at the country’s Mount Clear gold mine following an underground collapse, recriminations had already started. The incident – which involved the rescue of 28 trapped workers and left another miner fighting for his life – “should have been avoided”, according to Australian Workers Union Victorian Branch secretary Ronnie Hayden.
He alleged the crew was manually drilling in conditions they should not have been required to. “This form of air-legging shouldn’t be used to do this type of work” he said, suggesting it was being conducted on unsupported ground.
Despite the evolution of enhanced safety procedures, more robust regulations and an abundance of new technologies, the mining industry has not yet been able to eliminate fatalities. In the US, the Labor Department last year said a total of 42 miners had died, up 31% year on year, describing the number as ‘troubling’.
Mine safety is a multi-dimensional issue
“Each mining subsector, and in fact each mine, faces unique challenges related to health and safety,” explains a member of the US National Institute for Occupational Safety and Health (NIOSH) Mining Program’s leadership team. “While some hazards in the industry are well characterised with known controls, health and safety risks in mining, as well as our understanding of these risks, are dynamic.”
There are numerous factors at play in creating safe mines and mining practices: stringent and appropriate regulations, good mine management, a skilled and well-maintained workforce, and putting health and safety above all else. Technology is an integral part of this critical structure, if correctly employed.
“While many potential health and safety risks in the industry have remained relatively unchanged… there are also risks that have been both mitigated and introduced through the implementation of changes in mining processes and adoption of new technologies,” says the NIOSH team.
While some hazards in the industry are well characterised with known controls, health and safety risks in mining, as well as our understanding of these risks, are dynamic.
It is without doubt that technological advances are playing a significant role in addressing safety fears. But as NIOSH highlights, their successful implementation requires buy-in from employees, supported by enhanced training, adequate transition time, and an evaluation of health and safety impacts.
NIOSH is working with industry and partners, at home and internationally, to better understand the role the newest technology can play, with a comprehensive understanding of both the benefits and potential risks it brings.
A particular focus is on the ability of wireless systems to satisfactorily function and ‘coexist’ in the presence of other wireless systems, NIOSH says, with the hope of developing a framework that could be used for assured autonomy, that is, “the ability of autonomous equipment to safely operate in the presence of humans”. The team says automation has the potential to reduce incidents by removing workers from hazardous situations in or near equipment.
Remote and autonomous technologies for search and rescue
One area where automation and remote operations is having an impact is mine search and rescue.
We’re all too familiar with news of miners trapped for hours, days and sometimes evens weeks – all the while rescuers and loved ones are above ground, acutely aware of the perils delayed access to them can bring. Events at the San Jose copper mine in Chile back in 2010 – where 33 men waited months to be rescued – highlighted the risks miners face on every shift. That now infamous, albeit successful, rescue was just one of many where workers have faced an uncertain wait.
More recently, eight miners’ bodies were found days after a flood at the Perkoa zinc mine in Burkina Faso. Caused by unexpected rains during the country’s dry season, the incident led to the involuntary manslaughter convictions of two senior managers working on behalf of Canadian mining company Trevali. And in mid-February, nine miners were reported trapped at the controversial Üçler gold mine in Türkiye’s eastern Erzincan province following a landslide.
With capabilities such as infrared cameras and thermal imaging, drones can locate personnel, potentially cutting down on the time it takes to begin a rescue.
These incidents once again highlight the dangers faced by miners and the difficulties rescue teams encounter. But technology is helping, as was the case in Türkiye, where officials were at pains to point out drones had been used as part of their efforts to locate the victims. Headed by a team from the country’s Disaster and Emergency Management Authority, rescuers used at least five drones as part of their search efforts.
With capabilities such as infrared cameras and thermal imaging, drones can locate personnel, potentially cutting down on the time it takes to begin a rescue. They are only helpful in some circumstances, though. When an incident occurs out of the reach aerial vehicles, other technologies are needed, including robots which can go where rescuers can’t – often a collapse or explosion can make environments unsafe due to limited space, a lack of oxygen, the presence of dangerous gasses or poor visibility.
Safety and rescue technology for hazardous environments
As well as offering the potential to find lost miners and even report back on their physical condition through cameras, communications and sensors, robots can map the mine to provide an insight into its condition, such as compromises to structures.
Many mines are now equipped with networks of sensors providing data from multiple sources such as light, temperature, motion, pressure, and even weather conditions. The most common sensor types are temperature, pressure, proximity, optical, accelerometers and gyroscopes, according to industry intelligence provider GlobalData.
Mining Technology’sanalysis of innovation in mine sensor networks, based on GlobalData research, reveals that “activity is driven by improved computing power and connected sensors to control and monitor the mining environment. In the last three years alone, there have been over 62,000 patents filed and granted”.
The most common sensor types are temperature, pressure, proximity, optical, accelerometers and gyroscopes.
These sensors are also becoming commonplace on miners through wearables like hard hats or other clothing, glasses, badges and watches. Connected through real-time location services (RTLS), largely RFID and a network of sensors, they track the movement of individuals during a shift and provide improved location data in the event of an incident, meaning there’s a greater chance of reaching miners more quickly. Key players in this technology area include Sandvik’s Newtrax, Epiroc and GroundHog.
However, regardless of which RTLS system is used – and there are a few variants – they need to be able to communicate with each other, largely via the Wi-Fi networks NIOSH spoke of.
“Some of the highest impact technologies have been proximity detection and improvements to tracking/texting underground and on surface,” explains the Society for Mining, Metallurgy and Exploration’s Kimberly Walster, CMSP.
“Expanding Wi-Fi capabilities helps miners with communication and access to data in real time. With advances in technology, the capability of our control room has greatly improved. Anytime we can decrease the physical labour aspect, there is the potential for injury avoidance.”
Once trapped miners are located, technology can also assist with their rescue. According to GlobalData, Sandvik, Epiroc, Atlas Copco and POSCO E&C are among the leading innovators (based on the number of patents filed) in emergency rescue systems.
One such technology is Sandvik’s OptiMine Evacuation Assistant, which can locate personnel, visualise an evacuation, and send people to the nearest safe place or rescue chamber based on the location and capacity of those chambers. Epiroc’s Mobilaris system can also navigate workers to their closest rescue chamber.
Workforce training is an essential component of safety
While technology plays a crucial role in mine safety and rescue, both NIOSH and Walster stress that relying on such equipment alone isn’t enough; worker training is critical.
“While technology is great, you cannot rely on it at all times,” Walster says. “Employees need to be comfortable with technology, but capable if it’s not functioning. For example, proximity should not be considered as a standalone safety device, but a training tool to stay out of red zones. Awareness is key.”
Employees need to be comfortable with technology, but capable if it’s not functioning.
The NIOSH team adds that automation can introduce new risks as workers interact with automated equipment. They say operators would benefit by continually evaluating, monitoring, and improving health and safety management systems to address existing, priority, and emerging risks, including effective training as a key component.
As the events at Mount Clear once again illustrated, the risk of death is never far from the thoughts of the world’s mining community. But with continued innovation in safety and rescue equipment, along with improvements in workforce training and awareness, the mining industry is working on all fronts to reduce the frequency of deaths and serious injury.