Company Insight
Sponsored by Martin Engineering
True Cost of Material Spillage
Standfirst
If there’s a hole in your bucket, you’ll inevitably end up with four distinct but related dilemmas: less of whatever you had in the bucket before, a mess, another chore and less time to do what you set out to do in the first place.
Needless to say, using a bucket without a hole in it is far more efficient and productive than using a bucket with a hole in it. So, if you find that your bucket has a hole, how long do you wait until you either plug the hole or replace the bucket?
Quick Fix or Proper Solution?
Oftentimes, our propensity for shortsightedness and drive to keep our head down and push forward, particularly in the face of adversity, gets the best of us. As our bucket starts leaking, we simply pick up our pace and start walking faster. We’d serve ourselves better to pause, evaluate the situation, recognize the dilemmas we’re walking into, and take corrective action early to avoid catastrophe. We’re faced with the challenge, or opportunity, to choose the quick win, the small victory, and keep things moving or to focus on the long view and set ourselves up to reap the rewards of continued, long-term success.

Caption. Credit:
When we realize that an operation’s conveyor system has a hole in it — an underlying issue causing fugitive material — we’re faced with this opportunity. The dust or material spillage could be caused by:
- inadequate belt support and/or sealing at the transfer point.
- lack of proper chute work to allow the transferred material and airflow to settle.
- a belt that’s mistracking.
- a belt not being cleaned to prevent carryback on the return run.
Whatever “hole" the conveyor has, the earlier it is addressed, the less severe the impact of the inevitable dilemmas will be.
Dilemma #1: Where’d it go?
A conveyor system that suffers from material spillage has an immediate and continuous impact on production. Material lost moving from point A to point B lowers throughput, requiring more time and effort to meet production goals.
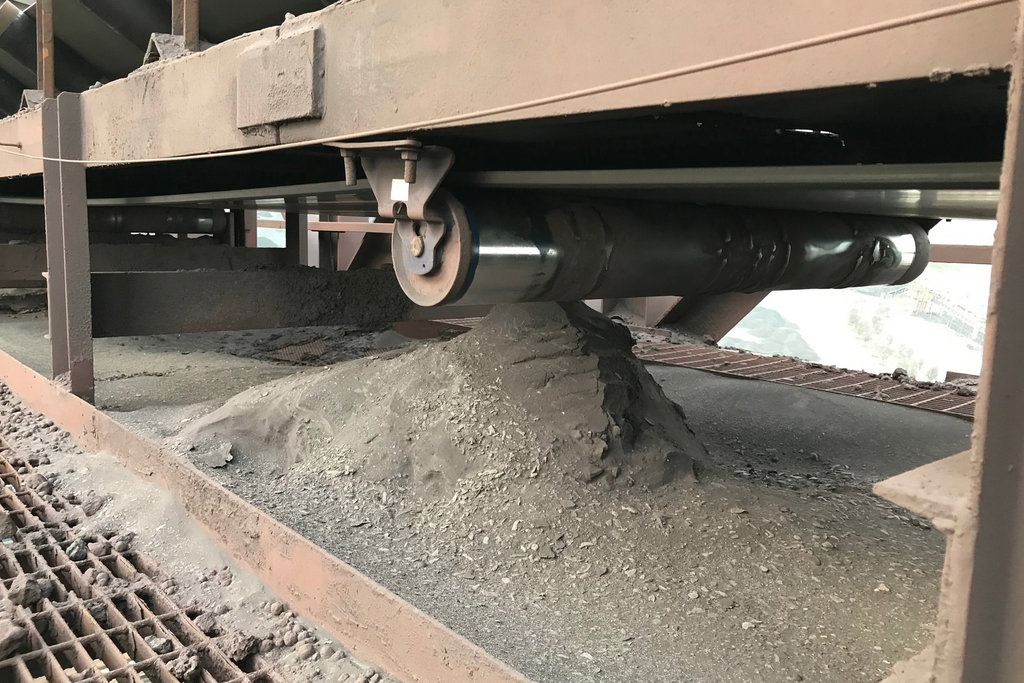
Caption. Credit:
Dilemma #2: There it is
That lost material creates a mess, and that mess continues to grow directly in relation to the loss in production. Not only is the material not getting where it needs to go, but it’s also creating safety and health hazards as well as costly damage to the belt, conveyor structure, and surrounding equipment. The problems are compounding.
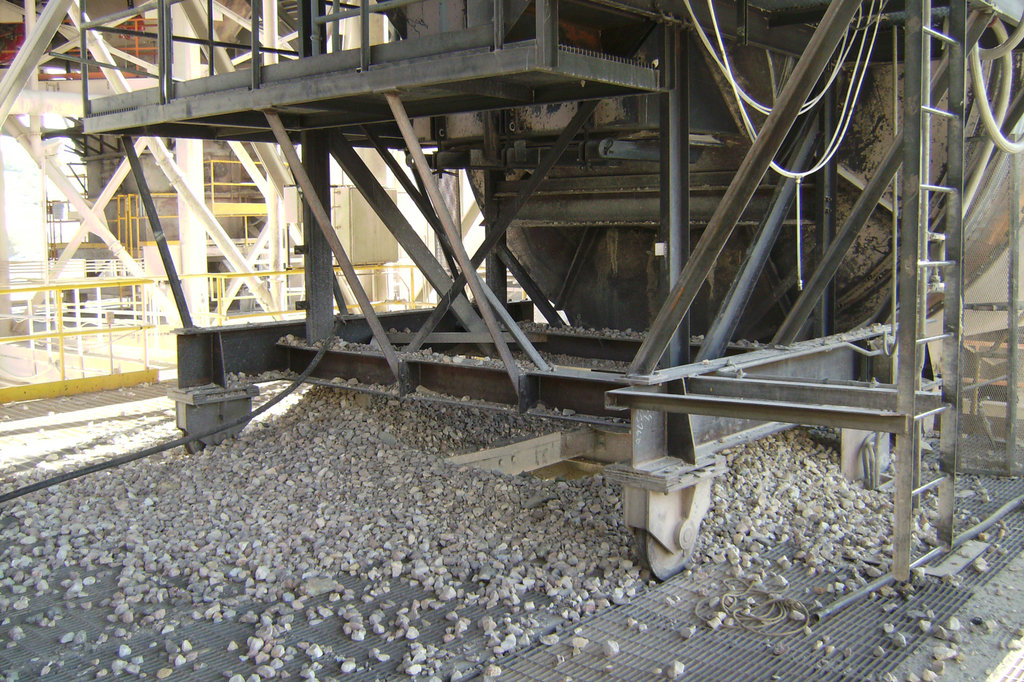
Caption. Credit:
Dilemma #3: Now this to take care of
Airborne dust and piles of spilled material are real problems that shouldn’t and, in most cases, can’t be ignored. The health and safety risks come at steep costs by way of illness, injuries, lawsuits, and regulatory fines. Beyond lowering production capacity and creating hazards and damage, the hole in the conveyor system has now created additional headaches to manage and work to do.
Dilemma #4: What was it we were trying to do again?
No one in their right mind would spend a single day moving a pile of material from one end of a lot to the other using a bucket with a hole in it. Not only would they end up with less material, but they’d end up tripping and stumbling over what had been spilled and spending countless hours trying to reclaim what had been lost.
We know that in order to meet the operation’s production goals, we rely on the efficiency of conveyor systems to move material around the site and through the process. Therefore, we should hold fast to the wisdom in proactive, preventative maintenance to avoid inevitable problems that compound quickly and work directly against us and our goals.
Don’t settle for a bucket with a hole in it; you’ll end up working in circles.
Get in touch with Martin® to help you solve your operational challenges.
Contact information
Martin Engineering Australia
www.martin-eng.com.au
mea@martin-eng.com
1300 627 364