Company Insight
Sponsored by Martin Engineering
Aligned for Success: keeping your belt safe is key
Standfirst
One of the biggest problems a bulk handling operation can face is the belt suffering damage. This problem causes the system to stop for many hours, which means damage to the plant, financial loss and risks to the safety of employees.
A damaged belt will also cause spillage of material and damage to the conveyor structure. Fortunately, however, this is an easily avoidable problem if your bulk material transport operation relies on belt monitoring solutions.
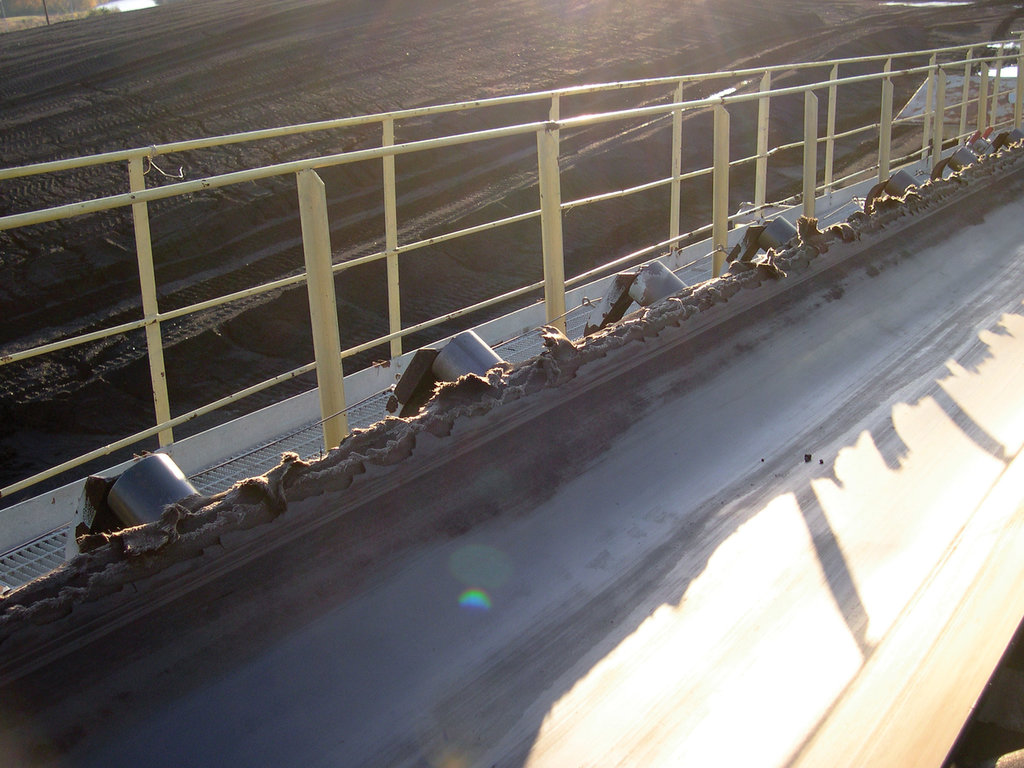
It’s a common, but preventable, problem
Every facility has faced a problem with belt durability from time to time. Besides being the most expensive component of the conveyor system, a high-quality belt and proper maintenance procedures can ensure systems operate smoothly and efficiently, improving productivity and reducing costs.
There are some common reasons why the belt is damaged. For example, many conveyor systems operate in hot environments, but exposure to extreme temperatures through direct contact with heated materials can prove particularly damaging. Abrasion and tension are responsible for a large portion of conveyor belt damage, but other forms of stress such as heat damage also contribute.
Another reason is simpler: impact. Impact damage stems from materials striking the top belt with enough force to scratch or puncture the material. Impact damage is of greatest concern with heavy, sharp objects, notably raw materials like coal and ore, particularly directly out of the mine or after passing through a crusher. However, comparatively lighter, and duller materials can still cause significant damage with enough energy behind them.
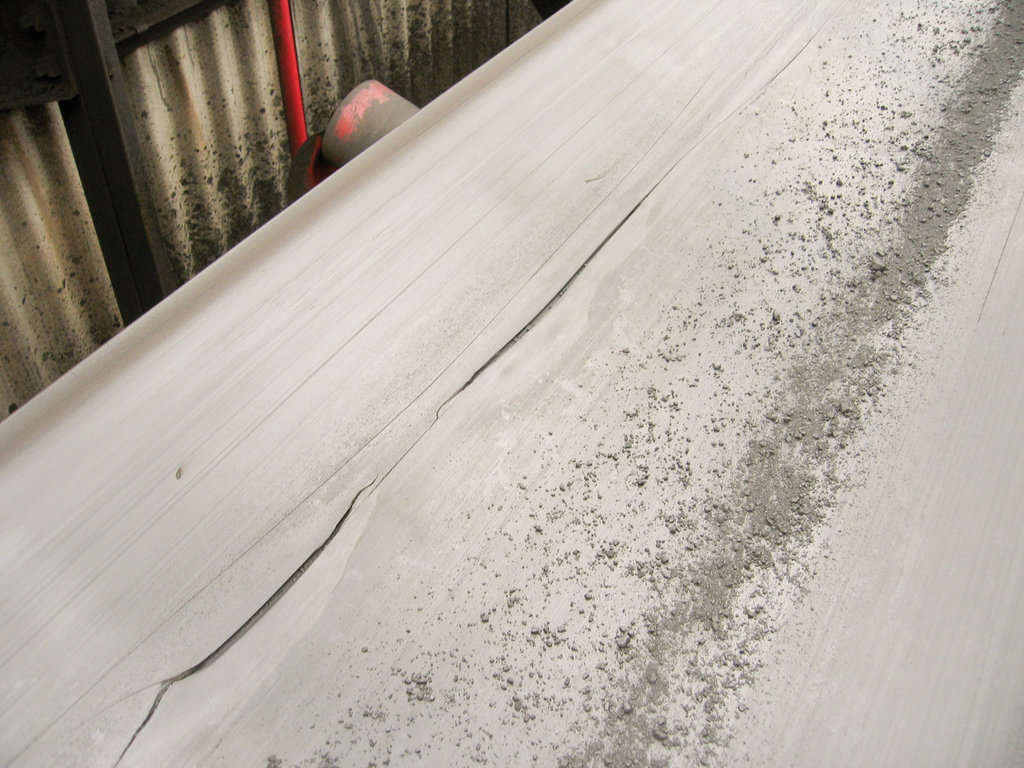
Usually caused by belt mistracking, the constant friction against the belt begins to wear it away. While many flaws in a conveyor are prone to gouge or tear the belt, something as simple as fraying can prove just as damaging over the long run, according to chapter four of Foundations from Martin Engineering. But keep in mind: belt-edge damage is rarely the product of any extreme circumstances, and so it will not produce any suddenly noticeable scars.
Other cases involve belt delamination, worn top cover, entrapment damage, belt-edge damage, and top-cover cracking.
Efficient cleaning is indispensable
When we talk about efficiency and cleaning, Martin Engineering comes to mind!
Keeping belts clean is more than just a matter of cleanliness. It allows conveyor equipment, including the belt itself, to last longer. For example, the material that is carried back under the belt often ends up inside the conveyor system and can damage rollers and idlers while causing belts to wander and fray.
High-performing belt cleaners keep belts clean, protecting the belt, eliminating carryback, and making conveyor systems safer and more productive. At Martin Engineering, we offer belt cleaners that work with all belt sizes and speeds, regardless of industry or type of material. We also offer belt cleaners that work in the most challenging and unique environments, such as on conveyor systems where there’s minimal space around the head pulley.

And, of course, the belt safety is not the main safety we are concerned about. When fugitive material accumulates under the belt, employees can easily slip and fall trying to walk through the mess. Plus, uncontained dust can cause health problems when inhaled and can ignite causing a deadly explosion. An effective belt cleaning can prevent those issues and collaborate to keep your employees safe.
Our technicians and engineers are available to provide expert advice and assistance on how to keep your belt healthy and your operation clean!
Contact information
Martin Engineering Australia
www.martin-eng.com.au
mea@martin-eng.com
1300 627 364