Company Insight
Sponsored by Coerco
An expert guide to liquid management success
Standfirst...
Main image credit:
In large-scale industrial and mining operations, the success of a liquid management project hinges on thorough planning, engineering, and consideration of key environmental factors. Missteps can result in costly delays, inefficiencies, or performance issues.
The right expertise matters when constructing a floating mine pontoon and heavy-duty access walkway or managing dam tailings, dewatering, sludge pond reclamation and dredging. At Coerco, extensive experience in the design and delivery of liquid management systems for the most challenging applications is helping clients avoid common pitfalls.
This guide ensures projects stay on track, prevent operational setbacks, and de-risk a project to achieve the best outcomes.
1. Site assessments: The foundation for success
A common cause of failure in liquid management projects is oversight of unique site requirements. Comprehensive site assessments, including topography, soil conditions, climate, and water level fluctuations, are critical in developing an effective solution. Coerco’s collaboration with Xylem at Sydney Water’s Picton Water Resource Recovery Facility highlights the importance of this. The design had to accommodate varying water levels, heavy pumps, and land on an uneven surface. According to Coerco Head of Projects Warren Classen, the team had to evaluate everything from the lake’s topography, submergence and fluctuations in water levels and water density to wind loading, pump dimensions, pontoon configuration and assembly.
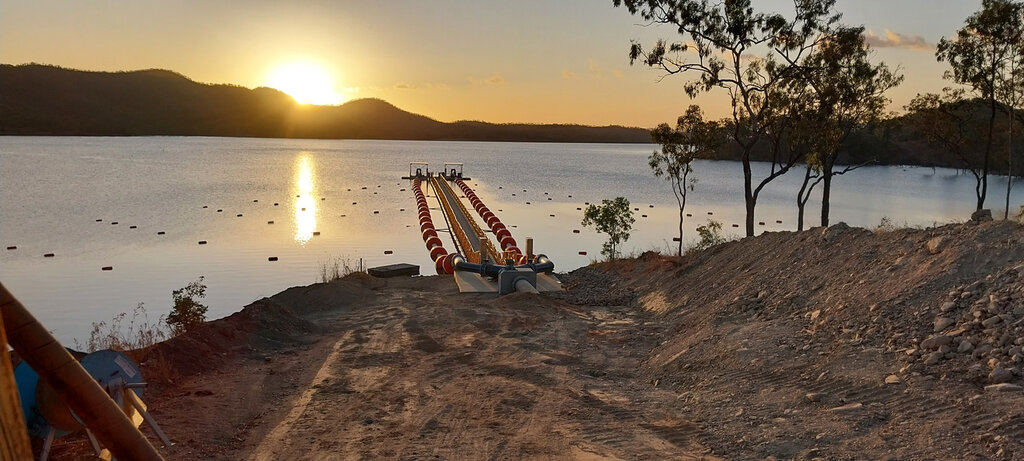
Caption. Credit:
2. Equipment selection: Finding the perfect match
Equipment mismatches can complicate projects. The design and specifications of equipment, including load capacity and material selection, must align with project goals. Coerco offers various options, from heavy-duty platforms to lightweight poly pontoons, each designed for specific environments and load capacities. According to Coerco Technical Director Gareth Wallis, factors like load, buoyancy, durability, UV stabilisation and corrosion resistance are critical when choosing a floating pontoon system.
3. Modular designs: Streamlining installation & maintenance
Larger projects, especially remote and difficult-to-access locations, benefit from modular pontoon designs. These allow more efficient transportation, installation, and maintenance. To meet different site layouts and topographies, Coerco carefully considers every modular aspect in all its pontoon designs, such as the Queensland Kidston Hydro Project, where modularisation resulted in faster installation and an ability to adapt to fluctuating water levels. According to Coerco Technical Director Gareth Wallis, modular pontoons are easier to assemble, reassemble, or take apart, which offers flexibility when adding or removing pump float units. It also helps load them onto shipping and freight containers, launch them into a dam with access limitations, and manoeuvre around a site.
4. Regulatory compliance: Meeting standards at every stage
Compliance with environmental and safety regulations is crucial in liquid management projects. Whether it’s ensuring safe access and inspection points or managing operational risks, this only presents additional challenges for designing pontoon systems. Coerco’s projects adhere to industry standards and regulations, such as AS 4100:2020 and AS 4997-2005, ensuring the highest levels of product quality and safety.
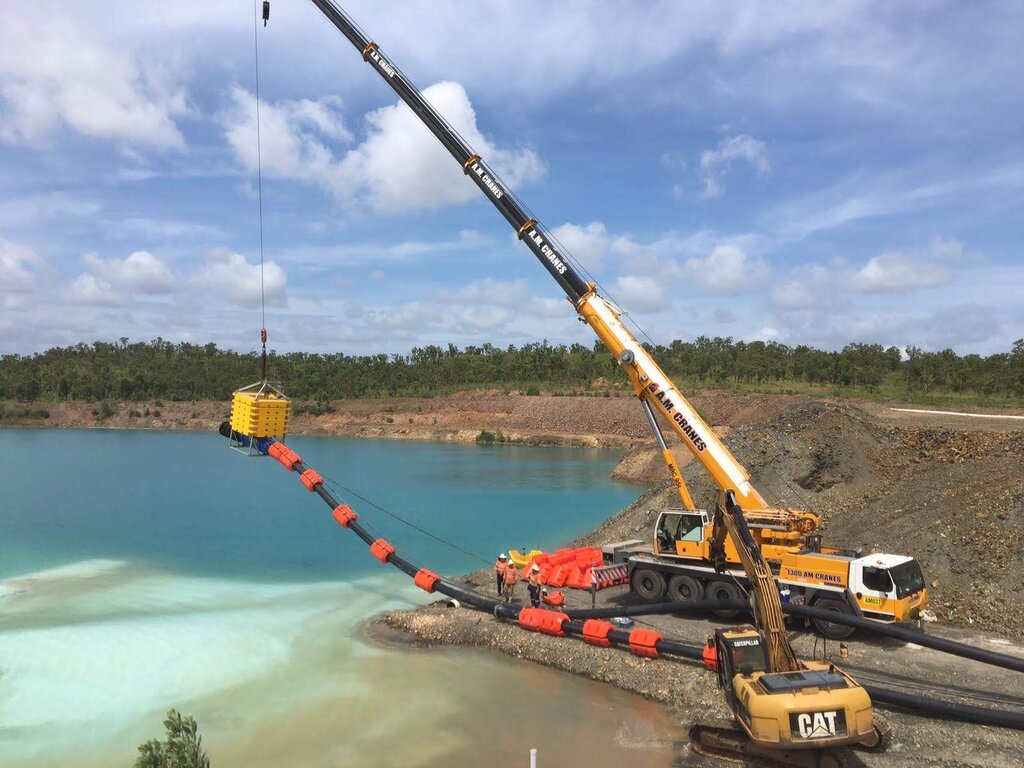
Caption. Credit:
5. Collaboration: Expertise from conception to completion
Complex projects require collaboration and multidisciplinary expertise. Coerco’s project delivery pathway manages and delivers technical projects at scale, addressing time pressures, design complexities, logistics, resource utilisation, and compliance. Working with experienced partners like Coerco, who can offer support from the discovery phase to project completion, can help mitigate issues before they arise.
6. Customisation: The key to peak performance
In liquid management, there’s no one-size-fits-all approach. Customised designs for specific operational needs can be the difference between a successful project and one plagued with issues. For over 30 years, Coerco’s philosophy has centred on providing engineered solutions that meet customer specifications, giving them total control of their liquid management. Whether it’s design, fabrication, project management, or technical know-how, you can be assured the Coerco team will deliver at every step of the process.
7. Testing & feedback: Connecting the loop
Testing equipment under operational conditions helps identify weak points before full deployment. Feedback loops between stakeholders ensure adjustments can be made, which helps businesses avoid common pitfalls that derail a project. Coerco’s in-house engineering team rigorously tests products under site conditions to ensure project success. You can be assured that when you deal with Coerco, you’ll receive a high-spec engineered solution built to solve any complex challenge. We leverage shared capabilities to achieve success in all areas of liquid containment, flotation on liquid, and liquid movement.
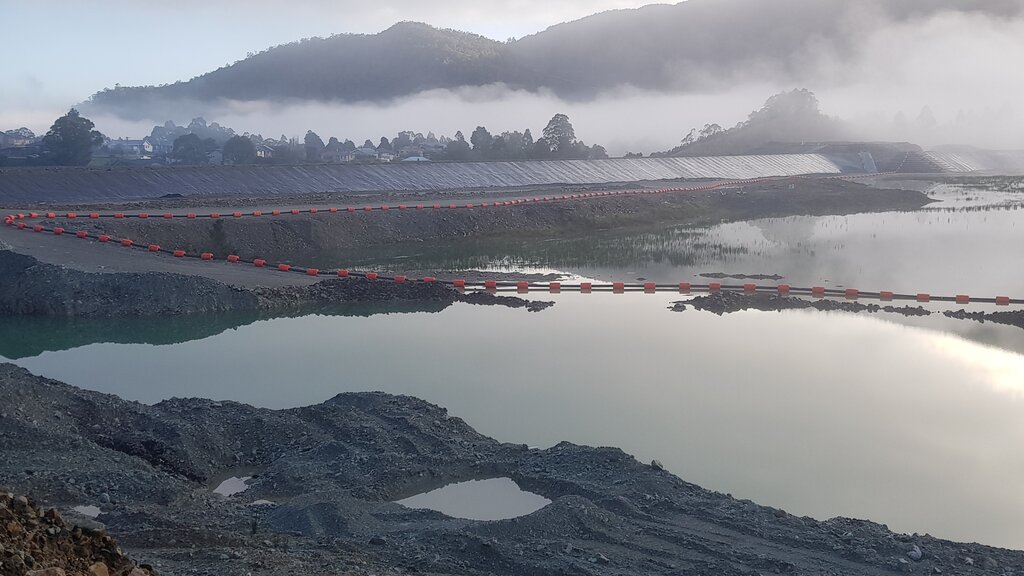
Caption. Credit:
If you’re looking for a trusted partner for your next liquid management project, visit Coerco at the WA Mining Conference and Exhibition (stand E118) on October 9-10, and IMARC (stand C12) on 29-31 October 2024. You can also check out our Guide to Floating Mining Pump Pontoons for more insights.
Contact information
Coerco Perth Office
23 Harris Rd,
Malaga WA 6090
Coerco Brisbane Office
31 Beal St,
Meadowbrook QLD 4131
Tel.: +61 1800 646 277
Email: info@coerco.com.au
Web: www.coerco.com.au