Company Insight
Sponsored by Endress+Hauser
From Data to Process Optimization: Unleashing Efficiency through Floc Viscosity measurement
Efficiency and optimization are key objectives in mining industries. One area that can greatly benefit from data-driven optimization is the control of floc viscosity. Floc viscosity plays a crucial role in processes such as flocculation, filtration, and sedimentation. By utilizing a Coriolis flowmeter in monitoring and optimizing floc viscosity, significant improvements in operational efficiency and cost savings can be achieved.

Flocculation is a widely used process that involves the aggregation of suspended particles into larger, more settleable flocs. The viscosity of the floc suspension directly affects its settling velocity and filtration characteristics. Traditionally, viscosity control has relied on manual measurements and laboratory analysis, which are time-consuming, labour-intensive, and often lack real-time data. These limitations hinder the ability to make immediate adjustments for optimal process performance. Additional to that, chemical costs for mining operations are a large part of the operational costs. When there is no visibility of chemical flow or quality, the use of these chemicals are often above an optimum amount to compensate for the risk of underdosing.
Technical Details
Integrating a Coriolis flowmeter into the floc viscosity control system enables continuous and precise monitoring of the viscosity in real-time. The patented measuring principle is based on a torsion bar fitted to the measuring tube imposes a torsional movement which is used to measure viscosity of the fluid. The torsional movement creates a velocity profile in the liquid across the pipe cross section. The velocity profile is the thus an expression of the fluid viscosity. The viscosity of the fluid dampens the torsional oscillation of the measuring tube so if viscosity is high, more excitation current is needed to sustain the torsional oscillation. Thus dynamic viscosity is determined by measuring the required excitation power. Fluid density is measured independently and simultaneously, so the kinematic viscosity can be determined.
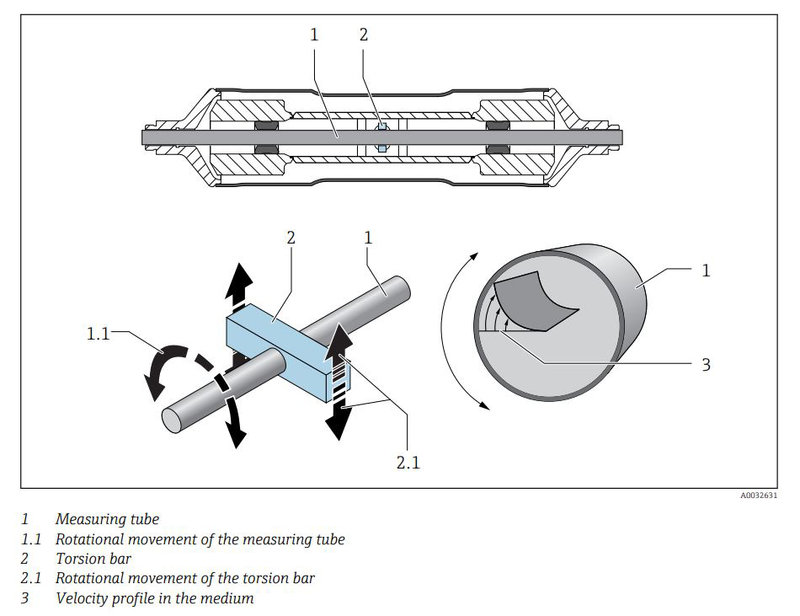
By integrating the flowmeter data with control systems, automated adjustments can be made to optimize the flocculation process. For example, if the floc viscosity deviates from the desired range, the system can automatically adjust parameters such as flocculant dosage, mixing intensity, or temperature, ensuring optimal conditions for efficient separation and filtration. This dynamic control mechanism minimizes the risk of inefficient flocculation, leading to cost savings through reduced chemical consumption and improved filtration efficiency.
Another advantage of using a Coriolis flowmeter for floc viscosity optimization is the ability to detect and respond to process deviations promptly. Fluctuations in viscosity can occur due to changes in raw materials, variations in process conditions, or equipment malfunctions. The Coriolis flowmeter can detect these changes in real-time, triggering immediate corrective actions. By continuously monitoring the floc viscosity, the system can quickly identify any deviations and activate alarms or control mechanisms to rectify the issue, ensuring consistent performance and preventing potential process failures.
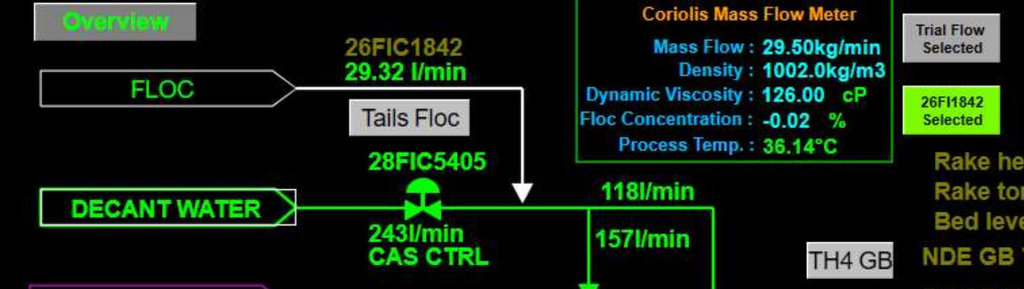
Furthermore, the integration of a Coriolis flowmeter into the floc viscosity control system enables comprehensive data collection and analysis. The flowmeter provides detailed information about fluid properties, including viscosity, density, and temperature. This data can be stored and analysed to identify trends, correlations, and anomalies. Advanced analytics techniques, such as machine learning algorithms, can be applied to extract valuable insights from the data, enabling further process optimization opportunities.
The straight single-tube, full bore design of Promass I provides in-line viscosity measurement in addition to mass flow, density, and temperature measurement. The device is also equipped with the viscosity package, which is used to correlate the concentration of the floc against the viscosity of the non-Newtonian pseudo plastic fluid. The flowmeter is also equipped with Ethernet/IP, which enables fast and easy commissioning by site engineers. The advantage of using Ethernet/IP is that the settings of the device can be examined via the webserver from the control room. The benefits of data-driven floc viscosity optimization using a Coriolis flowmeter extend beyond operational efficiency and cost savings. Improved viscosity control leads to enhanced product quality and consistency. In industries where product quality is critical, maintaining consistent floc viscosity ensures the desired texture, stability, and sensory attributes of the final product.
In conclusion, the integration of a Coriolis flowmeter into the floc viscosity control system revolutionizes process optimization, offering numerous benefits across industries. Real-time monitoring of floc viscosity enables immediate adjustments, ensuring optimal process performance and enhanced operational efficiency. The ability to automate parameters such as flocculant dosage, mixing intensity, and temperature based on flowmeter data results in significant cost savings through reduced chemical consumption and improved filtration efficiency. Prompt deviation detection and corrective actions minimize the risk of inefficient flocculation, preventing process failures and maintaining consistent performance. Moreover, the comprehensive data collection and analysis capabilities of the flowmeter enable valuable insights and trends to be extracted, facilitating further process optimization opportunities. By leveraging data-driven approaches and the power of the Coriolis flowmeter, industries can achieve higher levels of operational excellence, cost savings, and improved product quality. This integration provides a competitive advantage, allowing businesses to stay at the forefront of efficiency, innovation, and sustainable growth.
Vikram Apte
Industry Manager, Metals & Mining/ Oil & Gas.
Contact information
Endress+Hauser Australia
Mobile: +61 447 768 932
Email:vikram.apte@endress.com
Web: www.au.endress.com