The mining industry continues to be a hotbed of innovation, with activity driven by the need for greater productivity as well as safety. Related to this, miners are using tunnelling machines in place of traditional drilling and blasting methods.
Deployment of these potentially reduces disturbances to the geographic conditions thereby increasing safety. In the last three years alone, there have been over 48,000 patents filed and granted in the mining industry, according to GlobalData’s report on Robotics in Mining: Tunnelling Machines.
However, not all innovations are equal and nor do they follow a constant upward trend. Instead, their evolution takes the form of an S-shaped curve that reflects their typical lifecycle from early emergence to accelerating adoption, before finally stabilising and reaching maturity.
Identifying where a particular innovation is on this journey, especially those that are in the emerging and accelerating stages, is essential for understanding their current level of adoption and the likely future trajectory and impact they will have.
150+ innovations will shape the mining industry
According to GlobalData’s Technology Foresights, which plots the S-curve for the mining industry using innovation intensity models built on over 350,000 patents, there are 150+ innovation areas that will shape the future of the industry.
Within the emerging innovation stage, defect detection techniques, energy demand optimisation, and magnetic route detectors are disruptive technologies that are in the early stages of application and should be tracked closely.
Hydraulic mining conveyors, tunnel safety devices, and tunnel lining construction devices are some of the accelerating innovation areas, where adoption has been steadily increasing. Among maturing innovation areas are CAD for drill planning and SCARA robotic arms, which are now well established in the industry.
Innovation S-curve for robotics in the mining industry
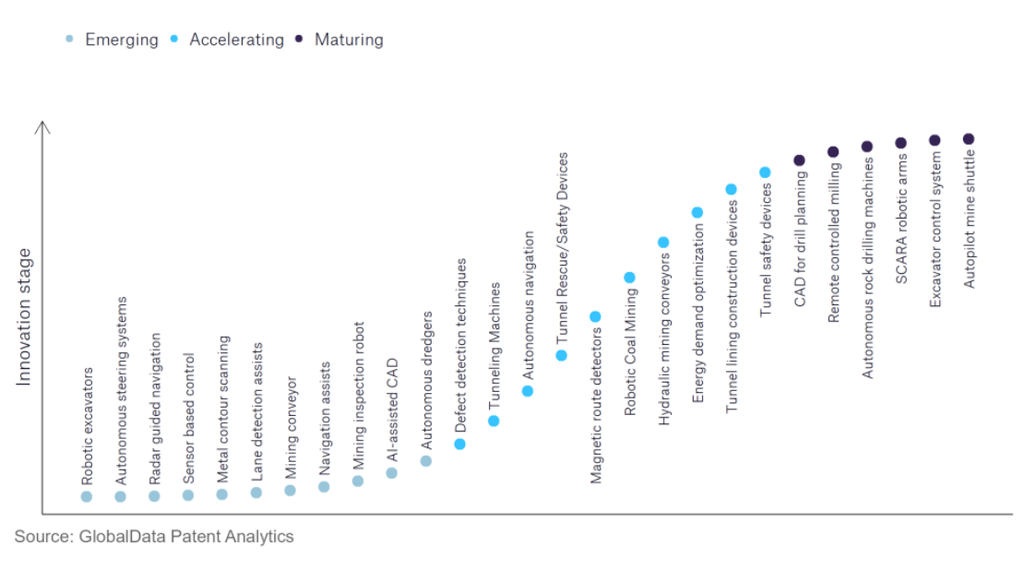
Tunnelling machines is a key innovation area in robotics
Tunnelling machines perform boring functions, to excavate tunnels with a circular cross-section through a variety of soil and rock strata. These are used instead of drilling and blasting through rock and conventional mechanical excavation in soft ground and have been used for a variety of purposes as part of new and expanding mining projects, including new access, ore and waste conveyance, drainage, exploration, and water diversion.
Some of the benefits of using tunnelling machines include higher and more sustainable progress rates in generally good quality hard rock conditions. Lower ventilation is required, allowing for the construction of smaller tunnels and improved health conditions for workers who are not exposed to blast smoke and fumes.
They also produce a smooth tunnel wall, which lowers the final lining cost. Tunnelling machines significantly reduce the total excavation time of long tunnels when compared to conventional excavation methods.
GlobalData’s analysis also uncovers the companies at the forefront of each innovation area and assesses the potential reach and impact of their patenting activity across different applications and geographies. According to GlobalData, there are 10+ companies, spanning technology vendors, established mining companies, and up-and-coming start-ups engaged in the development and application of tunnelling machines.
Key players in tunnelling machines – a disruptive innovation in the mining industry
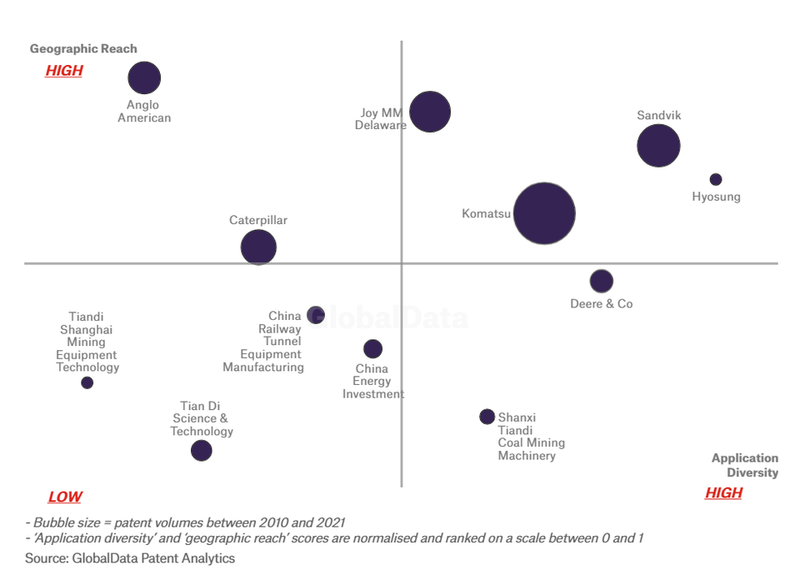
‘Application diversity’ measures the number of different applications identified for each relevant patent and broadly splits companies into either ‘niche’ or ‘diversified’ innovators.
‘Geographic reach’ refers to the number of different countries each relevant patent is registered in and reflects the breadth of geographic application intended, ranging from ‘global’ to ‘local’.
Patent volumes related to tunnelling machines
Leaders in tunnel machines include Komatsu and Sandvik. Amongst the innovations, Komatsu has partnered with Codelco to test a new tunnel excavation method using Komatsu's newly developed mining TBM. The mining TBM is outfitted with new technologies that allow it to adapt to small curves, reverse direction, and pass-through intersections in hard rock tunnel excavation.
This new technology increases equipment flexibility and allows tunnels to be excavated in accordance with the more unique designs of each mine. The trial, which will begin in 2024 at Codelco's Chuquicamata mine in Chile, aims to accelerate the potential implementation of the new technology.
Similarly, Sandvik's tunnelling jumbos provide high productivity and dependability using face drilling, mechanised longhole drilling and bolting. The company’s tunnelling machines include DT1232i, DT923i (fully automated), DT1231, DT1131 (three-boom, electro-hydraulic), and DT912D (self-contained, air-mist flushing, diesel-hydraulic high reach single boom).
To further understand the key themes and technologies disrupting the mining industry, access GlobalData’s latest thematic research report on Mining.
GlobalData, the leading provider of industry intelligence, provided the underlying data, research, and analysis;used to produce this article.
GlobalData’s Patent Analytics tracks patent filings and grants from official offices around the world. Textual analysis and official patent classifications are used to group patents into key thematic areas and link them to specific companies across the world’s largest industries.