Feature
Are mining robots putting mining jobs at risk?
As the role of robotics becomes increasingly key in the mining industry, will miners find getting work harder? Kit Million Ross seeks the truth of the matter.
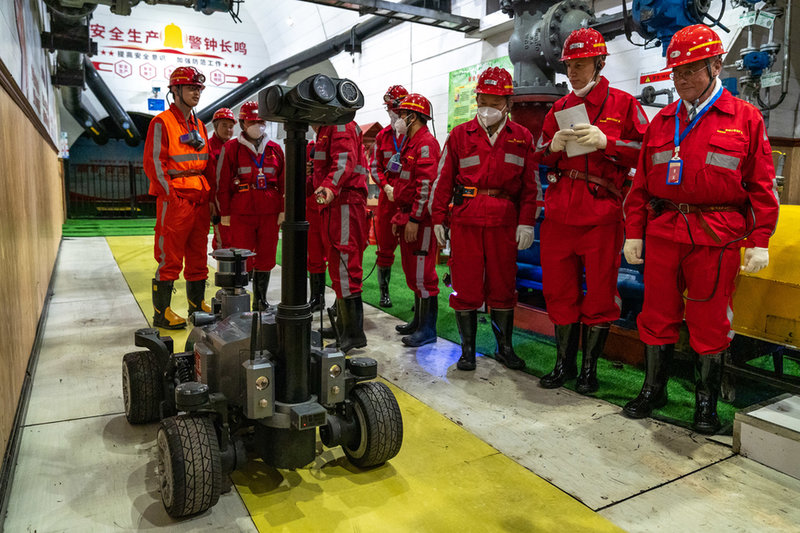
Workers and robots at the Xiaobaodang Coal Mine in Yulin, China.
The clank of pickaxes and the whir of drills are being replaced by the whir of robotic arms and the hum of autonomous vehicles. As technology advances, robots are making lighter work not only in extracting resources from the Earth, but also the nature of the industry itself. While it’s true that robots are making mining work safer, cleaner, and less labour intensive, it is worth considering what the impact may be on jobs in the industry. Are workers being pushed out by robots? How can industry workers make sure that their skills are suitable for the future? And how can employers balance worker’s rights and innovation?
We peer into the mines to uncover the profound impact that robotics is having on safety, efficiency, sustainability, and the workforce, and how it is reshaping an age-old profession into a cutting-edge field of innovation.
The current state of affairs
Although it has been proven that humans cannot be totally removed from operating mines, the first self-proclaimed “fully automated” mine was opened in Mali in 2018. Nevertheless, it becoming increasingly common for mining operations, even smaller ones, to have some level of robotics in their projects; analysts Technavio forecast the global robotics market in the mining industry to grow at a compound annual growth rate of around 27%.
It is interesting to note that employing human workers is beneficial to mining firms in some unexpected ways. A 2020 paper notes: “it is widespread to observe new mining projects receiving political support and their social license to operate based on the promise of job creation in new projects (Dumbrell et al, 2020; Nguyen, 2020). The potential new - generally well paid - jobs that mining projects bring to regions is the main benefit that mining companies typically bring to the negotiation table to seek support from local stakeholders when applying for new or expanding mine operations.”
The potential new jobs that mining projects bring is the main benefit that mining companies typically bring to the negotiation table.
Several major mining firms have implemented robotics into their operations: in June 2022, Rio Tinto installed a huge number of robots into their newly built Gudai-Darri mine. At Gudai-Darri, robots have assisted with tasks in the ore sampling laboratory, conveyed parts in workshops, and carried pallet frames in warehouses. While not exactly “robots”, autonomous trucks, carts, and drills are also in use at the site. Approximately 600 permanent jobs were created by the opening of this mine, as well as 3,000 developmental jobs, so perhaps robotics can be an opportunity, and not a threat, to job security in the industry.
Anglo American has implemented robotic technologies at all of its South African mines. Remotely operated rigs and continuous haulage systems are in use at the firm’s Twickenham mine, which produces gold, nickel, palladium, platinum and rhodium.
How big is the risk to jobs?
According to a report by MINE magazine’s parent company GlobalData, the most frequently used field robots in mining are automated drills, autonomous haulage systems, and underground mining robots. It’s natural to assume that jobs involving haulage, drilling and underground work are those most at risk, and this is not an unfounded belief; in Q2 2023 the European mining sector saw the greatest hiring activity not in any on-the-ground sector, but rather in management occupations.
The fear of job losses is backed up by data. A 2020 paper estimated that automation could see around 10,000 coal mining jobs in Queensland, Australia being replaced – approximately 40% of Queensland’s coal mining workforce. Naturally industry workers will be concerned by statistics like these, but a 2021 paper published in The Extractive Industries and Society journal notes that this could merely represent a shift, rather than a reduction in the workforce: “While low-skill, routine jobs are more in jeopardy, demand for high-skill workers will tend to keep increasing as automation technology would require a workforce capable of operating sophisticated machinery and computer coding.”
While low-skill, routine jobs are more in jeopardy, demand for high-skill workers will tend to keep increasing.
As such, governments and companies have taken notice of or invested in retraining and upskilling programmes. In December 2022, the government of Queensland announced a $3m programme to upskill and retrain existing mining industry employees to deal with a growing skills shortage in the area.
However, the 2021 paper does note that upskilling workers can only help so much. The author notes that “the increase in demand of skilled workers will never provide the number of jobs to be lost for automation as economy of scales will tend to decrease employment needs.” So how do we prevent worker displacement in the industry? Is it just an inevitable fact of progress, just the cost of doing business?
Ethical automation and the future of robotics
As mining becomes more automated, it becomes essential to address the impact on the workforce. Displaced workers may face challenges in transitioning to new roles or industries. Mining companies need to ensure that they take responsibility for managing the transition effectively, and consider the welfare of their workforce. Initiatives such as retraining programs and support for workers in transitioning to new roles or industries can be helpful, but perhaps the best way of thinking of the issue avoids a “man vs machines” view; the integration of robotics should not be seen as a replacement for human workers but as a complement.
The future of mining is inextricably intertwined with robotics and automation. While these technologies offer huge advantages in safety and efficiency, the industry must prioritise the wellbeing of its employees. As mining companies embrace automation, they have an ethical obligation to also invest in retraining and upskilling programs to ensure that employees remain relevant as the mining industry changes.
Automation has the potential to transform the industry, but also raises huge concerns regarding workforce displacement. The increasing use of robotics brings a new question in striking a balance between the benefits of automation and the well-being of workers and mining communities. If trod carefully, ethical automation can lead to a better future for all.
GlobalData, the leading provider of industry intelligence, provided the underlying data, research, and analysis used to produce this article.
GlobalData’s Thematic Intelligence uses proprietary data, research, and analysis to provide a forward-looking perspective on the key themes that will shape the future of the world’s largest industries and the organisations within them.