Innovative material handling technologies in heavy duty areas
For more than 70 years IFE Aufbereitungstechnik GmbH has been dealing with the construction of machines for bulk material handling and has decades of experience in the field of grainy and abrasive substances and masses.
Scroll down to read the article
A wide portfolio of vibrating screens, magnetic separators and vibroconveyors is available for a variety of applications e.g.:
- metal ores and concentrates
- sintering plants in the steel industry
- carbon and graphite masses
- raw materials and materials in the ceramics industry
- non-ferrous metals in powder metallurgy
- raw materials for the manufacturing of refractory products
- salts for industrial applications
IFE is well known for the longevity of the machines. Machine lifecycles of more than 15 years at 8.000+ operating hours per year speak for themselves! All machines are undergoing a trial run before delivery, as this is part of the IFE quality standards. Worldwide service as well as long-term spare parts availability are guaranteed.
In terms of the material handling process, the equipment is used in the fields of scalping, separating, sizing and conveying:
Scalping
For scalping usually the robust IFE grizzly feeders in heavy duty design are in operation. They are used to feed crushers and mills, or as separating grates. Example: Feed material with sizes up to 1000 mm and feed rates of more than 5000 t/h for iron ore are fed to a cone crusher, where the feddmaterial scalper removes fines below a cut point of 100 mm. The robust and reliable design combined with special wear plates (thickness 50 mm) allows for long lasting, safe operation under heavy duty conditions.
Throughout Ukraine, the mining industry’s general debt is estimated to be $18.7m
Scalper screen for iron ore separation
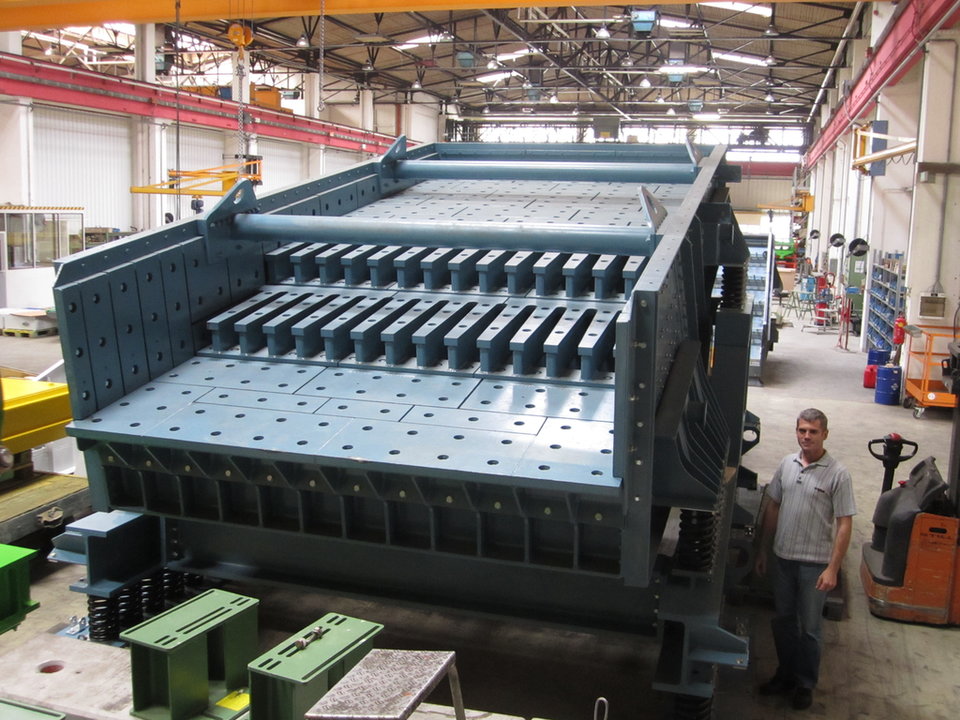
During the first ten months of 2017, Ukraine spent $2.15bn on coal imports
Sizing
One of the main mechanical handling methods used for granular bulk material is screening. The type of material, the grain shape and grain size, humidity, output and screen cut size as well as many other parameters necessitate a broad spectrum of different solutions.
Computer-based machine calculation and design, long-term experience in the mechanical process technology as well as technical and manufacturing know-how result in the engineering of the optimal screen size and design. In general, the massive dimensions of the machines and the nature of the feed material require an extremely robust equipment as well as the best available wear protection of all parts in contact with material.
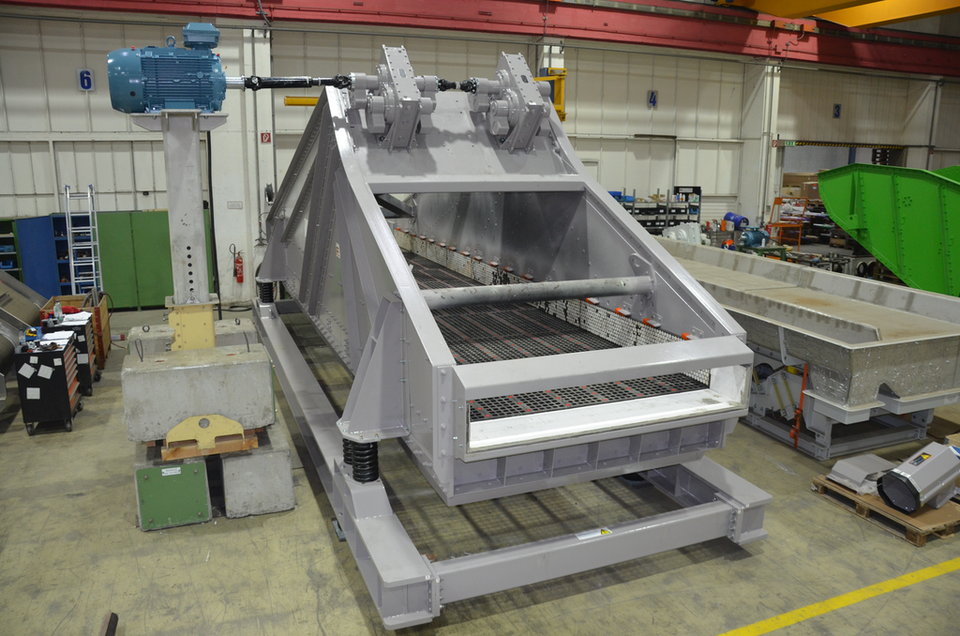
Linear motion vibrating screen in heavy-duty design for screening coke
Individual Solutions
In the field of fine screening, where conventional screening machines such as linear or circular vibrating screens have reached their limits, special machines for very demanding duties are required.
Sticky material
The flip-flop screen IFE TRISOMAT with its flexible screening panels is used for the classification of difficult-to-screen, sticky or moist material in separating cuts of approximately 2 to 20 mm. Tensioning and loosening of the screen panels produces a self-cleaning effect. Besides sand and gravel, this all-rounder screen is also used for screening coal and coke and also finds use in steel works.
Very high throughputs
The banana screen can handle two to three times higher feed rates compared to conventional vibrating screens. These screens are thus particularly well suited when a massive increase in capacity needs to be achieved or when the required capacity is very high in general. 34.100 kg of oscillating weight moves in the biggest IFE banana screen (3200 x 10000) built by today – it is used for screening coal in Norway.
It is essential to pay wage arrears in full [and] stamp out corruption in the industry
Double-deck flip-flop screen TRISOMAT
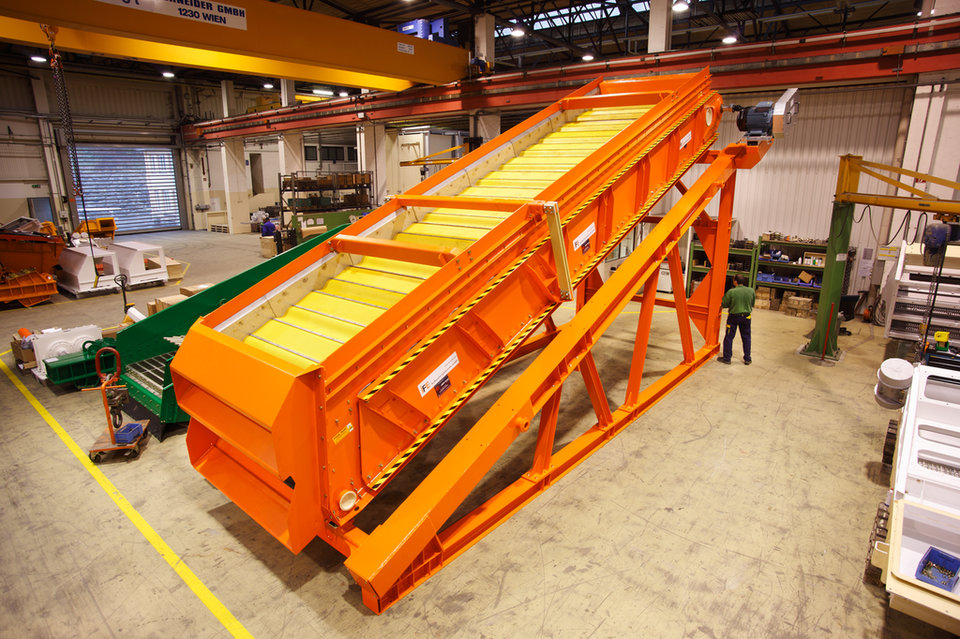
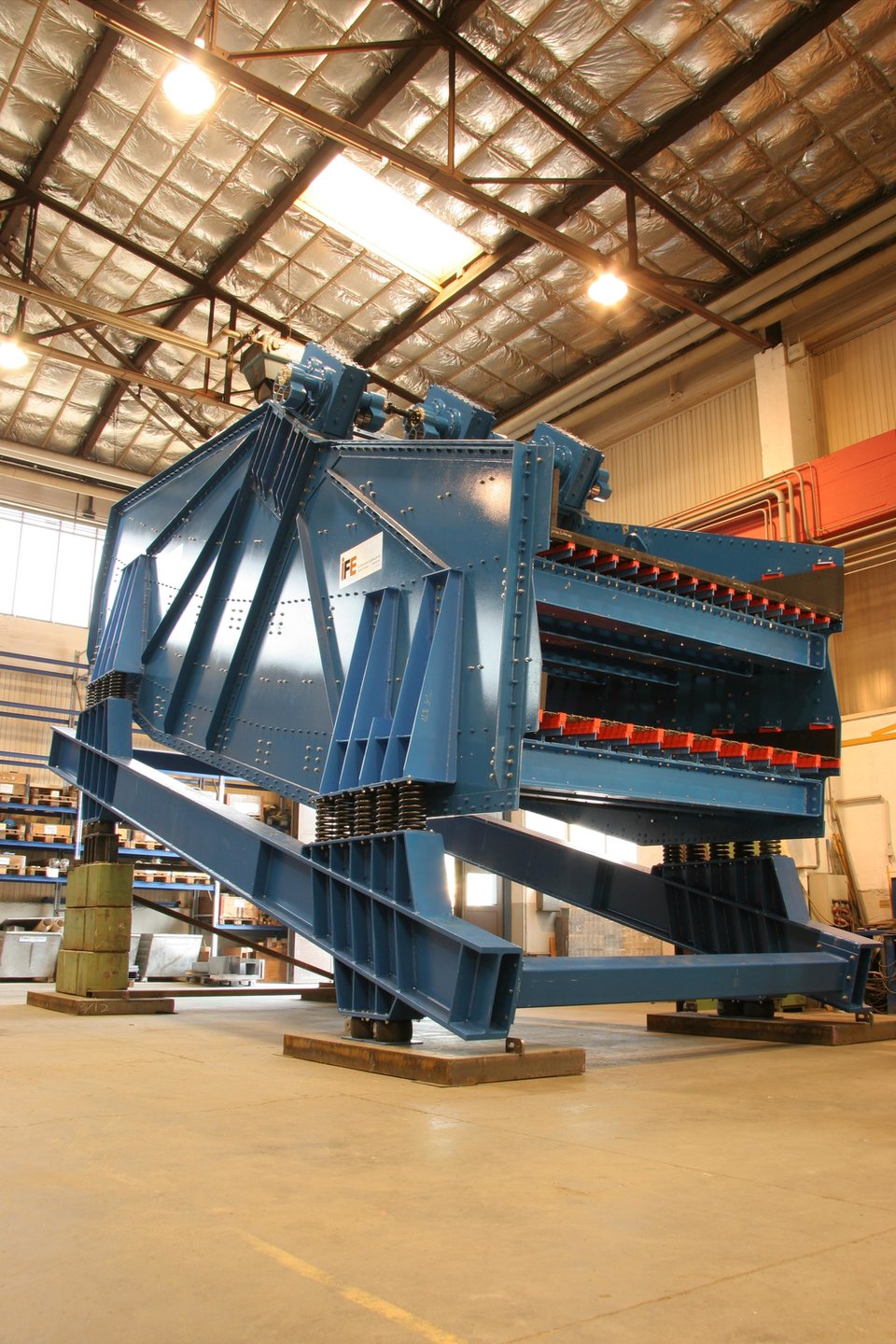
Double-deck banana screen for coal
separation in Norway
During the first ten months of 2017, Ukraine spent $2.15bn on coal imports
Magnetite Processing
Conveying and screening are usefully complemented by magnetic technology, when machines have to be protected against tramp iron or if products have to be cleaned or enriched.
For magnetite processing, IFE provides an enormous spectrum - from pre-concentration by magnetic drum to wet drum separation.
IFE wet drum separators are used to regenerate magnetisable media, to extract particles out of suspensions and to concentrate iron ore.
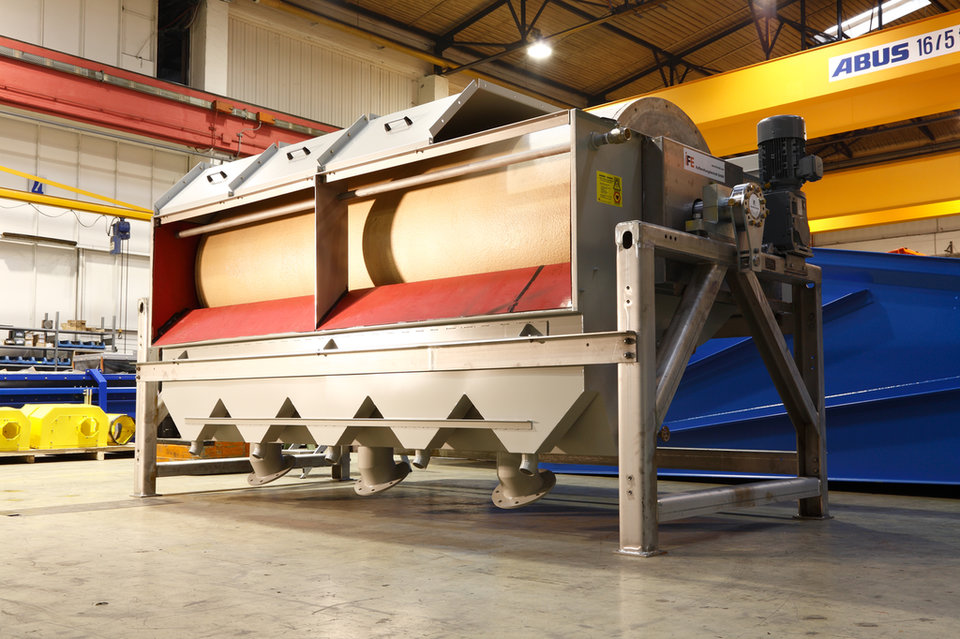
Wet drum separator for ore concentration processes
Conveying
While vibrating feeders are generally not the focus of a plant, they can negatively impact both, throughput and product quality if not properly designed. Therefore, IFE vibroconveyors are always designed and manufactured for specific applications. IFE heavy-duty feeders are ideally used for high feed rates and perform well in harsh conditions. They are available in large machine dimensions and manufactured with robust materials. Typical applications involve the crusher feeding as well as the distribution and handling of high capacity materials, such as chrome and iron ore.
It is essential to pay wage arrears in full [and] stamp out corruption in the industry
Heavy-duty feeder for primary crusher feed
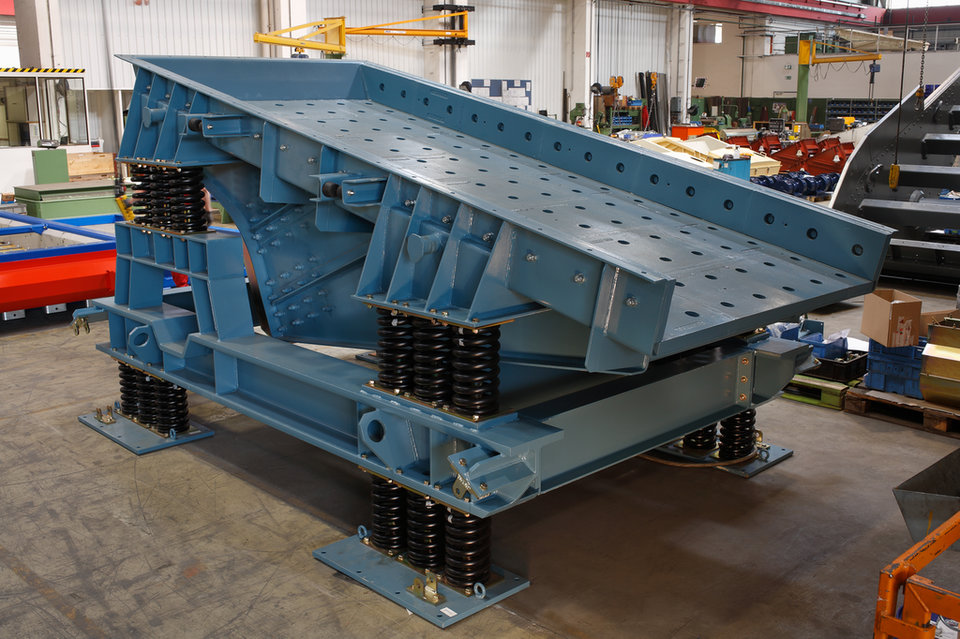
During the first ten months of 2017, Ukraine spent $2.15bn on coal imports
IFE is the only manufacturer that offers package solutions in the product areas of conveying, screening and magnetic technology. For that reason, IFE is able to supply the necessary know-how for the design and dimensioning of all kinds of heavy-duty processing applications.
Contact information
PO Box 946
Travelers Rest
SC 29690
United States of America
Web: www.ife-bulk.com
Email: office@ife-bulk.com