COMPANY Insight
Carroll Technologies Group has provided safety equipment to mine operators for more than forty years, offering a high-end, personalised service to all its customers. Carroll Engineering president Allen Haywood spoke to JP Casey about the flexibility, simplicity and effectiveness of the company’s leaky feeder communications and tracking system.
Carroll Engineering President on communications and tracking
Scroll down to read the article
Advanced communication systems
“The leaky feeder system is a cable that leaks the antenna’s reception and transmission, and that cable is stretched throughout the mine and acts as a huge antenna,” said Haywood. “With leaky feeder, if you have line of sight with that antenna, or are in reasonable distance, you can talk to that cable rather than talking to another radio. The cable transmits the message from the radio, say ten miles underground to possibly ten miles above ground to another radio, with clear communications.”
This simple systems forms the base of many of the services Carroll offers and enables a range of additional parts and devices to be added to extend this solution further. The company provides more than 20,000 different products from over 70 distributors, so having a single system onto which any product can be added helps tie these products together into a single service.
Some of the key services include a miner tracking system, where individuals’ positions are monitored through the leaky feeder system via a tag on each person; ventilation controls, where fans can be operated remotely through the system; and an atmospheric monitoring system which can feed data collected by individual miners back to a central location, to observe and respond to the presence of hazardous gases.
The same system can be used to improve mine efficiency. Haywood used the example of a medically-trained worker whose location can be monitored so they can be instructed to move through the mine in the event of an accident where someone requires medical attention, all through the leaky feeder system. This approach can be used for equipment, both in terms of tracking the positions of vehicles and equipment, and also monitoring their effectiveness; the time it takes for a truck to make a trip or perform a task can be recorded and the data analysed.
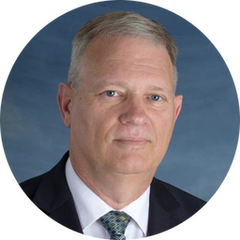
Carroll Engineering President Allen Haywood. Credit: Carroll Technologies
Data and analysis
Carroll releases regular reports on safety trends in the mining industry and collects much of the data for these reports through the leaky feeder system. “One of the things they use that data for, that they want to look at and serve operations, is air flow,” said Haywood. “It’s critical for these operations to have proper ventilation to keep air flowing throughout the mines underground, and they can measure, on this system, the amount of air flow in particular areas.
“And that’s recorded, in case they want to go back and look and see what that air flow is, they can go back and look at the history of that.”
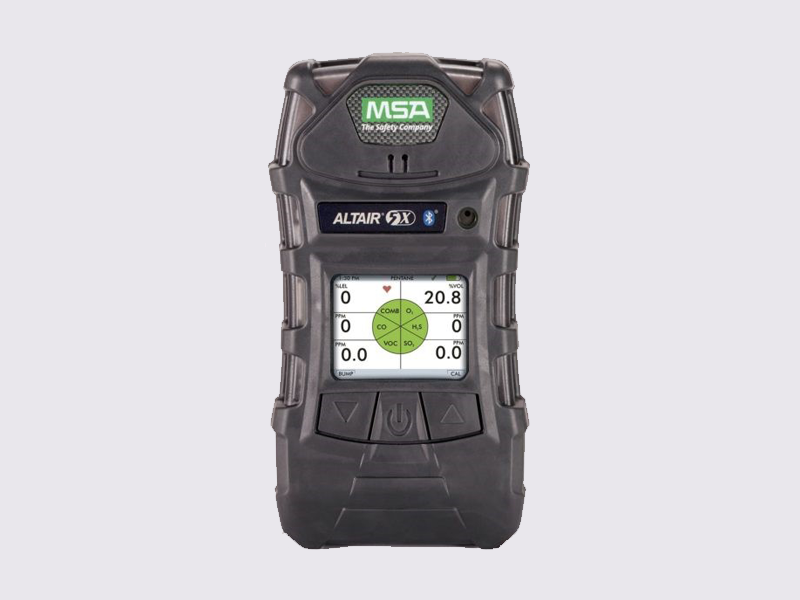
The MSA Altair 5X Gas Detector. Credit: Carroll Technologies Group
Personalised services
Haywood made it clear that Carroll’s business is providing a comprehensive service to customers, not just supplying materials and devices. “One of the things that we offer our customer base that has these systems is what we call a service agreement. We offer a service agreement to be there, on-site, and we do an inspection of the system, we do backups of the system and the information, and we do any upgrades that have come out and need to be upgraded and, more importantly, if they’ve had any problems or have questions they can ask those questions or present those problems to us that they need help with.
“We look at that as if it is a regular training process for the mining personnel; when we’re there, it’s continual training and re-training.”
This holistic approach and comprehensive relationship between Carroll and its customers set the company apart from other companies that offer similar communication network technology.
“A company may come to use and say, ‘Listen, we’ve got your communications system and we’re doing tracking, and we were wondering if we could also incorporate this other function into it?’ We like those requests because we take those and customise some things to fit that system, and you don’t have that a lot with other companies. So we do customised catering to their needs.”
“We built this business on servicing the customers, not just selling a product and waiting to hear back from them.”
Contact Information
Carroll Technologies Group
Office: +1 (606) 573-1000
www.carrollengineeringco.com
www.deltaelectricwv.com