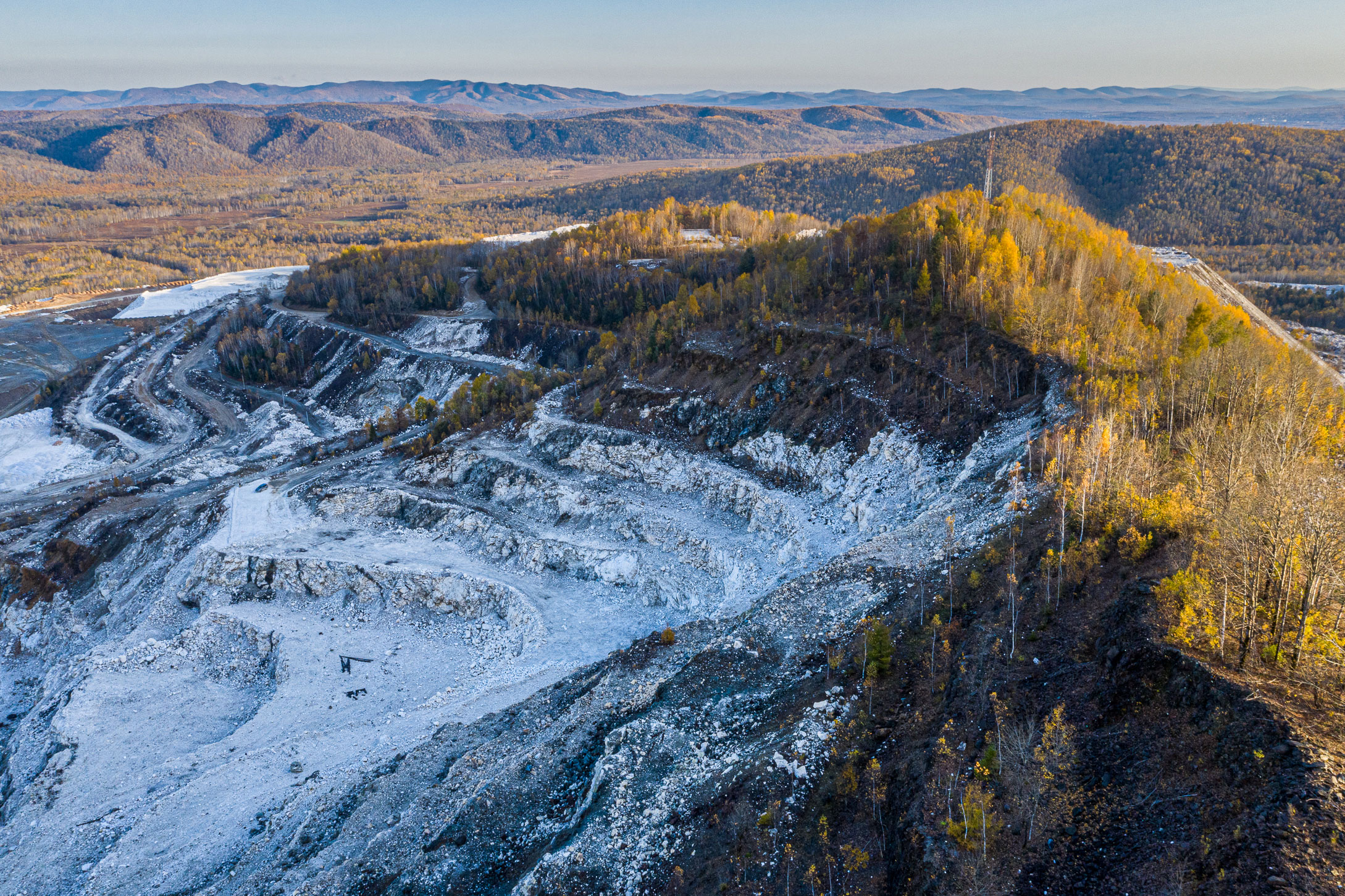
COMPANY INSIGHT
Sponsored by Brucite+
The Kuldur brucite deposit – a source of magnesium hydroxide
The Jewish Autonomous Oblast (JAO) is rich in natural resources. There are over 20 known deposits of valuable raw materials, such as iron, coal, tin, manganese, graphite, gold and, of course, brucite, within its territories.
T
he Jewish Autonomous Oblast (JAO) is rich in natural resources. There are over 20 known deposits of valuable raw materials, such as iron, coal, tin, manganese, graphite, gold and, of course, brucite, within its territories.
There was an increased interest in this region’s resources as far back as the middle of the 19th century. And it was renewed in the 1930s after the JAO was established in Russia’s Far East.
Named after a near-by river, the Kuldur brucite deposit was first discovered in 1965 by geologists who were working in the region at the time. According to further studies the following year, it was estimated that there were 14 million tons of brucite ore in the area. Three years later, in 1969, the Kuldur mine began its operations.
For quite a number of years, the only consumer of the extracted mineral was the Bogdanovich fire-retardant materials factory, and its output product volume at that time accounted for 10% of that at present. Brucite used to be refined primarily with the aid of manual labor.
This changed in 2006 when the Russian Mining Chemical Company (RMCC) LLC, which manages the Group of companies under the Brucite+ brand, took over mining operations. The RMCC leadership chose to re-equip the facility and find novel uses for brucite, which, in turn, marked a new milestone for the region rich in mineral deposits.
At present, products on the basis of brucite ore are used by Russian as well as foreign consumers in industrial, agricultural and environmental protection spheres as well as in their daily lives.
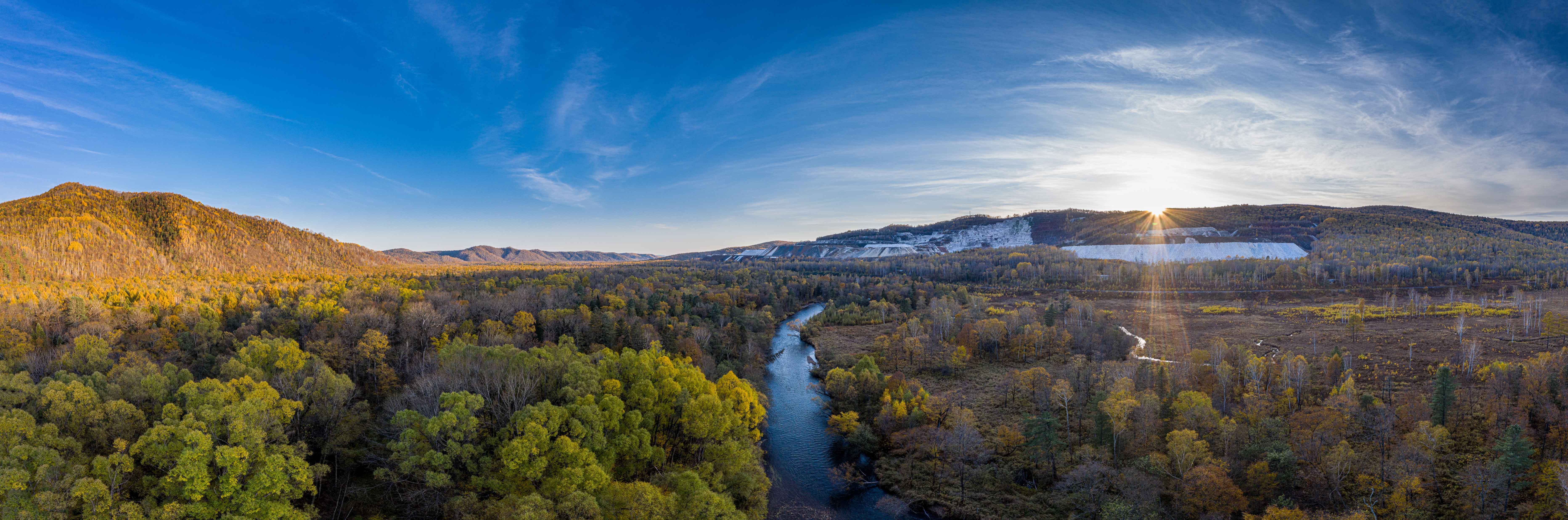
Brucite reserves
The Kuldur deposit is one of the largest deposits in the world in terms of reserves. At the moment, they are estimated at 6.6 million tons of brucite ores. The volume of production from the open pit of the Main deposit is about 450 thousand tons per year, in the near future it is planned to increase production volumes up to 500 thousand tons annually. With this productivity, the Group's supply of raw materials will be about 13-14 years.
In order to increase the mineral resource base of the Kuldur deposit, a preliminary assessment of the resource base and economic indicators of two options for the development of the South bank of the deposit was carried out in 2021, both of which demonstrated a positive economic result. The expected growth in the reserves of the Kuldur deposit due to the increase in the recoverable reserves of the South bank will amount to 1.2-1.5 million tons, which will increase the period of development of the deposit by 2-3 years.
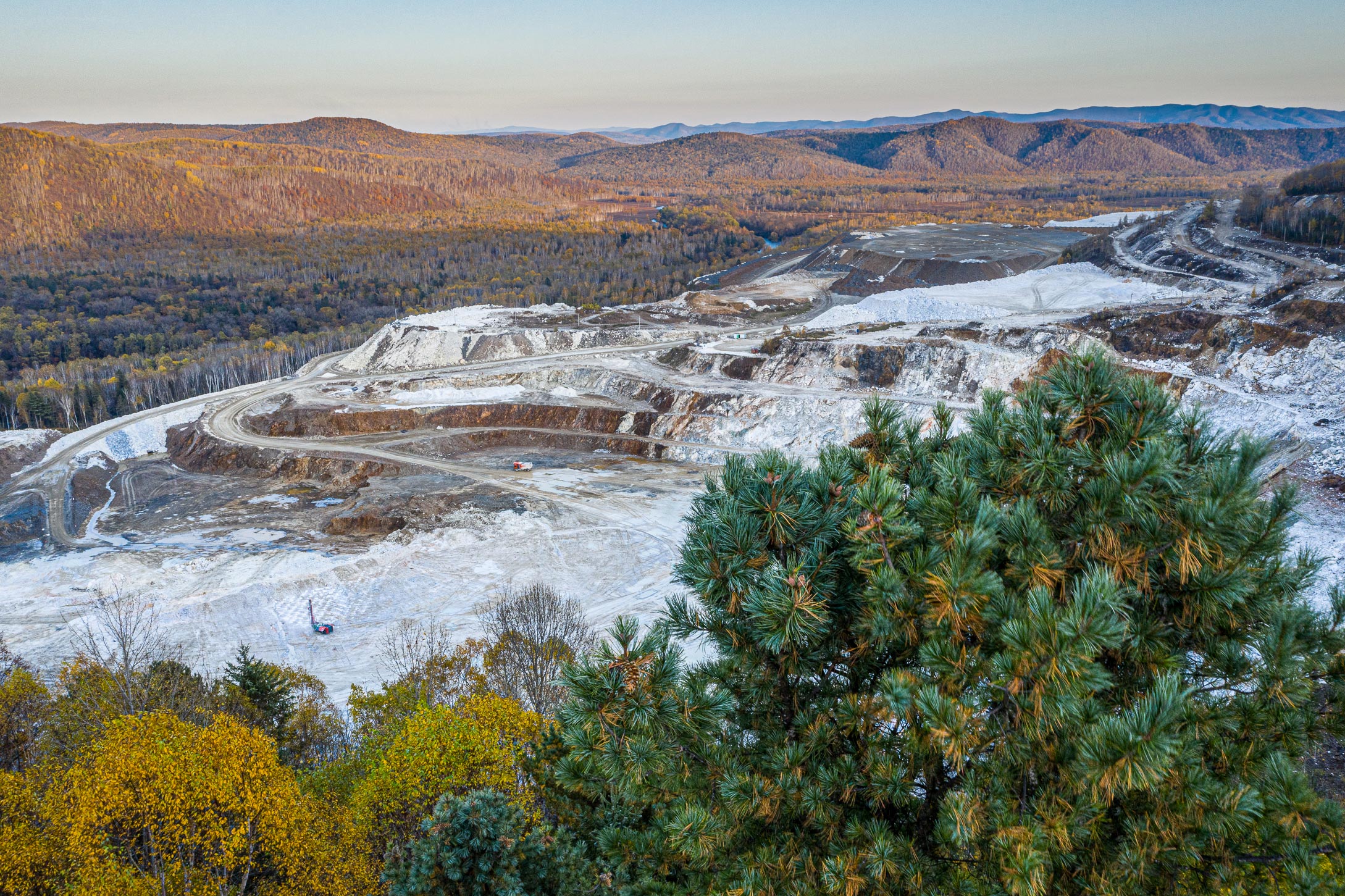
Development of the deposit
Currently, the processing takes place at two milling and sorting facilities. Since 2020, the Brucite+ group of companies has started working on a large-scale project to re-equip the processing complex of the Kuldur mine by, among other things, setting up a modern milling and sorting facility (DSK-3) and introducing a new technology of X-ray absorption (XRT) beneficiation, which will make it possible to obtain products of high chemical purity.
An advantage of XRT technology is that an entire piece, not only the surface, is checked by the emitted radiation, therefore better quality and higher grade Brucite+ products with fewer impurities will be obtained using it. The XRT separator has been launched in a test mode, a permanent placement section is being prepared for it.
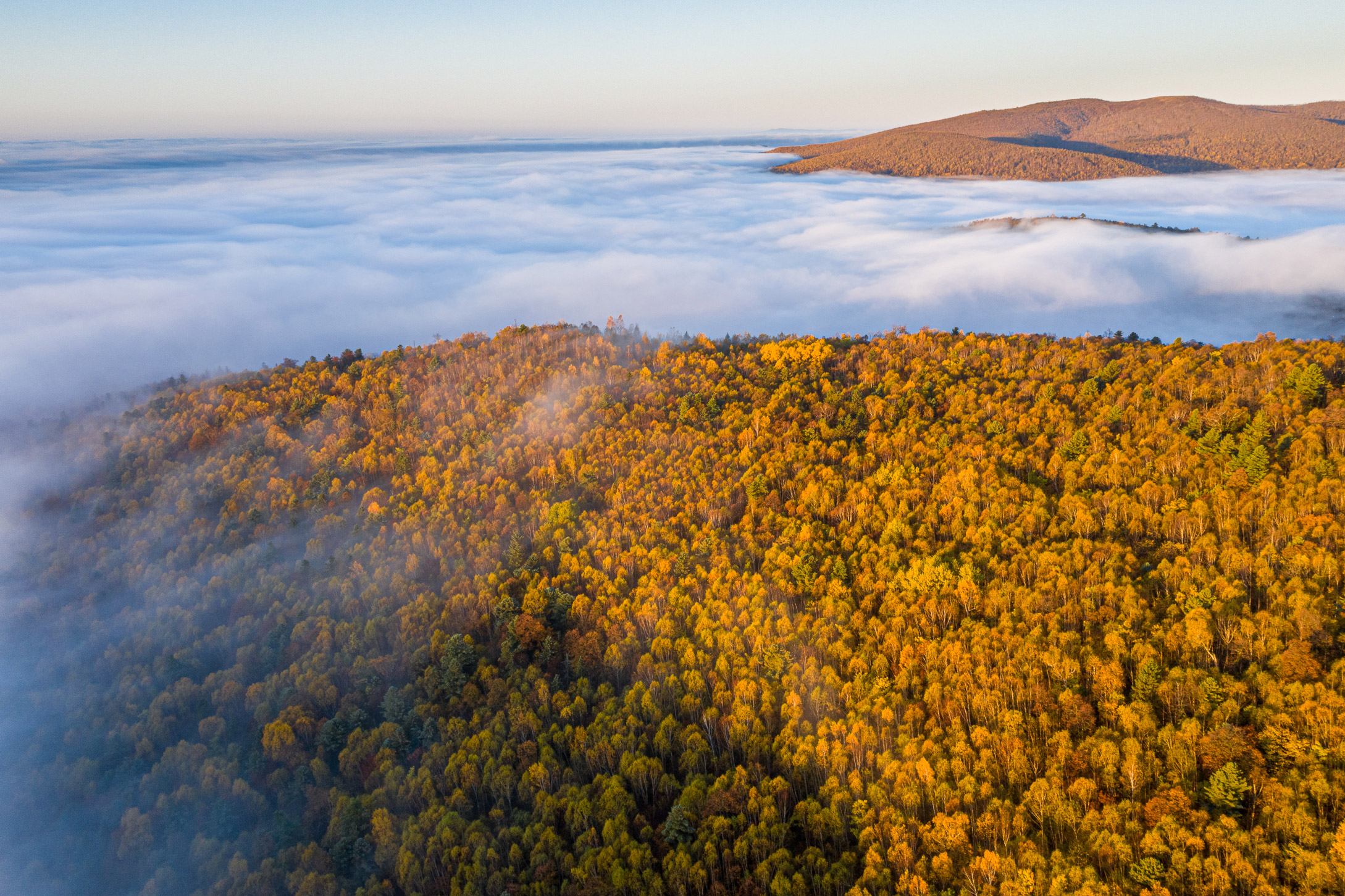
Think green. Think global
Subheader
Sustainability and protection of the environment are at the core of all Brucite+ activities. Brucite+ is striving to achieve carbon neutrality by not only reducing emissions but also offsetting them via carbon dioxide capture. According to conducted research, at present, the amount of carbon dioxide generated during the extraction of 1 kg of minerals at Kuldur is only 9 g, which is already close to 0.
Brucite+ is confident that it is important to do everything in one’s power to protect and restore the environment while rationally using our nature’s riches.
From geology to innovation,
Why LaseTVM-Line
EXPERIENCE
30 years of experience in laser measurement technology for volumetric measurements in mining, steel, bulk material logistics, ports etc.
RELIABILITY
Reproducible, non-manipulable measurements, exclusion of the human error factor.
ACCURACY
Exact determination of volume, excludes inaccuracies due to material moisture.