COMMODITIES
Star commodities: new uses for existing metals
The Covid-19 pandemic has triggered renewed interest in copper as a medical material, highlighting the prospect of alternate uses for minerals across a number of sectors. From platinum fuel cells to aluminium wind turbines, JP Casey considers new uses for existing metals.
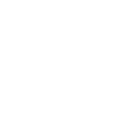
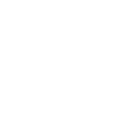
A
s technology has developed, commodities that were once an afterthought have pushed themselves to the forefront of the mining industry, with new uses for old materials driving this change. The fortunes of bauxite in the Democratic Republic of the Congo are often highlighted as an example of this dramatic shift, with the mineral, often used in smartphones, driving a mining explosion that has seen the sector contribute nearly one-quarter of the country’s GDP.
Yet this is not the only example of new uses for old minerals, with the Covid-19 pandemic in particular triggering a swathe of demands for new medical devices, powered by a broad range of commodities. From platinum fuel cells to copper biomedical devices, this shifting demand could help breathe new life into some of the mining industry’s most well-established sectors.
More than half of the country’s coal mines are managed by pro-Russian separatist militia.Credit: DmyTo/Shutterstock.
More than half of the country’s coal mines are managed by pro-Russian separatist militia.
Credit: DmyTo/Shutterstock.
Copper in smart biomedical devices
Copper has long been a popular metal in the medical industry, as it can interfere with the cell membranes of organisms it comes into contact with, preventing processes such as metabolism from taking place. By coating surfaces in hospitals such as bed frames and door handles in copper, bacteria-resistant surfaces are created, helping to stem the spread of disease in these environments.
A four-year study, published in Infection Control and Hospital Epidemiology found that by coating hospital surfaces with antimicrobial copper compounds, the number of healthcare-related infections could be reduced by 58%.
“By coating hospital surfaces with antimicrobial copper compounds, the number of healthcare-related infections could be reduced by 58%.”
More recently, copper alloys have risen to prominence as medical technology has advanced. In August, researchers from the Ecole Polytechnique Federale de Lausanne in Switzerland developed an alloy consisting of platinum, copper, nickel, and phosphorus that can be used to make electrodes for plastic fibres. These fibres are critical to the function of implanted devices that rely on electrical stimulation, such as cochlear implants and devices affecting the brain, complex medical processes that stand to benefit from these new alloys.
The alloys can be used while in a viscous state, making the technology more reliable when compared to existing crystalline metal technology that can only function as a liquid, which can break up into droplets. In addition, the researchers developed a functional fibre that is 50 times smaller than a standard electrode fibre, with this miniaturisation of technology enabling the construction of more precise devices.
Platinum fuel cells
Platinum has seen increased interest from the clean energy sector due to its potential for use in fuel cell technology. The precious metal is particularly effective at converting hydrogen and oxygen into water and electricity, providing a stable base for electrochemical reactions, the cornerstone of many new battery technologies.
Research from the US Department of Energy’s Argonne National Laboratory, published in Science in December 2018, found two new ways to improve the efficiency of platinum used in fuel cells: by changing the shape of the platinum itself to improve the efficiency of the reactions, and developing a carbon-cobalt-nitrogen substrate to support the platinum.
“55% of the world’s processed platinum is already used in catalytic converters.”
However, there are concerns as to the long-term viability of platinum in fuel cells as, despite its electrochemical prowess, the significant cost of producing and purchasing platinum could make platinum-based fuel cells prohibitively expensive. In 2019, German engineering firm Bosch told Reuters that it is aiming to use just one-tenth of the current platinum usage in fuel cell technology in the future.
Indeed, 55% of the world’s processed platinum is already used in catalytic converters, according to Fuel Cell Works, suggesting that the world’s platinum supply chain is integrated with an entirely different solution to vehicle emissions. The fact that catalytic converters are a more short-term solution than fuel cells, which offer a more comprehensive overhaul of the energy industry, further suggests that platinum may not have a long-term future in fuel cell technology.
Aluminium powering renewable energy
One metal with a more stable long-term future is aluminium, which has emerged as a material of choice for renewable power manufacturers. Large-scale solar installations, such as concentrated solar facility Nevada Solar One, have demonstrated the effectiveness of replacing steel infrastructure with aluminium. Despite the latter’s greater per-pound cost, the lightness and flexibility of the metal allows for a greater range of solar panels to be constructed, generating long-term financial benefits.
Indeed, a study from IBIS Associates found that, over a 20-year period, steel-based solar panels would provide no significant advantages over aluminium-based ones. The research found that installation costs were comparable between the two metals, with aluminium costing, on average, $0.12 per watt less for a commercial rooftop installation, and costing $0.009 per watt less in shipping costs to such a project. The report concludes that while aluminium installations are “constrained by their volume before mass, shipping the aluminium systems costs 23% to 66% less than comparable steel designs".
“Over a 20-year period, steel-based solar panels would provide no significant advantages over aluminium-based ones.”
Furthermore, figures from the US Geological Survey reveal that aluminium has a recycling value over three times that of steel, with the 2009 scrap price of aluminium reaching $0.79 per pound, compared to just $0.09 per pound for steel, suggesting that aluminium could have a role to play in a more holistic energy industry that places a greater emphasis on recycling and reuse.
Aluminium has also seen use in wind turbines, with British firm Corex Honeycomb developing an aluminium honeycomb structure, the strength, lightness, and flexibility of which makes it ideal for use in wind turbines. In 2016, the company partnered with TWI, a research and technology organisation, and the EU to develop an “embedded early failure crack detection sensor”, a pilot wind turbine, built using Corex’s honeycomb structure, that was able to identify and report potential structural damage before it interfered with operations.
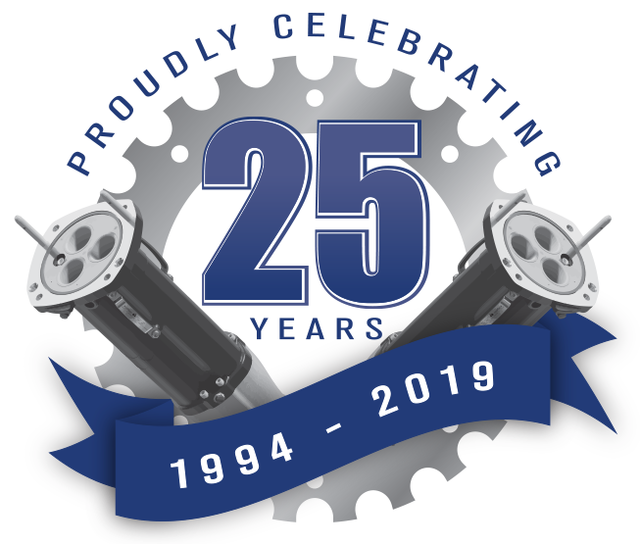
AusProof is celebrating 25 years of business in Australia in 2019.
Silver in industrial processes
Silver has been a mainstay of the industrial sector and accounted for more than half of the world’s industrial demand for metals over the last five years. The precious metal has a range of uses, from soldering alloys to use in LED chips, and is one of the most flexible metals used in industrial processes.
The metal has also received significant attention from the clean energy sector, with the high electrical and thermal conductivity of silver making it an excellent candidate for use in solar panels. Global silver demand from the solar industry increased by 20% in 2017 as the world shifts towards a greater reliance on clean energy, and the growing small-scale solar industry, which is seeing more panels than ever sold to and installed by members of the public.
“Global silver demand from the solar industry increased by 20% in 2017.”
Yet these positive trends are somewhat hampered by the demand for silver as a luxury good, used, for instance, in jewellery and art, which has driven its price to prohibitively high levels. Research from Kent Business School found that despite the average solar panel only containing 20g of silver, this accounted for 6.1% of the price of building that unit, making silver as expensive as it is necessary.
Furthermore, the fact that silver has extensive uses in both the luxury and industrial settings means its price is affected by changing market conditions in both environments, making the metal considerably volatile. The Kent study found that the price of silver increased considerably after the 2008 recession, and the 2011 increase in oil prices, showing that the price of the metal increased at precisely the points at which people were interested in pursuing new forms of cheap and low-cost energy generation. These financial concerns make silver an unstable industrial investment, despite the stability and reliability of the metal itself.
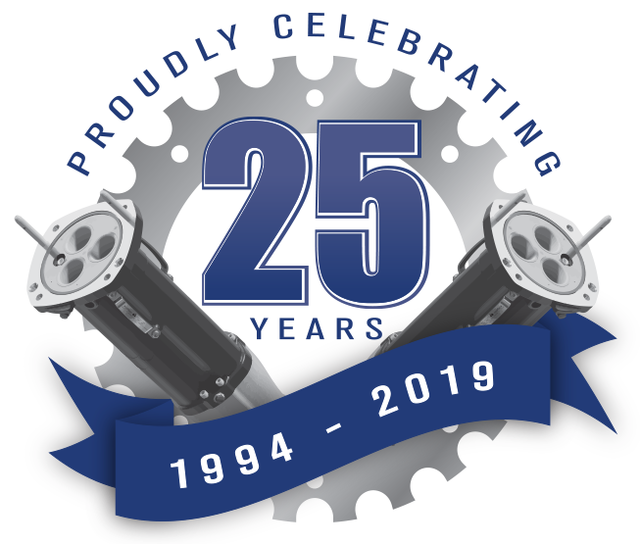
AusProof is celebrating 25 years of business in Australia in 2019.