Feature
Fuels and lubricants: navigating emissions reduction from mine fleets
Caroline Peachey reports on the challenges around emissions reductions in off-highway fleets, focusing on the role of renewable fuels.
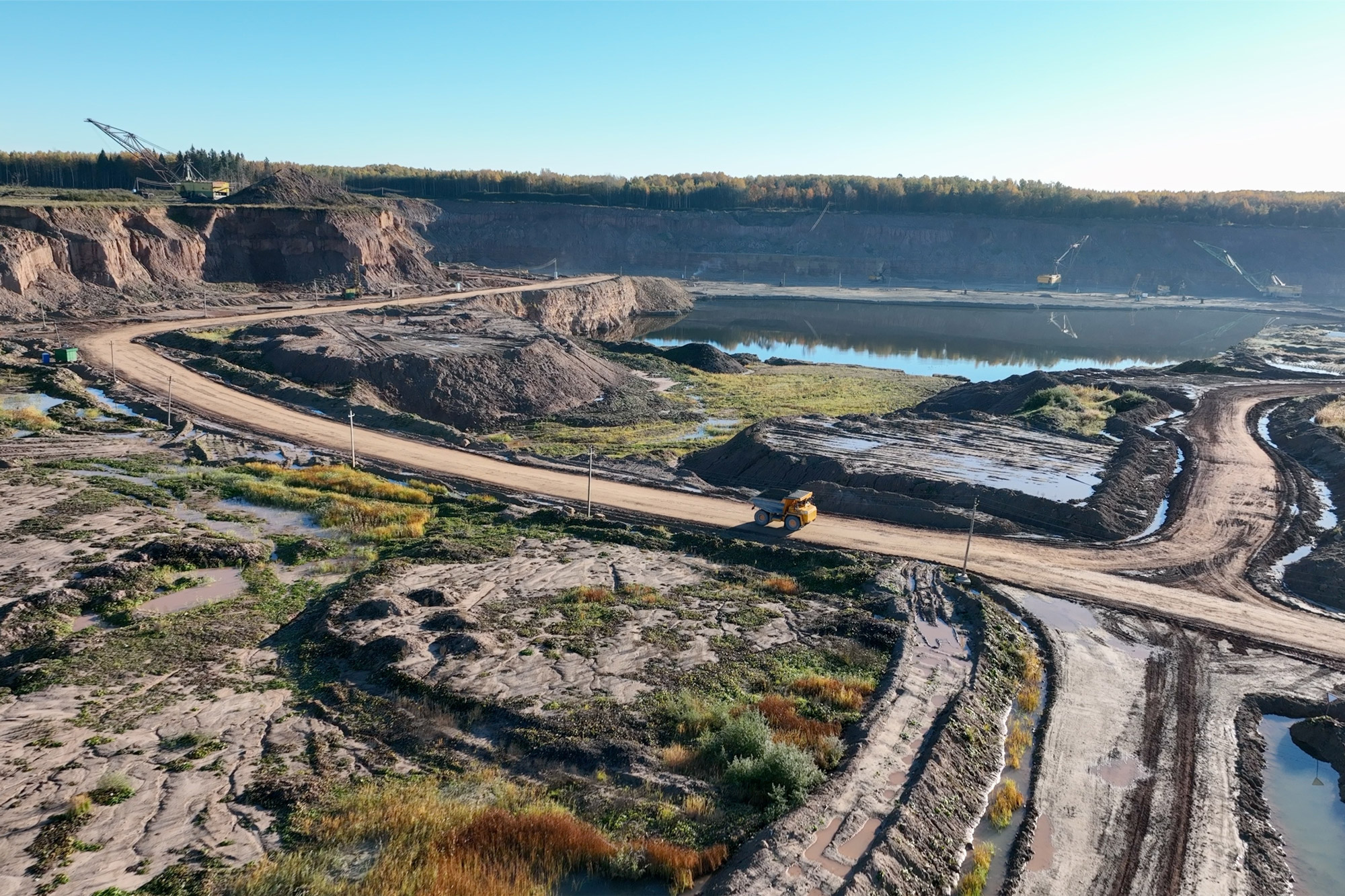
Credit:
Most mining companies are aiming to achieve net-zero emissions by 2050 or sooner, in line with the ambitions of the Paris Agreement. Meanwhile, many have interim targets to cut scope 1 and 2 emissions by between 30 and 50% by 2030.
These near-term targets are often based on the potential to transition from fossil-fuel-generated power, either by installing renewables such as solar PV on-site or entering into power purchase agreements (PPAs) with utilities or independent power producers.
Harmony Gold, for example, is targeting a 63% decline in emissions by 2036 (from a 2021 baseline), with a significant proportion coming from a move to renewables from principally coal-fired grid power in South Africa.
In fact, a recent survey by GlobalData found that on-site renewable power is seen as the most viable option for minimising mine site emissions through to the end of the decade. Other decarbonisation options included battery/electric vehicles, hydrogen-powered vehicles, the use of sustainable fuels and renewable energy PPAs.
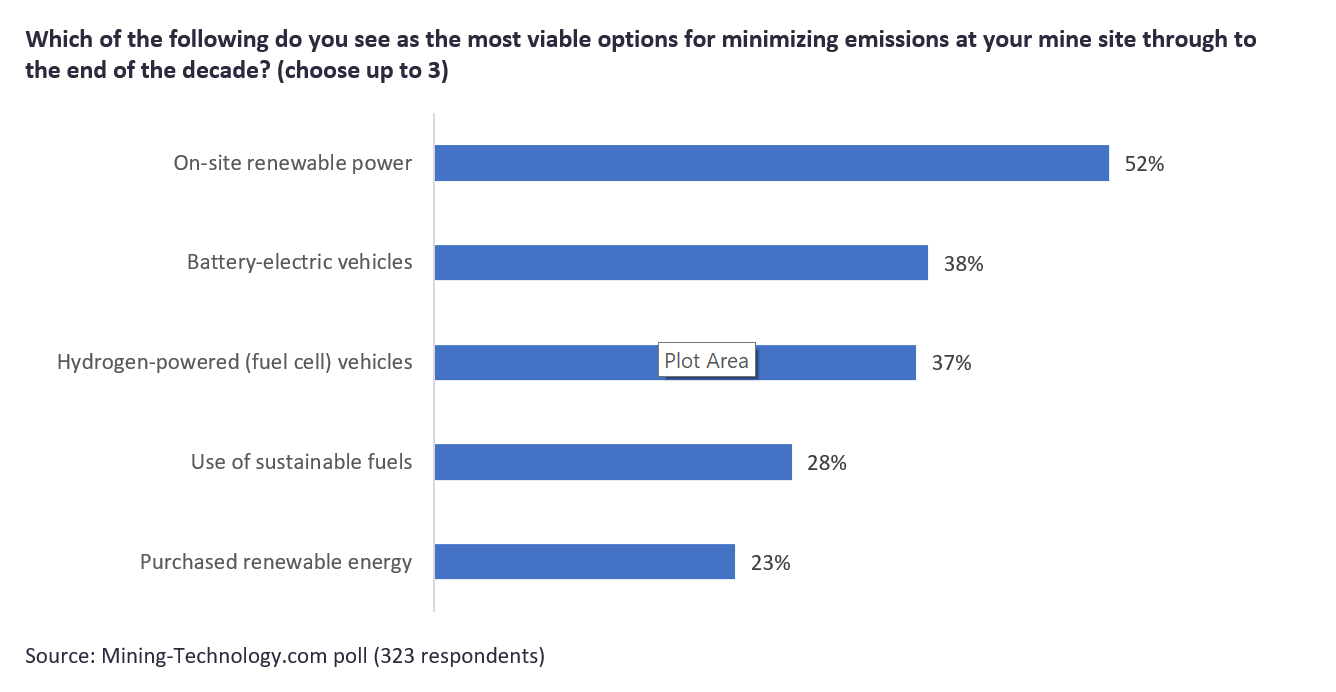
Caption. Credit:
Fleet emissions reduction: progress and opportunities for miners
In 2022, scope 1 and 2 emissions were down by an average of 14% relative to 2018, for 85 leading mining companies. A further fall in emissions is projected for 2023, according to GlobalData.
De-fossilisation of power sources is responsible for a large proportion of this drop. However, in the short term, miners also need to reduce scope 1 emissions from the heavy machinery used on-site – an area where progress has been “quite limited” to date.
Companies are adopting renewable diesel and biofuels as a “transition pathway” to achieve interim emissions targets, alongside other benefits.
“Companies are planning to shift to battery-electric or possibly hydrogen-powered machines in order to progress towards net zero… as well as achieve other benefits related to productivity, vehicle lifespan and running costs,” explains David Kurtz, director of research and analysis at GlobalData.
“However, the take-up of battery-electric machines is currently low, with ongoing trials and need for further technology development. Expectations are for switching to take place primarily during the 2030s,” he adds.
Meanwhile, companies are adopting renewable diesel and biofuels as a “transition pathway” to achieve interim emissions targets, alongside other benefits.
Moving away from diesel fuel to support emissions reduction
Mobile diesel accounts for a significant share of operational mine emissions – anywhere from 25% up to 90% of scope 1 emissions for surface mines, GlobalData says.
As more fossil fuel power gets replaced with renewables, the proportion of emissions from mobile diesel is projected to keep rising. BHP, for example, has seen its share of scope 1 and 2 emissions from mobile diesel increase from 40% in 2020/21 to 61% in 2022/23.
BHP has teamed up with BP to trial the use of a blended HVO (hydrotreated vegetable oil) diesel at its Yandi iron ore mine in Western Australia’s Pilbara region. The trial “provided valuable insight and knowledge in renewable diesel”, with BHP saying that the results will be used to determine how renewable diesel may be “a practical complementary transition pathway” to its operational decarbonisation plan.
Mining giant Rio Tinto has already made the shift to biofuels. In May 2023, its Boron operation in California became the world’s first open-cut mine to fully transition all its heavy vehicle fleet to renewable diesel, reducing emissions by up to 45,000 tonnes per annum (tpa) of CO₂ equivalent.
In 2024, Rio is also planning to replace fossil diesel with renewable diesel in 90 haul trucks, all heavy machinery, the concentrator, smelter and refinery, at its Kennecott copper mine in Utah. This transition would cut Kennecott’s scope 1 carbon emissions by approximately 495,000tpa of CO₂ equivalent.
Combined, both initiatives would replace 11% of Rio Tinto’s global fossil diesel consumption, according to Rio Tinto’s chief decarbonisation officer Jonathon McCarthy.
Speaking in December, McCarthy explained: “The use of drop-in fuel such as renewable diesel will allow Rio Tinto to reduce emissions in the short term, complementing ongoing work towards the commercial readiness of longer-term technical solutions such as battery electric haul trucks.”
In May, Rio Tinto announced it would collaborate with fellow mining giant BHP to trial battery-electric haul trucks in Western Australia’s Pilbara region. As part of that collaboration, two Cat 793 haul trucks will be trialled from the second half of 2024, and two Komatsu 930 haul trucks tested from 2026. One truck will be trialled by each of the miners, and the trial outcomes shared.
Vale teams up with Komatsu and Cummins on ethanol-diesel trucks
Recently, Vale, Komatsu and Cummins revealed a collaboration to develop dual fuel large trucks, with payloads of 230–290 tonnes, powered by ethanol and diesel.
This effort will support Vale’s goals of cutting scope 1 and 2 carbon emissions by a third by 2030 and becoming net-zero by 2050. Diesel emissions from mine operations account for 15% of Vale’s direct CO₂ emissions, with haul trucks the biggest consumers of diesel and thus the biggest emitters, according to the company.
"Removing a fossil fuel like diesel from our mine operations is fundamental to achieving our decarbonisation targets,” says José Baltazar, engineering director for mine and plant operations at Vale.
“Applying the solution to the existing fleet, without the need to immediately purchase new trucks, is an excellent way to move forward with the decarbonisation process, while also maintaining our focus on reliability and production efficiency," he adds.
Over the next two years, work is expected to encompass development, testing and implementation of ethanol-diesel engines manufactured by Cummins. The aim is to retrofit existing diesel engines in haul trucks to run on a mix of up to 70% ethanol and diesel, which could reduce direct CO₂ emissions by up to 70%, Vale says.
The decision to develop an ethanol-based solution is driven by its availability within existing supplier networks and high adoption rate in Brazil, where Vale is headquartered.
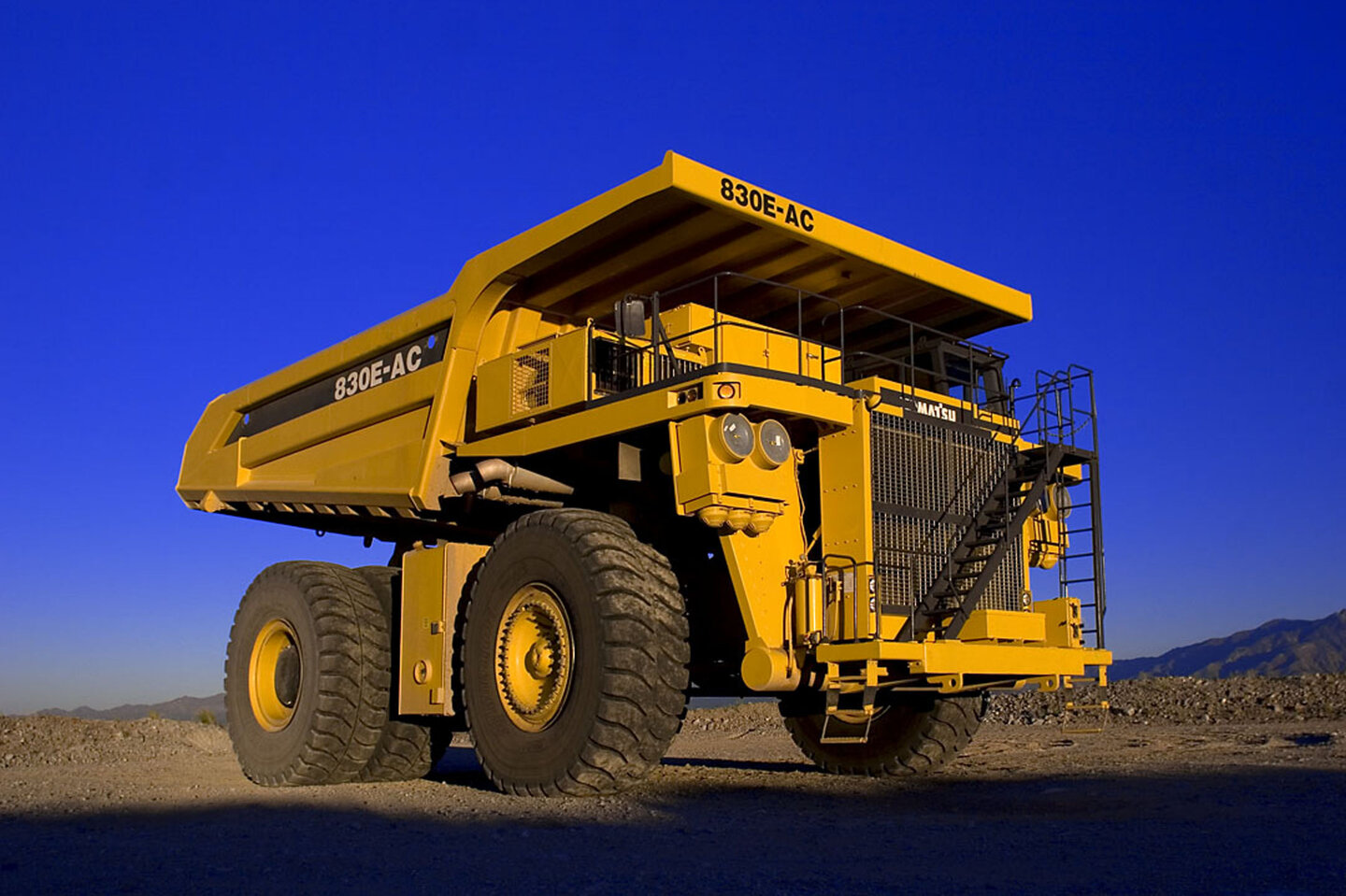
Komatsu and Cummins have teamed up with Brazil-based miner Vale to develop ethanol-diesel powered haul trucks. Credit: Komatsu
How can miners optimise existing diesel fleets?
Diesel-powered heavy equipment is deeply embedded in the mining industry. Despite ongoing trials and plans to switch to battery-electric vehicles by mine operators including Anglo American, BHP, Glencore, Newmont, Rio Tinto, Teck and many others, widespread deployment is not expected until the 2030s.
“A challenge… with mining is that you can switch to battery power for smaller machines, but those that are larger need more power, making supply by diesel the better option,” explains Kurtz.
“That can only help to reduce the emissions over the next ten to 20 years when viable, fully zero-emission solutions are developed.”
Ensuring the existing diesel-powered fleets are operating efficiently and reliably could offer some emissions reductions as well as other benefits.
Teck, for example, has an agreement with Caterpillar to deploy 30 zero-emissions large haul trucks by 2030. However, that isn’t expected to begin until 2027. Anglo American is investing in a hydrogen-powered haulage system, designed in partnership with First Mode. Initial trials have taken place at the Mogalakwena mine in South Africa, with plans to roll out to 5–7 priority sites by 2030.
Switching from fossil diesel to biofuels in the interim can be costly, disruptive and may not be feasible for all mine sites. For these mine operators, ensuring the existing diesel-powered fleets are operating efficiently and reliably could offer some emissions reductions as well as other benefits. One way to do this is through selecting the optimal lubricant.
According to Texaco, lubricant additives account for up to 90% of the ash collected in diesel particulate filters (DPFs), whereas just 10% comes from wear metals and contaminants.
Equipment manufacturers build in complex algorithms to ensure that DPFs are actively regenerated. However, this involves injecting more fuel, which Eddy Devries, Texaco Lubricants’ manager for Europe OEMs, explains can have a significant impact on the cost of operations, with fuel typically accounting for about 25% of these costs.
A further consideration, says Devries, is that since China and India have introduced standards that require DPFs, this has put some pressure on the DPF supply chain, further incentivising operators to run machines for as long as possible.
Speaking during a recent webinar hosted by MINE’s parent company, GlobalData, Devries shared examples of the impact changing engine lubricant can have. One trucking company in the US reduced its fuel consumption by 61% and extended engine life by 2.5 million miles by switching oil.
Companies outside of mining have successfully reduced fuel consumption by effective route planning, although this is not likely to be a solution for this industry.
Back to the mining sector, there have been several successes implementing biofuels in off-highway fleets, as a bridge to battery technology. As Lisa Archbold is vice-president business development & low carbon solutions, BP Australia, said in March: “In the short to medium term, renewable fuels are the most viable decarbonisation solution for the mining, heavy transport and aviation sectors.”