Feature
Evolving landscape: the future of Australia's iron ore industry
Australia's iron ore industry faces challenges due to falling demand and shifts in steel production, but as Smruthi Nadig discovers, miners are making efforts to decarbonise.
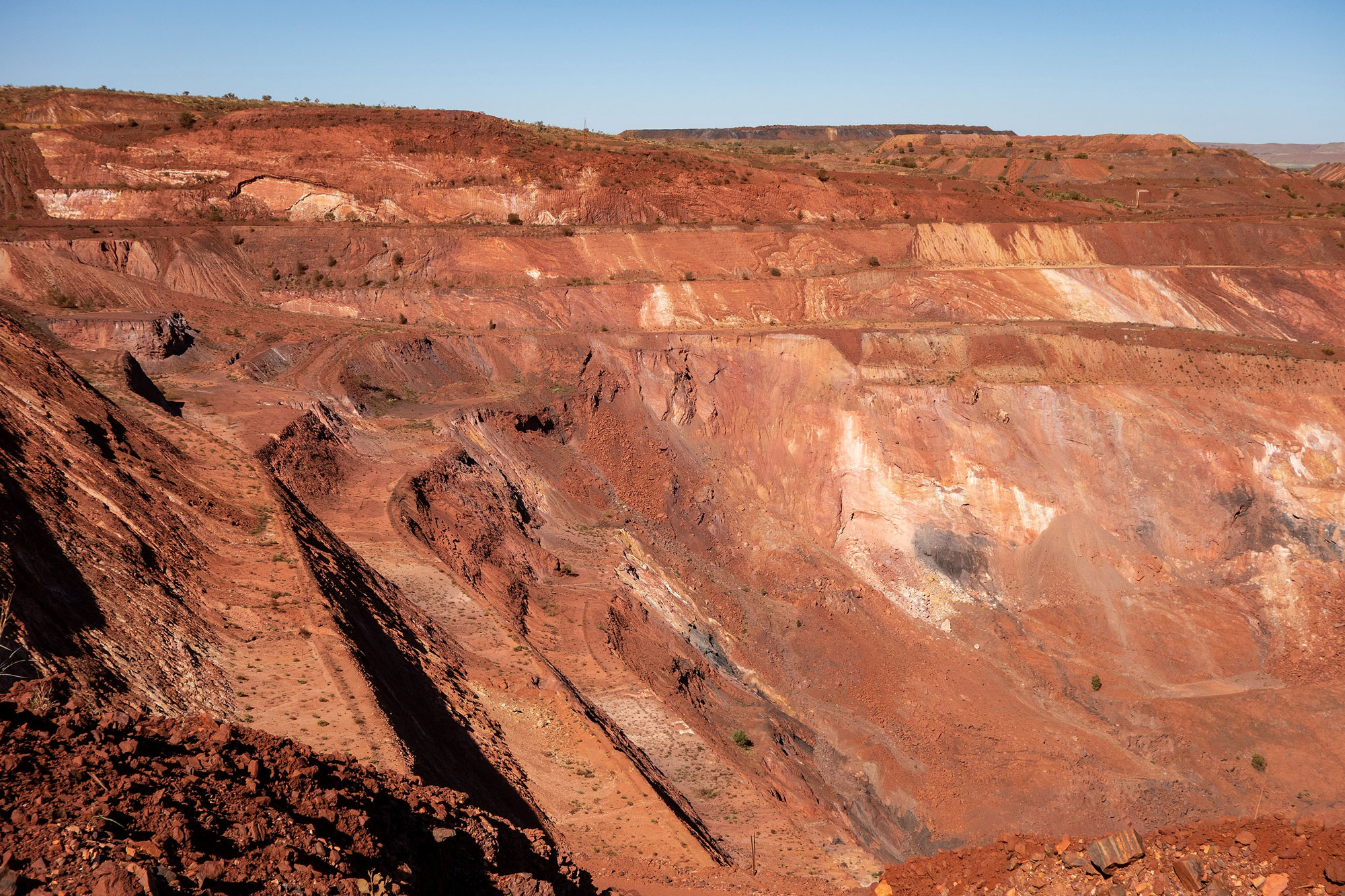
An active deep pit of red iron ore in the Pilbara region of Western Australia. Credit: Mino Surkala / Shutterstock
Australia maintained its iron ore production at around 945 million tonnes (mt) in 2023, with a 3.1% increase projected for 2024, GlobalData reports. By 2030, production is expected to reach 1.22 billion tonnes (bt), driven by various upcoming projects and expansions, including the Onslow project (2024), the Jimblebar Expansion project (2024) and the Western Range project (2025), all located in the Pilbara region of Western Australia (WA).
Despite these growth projections, Australia's iron ore industry is experiencing a period of transition and uncertainty due to factors such as shifts in global steel production, decarbonisation efforts and changing demand from key markets like China. What does this mean for Australia’s iron ore miners?
Challenges facing Australia's iron ore sector
Australia is facing significant challenges in its efforts to expand iron ore production. Iron ore and concentrates exports, valued at $89bn (A$136bn) last year, currently account for a fifth of the country’s total exports.
Decreasing steel demand in China, which currently relies heavily on Australia’s coking coal and iron ore, as well as a broader shift towards lower-carbon alternatives, are both concerns.
“As China transitions away from traditional steelmaking processes and towards scrap metal and direct reduced iron (DRI), the demand for Australia's high-grade iron ore is expected to diminish. This fundamental shift in the industry could lead to increased price volatility as supply and demand dynamics adjust,” says Vinneth Bajaj, GlobalData’s project manager.
The Institute for Energy Economics and Financial Analysis (IEEFA) says that Chinese imports account for 76% of global iron ore trade.
In 2022, China accounted for 83.7% of Australia's iron ore exports, importing 743.1mt.
As China transitions away from traditional steelmaking processes and towards scrap metal and direct reduced iron (DRI), the demand for Australia's high-grade iron ore is expected to diminish.
Australian miners face both risks and opportunities as steel producers work to cut carbon emissions given the uncertainty surrounding the best low-carbon steel production technology. Simon Nicholas, IEEFA’s lead analyst for the global steel sector, told Mining Technology that “the big miners will continue to focus on keeping their costs down”. Most, he adds, “are focused on producing more high-grade iron ore suitable for low-carbon steelmaking” as steelmakers shift from blast furnaces to DRI technology.
DRI primarily uses non-coking coal, natural gas or hydrogen as an energy source to produce ‘sponge iron’. According to research by Ling et al this process reduces CO₂ emissions by up to 61% compared with traditional ironmaking.
Regardless of whether it is based on green hydrogen or gas, DRI requires iron ore of a “significantly higher grade than most Pilbara production”, Nicholas says. Therefore, the global demand for iron ore will likely move towards “higher quality as steelmakers transition to DRI”.
Progressing towards ‘green’ iron and steel
The global mining industry is evolving as companies invest in research and development to address decarbonisation and changing market demands.
In Australia, Rio Tinto has allocated $143m (A$215m) to establish a facility to evaluate the efficiency of its low-carbon ironmaking process, BioIron, which could assist in decarbonising the global steel supply chain.
Rio Tinto, BHP and BlueScope are also collaborating to explore the development of the first ironmaking electric smelting furnace pilot plant in Australia. This partnership aims to produce molten iron from Pilbara ores using renewable power and DRI process technology.
On announcing the venture in February, Rio Tinto iron ore chief executive Simon Trott said: “The carbon intensity of iron and steelmaking requires profound change to meet the needs of our planet and our climate objectives.”
In another instance, BHP is working with global partners and stakeholders to achieve net-zero Scope 3 emissions by 2050. The company says it has made significant progress in its strategy related to steelmaking and maritime decarbonisation through partnerships, trials and pilot programmes. BHP has partnered with major players in the steel industry including Tata Steel and ArcelorMittal, which jointly account for 17% of worldwide production.
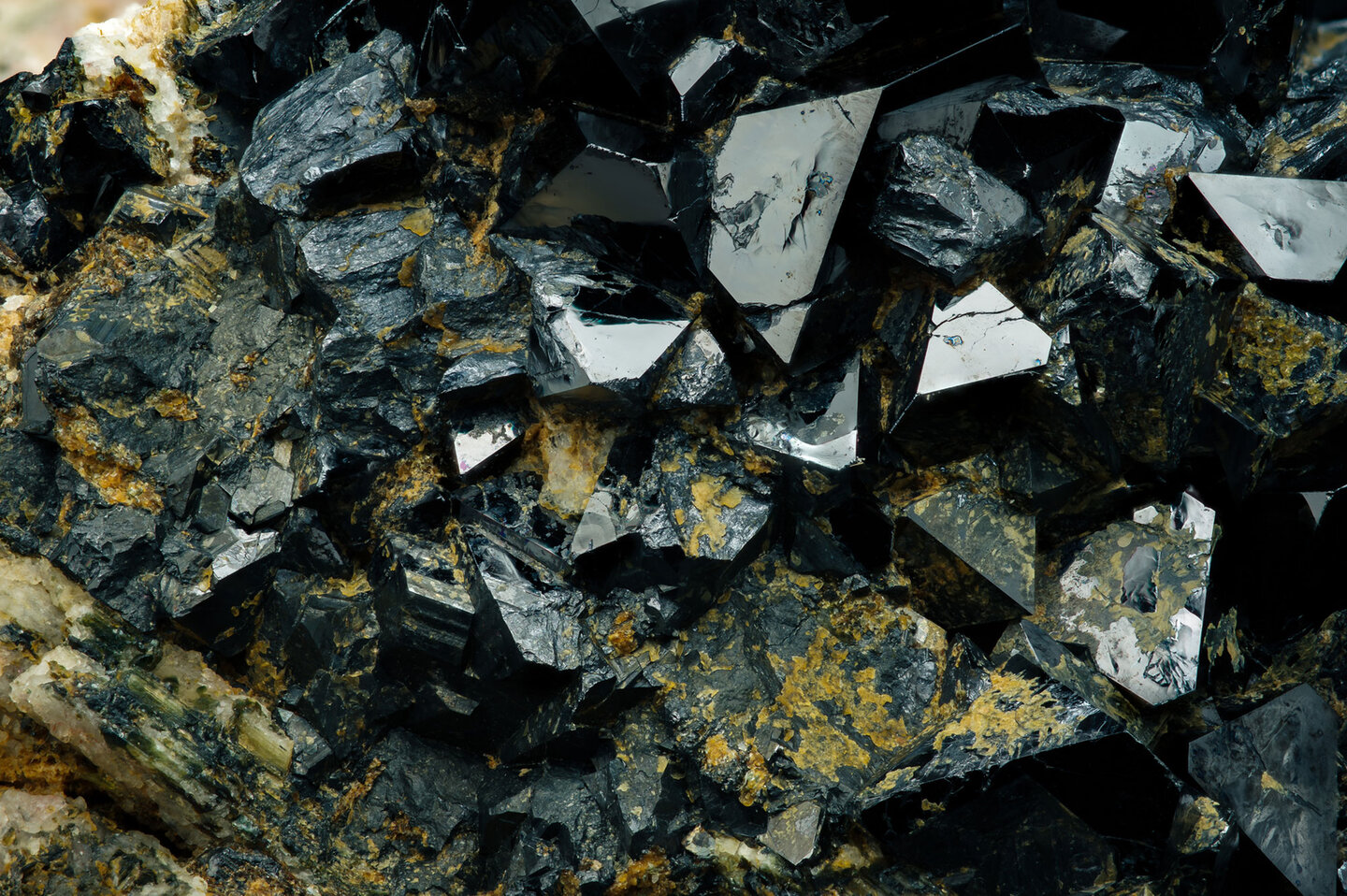
Several major mining companies in Australia are moving away from steel production due to reduced demand from China. Others are focusing on higher-grade magnetite ores.
The IEEFA analyst says that Fortescue is increasing production at the high-quality magnetite Iron Bridge project in WA and investigating a high-quality deposit in Gabon.
However, Nicholas contends that BHP stands out and does not aim for higher-grade ore. BHP believes that steel decarbonisation will occur by adding carbon capture and storage units to blast furnace-based steel plants, despite the growing realisation that “this is not realistic”.
He added: “So if Australia is not to see iron ore export revenues even further impacted, Australian miners will need to target higher-grade magnetite in response or find ways to allow the use of lower-grade ore in DRI-based steelmaking – something they are already working on.”
Bajaj says that Australia is also implementing several strategies to mitigate overreliance on the Chinese market. “These include expanding into new territories such as India, Japan and South Korea to diversify the customer base and upgrading product offerings to higher-value segments like lump ore and premium magnetite. This dual approach aims to reduce vulnerability to market fluctuations and capture greater profit margins.”
Australian iron ore’s future outlook
Australian mining companies have made efforts to allocate substantial funds towards hydrogen and clean energy technologies by the end of the fiscal year in June 2024. Foreign investments also have the potential to revolutionise the country's iron ore production methods.
“While the short-term volatility persists, the long-term vision involves transforming Australia into a global hub for hydrogen-based steel production, leveraging its abundant renewable energy resources and iron ore reserves. This transition promises economic growth, job creation and reduced emissions but requires significant investments,” says Bajaj.
For example, POSCO, a major South Korean steel manufacturer, is “looking at producing DRI in the Pilbara and shipping it as hot briquetted iron to South Korea, but it is very early days”, Nicholas says.
In a report, the IEEFA analyst also highlights how Nippon Steel is evaluating a $700m (Y102.81bn) investment in hydrogen-based green steel production outside of Japan, and China Baowu Group is exploring a green iron project in WA.
He adds that steelmakers are considering “locating ironmaking plants where there is suitable iron ore and green hydrogen can be produced at lower cost, including Australia,” which has attracted several foreign investments into WA.
Bajaj believes that Australia is emerging as a global hub for producing green steel using hydrogen. “The country's abundant solar and wind resources, as well as a favourable investment environment, are attracting significant foreign investment,” he states. Additionally, Australia's vast iron ore reserves ensure a reliable source of raw materials, further solidifying its position in this expanding industry.
The long-term vision involves transforming Australia into a global hub for hydrogen-based steel production, leveraging its abundant renewable energy resources and iron ore reserves.
Australia should also maximise investment in magnetite mines for domestic use and export to achieve carbon emissions targets and manage Scope 3 emissions associated with iron ore mining. Fortescue and Liberty Steel Group already aim to use magnetite ores to produce high-grade iron ore and low-emissions steel.
According to the IEEFA analyst, this change could reduce the expense of the worldwide steel industry's move away from fossil fuels. Yet, foreign governments and steel companies might hesitate to transfer iron ore production to a different country. He argues that Australian authorities must collaborate with overseas governments to guarantee a future demand for Australian environmentally friendly iron exports.
Meanwhile, both state and federal governments have launched initiatives to support green iron and steelmaking in Australia.
Liberty Steel plans to replace coal-based steelmaking at its Whyalla Steelworks with low-carbon electric arc furnaces and DRI production, reducing carbon emissions by up to 90%. The Australian Government has provided $63.2m to support this initiative, with the South Australian Government pledging a further $50m. South Australia holds more than 18bt of magnetite ore and plans to lead in global iron and steel decarbonisation, supported by its government’s Green Iron and Steel Strategy, which aims to establish a new DRI plant by 2030.
Additionally, in May 2024, the Albanese administration announced its plans to introduce a short-term Hydrogen Production Tax Incentive. This time-limited, refundable tax offset with no cap would encourage renewable hydrogen production for qualifying Australian companies. Andrew Forrest, Fortescue's executive chairman, believes this incentive will “fast-track the development of a green iron industry in Australia, bringing massive employment opportunities… and slashing steel production’s debilitating global emissions”.
Fortescue is testing its green hydrogen technology at its Chichester operations, one of the world's largest iron ore producers. It is also collaborating with the government on its Christmas Creek Green Iron Plant in Pilbara, WA, which is targeting its first production in 2025.
Realising this potential necessitates substantial investments in renewable energy infrastructure and hydrogen production facilities, which may pose challenges in the initial stages.
Bajaj adds: “A pivotal benefit is the substantial reduction in greenhouse gas emissions from the steel industry, aligning with Australia's climate goals. However, realising this potential necessitates substantial investments in renewable energy infrastructure and hydrogen production facilities, which may pose challenges in the initial stages.”
Meanwhile, several companies still argue that Australia must maintain coal's important role in steelmaking. BlueScope plans to continue using coal-based technology, stating that green technology is not yet available, according to IEEFA. Nicholas states that BHP, a significant exporter of metallurgical coal, is motivated to influence steelmakers to reduce carbon emissions while still advocating coal use.
Despite lower demand from China, the IEEFA analyst suggests that there will be a big increase in iron ore mining in Australia, Brazil and Guinea, leading to oversupply and lower prices. Australia's economy will likely be affected, but some companies shifting to green mining technologies could change the scenario for the region.