Company Insight
Sponsored by myosh
Advanced critical control management on the myosh platform
Designed to suit mining operations of any scale, myosh has created an all-in-one CCM framework that bridges practical necessities with the latest compliance demands. The system links instantaneous inspection results to auditable records, displayed in an intuitive digital bow-tie format for critical controls.
Main image credit:
As an Australian software company founded in 2003, myosh has spent over two decades refining its comprehensive suite of health, safety, environment, and quality management modules. With recent legislative changes in Queensland increasing pressure on mine safety, myosh is deploying its most advanced iteration of the flagship Critical Control Management module, allowing workers to feed real-time data into the software engine.
The problem
As mining operations have grown more complex in the information era, the industry has faced significant challenges. Companies have been driven to seek innovative solutions that address both productivity and comprehensive safety concerns to meet rising social and legislative expectations.
The most recent example of this is the amendment of Queensland’s Resources Safety and Health Legislation Amendment Act on the back of the Grosvenor mine explosion and fire. The new laws now require mine and quarry sites to incorporate critical controls as part of the mine’s safety and health management systems.
Critical controls are the last, or major, line of defence against Material Unwanted Events (MUEs), such as uncontrolled explosions and fires. The concept of a bow-tie diagram has been employed for decades, as a means of graphically illustrating the MUE prevention strategy.
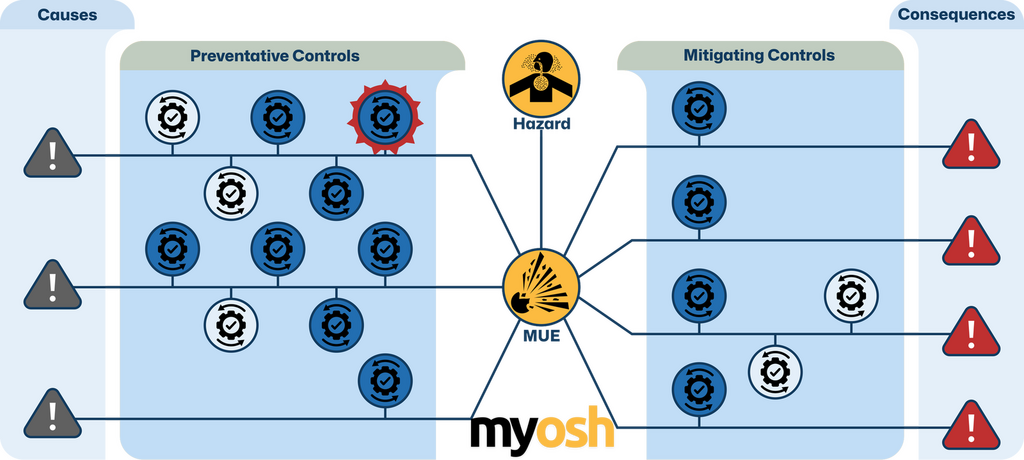
A bow-tie diagram provides a visualisation of the relationship between initiating causes, preventative controls that reduce their probability of triggering the MUE, and the mitigating controls that reduce the severity of the potential consequences.
The problem is that static bow-tie diagrams and excel spreadsheets of control verifications are no longer capable of keeping up with the pace of modern efficiencies in speed and complexity. This is largely because of the increased number of controls that can now be deployed, and the increasing requirements for a rapid feedback cycle on the status of these controls.
The solution
myosh has been working closely with companies in the mining sector to develop a Digital Bow-Tie interface that addresses the pain points of modern Critical Control Management.
First, user simplicity
Complexity should be in the background. According to Adrian Manessis, Director at myosh, "The system should fit in with everyday processes. It shouldn't add to your existing workload. People are busy enough already, they don't want to be adding extra things and employing more people just to do these tasks - and, in fact, it's not necessary."
What this looks like today is a system that allows personnel on site to simply perform unbiased inspections, with results immediately generating verification records in the background.
Second, system configurability
No cookie-cutter approach can fit the diversity of situations in which a comprehensive CCM framework could be deployed. So, while the complexity of the system is tucked in the background, myosh has taken the approach to make the ‘wires and switches’ entirely available to the safety management team using it, culminating in the myosh Rules Engine. Their Rules Engine functions similarly to email inbox rules, determining which data inputs feed into what actions inside the system.
As Adrian explains, "The system is fully configurable. Every single form that you see in the system and every single report, you can actually build yourself. Whether it's workflow, whether it's access to the system, whether it's the information that you capture, the whole thing is configurable. We start off with a basic build of the system, but our users then go through and change it, and they can change it on an ongoing basis. Right, to an advanced level. And it's not rocket science, it's no programming. It's all just configuration checkboxes and radio buttons."
Third, speed and convenience
Adrian, who led the latest CCM and Bow-Tie module developments, believes “Ease of use is the most important thing [...] something that's not going to impact the people within the organisation and their day-to-day tasks to any significant degree. If it's simple, they'll use it. And if they're engaged in the process - if they're involved in the process - they will also use it and they will rigorously and willingly do those inspections."
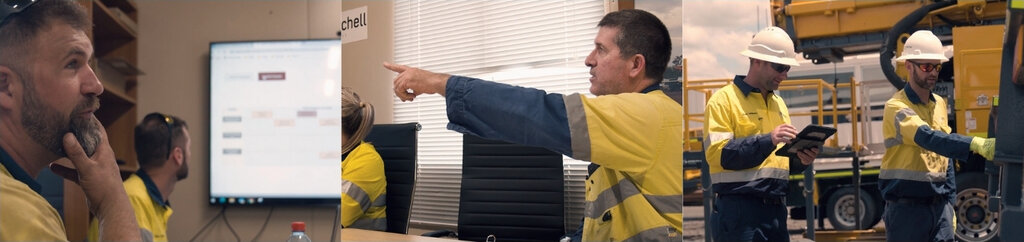
Interactive and configurable cloud-based platform that allows all stakeholders to participate in the CCM strategy.
Inside the myosh platform, the bow-tie interface not only feeds in from on-site inspection data, it also functions as a template for setting up the matrix of controls around an identified MUE hazard. This allows safety teams that use it today to quickly spin up critical control strategies, using guided flows that require the minimum amount of input to set up all the necessary digital records that are then subject to verification audit trials.
Towards more effective risk management in mining
The digital transformation of Critical Control Management marks a significant shift from static diagrams and files to dynamic, real-time risk management. While advanced platforms offer promising features in user engagement and configurability, their success hinges on effective implementation and worker adoption. As the mining industry evolves, companies should evaluate their current CCM practices, considering whether digital solutions could enhance their ability to prevent and mitigate critical events. Ultimately, the goal remains to create safer work environments in this challenging industry—a mission on which myosh is proud to collaborate with dedicated safety teams across the sector.