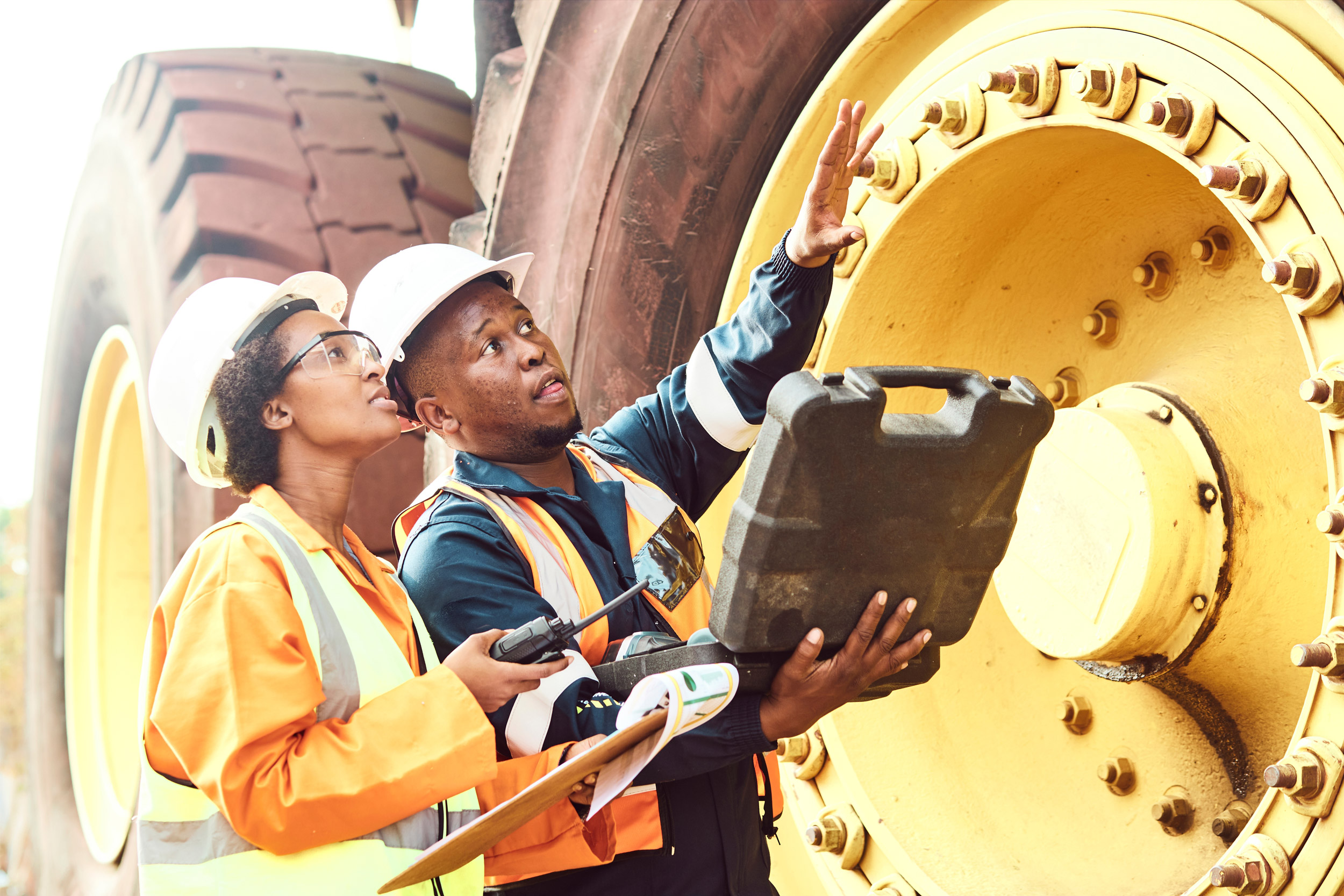
Digital Transformation
Digital transformation: how Australian mining is embracing technological innovation
To increase productivity and take necessary safety measures, Australian miners are investing in AI, sensors and tunnel safety optimisation. Smruthi Nadig investigates.
Mining and ore excavation is one of the oldest professions, as the world’s appetite for mineral wealth has rarely diminished over human history. While demand for metals and ores has not changed over the generations, the processes involved in mining have changed considerably; over the years, the mining industry introduced cutting-edge technologies, such as cloud, artificial intelligence (AI), robotics, and big data, to improve operations.
Yet the path is not obvious as to the future of technological innovation. On one hand, the mining industry is encouraged to maintain a sense of the status quo; with human lives and environmental security at risk, drastic changes are unlikely to take place. On another, there exist a range of technological inventions for companies to choose from, and it is unclear which will continue to make an impact in the long-term.
The World Economic Forum in 2016 outlined four major digitalisation trends: automation and operational hardware; the digitally-enabled workforce; integrated enterprise, platforms and ecosystems; and next-generation analytics and decision support.
These trends could be increasingly appealing to miners around the world. According to Infosys’ report, over the last decade, global mining operations have seen productivity decline by 28% compared to a decade ago. Due to increasing costs, a shortage of skilled labourers, market volatility and more stringent regulatory compliance, the industry has had to look for ways to improve efficiency and productivity.
This is where Australian mining has, historically, led the world. From the vast autonomous operations in the Pilbara to government funding for a range of academic courses and projects, Australian mining has established itself as a hotbed of innovation and invention.
Autonomous vehicles and communication
Tunnel safety optimisation, underground tracking systems and mining process simulation are potentially disruptive technologies, provided they can be effectively implemented. According to GlobalData insights, autonomous navigation, tunnel path modelling, and inertial guidance systems have become more commonplace in recent years.
Driverless heavy vehicles, also known as autonomous mining trucks (AMT), sense the surroundings and navigate the haul road surface without human interference. AMTs can work all day and require zero breaks throughout the day, reduces the potential for human errors, and increasing productivity by up to 20% with increased efficiency in operations.
Australia has historically dominated the sector’s use of autonomous vehicles. According to GlobalData figures, there were 706 autonomous vehicles in operation at Australian mines in May 2022, up from 561 the previous year, and significantly more than Canada, whose 177 AMTs ranked the country second in the world.
According to GlobalData figures, there were 706 autonomous vehicles in operation at Australian mines in May 2022, up from 561 the previous year.
However, AMT cycle times increase dust on haul roads in autonomous operating zones, posing a health risk to both local people and the environment, which will need to be considered as miners embrace automation on a larger scale.
Remote tunnel monitoring systems also provide critical information, such as the tunnel’s structural and geotechnical behaviour and underground conditions. GloabalData’s analysis shows that 20 companies, such as technology vendors, a few established mining companies, and new start-ups, have engaged in developing and applying remote tunnel monitoring systems.
Companies like Strata Worldwide assist with underground communications, tracking, monitoring and control solutions. It includes “two-way voice, text and data communications, personnel and asset tracking, atmospheric condition monitoring and gas detection, and control of fans, belt drives and pumps”.
According to McKinsey, modern drills have been equipped with advanced sensors at the bit tips of drills. This makes excavation more effective, as sensors can measure grades in real-time. Miners can understand the environment, including the terrains, through data analysis and error elimination. They can make informed decisions about the importance of discovered minerals and begin operations safely and efficiently.
Artificial intelligence and the internet of things
The internet of things (IoT) is a communication network where physical objects interconnect and communicate over the internet. It can be accessed and controlled from any position, and has obvious benefits for an industry such as mining, where the positions and loading status of vehicles and equipment can be tracked with the help of IoT in mining.
Similarly, processes such as big data enable miners to understand data in a manner beyond that of traditional human comprehension. According to research, predictive maintenance systems for belt conveyors or dump trucks depend on technologies like big data and real-time infrastructure, which forecast mechanical breakdowns, enabling miners to better plan repairs and replacements.
Other applications include the monitoring of airflow in large underground chambers and the visualisation of block-caving cavities. Atmospheric monitoring systems also detect methane, carbon monoxide, and dust exposures using “real-time data” to spot defects quickly.
One of the most dramatic examples of this approach is Anglo American’s Capcoal mine in Queensland, which received a $226m investment in 2019 to implement its ‘FutureSmart mining initiative’.
One of the most dramatic examples of this approach is Anglo American’s Capcoal mine in Queensland, which received a $226m (A$327.8m) investment in 2019 to implement its “FutureSmart mining initiative”. The project aims to improve workers’ access to and analysis of data, and could improve operational efficiency to the point where the mine’s life is extended by six years.
Elsewhere, AI technology has disrupted the mining industry by identifying potential drilling areas without human efforts. The increase in accuracy helps with cost reduction as well as time management. OffWorld, an AI-powered robotics platform maker, said in its report that the application of electric robotic mining swarms could replace explosives with precision mining. It would also leave a zero-mining carbon footprint, and people would not have to risk their lives working in dangerous conditions.
Regarding safety, AI can use sensors, real-time data and analytics to understand that temperature and vibration could lead to danger. Sensors and AI can detect anything as small as a broken tooth, which could damage the crusher during excavation. It can detect drowsy drivers, one of the biggest causes of mining accidents, using AI technology to alert drivers.
3D printing
In mining, 3D printing could pride spare parts and custom-built components, which could reduce the cost of storage, production, and delivery times. For illustrative purposes, geological data, pictures of drones or point clouds from laser scanners could also create digital items such as 3D ore deposits or open pit models. The computerised production process enhances the effectiveness of automated processes, which is why 3D printing often relates to automation and AI.
These advantages are evident in a GlobalData report on AI in mining; and while the digital transition in the industry has remained slow for many years, AI has shown the potential to “deliver tangible benefits across the mining value chain, from discovery to extraction and maintenance.” The impact of AI on the mining industry resolves challenges related to cost control, supply chain, productivity, and safety.
[AI could] deliver tangible benefits across the mining value chain, from discovery to extraction and maintenance.
According to the research, the need for more technology diffusion and the diffusion of digital technologies depends on production rates. The deficit of digital technologies among smaller operations makes it difficult for companies to keep up with the changes in the surroundings. Indeed, it is true that only some of the largest miners have invested considerably in 3D printing, such as an international project spearheaded by Sandvik.
More extensive operations have, however, sped up the application of digital technologies in the mining industry, and it is likely that the future of Australian mining will see more adoption of processes such as these.
// Main image: Mine workers. Credit: Magnifical Productions via Shutterstock