Working Safely around Conveyors
The productivity of a belt conveyor is essential for the success and profitability of an operation. However, if it is not accompanied by concern for the safety of everyone involved, the process of handling bulk material will be a failure, especially from the point of view of good ESG practices.
Martin Engineering's history begins with concern for the health and safety of employees in the workplace. The idealization of the Vibrolator® was due to a concern of Edwin F. Peterson to reduce the risk of accidents for workers in his current workplace. Since then, the issue of safety has been part of Martin's mission around the world, particularly around belt conveyors.
In addition to manufacturing products that move bulk materials and protect employees from potential hazards, Martin is an internationally recognized authority on safety. Whether by an organizational culture that has the integrity of workers as a pillar, or by publishing the book Foundations™ For Conveyor Safety, a manual with more than 500 pages that addresses the best global practices for safer handling of bulk materials.
The main hazards related to belt conveyors are mechanical, including moving components that can cause pinch damage at pinch points, grazes and burns, and pinch zones that can cause damage from cuts and crushes.
All these dangers can and should be avoided with training, preparation and safety precautions. Because of the sheer volume and size of material loads, the speed of transport, and the amount of energy they consume, conveyors have proven to be a leading cause of industrial accidents, including serious injuries and even mortality.
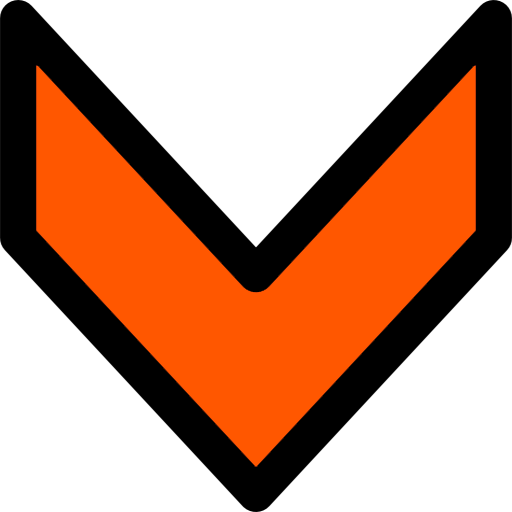
Preventable by the right choices
Quality products, properly installed and maintained, are essential for a safe work environment.
For example, realigning belts is one of the highest risk activities involving conveyors. When alignment is attempted on a moving belt, workers can get hands, tools or clothing caught in machinery, be struck by components or be pulled into pinch points where they may lose a limb or be crushed. Utilizing track-mounted impact and support cradles and troughing idlers will simplify installation and maintenance.
Most importantly, don’t take chances around conveyor belts. Don’t perform work that will expose you to pinch points, like clearing material from a roller, while the belt is moving. Only work on a conveyor that is properly locked and tagged out.
The use of skirt boards, such as Martin ApronSeal™, will limit the amount of material that falls from conveyors. The skirt boards should be placed at “high-risk” areas along the beltline, where these types of accidents are more likely to occur. Also, installing Martin Conveyor Guards to prevent inadvertent contact with pinch points and Martin Inspection Doors to inspect and access chutes and other enclosures is a valuable practice.
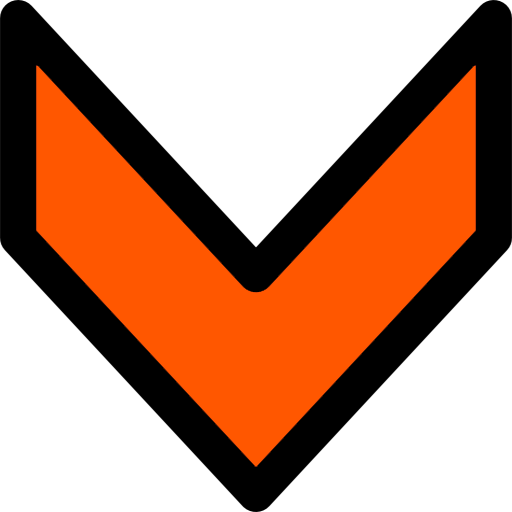
Martin Inspection Door
ApronSeal Double Skirting
Belt Alignment
For over 75 years, Martin Engineering has worked side by side with experts from all industries who are committed to the safety of their people.
Decades of experience have provided a unique perspective on the importance of safety in belt conveyor performance. You can trust us!
Martin Engineering Australia
www.martin-eng.com.au
+61 1300 627 364
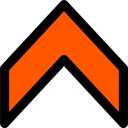