Company Insight
Sponsored by Andvare
Decarbonisation, cost savings, and social licence to operate… All from your new idler?
Justin Willis from Andvare Materials Handling talks about their quieter, lighter, more reliable and highly economical conveyor idler system.
Tackling the High Arctic's extreme operational constraints, Andvare’s upgrades at Milne Inlet turned Milne Inlet Port into a powerhouse, resulting in Canada’s fastest loading port and increasing export capacity sixfold.
Energy accounts for about 30% of total mining costs, making efficiency improvements highly valuable for all stakeholders and critical for the industry's future. With increasing pressure on mining companies to meet societal expectations in carbon emissions reduction targets, energy efficiency is paramount in securing the accepted social licence to operate. Even major fossil fuel suppliers are turning to renewables to cut costs and emissions. Reducing energy use not only boosts profitability through reduction of direct operational costs but also supports long-term sustainability of an operation through aligning with emissions reduction targets, thereby avoiding emissions related penalties.
Andvare Materials Handling Pty Ltd is focused on creating advanced solutions that promise to assist the industry's drive for efficiency and sustainability. Their flagship product, the Alfar® Idler System provides a lightweight alternative to traditional idler designs. Through primarily reducing the weight of conveyor rotational components, the Alfar® idlers help lower rolling resistance and energy consumption, directly contributing to cost savings and emissions reduction.
What is Andvare’s unique value proposition, particularly when it comes to decarbonisation?
Justin Willis: We didn’t focus heavily on decarbonisation initially, as we’ve been more involved in primarily ensuring reliability. But with the direction the industry is moving in—reducing plastics and dependence on fossil fuels—we've realised our systems are actually well-suited for that.
The industry has shifted to being more conscious of the materials used, especially the mass of components and the ease of installation. This has led to a trend of using composites and lighter materials, but these often don’t match the strength of steel. Plus, many composites are plastic-based, which introduces petroleum products into the mix. The result is more carbon being added, not less, plus, as these products wear, you’re inadvertently adding microplastics into the environment.
This is where our idler systems come into play. They’re almost entirely made of aluminium, with just a few plastic end caps made from ABS (acrylonitrile butadiene styrene), which is recyclable. Even the steel bearings can be reused as they are designed to outlive the idler shell, so the system is highly recyclable overall.
Another significant part of our decarbonisation advantage is tied to energy savings. Our idlers are lightweight, which allows the use of oversized bearings, leading to a significant reduction in rolling resistance and rolling inertia. That translates to less power needed to run conveyors. We've seen power draw reductions in two separate, measured installations of 12% and 18%.
Now, consider a basic plant with about three kilometres of conveyors. The installed power requirement could be around 1.3MW, depending on the topography and conveying rate, and running for about 5,000 hours a year. That adds up to about 6.5 GWh annually. A 10% reduction in energy usage, thanks to our idlers, means you're saving 650 MWh per year.
When you translate that into monetary value, assuming an energy cost of around 17 cents per kilowatt hour, in this scenario, that results in a 12-year direct cost payback period. Our idlers have a lifespan of 17 to 20 years, so after that initial 12-year period you’re effectively operating at a positive for the remaining 5 to 8 years.
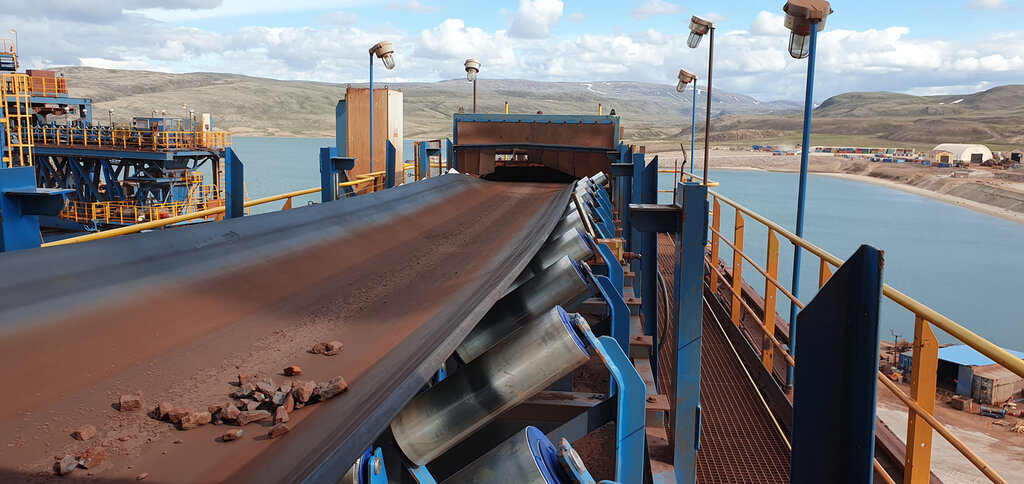
Caption. Credit:
Beyond energy efficiency, are there other benefits to using lightweight idlers?
Justin Willis: One major advantage is ergonomics. Heavy-duty composite idlers are marketed as lightweight, but they often weigh around 18 kilograms. Ours, by contrast, are about one-third the mass.
Think of this in terms of worker safety and injury reduction through ease of handling. Heavy steel idlers are a lot harder to manage on-site, especially as more women enter field engineering and maintenance roles. Lifting something that weighs 7-8kg, as opposed to 18-21kg, is a lot more manageable. In some instances, physical handing of the existing units is not an option as they weigh in at more than 100kg per unit. The Alfar equivalent idler for this example would be approximately 16kg, meaning that a single person could easily undertake a replacement task.
Can you share any specific projects where Andvare’s idlers have made a significant impact?
Justin Willis: One of our standout projects is in the high Canadian Arctic. We used our idlers to reduce the weight of a telescoping shuttle system on a dual quadrant, twin tower shiploading system significantly, which eased the load on the main slew bearings. It wasn’t just about energy savings in this instance; this was a necessary weight-saving solution that improved the balance of the machines and increasing the life of the slew bearings, as the shiploading circuit was required to service larger vessels than intended under the original design criteria.
Another project was at an iron ore mine in the Yilgarn region of Western Australia. We replaced the idlers on the stockyard reclaimer that had a serious out of balance issue (it was very boom-heavy), which is the last thing you want for a reclaimer. By swapping out the existing idlers for our Alfar units, we were able to reduce the boom weight by around five and a half tonnes. That not only put the machine back in balance without extensive and expensive reballasting as would normally be the case, but allowed it to handle an increased tonnage rate (approximately 25%); plus, it saved the slew bearing from unnecessary wear extending the projected replacement date from 2 years to 8 years.
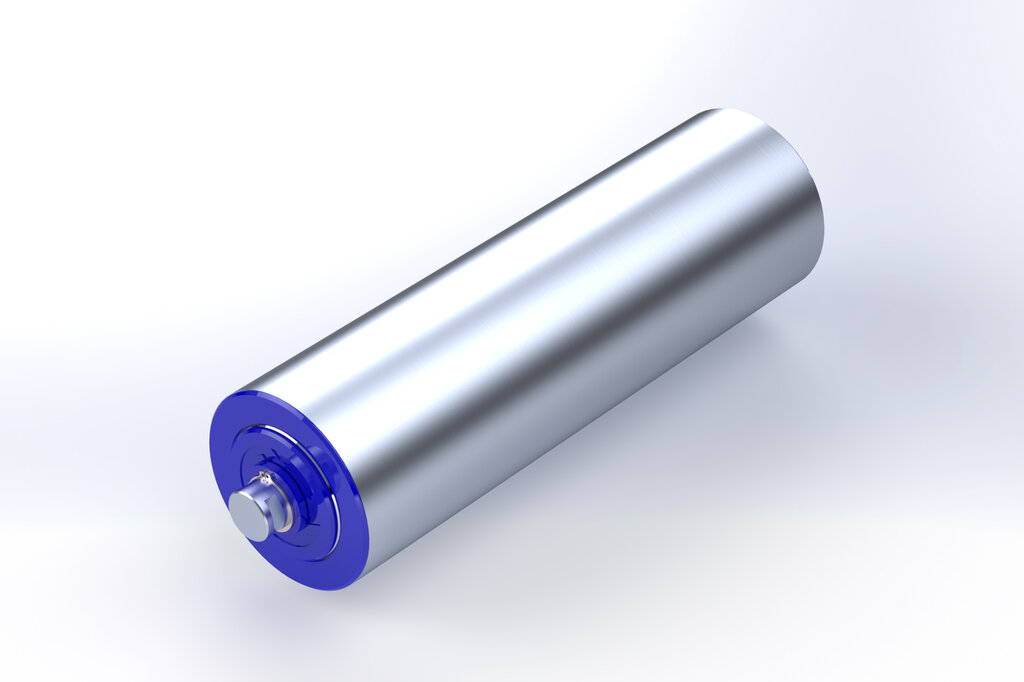
Optimised for efficiency, the Alfar® Idler features an aluminium shell and oversized bearings, reducing energy consumption across conveyor systems.
Noise reduction seems to be a feature as well. How do your idlers achieve that?
Justin Willis: Our idlers are extremely quiet. Standard low-noise idlers operate at about 72-74 decibels (dBA) at one metre. Ours are 59 dBA at source, which is quieter than normal conversation. Noise pollution is a big deal, especially in suburban operations or locations close to water, like the Port of Newcastle for example. Noise isn’t just an annoyance—it’s a sign of energy loss. A noisy idler is using energy that could otherwise be harnessed for more productive purposes, rather than excess vibration and friction.
There’s a really important focus on the “social licence to operate” for companies, especially in areas like Cape Lambert, Port Hedland, and Newcastle, where noise and pollution are closely monitored. Using systems like ours that are quieter, lighter, and more energy-efficient helps companies align with community expectations and environmental standards.
Finally, what do you see as the broader implications for mining operations adopting lighter materials and more efficient systems like yours?
Justin Willis: The future is moving towards electrification and reducing overall energy consumption. As companies strive to decarbonise, lightweight materials will play an increasingly important role, not just for power savings but also for environmental and social reasons.
We see a significant opportunity for mining companies by adopting these kinds of technologies.
Contact information
Andvare Materials Handling
U1, 28 Oxleigh Drive
Malaga 6090
Western Australia
Email: newbusiness@andvaregroup.com
Web: www.andvaregroup.com