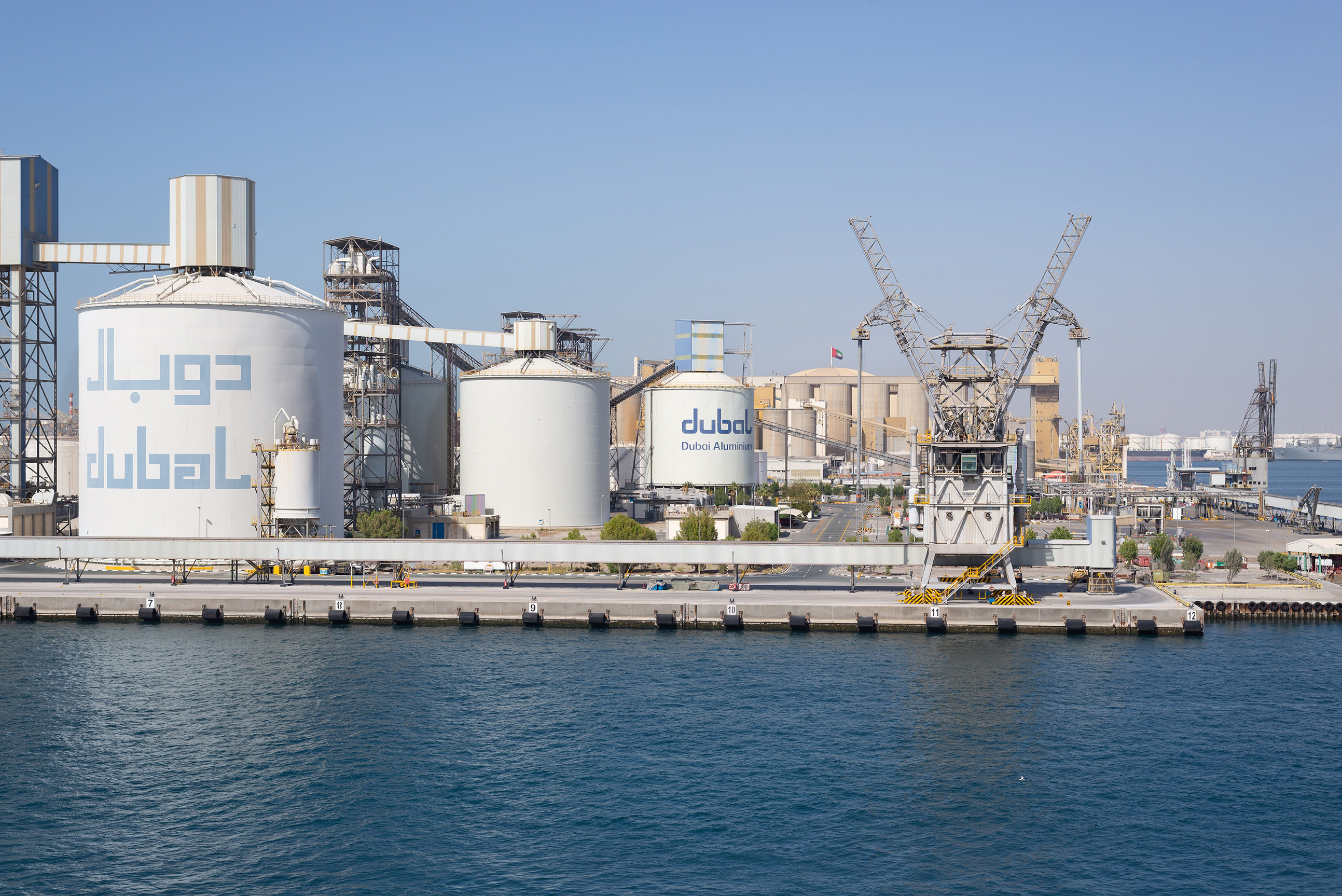
Supply chains
High costs, high priorities: inside the aluminium supply chain
Demand for aluminium is expected to double by 2050 as the world undertakes an energy transition, but, as Jason Mitchell explores, its complex value chain is beset with environmental issues.
T
he energy transition is driving a huge surge in demand for aluminium, but the industry is facing huge capacity constraints because of the big hike in energy costs in 2022.
Aluminium is both an important input to a number of technologies critical to the energy transition and a major source of carbon emissions, responsible for around 3% of the world’s direct industrial emissions in 2021, according to the International Energy Agency (IEA). Alumina refining and aluminium smelting are responsible for more than 90% of aluminium production’s direct carbon gas emissions.
The global consumption of aluminium semi-finished products is forecast to grow by 33.3 million tonnes in the following decade to 119.5 tonnes in 2030 from 86.2 tonnes in 2020, according to CRU Consulting. It is expected that global demand will increase to 179 tonnes per year by 2050. Semi-finished products are all those ‘intermediate’ goods that underwent a first industrial process but require additional processing to define their final use.
Around 37% of this growth is expected to come from China, followed by 26% from Asia (excluding China), 15% from North America and 14% from Europe. Global aluminium production saw average annual growth of 6% in the period between 2010 and 2018.
The highest growth in terms of absolute demand will come from the transportation sector, driven by decarbonisation policies and the shift from vehicles powered by traditional fossil fuels to electric vehicles (EVs), according to CRU Consulting. It will go from consuming 19.9 tonnes of aluminium in 2020 to consuming 31.7 tonnes in 2030. Around one-third of this growth will come from China, and as the metal sees increased demand from a number of sectors, it remains to be seen how the aluminium supply chains will hold up.
Demand for power
In the electrical sector, the transition towards green energy sources will strengthen demand for aluminium, which will reach 15.6 tonnes in 2030, starting from 10.4 tonnes in 2020. China is expected to account for 47% of this growth.
The electrical sector represents one of the greatest opportunities for the aluminium industry in coming years as countries transition to renewable energies – which are more intensive in their use of aluminium than traditional energy sources – and expand their power grids. Solar power requires more than four times more aluminium per installed megawatt than wind power and about 25 times more than coal.
The need for conductor cables for power distribution will also increase. Although they have been traditionally made from copper, aluminium is a cheaper alternative. It is lighter than copper but requires more material to be used to achieve the same electrical conductivity.
Furthermore, aluminium consumption from the packaging sector is expected to jump to 10.5 tonnes in 2030 from 7.2 tonnes in 2020, driven mainly by the rise in popularity of canned drinks in North America, Europe and China. This is strongly linked to the negative perception that Western consumers have of polyethylene terephthalate and other plastics that normally compete with aluminium in this space.
However, the aluminium value chain is facing myriad challenges and one of the biggest is where all the increased smelting capacity will come from. During the past two decades, China has built up a massive smelting capacity, but, in 2017, the government put in place a capacity ceiling of 45 tonnes of aluminium production a year. It has been enforcing a strict old-for-new policy in the aluminium sector – new smelters have only been permitted when matching older capacity is closed.
Electricity used during aluminium smelting accounts for more than 60% of the aluminium industry’s carbon emissions, according to Accenture. In October 2020, President Xi Jinping pledged that China would reach peak carbon emissions before 2030 and become carbon neutral by 2060. That is a big ask for the country’s aluminium sector, which, in 2018, was 90% reliant on coal power to energise its potlines.
Smelting and producing
This could create a window of opportunity for producers elsewhere in the world, but aluminium smelters are power-hungry plants and the rise in electricity prices in 2022 has hamstrung the aluminium smelting industry in the developed world. One metric tonne of aluminium takes about 14,000 kilowatt-hours to produce, enough to supply electricity to the average UK home for almost five years.
German power prices for 2023, a benchmark for Europe, soared to $553 (€543) per megawatt-hour in August 2022, 12 times higher than two years before (the price was back down at $158 (€155) on 16 October 2022 but still much higher than previously).
Energy costs account for 40% of total primary aluminium production costs normally, according to European Aluminium, an industry body. This year they would have gone up significantly. Aluminium production requires around 40% more energy than copper, for example.
Experts say it is a paradox that aluminium production is being hobbled by the very sector – electricity – which needs it most for decarbonisation – whether it be directly in the form of solar panels or indirectly in the lightweighting of EVs.
Around 1.1 tonnes – amounting to 50% of the EU's aluminium production capacity – has already been forced offline during 2022 due to the power crisis.
Around 1.1 tonnes – amounting to 50% of the EU's aluminium production capacity – has already been forced offline during 2022 due to the power crisis, according to Eurometaux, an industry body. This year, a number of European smelters have had to close and European aluminium production now sits at its lowest level since the 1970s. In October 2021, the Dutch aluminium producer Delfzijl Aluminium, popularly known as Aldel, stopped annual production capacity of 110,000 tonnes (t) due to high electricity prices.
In September 2022, Norsk Hydro shuttered a smelter in Slovakia while Aluminium Dunkerque Industries France, Europe’s largest aluminum smelter, reduced its production by 22% in October 2022. There has also been a 33% curtailment at Alcoa's Lista smelter in Norway, a 59% production cut at Speira's Rheinwerk smelter in Germany and reduced output at Alcoa's San Ciprian alumina refinery in Spain.
These closures run counter to the EU’s goal of strengthening the domestic processing of strategic minerals, with the bloc’s latest list including bauxite, the ore used to produce aluminium. Industry figures say the closures would also knock global efforts to slash carbon gas emissions because European smelters generate three times less than those in China, where coal is often used to generate electricity.
The world has enough bauxite for up to 340 years
Aluminium production starts with the raw material bauxite, a mineral found mostly in a belt around the equator. Bauxite is the only ore that is used for commercial extraction of aluminium today. Four tonnes of it are needed to make a single tonne of aluminium. Global bauxite resources are estimated to be 55–75 billion tonnes, and at the current rate of extraction, these reserves will last 250 to 340 years. The majority of the global bauxite reserves can be found in Australia and Africa.
Aluminium oxide – alumina – is extracted from bauxite in a refinery. Alumina is then used to produce primary aluminium through the smelting process. The production of primary aluminium takes place in large production lines. Primary aluminium is alloyed with other elements such as copper, manganese and silicon for additional strength, corrosion resistance and other properties. These are then cast into billets, remelt ingots, slabs and rods and other castings for further processing.
The world’s stock of aluminium in use is like a resource bank. Around 75% of the aluminium ever produced is still in use and some of it has been through countless recycle loops.
Since China announced its cap on aluminium production capacity, the Middle East has become a much bigger player in the smelting industry. The Middle Eastern countries – including the United Arab Emirates, Bahrain, Qatar, Oman and Saudi Arabia – with access to cheap gas are looking to develop their broader economies, and smelting is playing a significant role. The energy-intensive nature of producing aluminium means that parts of the world with low-cost hydroelectric power or natural gas have an advantage.
“Aluminium can be a way of converting competitive electricity into a tradeable commodity,” says Miles Prosser, secretary-general of the International Aluminium Institute, drawing attention to the flexibility of aluminium, and its unique role in the global metals exchange. Regardless of concerns as to the strength of the metal’s supply chains, this versatility could stand aluminium in good stead in the long term.
“If a country has electricity, it is difficult to sell it because it needs cables and wires to sell it elsewhere in the world,” adds Prosser. “However, with aluminium you can convert that electricity into a physical product that can be traded around the world.”
// Main image:Aluminium facilities. Credit: Druid007 via Shutterstock