Q&A with Marco Ruiz Hernandez: The Enaex Robotics capabilities defining the future of mining
wireless enabled electronic system with 2 way
communication capabilities
read interview
With unprecedented blasting capabilities and some of the most innovative robotics technology of its kind, Enaex Robotics is ushering in the future of mining.
The purpose is to humanize mining by improving peoples’ lives by eliminating exposure to hazards, maximising efficiency, and achieving the global optimum for mining operations worldwide. Director of Enaex Robotics, Marco Ruiz Hernandez, explains what it's like to break new ground.
How do remote and robotic capabilities for underground mining improve workers’ welfare and reduce risk in high-exposure operations?
At Enaex Robotics our main objective is to increase safety, reduce exposure and improve productivity.
When it comes to risk management, you use protection gear, incorporate safety procedures, and use engineering tools, but the best way is to eliminate the risk itself. Even if the blasting and loading process is relatively safe, there are challenges in the mining operation that require management of external risks and exposure to hazards. That’s what we aim to achieve with Enaex Robotics technology, by using our robotics equipment to perform all the necessary tasks without direct human intervention and operated from a control station.
Underground workers have protection gear, moisture, dust, and often high temperatures to deal with. Conditions are much better inside the control station of the mine, or even better on the surface. In the future, workers could even be operating technologies from another city, meaning they could stay near their families.
This is a clear step forward to humanising mining – by making miners’ job conditions better.
The technology will also help to speed up the development of the mine, as when you are dealing with risks, overall development is very slow. With this kind of technology, we can eliminate inefficiencies like isolation times and increase the productivity of the mine.
What has been the impact of Enaex’s technology?
We identified a very specific challenge in underground mining - rock burst - which is a spontaneous and dangerous failure of rock that can occur in high-stress mines and has the potential to kill a lot of people. Rock bursts are a serious hazard; for example, in South Africa, they kill around 20 miners each year. That is why we want to provide a unique solution, by eliminating exposure, and changing the way we do mining.
We have been developing the UG iTruck for several years now, which integrates all the main tasks that humans usually perform. In April 2022, we made the first fully remote blast without human intervention or interaction. That was a huge milestone because we know there is no precedent for this technology.
We are helping our clients overcome their challenges and progress their operations. The market is moving in this direction – and we are the first to deploy this technology and make it commercially available. We are already using this technology in a big underground mine in Chile, and we are open to receiving interest from other players in the market.
What are the challenges when it comes to developing remote capabilities for mining?
We are producing technology that is unique. Designing technology for robotic manipulation of explosives is something that is very new. The challenge is how to design a system that is safe and effective and that can also be competitive to human productivity.
You must also have explosives that are robot friendly. That is one of our strengths. Because we are in the world of explosives, we can develop and optimise our explosives, developing them ready for robotic capability to manipulate them.
Another challenge is related to authorities and regulations because you must demonstrate that the system works properly and is safe; and we´ve been very successful doing this during the last three years. Our relationship with the authorities was key to making this happen and developing innovative technology.
How did Enaex overcome these challenges?
All our decisions are driven by customer needs. We start with a pain point that exists for our clients, then we develop a specific technology to tackle it. We love taking up big challenges to do something that has never been done before.
Related to the technical challenges, the key to overcoming them was to collaborate and co-design. We have been extraordinarily successful in coordinating different key talents internally and externally at the design and development phase. Also, our agile philosophy has helped us provide value to our clients as early as possible, by refining our designs early, overcoming technical challenges to provide the best solution.
How do you envision the future of mining?
We are redesigning the way we do mining and opening a new spectrum of solutions. We´ve seen this with haulage in the past, with autonomous drilling, and now with Enaex Robotics for blasting. It’s extremely exciting to be part of this technological revolution and we are responsible for making this happen now.
In the future, mining will be driven by automation. Today, open-pit and underground mining are moving towards remote and tele-remote environments. In the long term, I think we will have digitally integrated, fully autonomous capabilities. This will enable productivity opportunities that are currently limited to human-based operations as we have today.
The vision is that mines will be fully autonomous with a fully integrated value chain. Enaex is part of this autonomous value chain, we are one of the key links that connect the entire process.
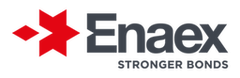
Q&A with Marco Ruiz Hernandez: The Enaex Robotics capabilities defining the future of mining
wireless enabled electronic system with 2 way communication capabilities
read interview
With unprecedented blasting capabilities and some of the first robotics technology of its kind, Enaex Robotics is ushering in the future of mining. The purpose? To humanize mining, by improving peoples’ lives, eliminating exposure to hazards, maximising efficiency and achieving the global optimum for mining operations worldwide. Director of Enaex Robotics, Marco Ruiz Hernandez, explains what its like to break brand new ground.
How do remote and robotic capabilities for underground mining improve workers’ welfare and reduce risk in high-exposure operations?
At ENAEX Robotics our main objective is to increase safety, reduce exposure and positively impact productivity.
When it comes to risk management, you can consider protection gear, incorporate procedures or engineer tools, but the best way is to eliminate the risk. Despite the blasting and loading process is pretty much safe, there are challenges in the mining operation that requires to manage external risks and exposure to hazards. That’s what we can achieve with Enaex Robotics technology.
Our robotics equipment can perform all the necessary tasks without direct human intervention, operated from a control station.
Underground, workers have protection gear, moisture, dust and in some cases high temperature to deal with. The conditions are radically better inside the control station on the mine or even bette rin surface. In the future, workers could even be operating technologies from another city, meaning they could stay near their families.
This is a clear step forward to humanise mining – by making miners’ job conditions better.
The technology also helps speed up the development of the mine. When you’re dealing with risks, overall development is very slow. With this kind of technology, we can eliminate inefficiencies like isolations times and increase the productivity of the mine.
What has been the impact of ENAEX’s technology?
We identified a very specific challenge in underground mining like ‘rock burst’ which is a spontaneous and violent failure of rock that can occur in high-stressmines, which has the potential to kill a lot of people. Rock bursts are a serious hazard; for example, in South Africa, they kill roughly 20 miners each year. That’s why we want to provide a unique solution and eliminate exposure and change the way how we do mining.
We have been developing the UG iTruck for several years now, which integrates all the main tasks that humans usually perform. In April 2022, we made the first fully remote blast without human intervention or interaction. That was a huge milestone because we know there’s no precedent for this technology.
We are helping our clients overcome their challenges and progress their operations. The market is moving in this direction – and we are the first to deploy this technology and make it commercially available. We are already deploying this technology in a big underground mine in Chile, and we are open to receiving interest from other players in the market.
What are the challenges when it comes to developing remote capabilities for mining?
We’re coming up with technology that is unique in the world. Designing technology for robotic manipulation of explosives is something that is very new. The challenge is how to design a system that is safe and effective and that can also be competitive to human productivity.
You also have to have explosives that are robot-friendly. That’s one of our strengths. Because we are in the explosives world, we can develop and optimise our explosives to be manipulated by robots, and develop the robotic capability to manipulate them.
There’s another challenge related to authorities and regulations because you must to demonstrate that the system works properly and is safe; and we´ve been very successful doing this during the last three year and our relationship with the authorities was key to make this happened (additionally to have cutting edge tech).
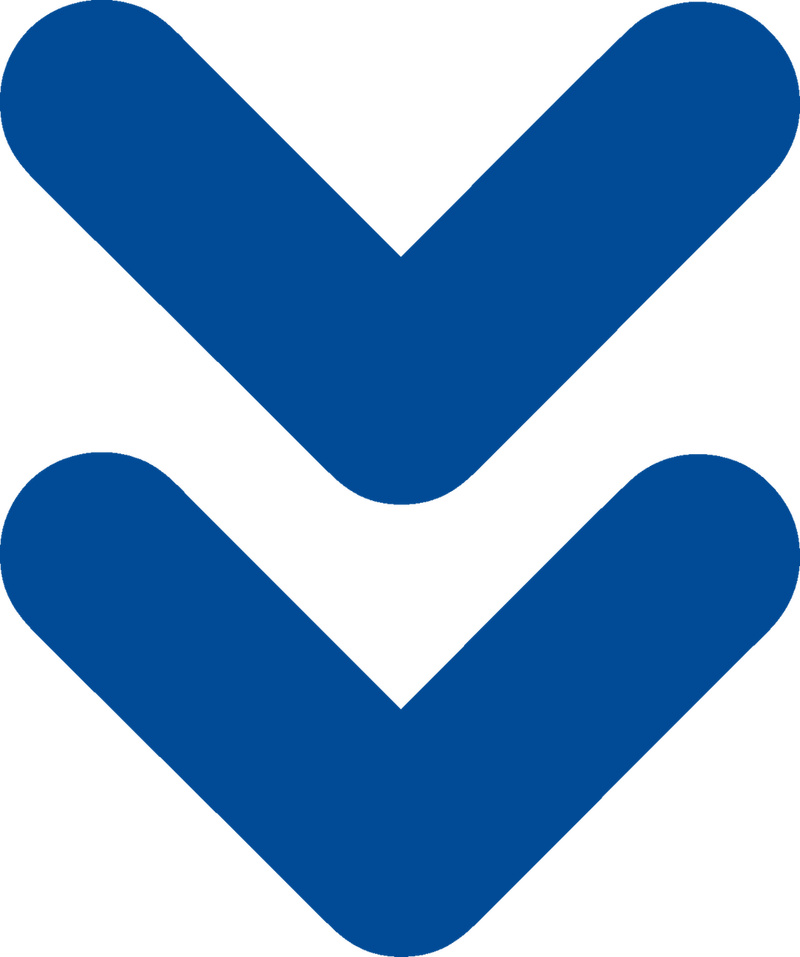
How did ENAEX overcome these challenges?
All our decisions are driven by customer needs. We start with a pain point that exists for our clients, then we develop a specific technology to tackle it. We’re not shy in taking up big challenges to do something it’s never done before.
Related to the technical challenges, the key to overcoming them was to collaborate and codesign. We have been very successful in coordinating different key talents internally and externally at the design and development phase. Also, our agile philosophy has helped us provide value to our clients as early as possible, by making the mistakes as early as possible to refine our designs, overcome technical challenges and provide the best solution.
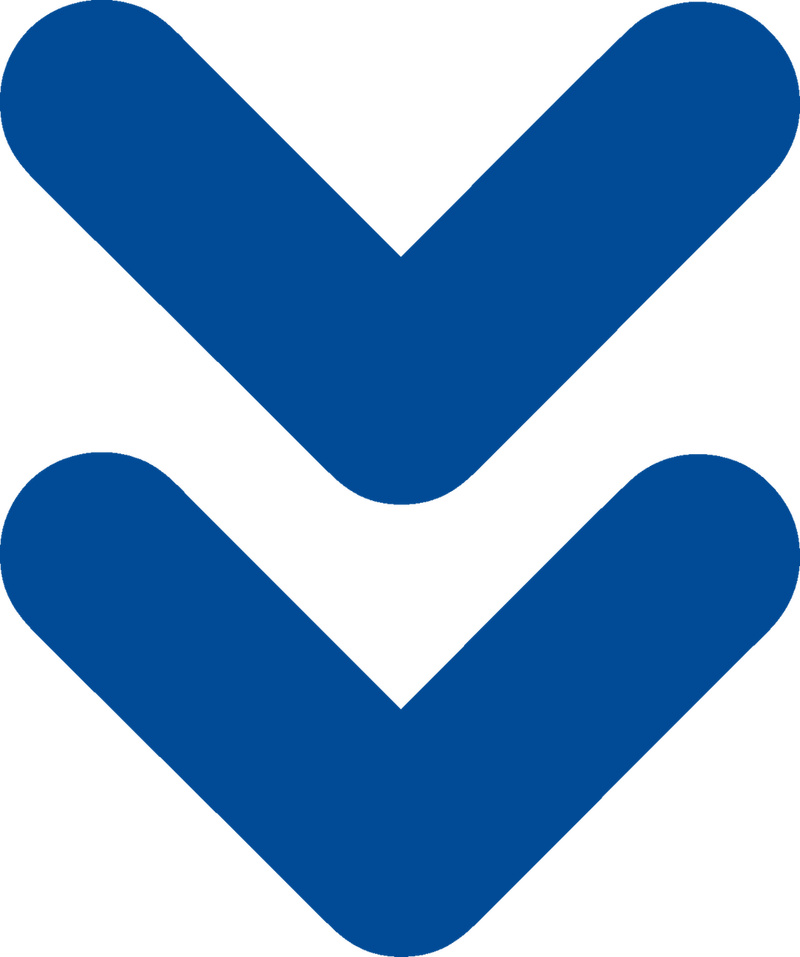
How do you envision the future of mining?
We are redesigning the way how we do mining and opening a new spectrum of solutions. We´ve seen this with haulage in the past, now are seeing this with autonomous drilling and it´s happening now with Enaex Robotics for blasting. It´s very exciting to be part of this technological revolution and we are the responsibles to make this happend now.
In the future, mining will be driven by automation. Today, open-pit and underground mining are moving towards remote and tele-remote environments. In the long term, I think we will have fully autonomous capabilities digitally integrated. This will enable to capture a lot of productivity opportunities that are limited in the human-based operations we have today.
The vision is that mines will be fully autonomous, and there will be a fully integrated value chain. Enaex is part of this autonomous value chain, as one of the key links to connect the whole process.
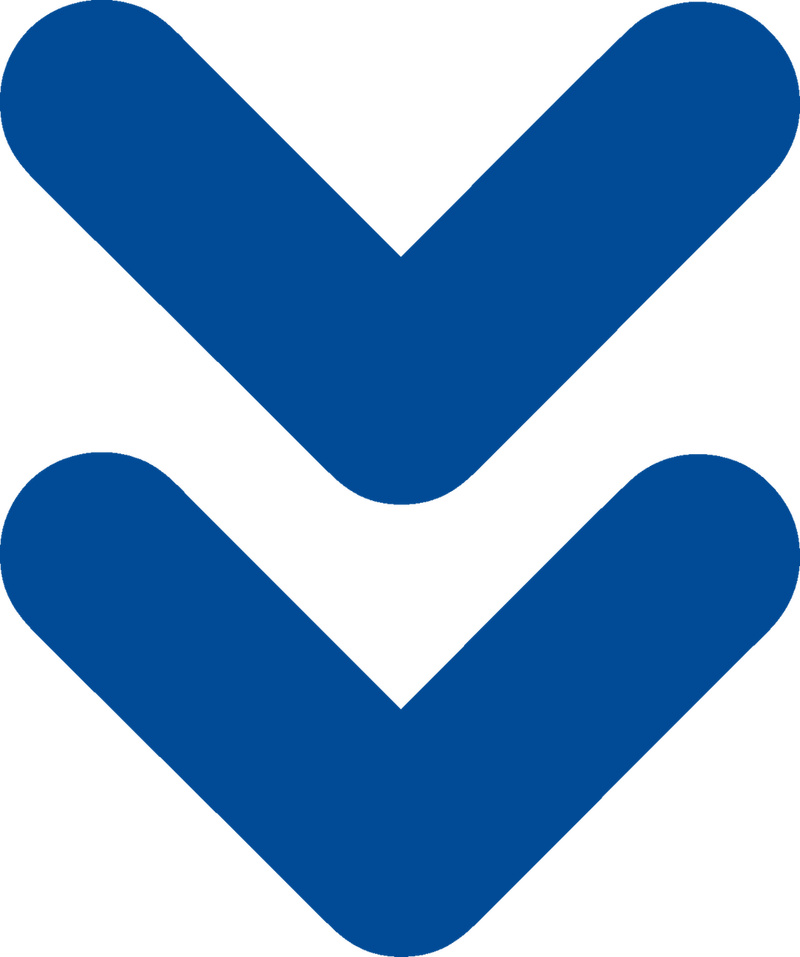