Several factors will contribute to the growth of the industrial robot market. For manufacturers, automation is still the fastest way to improve productivity. The greater cost-efficiency of robots will be another important factor. In addition, robots will become smarter but also more lightweight.
Finally, the widespread adoption of cloud computing will give industrial robots continuous access to data and improve the interaction between robots, further enhancing performance and contributing to the segment’s growth.
According to GlobalData, currently there are 12 emerging, nine accelerating and six maturing technologies in the robotics industry. The number of robotics patents increased consistently over the last decade. In 2020, four million robotics patents were granted across all geographies, which compares with 1.2 million patents granted in 2010.
Shaping the industry
Despite the general movement towards innovation, not all developments are equal and nor do they follow a constant upward trend. Instead, their evolution takes the form of an S-shaped curve that reflects their typical lifecycle from early emergence to accelerating adoption, before finally stabilising and reaching maturity.
Identifying where a particular innovation is on this journey, especially those that are in the emerging and accelerating stages, is essential for understanding their current level of adoption and the likely future trajectory and impact they will have.
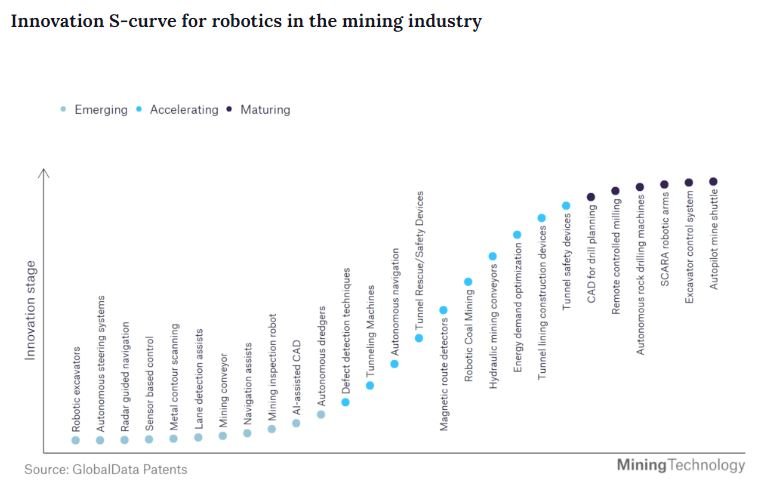
According to GlobalData’s Technology Foresights, which plots the S-curve for the mining industry using innovation intensity models built on over 350,000 patents, there are more than 150 innovation areas that will shape the future of the industry.
Within the emerging innovation stage, defect detection techniques, energy demand optimisation and magnetic route detectors are disruptive technologies that are in the early stages of application and should be tracked closely. Hydraulic mining conveyors, tunnel safety devices and tunnel lining construction devices are some of the accelerating innovation areas, where adoption has been steadily increasing. Among maturing innovation areas are CAD for drill planning and SCARA robotic arms, which are now well established in the industry.
An emerging innovation area
Regular inspections are required at operational mines to ensure the ventilation and operations are safe. Furthermore, many laws require rehabilitation after a mine’s life is over, but inspections and duties associated with rehabilitation are frequently overlooked. Personnel entering abandoned mines to conduct surveys become more dangerous as time passes.
Mining inspection robots are a far safer option, as they have advanced vision sensors, typically used for the inspection of critical and high-value infrastructure. A mining inspection robot can autonomously navigate flooded passages. It can then use cameras and other sensors to recognise different minerals.
Mining inspection robots are made up of autonomous robots and visual data management software. Fully autonomous drones or robots capture and collect visual data while automatically navigating around a facility. Autonomous robots are available 24 hours a day, can withstand extreme weather or dust, and can be controlled remotely. Data collected by autonomous robots is uploaded to the cloud, where it is organised and analysed. Users can request insights and automatically receive detailed reports when the insights are ready.
Autonomous inspections at a typical mine include stockpile measurements, tailings dam inspection, shutdowns and project management, environmental monitoring, environmental monitoring, emergency response and security, haul road inspection and pre- and post-blast analysis.
GlobalData’s analysis also uncovers the companies at the forefront of each innovation area and assesses the potential reach and impact of their patenting activity across different applications and geographies. According to GlobalData, there are more than 110 companies, spanning technology vendors, established mining companies and up-and-coming start-ups engaged in the development and application of mining inspection robots.
Leaders in ‘mining inspection robots’ include Sandvik. Sandvik has collaborated with Exyn Technologies, an autonomous aerial robot system, to integrate Exyn's data into Sandvik's OptiMine analytics and process optimisation suite. Exyn and Sandvik are assisting mining customers in transforming their underground operations to be safer, more productive, and efficient by combining critical data and capabilities.
Mining companies can harness completely pilotless flight to access impossible-to-reach data with maximum safety by using Exyn's industrial-grade autonomous drone. The collected data is processed using Exyn's onboard 3D mapping technology, which is powered by ExynAI, and then integrated with Sandvik's OptiMine Mine Visualizer solution for analysis and optimisation of underground mining production and processes.