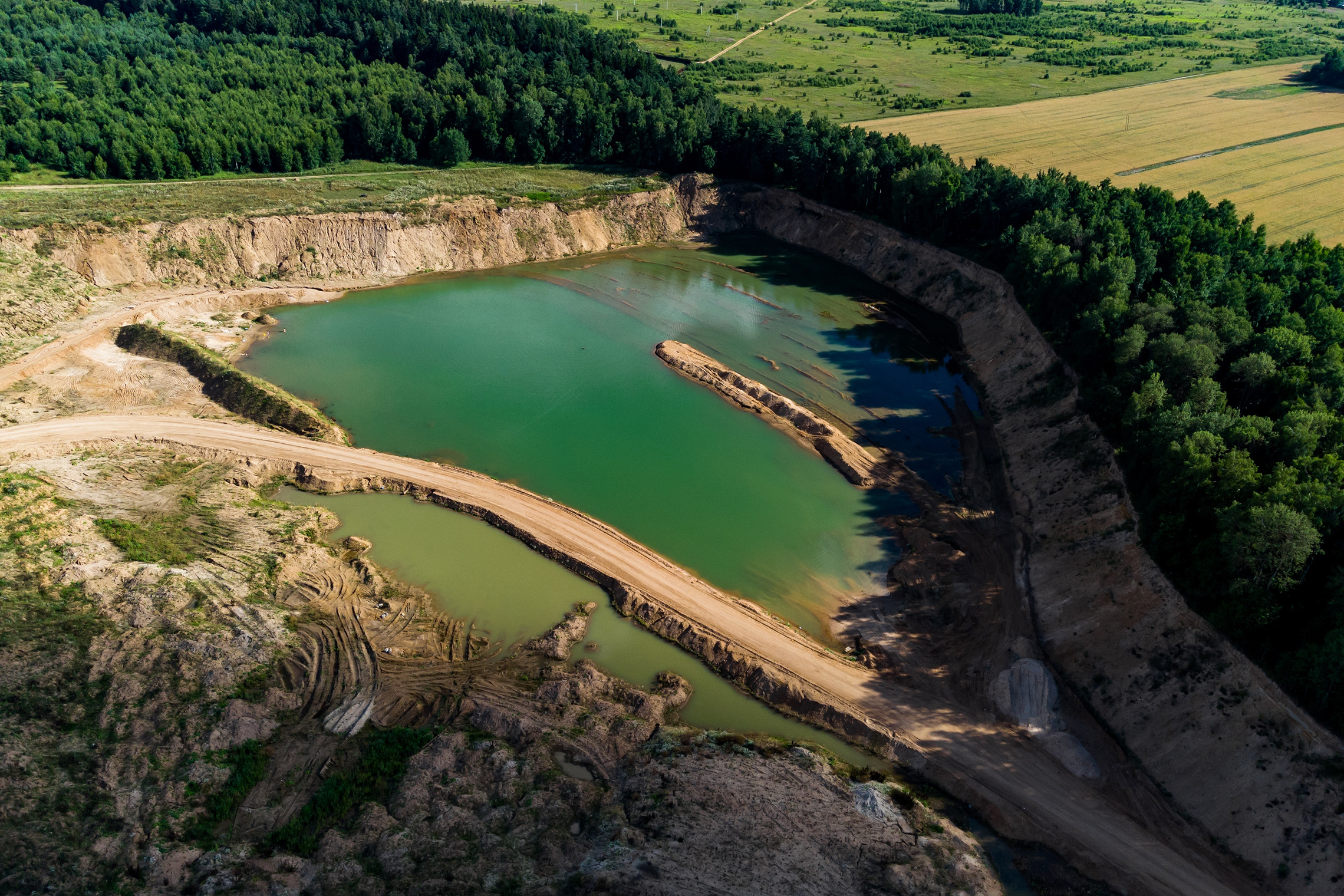
Emissions
“Important and timely”: how the mining industry collaborates to cut emissions
With emissions proving an existential threat to the mining industry, Nnamdi Anyadike considers how the sector is coming together to tackle such challenges.
T
ackling the world’s lurch towards environmental catastrophe is no easy task, and many of the world’s industrial leaders are relying on one another to spark investment and innovation in their respective sectors.
The metals and mining industries currently produce a significant portion of the global carbon dioxide emissions; according to the World Steel Association, steel sector alone produced 33.9Gt (gigatonnes) in 2020. This was around 10% of the total global energy-related emissions.
When all the other metals are taken into account, the mining industry’s global carbon dioxide footprint rises still further. The Dutch bank ING estimates that the total carbon emissions from steel, aluminium, copper, nickel and cobalt output is around 4.5Gt of carbon dioxide equivalent, or 13.5% of global carbon dioxide emissions.
In a bid to tackle mine pollution companies are increasingly joining forces and creating synergies to cover the various stages of production from ore excavation through to its transportation and refinement.
Working together
In October, two technology leaders FLSmidth and ABB Process Industries announced a collaboration to investigate how to improve environmental performance, safety and productivity. As Joachim Braun, division president at ABB Process Industries explained, “collaboration within the mining industry is increasingly important and timely if the industry is to achieve its targets as set out in agreements like the UN Paris Agreement.”
Further discussions are expected to take place over the coming months to explore the potential of using energy efficient solutions to also address power and energy management, and both companies have announced commitments to this central ambition of bringing sustainable technology to the mining market. The ABB collaboration follows the recent acquisition by FLSmidth of the mining business of ThyssenKrupp AG.
Other collaborations include the recent announcement by the US power technology company Cummins and Japan’s Komatsu of the signing of a memorandum of understanding. The accord will allow both companies to jointly develop “zero-emissions” haulage equipment, an area that is seen as ripe for innovation by the mining industry.
Analysis by McKinsey has identified haulage trucks ‘as the single biggest source of mine emissions’ with up to 25% of their emissions.
Analysis by McKinsey has identified haulage trucks “as the single biggest source of mine emissions” with up to 25% of their emissions. These are followed by: crushing equipment at approximately 20%; bulldozers at 7%; and excavators at 5% percent. Cummins and Komatsu will initially focus on zero emissions power technologies, including hydrogen fuel cell solutions for large mining haul truck applications.
The accord follows the announcement by Komatsu last year of its ‘power agnostic’ truck concept. The haulage vehicle will, “run on a variety of power sources, including diesel electric, trolley, battery power and hydrogen fuel cells,” said Amy Davis, vice president and president of new power at Cummins. Komatsu is targeting a 50% reduction in carbon dioxide emissions from use of its products and production of its equipment by 2030, compared to 2010 level. It is also aiming to achieve carbon neutrality by 2050.
An industry-wide approach
Komatsu’s carbon neutral target is in line with the International Council on Mining and Metals (ICMM’s) commitment to a goal of net zero direct and indirect carbon emissions by 2050 or sooner. This will be done by tackling scope one and two emissions, those a miner is directly responsible for, but action on scope three emissions, those produced by other companies and groups who use a miner’s products, will also be accelerated. The ICMM expects the targets to be set, “if not by the end of 2023, as soon as possible.”
James Whiteside, global head of corporate research at Wood Mackenzie, identifies three major determining factors that affect the cost of decarbonising mining operations: location, deposit type and technology. Location makes up roughly 60% of the emissions at a mine site, and both location and deposit type are aspects of a mineral reserve that mining companies, by definition, will have little influence over.
Location makes up roughly 60% of the emissions at a mine site, and both location and deposit type are aspects of a mineral reserve that mining companies, by definition, will have little influence over.
In the case of coal, it means an unavoidable spew of fugitive methane and in the case of nickel it means emissions associated with using high-pressure acid leaching. But technological development, which Wood Mackenzie has identified as the third major determining factor, is to date mainly the preserve of the larger companies.
As Whiteside explains, “if you’re Rio Tinto, you can develop your own inert anode technology. But most junior, or even mid-tier, miners simply don’t have the capital available to invest over the long term in making some of these technologies economic.” For their part, some of the bigger miners are making investments into this area; Rio Tinto recently announced a $7.5bn plan to halve its scope one and two carbon emissions by 2030, and Anglo American has also laid out a plan for achieving net-zero across all its operations by 2040.
Challenges remain
Although the mining industry is clearly making great efforts to achieve carbon neutrality the task is arduous. Dan Myerson, executive chair of Foran Mining, which is developing the world’s first carbon-neutral copper project at McIlvenna Bay in Saskatchewan, Canada explained, “the issue that we’ve got, as a society and also as a mining industry, is that to decarbonise and electrify the world you need mines. But it’s a bit of an oxymoron, in that mining actually contributes a lot of greenhouse gas emissions to the world. We’ve got to find a way to mine responsibly and innovatively.”
This paradox lies at the heart of the mining industry’s dilemma. The goal of controlling mine emissions is important if the industry is ever to rid itself of its public image as a source of pollution. However, in order for net-zero climate targets to be reached the mining of key materials such as copper will have to be increased in order to cope with the growing demand for solar panels, electric vehicles, and other renewable technologies.
Indeed, a recent report from S&P Global predicts that unless the global supply of copper is increased then efforts to reach carbon neutrality by 2050 are likely to remain out of reach. S&P Global showed that world demand for copper will reach 53 million tonnes per year by mid-century, a figure which will short of supply by 2.7 million tonnes without an increase in recycling and mining.
Crafting a series of well-laid out objectives to achieve net-zero is therefore crucial if the mining industry is to continue to play an important role in this regard. According to McKinsey, the capital markets are keeping a close eye on the sustainability of miners and access to capital is increasingly dependent on sustainability.
“The cost of capital can be 20% to 25% higher for those miners with the lowest environmental, social and governance scores,” said the consultancy. “We believe now is the right time for miners to take action and accelerate their efforts to decarbonise, using this as a differentiator toward customers.”
The cost of capital can be 20% to 25% higher for those miners with the lowest environmental, social and governance scores.
McKinsey argues for multiple efforts to address the principal sources of emissions and to decarbonise the sector including: a move toward sustainable sourcing, fuels, and drive-trains, as well as a switch to green electricity. Many of these options, McKinsey says, “are already cost-positive today [for scope one and two emissions] or will be by 2030.” For scope three emissions, however, moving entire supply chains toward greener operations remains a challenge for the industry.
Significant investments Achieving zero-carbon mines sometime between 2030 and 2040 will require significant mine-level investments, a requirement which has dissuaded significant investment in the field from some of the industry’s leaders. McKinsey estimates that the cost could reach up to $130m for a 25 million metric ton run-of-mine facility. But the task is not beyond the scope of industry, the management firm argues, provided action for decarbonisation is set out according to achievable short-, mid-, and long-term objectives.
In the short term, the focus should be on cost-positive alternatives using technology already available today. Improvements should be made to take operations to top-quartile levels. Meanwhile, a search for green energy alternatives, either through purchase or investment, should be undertaken. During this first stage, McKinsey believes, “up to 60% of emissions can be reduced over the next three to five years.”
However, in the mid- and long-term, improvements may require technological developments that are, “not yet commercially available”, McKinsey says.
The consultancy has identified three options that all offer routes to sustainable mining: a move to a fully electric mobile equipment fleet; the use of a fuel cell electric vehicles mobile fleet powered by hydrogen, combined with a build-up of green hydrogen capacity derived from wind or solar; or keeping the existing equipment, but using drop-in synthetic fuels created from green hydrogen and carbon capture, utilisation and storage.
// Main image: Sand pit at a mine site. Credit: PhotoChur via Shutterstock