
GIW Industries (A KSB Company) www.giwindustries.com
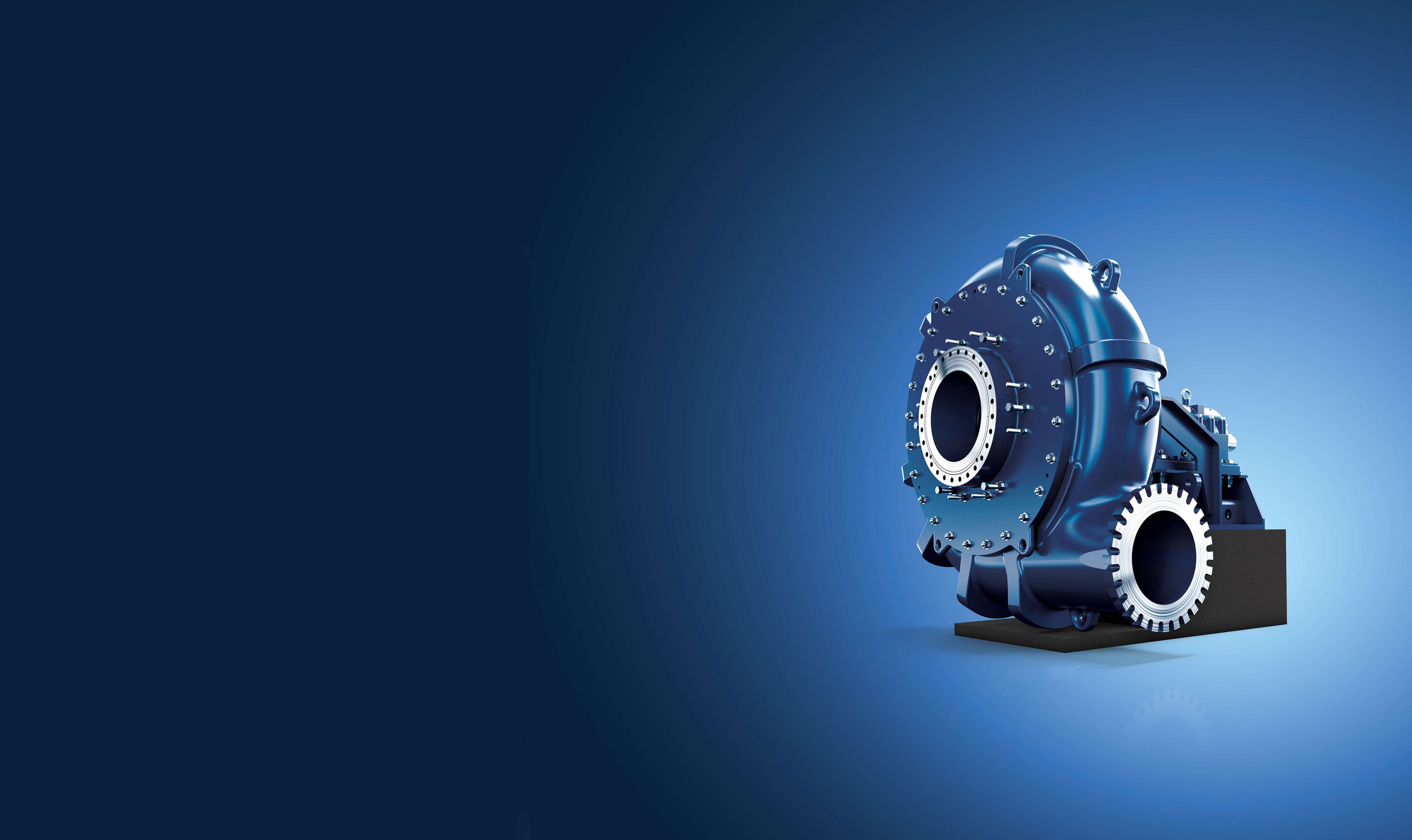
If you’ve asked yourself the question, “Why am I not getting the right performance from my cyclone feed pump”? then KSB has the answer for you.
KSB has over 150 years of experience in centrifugal pumps and continuous support. Our investment in R&D provides invaluable insights into slurry pumps and transport systems. This means our engineers are equipped with the tools needed to help you choose the right pump for your system and offer continuous improvements. Our line of GIW® slurry pumps are engineered products that include superior hydraulics, advanced material technology, coupled with technical support and service. When you select KSB you gain a partner that supports you through the entire life of the pump.
If your mill pump is underperforming consider the following:
- Do you have the right slurry pump for your process conditions?
- Are you making routine pump adjustments?
These two keys are critical in diagnosing problems in your pumps and systems. But that is just the beginning. Check out the answers to 4 common questions we hear from mine operators. They just might help you identify why you are struggling to meet production targets.
Still have questions? Each pumping system has unique operating conditions. Reach out to our Tech Service Team for a free consultation at 706-863-1011.
What’s the expected increase in the lifetime of the pump if I adjust my mill discharge pump regularly?
You will realize 20% - 50% wear life when making proper adjustments and the guaranteed minimum is 20%. Wear life is a function of how close the pump is running to the best efficiency point (BEP). The closer the pump is running to BEP, the more of an impact you will see from regular adjustments.
What are the symptoms of a worn impeller?
If you have a variable speed, you would increase the speed of the pump to keep production going. If it’s operating at peak speed you will no longer meet duty conditions of the pump and would not be able to get the pressure out of the pump, which would equal less flow. Look at the parts during planned maintenance intervals especially if there is a lot of variation and fluctuation in the slurry.
I have a highly aggressive application, how often should I adjust my pump?
You can never adjust the pump too much. If you have a highly aggressive application, you will need to adjust the pump more often. Determining when and what kind of adjustments are needed is learned over time. The average is 20 - 25 adjustments over the life of the part. For example, if the life of your part is 20 weeks, you should adjust it 20 times or once a week. Making regular adjustments to your pump will result in power savings, and longer wearing parts.
How do you analyze the cost of running a larger pump as opposed to operating pumps in parallel to meet production targets?
In certain instances, getting a motor for a large pump, along with the variable speed drive, can be expensive. On some occasions, using two smaller pumps in parallel against one large pump can be more cost efficient and effective especially when you may not have access to the needed motor or pump. motor or variable speed drive.
GIW Industries (A KSB Company) www.ksb.com/en-us
Longer Wearing Materials
KSB offers a wide range of white iron materials designed specifically to resist the abrasive nature of aggressive slurries. Combined with thicker cross sections, this translates into long and reliable pump service life.
Patented Inlet 5 Vane Impeller
Designed to efficiently transport aggressive slurries while maximizing pump performance and wear life, and minimize vibration.
Adjustable Suction Liner
Allows nose gap adjustment on the fly which in turn reduces downtime and extends the wear life.
Slurry Diverter
Our latest technology dramatically increases suction liner life by reducing particle recirculation between the impeller and liner.
You will realize 20% - 50% wear life when making proper adjustments and the guaranteed minimum is 20%. Wear life is a function of how close the pump is running to the best efficiency point (BEP). The closer the pump is running to BEP, the more of an impact you will see from regular adjustments.
In the case of a worn impeller, if you have a variable speed, you would have to increase the speed of the pump in order to keep production going. If it’s operating at peak speed you will no longer meet duty conditions of the pump and would not be able to get the pressure out of the pump, which would equal less flow. Be sure to look at the impeller during planned maintenance intervals especially if there is a lot of variation and fluctuation in the slurry.
You can never adjust the pump too much. If you have a highly aggressive application, you will need to adjust the pump more often. Determining when and what kind of adjustments are needed is learned over time. The average is 20 - 25 adjustments over the life of the part. For example, if the life of your part is 20 weeks, you should adjust it 20 times or once a week. Making regular adjustments to your pump will result in power savings, and longer wearing parts.
In certain instances, getting a motor for a large pump, along with the variable speed drive, can be expensive. On some occasions, using two smaller pumps in parallel against one large pump can be more cost efficient and effective especially when you may not have access to the needed motor or pump. motor or variable speed drive.