Feature
Building a fast future for battery mining vehicles, and what comes next
Battery-powered electric vehicles could help decarbonise mines and improve safety, but the sector must invest heavily if it wants to get the mix right. Andrew Tunnicliffe talks with Heather Ednie, CEO of the Global Mining Guidelines Group, to find out more.

Using electric vehicles underground means easier ventilation. Caption: Mark Agnor via Shutterstock.
Significant capital expenditures and infrastructure improvements are necessary if mines are to play their role in meeting 2050 net zero emissions targets, a commentary co-authored by stakeholders across consultancy McKinsey & Company’s global network warned. Writing in April this year, they said the industry would likely need to cut its emissions by as much as 85% by the middle of the century, arguing such a transition could “help power electrified mobile mining equipment and displace diesel”.
As MINE reported last year, mine owner/operators are increasingly investing in battery- and electric-powered fleets. The perceived wisdom is that if companies are to cut fleet emissions – often from huge machinery, such as 350kW giant haul trucks, which require colossal amounts of power – they need to consider two possibilities: battery-powered electric vehicles (BEVs) or hydrogen. The suitability debate has raged for some time, but if you base your methodology on opinion and spend the answer is now becoming clear.
Mining giants BHP, Fortescue and Rio Tinto have all indicated – in a big way – they are firmly in the BEV camp. They believe the efficiencies BEVs offer over both hydrogen and the likely-soon-defunct diesel alternatives are too appealing to ignore. Add to those efficiencies the almost total removal of operating emissions and the positive impact that has for health and safety, a revolution is surely upon us. By 2028 it’s estimated the electric vehicle industry will be worth a staggering $28bn when mining is combined with construction and agriculture, according to IDTechEx.
Two sides of electrification, and billions of dollars
For Heather Ednie, CEO of the Global Mining Guidelines (GMG) Group, this shift has been an evolution over years. “Electric equipment has been in operation for decades in mining. However, the current focus on electrification, and BEVs in underground mining, was really driven by mines in Canada,” she says, “which over the past decade have expanded to depths that made current ventilation and cooling technologies for diesel equipment prohibitive.”
Her not-for-profit was founded in 2012 with the aim of bringing miners together to share knowledge, expertise and experiences in the pursuit of developing guidance, resources and common practices to help address some of the biggest issues faced. She says in recent years, though, the global focus on electrification has gathered pace, in part to reduce diesel particulate matter (DPMs) underground and reduce greenhouse gas emissions. “Today, virtually every mining company has some level of focus on electrification towards meeting decarbonisation targets,” she adds.
Virtually every mining company has some level of focus on electrification.
In 2017, GMG published its first version of the Recommended Practices for Battery Electric Vehicles in Underground Mining guidance. Since then, the guidance has undergone several revisions and is now in its third iteration. “This guideline has truly left a mark on the industry. We have heard from users and participants that they feel it has been instrumental in pushing the development of underground BEVs forward,” Ednie continues.
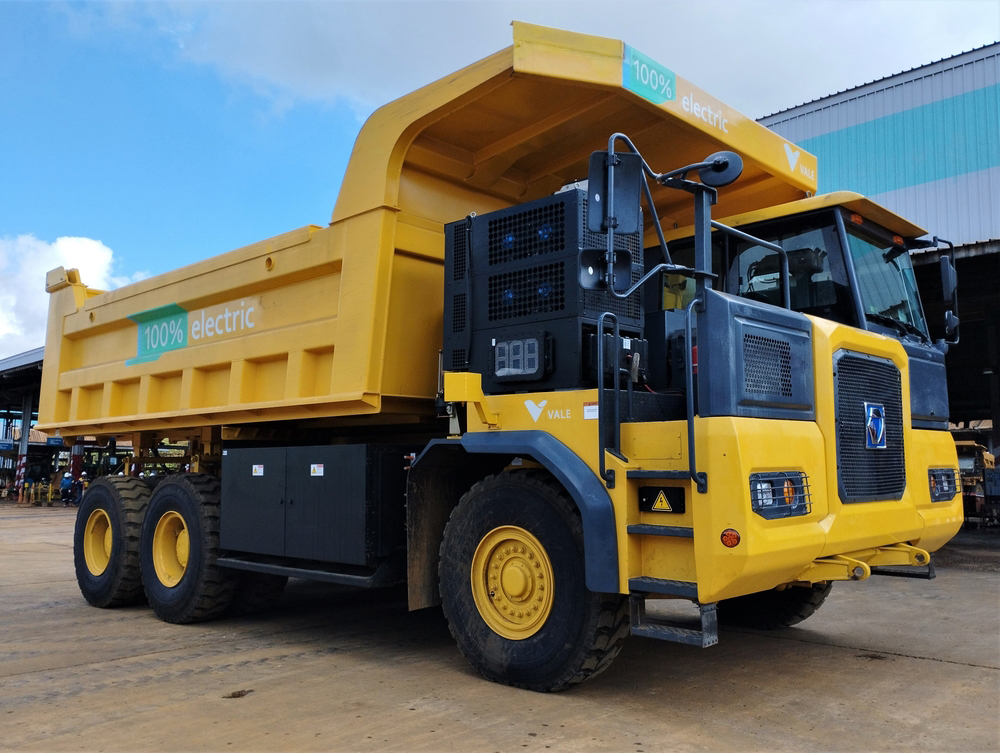
Alongside vehicles, electric infrastructure will need to evolve. Credit: Kaisarmuda via Shutterstock.
Whilst she’s largely positive about the sector’s use of BEVs, she acknowledges the challenges ahead if the transition is to be a success. One such, multifaceted, challenge is the available BEV infrastructure, as the McKinsey commentary suggested. It said that if mines are to be electrified, they would have to upgrade electric-grid connections, build additional on-site substations and networks, and install or contract renewable-power capacity, while the technology used in the batteries themselves would be required to achieve higher density, lower costs, faster charging rates, and larger scale to make electric equipment competitive. All this would come at a cost of tens of billions of dollars.
The evolving puzzle of powering battery-powered mining vehicles
Ednie seems to concur with that assessment: “Batteries are a constant challenge with the evolution of BEVs because of the different battery chemistries.” She adds there are connectivity and infrastructure challenges too, coupled with a need for interoperability between various equipment, charging infrastructures and other mine systems and equipment. “In particular, there is a major focus on developing a universal charger to standardise charging infrastructure requirements across equipment, regardless of the OEM [original equipment manufacturer]; however, it isn’t that simple,” she says.
She cautioned energy management was a real concern for the industry, requiring greater collaboration. Other obstacles include details on the charger and protection level available with lithium batteries; developing a common language around BEV terminology; the need for a better understanding of performance, good practice, battery life cycle, and further standardisation; the integration of charging infrastructure, batteries or trolley, into mine design and mine planning; and implementing low carbon energy sources. “For brownfield operations disconnected from the grid, the implementation of BEVs will change the power model. With grid connection, capacity challenges could arise,” she continued.
Maintenance teams will require new skill sets, creating the need for multi-skilled technicians.
There will also be the need for reskilling, ensuring the workforce of tomorrow has the expertise needed to operate new fleets safely and efficiently. “With the electrification of the equipment,” Ednie continues, “maintenance teams will require new skill sets, creating the need for multi-skilled technicians.” GMG has identified battery handling and safety, and BEV maintenance and support as key areas for development.
Seeming to share those views, in February Brandon Vance told delegates at a Workplace Safety North event in Canada that the introduction of BEVs should not be rushed. The mining advisory specialist, working for training company NORCAT, added that there has to be a plan to transition to electric. “I think a BEV awareness course is going to be critical to anybody that’s going to be working underground as you shift towards this being more prevalent in modern times,” he said.
“Not a ‘one size fits all’ solution”
However, done correctly, the wide scale introduction of BEVs will offer huge benefits beyond the mines themselves. On the ground, says Ednie, their use can enable a safer, cleaner and healthier environment by reducing DPM and equipment-generated heat and noise level exposure. They also offer a potential alternative to prohibitive ventilation costs required for diesel equipment operation underground, and a solution to what she calls the “ineffectiveness of ventilation and cooling systems” as mines go ultra-deep.
“An additional benefit is that the drive to meet industry targets, including the focus on mine electrification and BEVs, is helping to shift mindsets,” she adds. “Across our industry, miners and METs [mining equipment, technologies and services] are seeking innovative solutions and opening up to new ideas and approaches. We’re seeing many new vendors entering mining, bringing innovative solutions from other industries; and we’re seeing a rapid focus on technology innovation – from new equipment to new platforms and systems – that could result in great improvements.”
She did, though, warn against becoming too fixated on the social benefits such as fewer emissions - which would likely tie into miners’ environmental goals – saying: “There is a concern that as an industry, we need to ensure efforts to reduce carbon emissions don’t result in negative impacts in other areas.” She adds that for surface mines, the push to electrify and reduce emissions is not so simple. “BEVs might not be the answer, at least not for ultra-class equipment,” she says; although multiple potential solutions are under development.
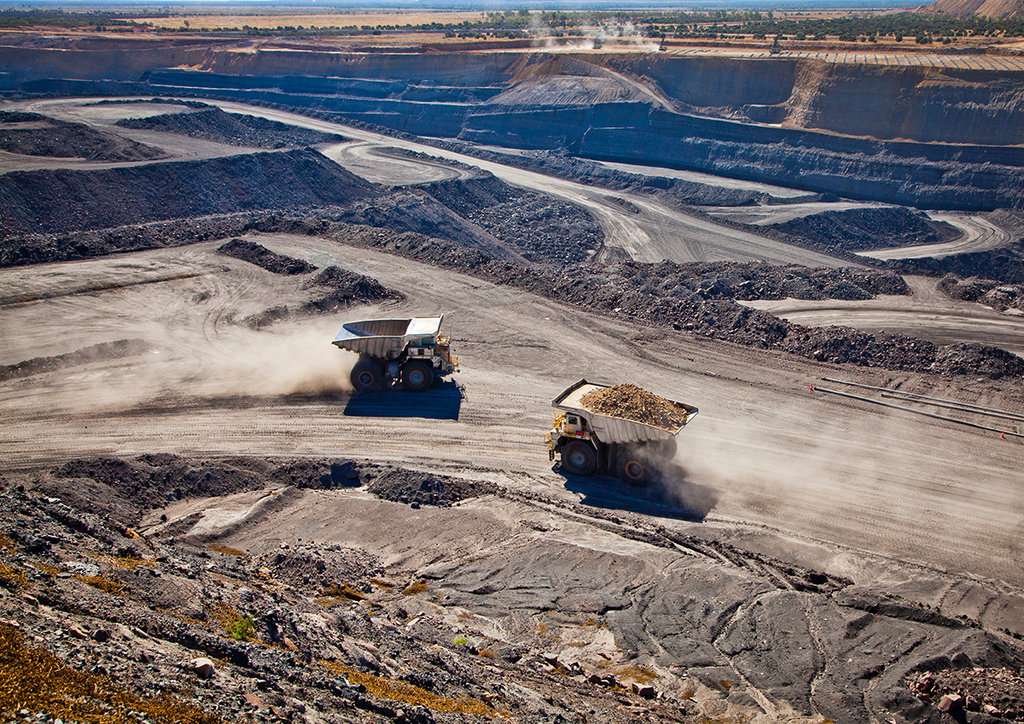
Traditional trucks operation at Blackwater, Australia. Credit: Jason Benz Benee via Shutterstock.
Although BEVs offer huge advantages, especially underground, Ednie believes they are dependent on the mine itself. “It’s not simply a ‘one size fits all’ solution… BEVs are a constantly developing and expanding technology, so there will always be new pieces to learn and explore to improve efficiency, safety and productivity. This requires constant, heightened collaboration and sharing of information across industry.”
As the march towards a cleaner and quieter mining future gathers pace, it seems clear BEVs have a huge role to play. For now, though, that role is just beginning to be shaped. For Ednie, it needs to be a jigsaw piece to the bigger picture. “I think it’s important that the electrification of mobile equipment is considered as part of a greater strategy. Climate risks and actions are on top of the corporate agenda and an energy intensive industry like mining is heavily impacted,” she concludes.