Event Report
Resourcing Tomorrow: Looming copper deficit a focus of discussion
New strategies are needed to address the growing copper supply deficit, including greater focus on exploration and recycling, mining leaders say. Caroline Peachey reports.

Mark Bristow, CEO and president of Barrick speaking at Resourcing Tomorrow. Credit: Caroline Peachey
The transition to clean energy is driving demand for copper to levels which will soon no longer be satisfied from existing and planned production, Mark Bristow, CEO and president of Barrick stated in his keynote address at Resourcing Tomorrow in London on 3 December.
“Discovery and development through either brownfields or greenfields exploration is the only way for the industry to create real value and remain sustainably profitable,” Bristow said.
According to the Barrick chief, global copper production and primary demand are due to part ways around 2026 with the gap growing rapidly soon after. Yet, while production is being squeezed, Bristow says “there’s no shortage of metals and minerals in the ground”.
The issue, he says, is that much of the metals and minerals endowment is concentrated in what are classified as low-GDP regions. In other words, the countries global mining companies have – and largely continue to – avoid because they are considered high-risk investment destinations.
Where will future copper supply come from?
Asked where the future supply of copper may come from, Bristow pointed out that most promising deposits are in so-called “challenging jurisdictions”.
“One place is, of course, the Central African Copperbelt. The Tethyan Metallogenic Belt, [which stretches] from Eastern Europe, all the way down through Asia, is another completely unexploited resource base,” Bristow said.
Barrick’s Reko Diq copper project in Pakistan, located near the Afghanistan and Iran borders, and its Lumwana project in Zambia are both set to come online in 2028. The projects have had a “significant head start” against others still dealing with costs, geometallurgical challenges, permitting and infrastructural issues, according to Bristow.
However, it is not just Africa and Asia that have untapped copper resources.
“There are still many copper deposits to be discovered in South America, and particularly if you move up the western seaboard, through into Ecuador and Colombia,” Bristow said.
“My point is that every one of those destinations I've just described are challenging jurisdictions.”
Government support is key to addressing copper deficit
Another promising copper project in South America is McEwen’s Los Azules in Argentina’s San Juan province, which is being developed in partnership with vehicle manufacturer Stellantis (18%) and mining major Rio Tinto (17%). Recent government initiatives have made the environment more favourable for its development.
“Argentina has been effectively closed for quite a while for large-scale mining development, and it has been a bit of a pariah in the investment community,” Robert McEwen, chairman and chief owner of McEwen Mining told Resourcing Tomorrow in a separate address.
That he says, changed with the election of President Javier Milei, who was sworn into office in late 2023, and subsequently implemented a range of measure that support the mining sector. These included “reducing the corporate tax rates, dividend rates, export taxes, and cleaned out a lot of the impediments to foreign investment.”
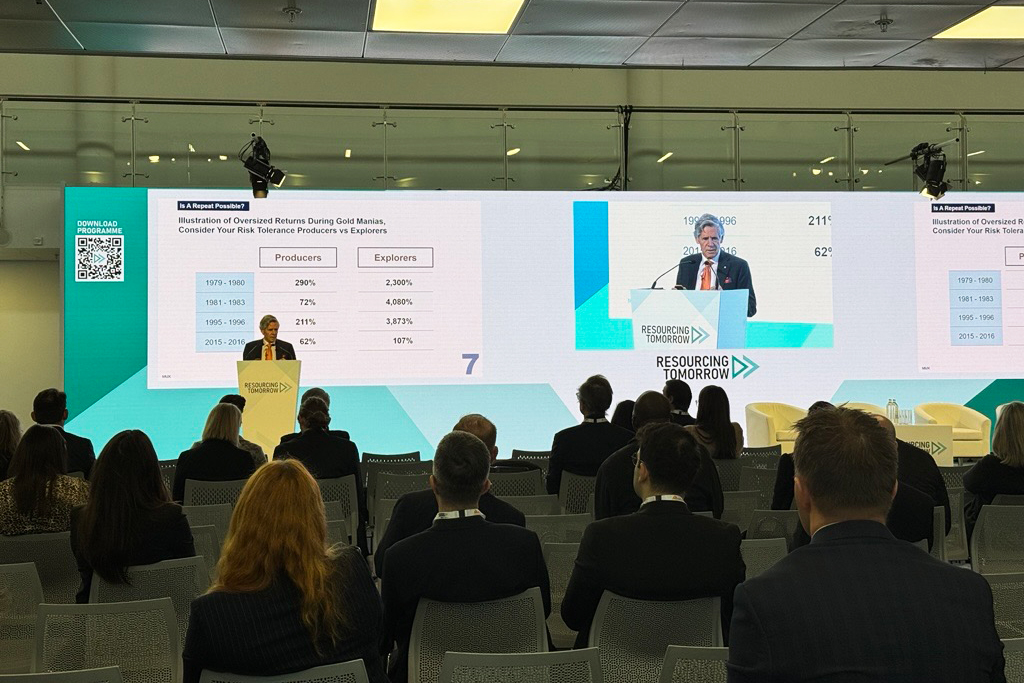
Robert McEwen, chairman and chief owner of McEwen Mining speaking at Resourcing Tomorrow. Credit: Caroline Peachey
McEwen Copper announced it has secured an environmental permit for construction and operation of Los Azules on 3 December. The company says the mine is designed to be “distinctly different” from a conventional copper mine by consuming less water, emitting less carbon and running off 100% renewable electricity once in operation.
Saudi Arabia is also looking to exploit its mineral resources, including copper.
"We are delivering $100bn investment opportunities by 2035, of which $32bn is under development across multiple value chains such as steel, battery materials, copper, aluminium, and others,” said H.E. Khalid Saleh Al-Mudaifer, vice-minister for mining affairs from the Ministry of Industry and Mineral Resources, Kingdom of Saudi Arabia.
The role of copper recycling
Copper recycling will have a role in helping to address the copper deficit, according to Mark Kristoff, CEO of Traxys, a company that provides sourcing, logistics, financing, and marketing services to the mining and minerals sector.
“Copper recycling is a big part of the story of how we deal with the [looming copper supply] deficits,” Kristoff said.
“As price appreciates, it incentivises more efficient recycling activities. So, I think that as the energy transition and raw materials markets mature, as you see obsolescence come into the equation, you will see significant recycling of products,” he added.
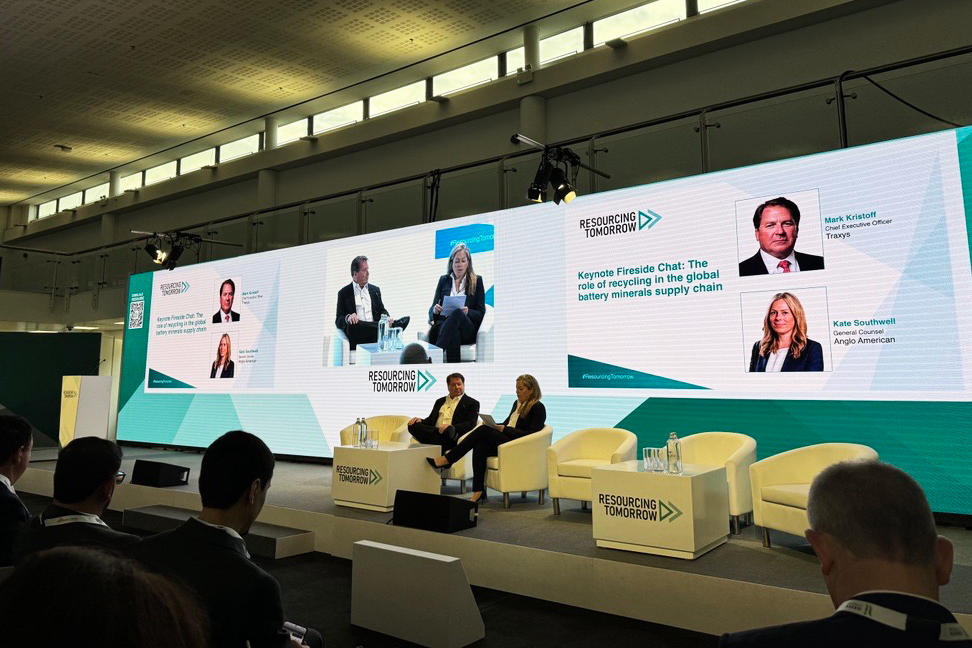
Mark Kristoff, CEO of Traxys has a fireside chat with Kate Southwell, general counsel at Anglo American. Credit: Caroline Peachey
However, Kate Southwell, general counsel at Anglo American pointed out that in the last 100 years, two-thirds of the 690 million tonnes of copper that have ever been produced are still in use.
“Even under the most optimistic circumstances, with lower-than-expected copper demand and very high recycling rates, it is estimated that the end of life, secondary copper demand would only reach around 49% in 2050,” Southwell said.
“So, to your point, primary copper extraction will need to rise significantly. But equally, we can address some of these supply deficits that we are facing by recycling more copper.”
Kristoff agreed, echoing previous comments on the importance of partnerships with local governments and communities.
“We need junior mining companies that are out exploring, finding new resources [and that] has been constrained because of financing limitations [so] the idea of joining forces with governments that are going to support project development in a sustainable way is a big thematic.”