IoT technology is deployed across the whole mining value chain, from prospecting to reclamation. Its spread has been encouraged by reduced latency, increased computing power, and the falling price of sensors, which have led to a faster ROI.
IoT solutions enable mining companies to automate workflows, improve efficiency while reducing costs, and improve safety and ESG credentials. IoT technologies enabling mining operations include drones, wearable tech, proximity detection sensors, and autonomous trucks. Also, AI has increased relevance across all IoT layers, and a growing number of products and services incorporate this disruptive technology into their capabilities, especially for predictive maintenance and digital twin modelling.
The matrix below details the areas in IoT where mining companies should focus their time and resources. We suggest that mining companies invest in technologies shaded in green, explore the prospect of investing in technologies shaded in yellow, and ignore areas shaded in red. Below, we outline how IoT can address challenges throughout the mining value chain.
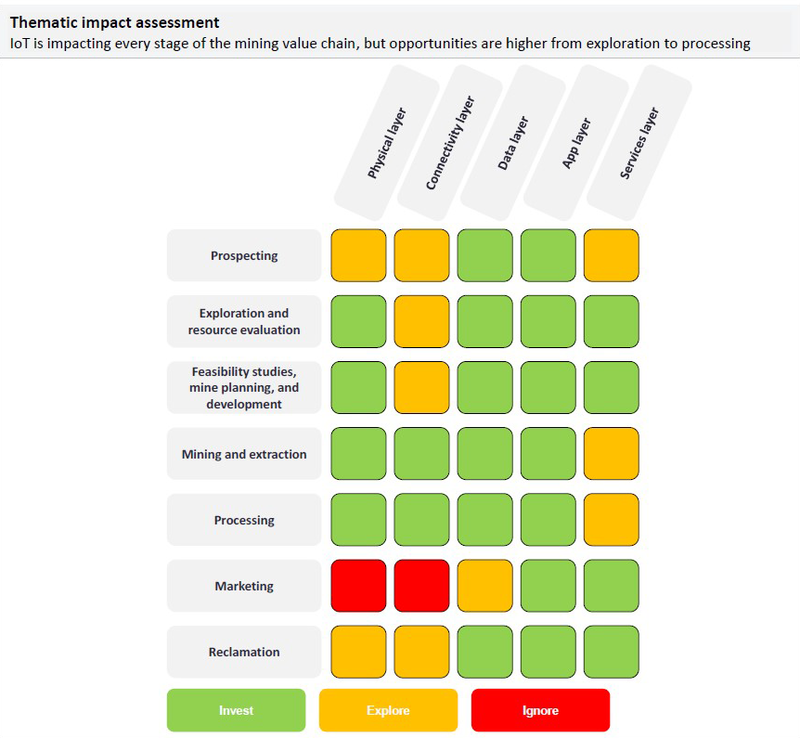
Caption. Credit:
Overall, most mining segments will benefit from investing, or continuing to invest, in all layers of the IoT value chain.
For example, sensors to monitor geological parameters or weather and environmental monitoring stations are necessary during the exploration, development, and reclamation phases, while drones for aerial surveys or radar and seismic sensors to understand geological formations are used primarily during the exploration and resource evaluation phase.
Feasibility studies and mine planning and development require IoT technology for digital twin modelling and further geological data collection for feasibility assessments. In terms of mining and extraction, mining companies use IoT-controlled drilling and blasting equipment and autonomous trucks, alongside automated sorting technology and IoT-optimised energy management solutions for processing.
The marketing and reclamation segments should focus particularly on the app and services layers. This is because, in these cases, the link with customers is closer, and it is more about presenting data already collected for quality assurance purposes, for example. Also, the reclamation segment relies on the services layer, as system integration and consulting services play a key role during mining abandonment and subsequent reclamation projects.
How IoT can help address the challenge of ESG
With a poor environmental and ethical track record, the mining industry is integrating ESG strategies into its operation. IoT technology can help with this transition, playing a central role in establishing responsible mining practices.
Satellite IoT, IoT services provided by networks of satellites, streamlines the collection of ESG-related data, offering real-time and detailed information. It monitors the consumption of resources such as water and electricity, air and water pollution levels, and waste generation, even in remote locations. An example is Orbio Earth's methane intelligence, a software platform that uses satellite data from the European Space Agency (ESA) to monitor global methane emissions. The company then links emissions information to companies' asset ownership data and ultimately benchmarks those data and classifies oil and gas and mining companies according to their methane emissions performance.
Orbio Earth’s co-founder, Jack Angela told GlobalData: “Our top focus is oil and gas companies, but we've spoken to mining companies too. There is a lot of pressure to monitor methane emissions coming from regulators, investors, and the public.” He added: “We sell our data both to financial companies who want to understand the good and bad performers in the industry and to the oil and gas and mining companies themselves, who want to understand how they are rated by financial companies”.
IoT technology can improve governance and transparency in the mining sector, for example, by monitoring compliance with regulations and transparency around data disclosure with stakeholders. For example, in March 2023, Rio Tinto started publishing site-by-site water usage data across its global mining network. Data collected included water volume, annual usage, and catchment runoff that can be compared with historical data. Similarly, in February 2023, Cognizant supplied Orica, an explosives and blasting systems provider, with an ESG reporting digital platform to help the company monitor, report, and forecast its greenhouse gas (GHG) emissions reductions.
IoT technology can also help mining companies in their journey towards electrification. A good example of a connected device that supports environmental initiatives is the 3MW fast-charger rolled out by Fortescue Metals in July 2023 to recharge the electric and hydrogen haul trucks the company is trialling.
IoT sensors and cameras in the device can monitor and gather data about the movement of materials and water in tailings, the material left over after separating the valuable fraction from the uneconomic part of the rock. In July 2023, the industrial IoT solutions providers Davra and IoTDC paired to launch an advanced software suite focused on real-time monitoring and management of tailings storage facilities. The software features advanced sensors, predictive analytics, machine learning algorithms, and Earth observation data.
How IoT can help address the challenge of safety
As stakeholders are increasingly concerned about worker safety, IoT can help the industry tackle this challenge. IoT-enabled mine-site technology is broadly adopted, and investment levels have increased in recent years, particularly for drones and fatigue detection, as revealed by GlobalData’s Global Mine-Site Technology Adoption Survey (2023). Over the last five years, the share of respondents (mine managers, general managers, and mine-site IT managers) that had invested in drones has risen from 44% to 74%, with the greatest penetration in Australasia.
Safety is enhanced by using drones for regular inspection of deep shafts, for blasting and ensuring all staff are clear before blasting activities begin, and for surveillance and security. Accidents can also be avoided using fatigue detection technology to track the operator’s eye and head movement and warn whenever signs of fatigue or distraction are identified. In 2022, Gold Fields equipped 35 mine vehicles with Hexagon’s Operator Alertness System Heavy Vehicle (OAS-HV) at the Damang Mine in Ghana.
According to GlobalData’s Safety Trends in Mining (2022), 32% of mines having either fully implemented or made a considerable investment in collision avoidance. Wearables, proximity detection systems (PDS), and vehicle control systems (VCS) can monitor the positions of workers and hazardous equipment, and employees can be warned about dangerous areas. For example, in 2021, Caterpillar launched the Connected Worker system, combining wearable tech with a platform that receives reports from the field and communicates potential safety risks to workers.
Remote control vehicles in underground sites tend to be implemented to keep the workforce far from dangerous environments. It is essential to provide employees with clean air and sufficient oxygen in underground mines. IoT sensors can monitor potential dangers in real-time with ventilation-on-demand (VOD) systems like the ABB’s Ability Ventilation Optimizer, which uses real-time data transmitted from sensors around the mine about the use of trucks, the location of staff, gas flow, and temperature. Similarly, in May 2023 GeoMoby and Digital Terrain partnered to provide real-time environmental monitoring in underground mines. Gas sensors can detect lethal gasses, and recording devices can trigger alarms if necessary, thus keeping miners safe.
How IoT can help address the challenge of productivity
IoT supports automation and remotisation of processes and activities, supporting operational efficiency. IoT solutions can help monitor mining activities like ore processing or quality control, thus reducing downtime. IoT technology allows predictive maintenance, with remote sensors collecting data on equipment health to identify potential issues. Compared to reactive maintenance, this practice saves time and money and increases machinery longevity.
In May 2023, GlobalData’s Global Mine-Site Technology Adoption Survey (2023) revealed that 19% of respondents had fully implemented predictive maintenance for mobile equipment, while 23% had fully implemented predictive maintenance for plants. Furthermore, over half of the mines surveyed had made considerable investments into or fully implemented mine planning and management software and mine communication systems.
In addition, autonomous vehicles boost productivity because they only need to stop for fuelling or maintenance. This means the machinery can work for 24 hours a day at peak performance. For example, BHP currently has 470 trucks operating autonomously or autonomous-ready. IoT-enabled vehicles provide real-time data on location, fuel consumption, and working status. Analysing this information helps optimise routes and fuel efficiency.
Drone usage continues to expand rapidly in the mining sector, bringing productivity improvements, especially in surveying and 3D mapping, as a drone and drone pilot replace a pilot and plane at one-tenth of the cost per hour. Indeed, drone technology can collect unlimited aerial data, enabling quicker decision-making, and engineers can now focus their efforts on analysis and interpretation.
How IoT can help address the challenge of resource development
Traditional prospecting and exploration methods are not feasible anymore to meet the current mineral demand, as they consume time, money, and workforce.
IoT technology helps as its increased accuracy reduces the time and money spent on exploration. In practice, collecting and analysing data from various sources, such as satellites, drones, and seismic sensors, helps identify potential ore targets and estimates more efficiently while reducing costs and risks.
In addition, the data collected by IoT devices blended with edge computing allows decisions to be taken quickly. Also, IoT devices blended with AI make a significant difference to the exploration success rate, as AI can help companies better understand the environment and terrain where exploitation is to begin.
GlobalData, the leading provider of industry intelligence, provided the underlying data, research, and analysis used to produce this article.
GlobalData’s Thematic Intelligence uses proprietary data, research, and analysis to provide a forward-looking perspective on the key themes that will shape the future of the world’s largest industries and the organisations within them.