Interview
5G: the ‘connectivity enabler’ for underground mining
Claire Jenns speaks to Ian Ross, head of private cellular networks at Ericsson about the promise and challenge of using 5G technology in underground mining.
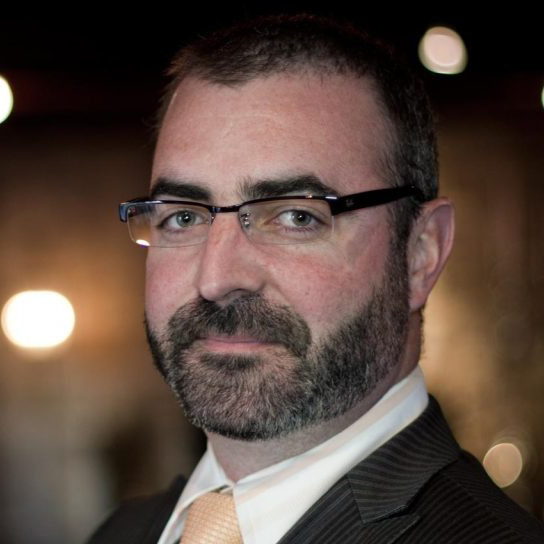
Ian Ross, head of private cellular networks ANZ for Enterprise Wireless Solutions at Ericsson.
5G technology helps improve safety and boost productivity in underground mining operations. So much so, a trial of 5G at the Cadia underground gold and copper mine in New South Wales, Australia, carried out by Newmont in partnership with Ericsson and Telstra Purple, has now prompted the miner to expand the use of 5G networks across its global network of Tier 1 underground gold-copper projects.
Newmont says it will use 5G to roll out more autonomous drill rigs, graders and auto haul trucks as part of future mining operations, while deploying radars and collision avoidance systems to improve mine safety.
“The trial results show the extraordinary potential of 5G to improve safety, increase the number of machines that can be operated on a single network and boost production efficiencies in underground mining,” said Suzy Retallack, Newmont chief safety and sustainability officer.
Mining Technology spoke to Ian Ross, Ericsson Enterprise Wireless Solutions' head of private cellular networks ANZ, about the use of 5G in mines, the complexity of delivering connectivity underground and how 5G can support greater automation and thus improve safety.
Claire Jenns: What benefits are there to using 5G technology in underground mining?
Ian Ross: Safer and smarter underground mining has great dependence on remote control, semi-autonomous and autonomous technologies to move workers out of harm’s way, and where possible, allow as much of the mine’s operation to occur from the safety of the surface or outside the mine pit.
Mine digitalisation also sees greater use of sensors and control systems through an underground complex. Drones can be used for mapping, gas detection and ventilation control systems. Digitalisation can also allow faster resumption of mining after blasting (while managing power consumption), smart rock bolts that can provide real-time visibility of the stability and safety of a drive, or proximity-detection and location management systems to keep track of works and equipment.
These systems are all inherently wireless and involve more critical data. As miners become dependent on these systems, they reach the capacity and performance limits of existing technologies and find their operations constrained. The connectivity needs to be pervasive through a facility, dependable, and capable of supporting the full array of applications that mining operators want to leverage, in any location and in any density of users and machines.
5G delivers significant benefits to miners, both over existing 4G cellular but most significantly over Wi-Fi.
This is where 5G delivers significant benefits to miners, both over existing 4G cellular and most significantly over Wi-Fi. 5G provides stable, deterministic performance, in that wirelessly connected mining operations depend upon predictable throughputs and latency, independent of load. This means that critical applications can receive the connectivity they need without unnecessarily triggering safety system alerts due to lost or delayed data packets.
Where large amounts of uplink throughput are needed, such as for video or remote control, 5G provides the ability to extract more performance from the radio spectrum than for example 4G. This means more machines can operate in a given area without networks running out of capacity to support them, or remote-control systems can utilise more cameras with better-quality video.
The complexity of delivering connectivity underground is higher than on the surface, with vastly different economics. In an underground mining setting, it is not as simple as putting a radio or antenna on a tower and covering kilometres of distance. Underground, we need to manage the propagation of radio signals through complex networks of declines, drives, and cuddies. Leaky feeders, like those used for two-way radio systems, are cost-effective for distributing radio signals but are unable to leverage the full performance of cellular networks. 5G technology applied to these leaky feeder systems has been found to double the available uplink throughout – essential for fleet monitoring and control – and with the multi-carrier radio innovations that have been developed for public networks, can provide further multipliers of performance.
Emerging 5G Internet of Things (IoT) technologies…will enable entire networks of lower-power sensors to be deployed – all powered by long-life batteries – allowing mine controllers to extract data and telemetry from any piece of machinery or part of the mine that has a temperature, makes a noise, vibrates, or moves.
Claire Jenns: What are the challenges in implementing 5G signals in deep underground mines?
Ian Ross: The biggest challenges are safety and maintainability, which is why we don’t see a lot of public 5G coverage underground. Carriers are unable to cost-effectively deploy and manage extensions of their networks themselves, which is why mine operators proceed to invest in their own private 5G networks, so they have all the benefits of 5G technology but via an infrastructure that they own, operate, and control with their on-site staff.
More practically, the challenge of implementing 5G underground comes to how to propagate radio signals, as described above. There is no one correct approach. The design and method of radio distribution in a mine varies with the mining technique being used to address the ore body, but also the size of the fleet and nature of the mining systems being used.
What is optimal for a long-hole stope may not be appropriate for a block cave, and neither may be appropriate for sub-level caving. We see a combination of leaky feeder distribution, discrete radios, and even different frequencies all combining in different places and ways to provide an effective 5G connectivity system.
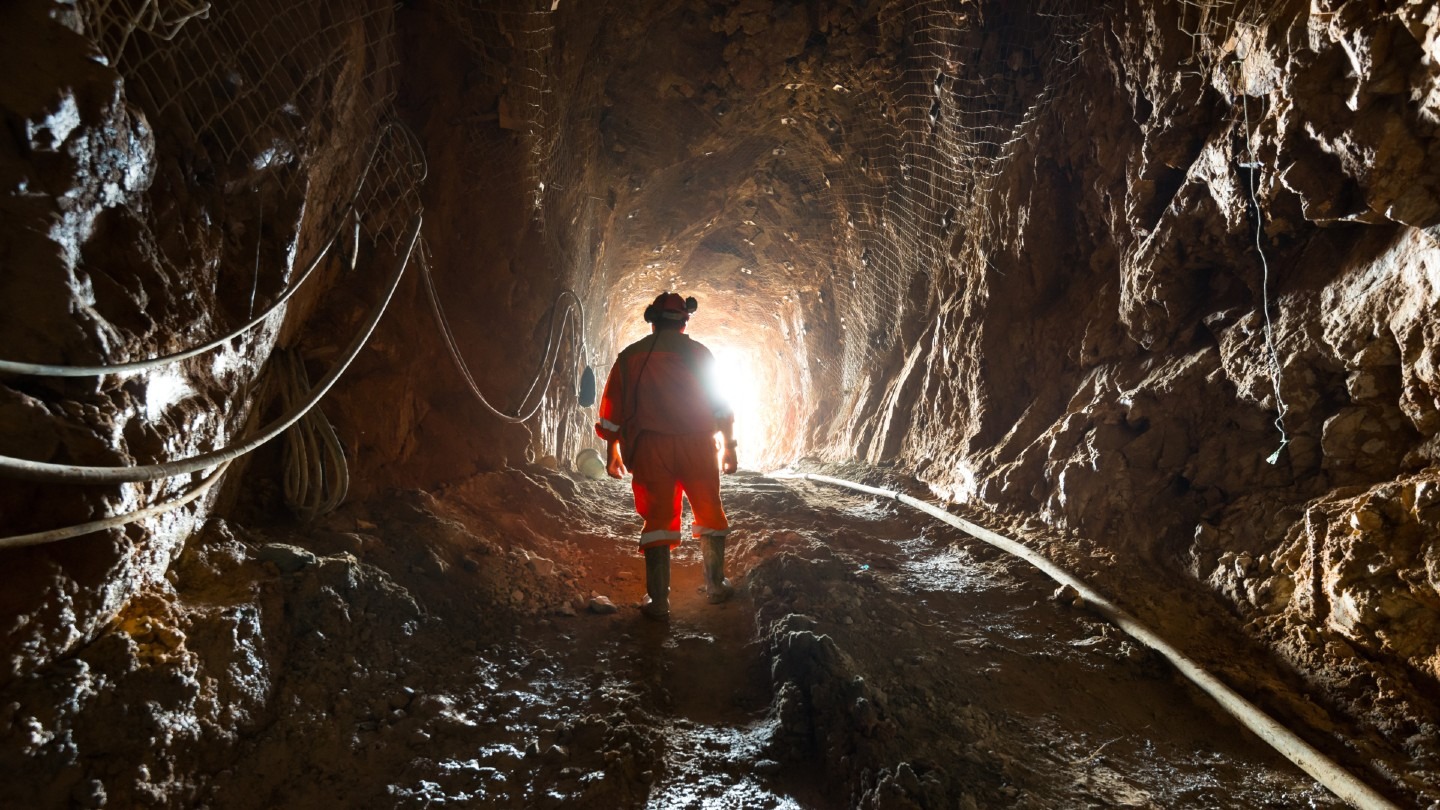
5G connectivity can help improve the safety of underground mining. Credit: tifonimages / Getty Images
Perhaps the most significant challenge is ultimately the perceived operational complexity of cellular networks, and many miners are apprehensive towards whether they have the skills and capabilities on the rosters to be able to safely and effectively deploy and operate these networks.
Ericsson, through our Ericsson Private 5G platform, has solved these issues by bringing…the associated orchestration and automation systems to enterprises. […] This means that miners can deploy and leverage all the benefits of 5G cellular through their operations with their existing technical teams, without any need to recruit, train, and retain deep cellular expertise.
Claire Jenns: How does 5G integrate with other equipment (such as vehicles)?
Ian Ross: 5G at its essence is a powerful, controllable, and predictable communications layer that can provide low latency, high throughput connectivity between devices in the field to workloads and control systems in a central on-site data centre or to the cloud.
Vehicles, workers, sensors, and process control systems can be easily integrated into a 5G network by replacing their existing connectivity – whether a Wi-Fi modem or fixed connection – with a 5G-equipped modem or router.
Connection to private 5G networks is controlled by private SIM cards that carry unique network codes and encryption keys that ensure that only approved devices can connect to the network, and when they do, what experience and priority they can obtain, and what other traffic they can interact with.
5G networks use common and open interfaces to connect to machinery and vehicle networks, as well as server workloads, so represent minimal complications when miners seek to connect equipment and systems designed for use on traditional IP networks.
Solutions like Ericsson Private 5G extend the integration capability further with a series of API interfaces that allow the 5G network to integrate with existing management and supervisory systems, allowing fault and performance monitoring, as well as KPI and provisioning integration.
Claire Jenns: How does 5G support the transition towards deeper mining?
Ian Ross: Deeper mining results in larger and more elaborate complexes of drives and galleries, with longer times to mobilise staff into the mining areas, and with the associated risks of higher temperatures and incredibly more dangerous task of safely recovering workers in the case of an incident.
5G provides the connectivity enabler for a whole suite of smart and safer mining technologies to be deployed reliably, viably, and efficiently in deeper mining operations.
The key to the safety and efficiency of these operations will be to make the operating levels ‘dark’, allowing workers to operate machinery at great depths without having to venture deep into the earth. Remote control and automation – whether drilling, loading, or hauling – eliminates the need for staff to work regularly in these higher-risk environments.
5G provides the connectivity enabler for a whole suite of smart and safer mining technologies to be deployed reliably, viably, and efficiently in deeper mining operations, letting robotics and automation take the risk of deep-earth operations while staff remain in the safety and relative comfort of surface facilities.