Feature
Mining pumps lead the way in water management innovation
Mining pumps are going from being the unsung heroes to the frontline of greater mining sustainability, as Andrew Tunnicliffe writes.
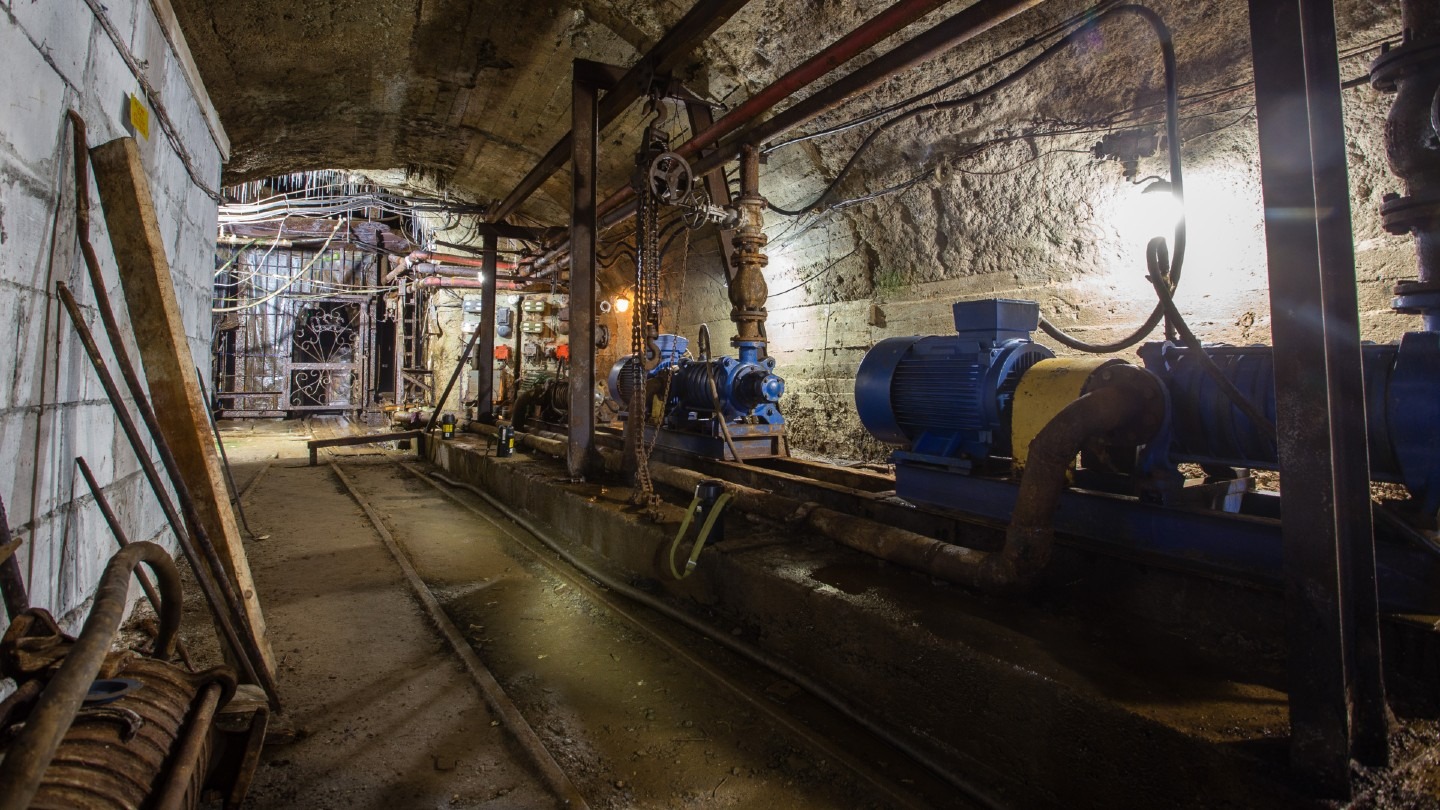
An underground gold mine water pumping station room with pumpsets. Credit: Mishainik / Shutterstock
Today, mining companies are more focused on sustainability than ever before, looking to protect the land and environments they work on and in. To that end, water consumption and its preservation are making a march towards the top of environmental, social and governance (ESG) agendas in mining companies large and small, driving innovation in mining pump design.
Atlantic Pumps managing director Andy Smith says preserving water, reducing a mine’s impact on the environment and much higher energy costs are leading the charge for innovative developments from pump original equipment manufacturers (OEMs).
“The realisation that water is a precious resource is still a relatively new concept and one which requires further education,” says Smith, who heads the UK-based manufacturer and supplier of electric and diesel dirty water and slurry pumps.
“However, mine operators are now having to operate with this in mind, making dewatering, and any processes using water, quite a different economic model.”
This growing awareness is helping drive innovations in both products and processes, Smith believes. “Water costs will continue to increase, making lifetime cost models drive better pump and treatment solutions,” he says, adding water recycling will become ever more cost-effective as a result.
Energy efficiency drives innovation
Among the other key drivers in mining pump innovation highlighted by Smith, the rise in energy costs that mining – one of the most energy-intensive industries in the world – has been facing looks to be “here to stay”.
In his view, this means efficiency is of growing importance in the design and development of modern pumps.
“Pump specification has generally been driven by the best fit on commissioning, whereas live time running is now being recognised as the more important driver,” Smith says.
With energy accounting for anywhere between 10% and 40% of mine operating costs, reducing consumption not only goes towards mines cutting their carbon emissions but can also play a significant role in decreasing operational expenditure.
Although mining's largest contributors to energy consumption come from exploration and extraction – such as digging and drilling equipment – and materials handling, today’s pumps have a noteworthy and growing role they can play.
Pumps are used from mine dewatering to the beneficiation plant and beyond. But Smith is confident that, regardless of where they are deployed, mining pumps are a continued focus of innovation. He says that although developments are happening across the sector, the critical three areas are: materials, being longer lasting and more sustainable; efficiency such as their energy requirements; and machine learning for improved maintenance support.
Digital technologies enhance maintenance
It is maintenance that Erkki Kohtanen, vice president of sales for industrial minerals and dredging at KSB Mining, believes will shape the mining pumps of tomorrow.
“With fewer personnel on the field and limited downtime, it is crucial that pumps require minimal maintenance,” he argues. “Pumps achieve optimal performance when properly maintained, so operators need efficient solutions for effective maintenance and monitoring.”
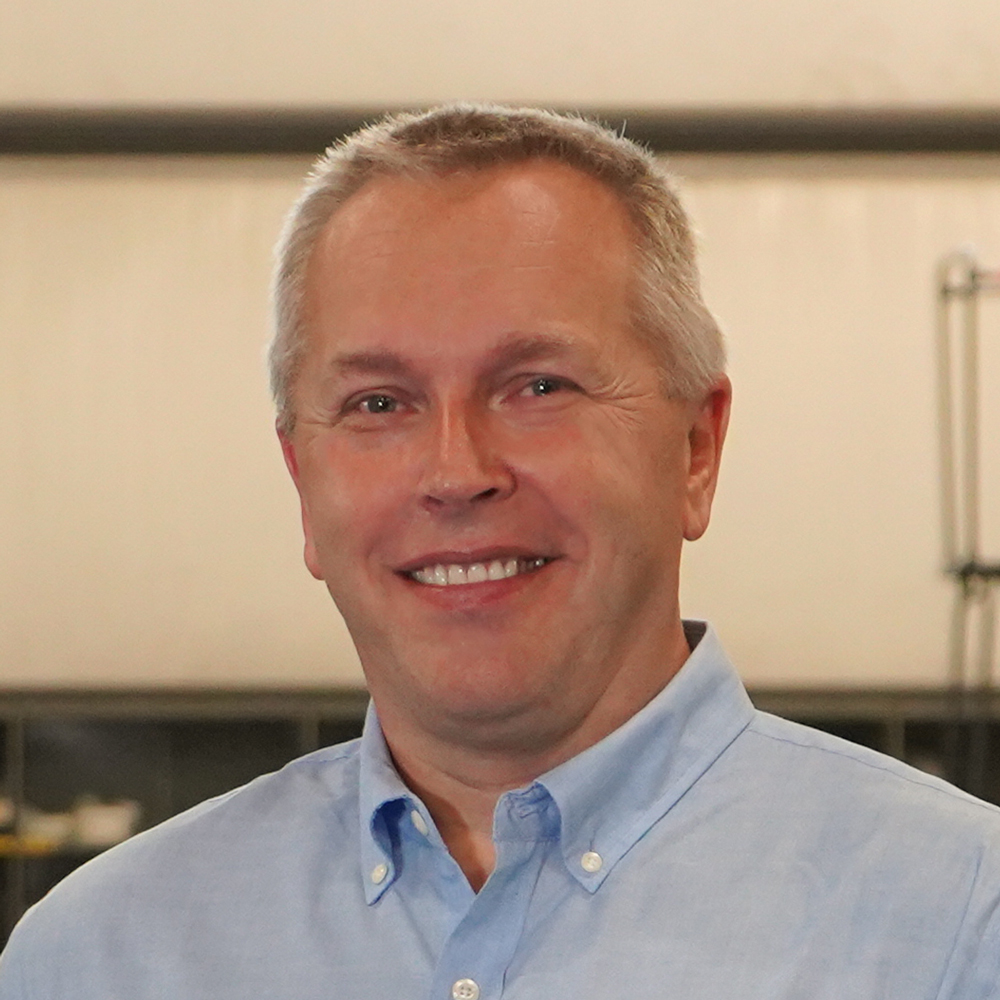
Erkki Kohtanen, vice president of sales for industrial minerals and dredging at KSB Mining
“With fewer personnel on the field and limited downtime, it is crucial that pumps require minimal maintenance.”
Erkki Kohtanen, vice president of sales for industrial minerals and dredging at KSB Mining
This, although still a relatively new concept in pump design and support offerings available to miners, is an area many pump OEMs are quickly embracing. Quinton Sutherland, Weir’s divisional senior product manager for pumps, says similar to many industries, digital technologies are playing an increasingly important role.
“For Weir, it’s another way [we] can support customers’ efforts to improve the efficiency of their operations,” he says.
The company’s NEXT Intelligent Solutions features an AI-powered intelligent assistant that, Sutherland says, helps miners overcome process optimisation challenges.
“This allows Weir to take a holistic approach in which, rather than focusing on the performance of individual pieces of equipment, analyses the performance of the entire circuit.”
Sutherland adds that as a result, miners can quickly adapt to variables such as changes in the feed or plant degradation, for example, to provide real-time optimal performance and sustainable production.
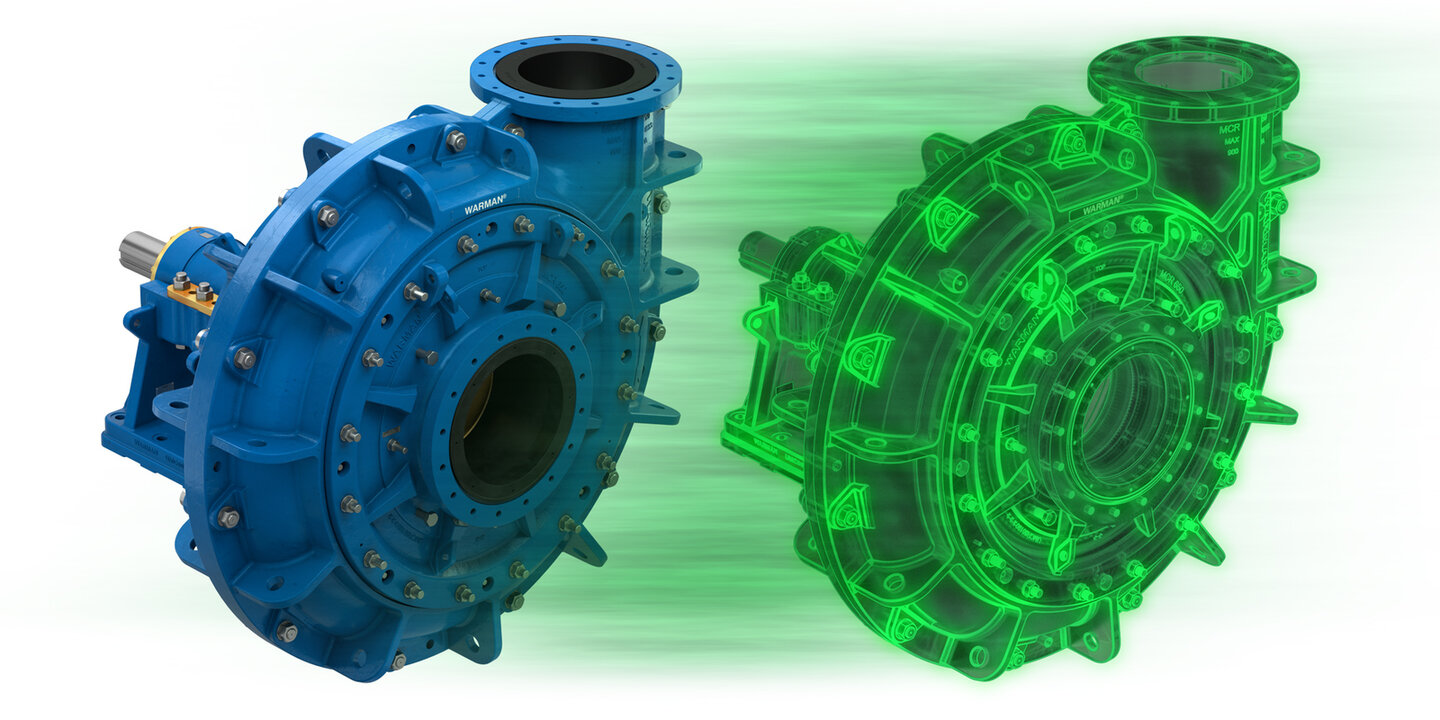
Digital twins play a key role in enhancing overall equipment effectiveness. Shown here is Weir’s WARMAN® MCR® 650 pump and its digital twin, which utilises NEXT Intelligent Solutions. Credit: Weir
Moving towards smart mining pumps
“The biggest next step shall be smart pumps,” says Kohtanen.
“KSB GIW has developed a special IoT [Internet of Things] solution, GIW SLYsight, which can measure the critical dimensions of the pump and indicate to the customer the need for pump adjustment, and expected run time left on wet end parts, etc.”
In conjunction with the GIW RAMSL, or remotely adjustable suction liner equipment, he adds, pumps can accurately be adjusted during their operation to “guarantee the most efficient, reliable and maintenance-friendly pumping solutions” for cyclone feed or any large hydro transport pumps.
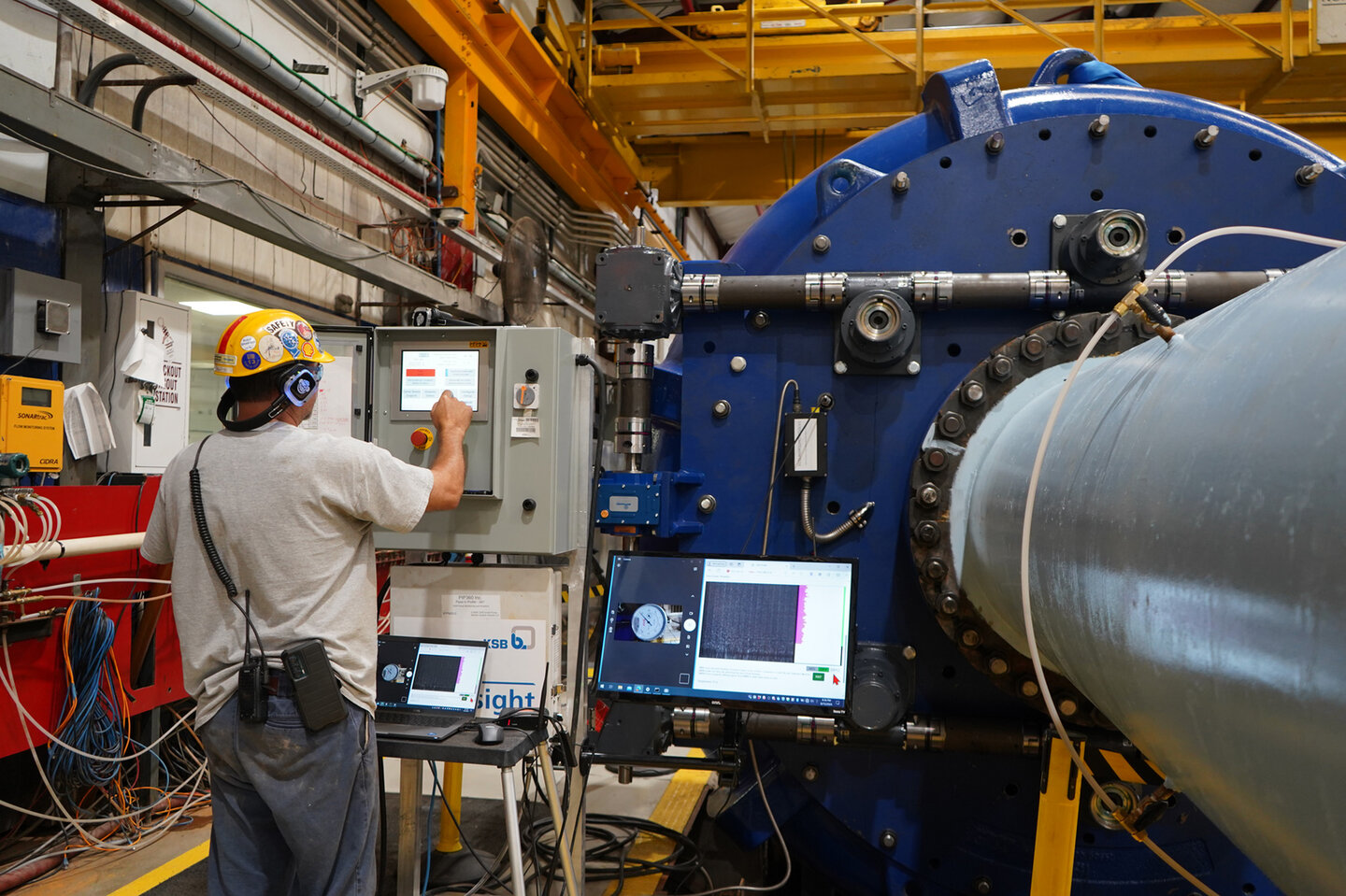
IoT-based solutions such as KSB GIW’s SLYsight and RAMSL can be used to adjust pumps during operation. Credit: KSB GIW
“KSB GIW is offering IoT technologies that allow operators to safely make pump adjustments and determine maintenance cycles, all while using the latest materials technology to increase the durability of pumps operating in various applications,” Kohtanen continues.
Key considerations in pump design
As Kohtanen alludes to, mining pumps come in a huge and growing array of iterations, each with its own specific requirements and objectives. But the core design principles remain: effective, efficient and durable.
To address these, the materials pumps are constructed from and their ability to operate in some of the most challenging environments is critical to their operating lifecycle. As a result, he says, the continuous development of wear materials “never stops”.
A further factor, again one of growing importance, is the need to conform. “Legislation around water discharge is also rapidly developing,” says Smith of Atlantic Pumps.
“This represents a huge risk for companies in an area they historically might have turned a blind eye to. Technology around monitoring and reporting is therefore rapidly developing.”
A major contributor to this growing need has been the increasing depth that underground mines are reaching in the quest for more and higher-grade ore deposits. But with that comes an amplified risk of minerals and contaminants being unearthed and making their way into water. This necessitates continuous treatment before discharge.
Innovation in dewatering systems
Kohtanen says that even now, as technologies evolve, the challenge posed by the amount of solids in drainage water remains; it is an issue that continues to drive pump OEM innovation as their mining customers increasingly look for dewatering systems that are reliable, require minimised processes, and help the site to stay efficient.
However, Kohtanen cautions that there is no one-size-fits-all: “Obviously, some compromises are always needed, which in the end defines which pumping arrangement would give the best long-term efficiency, reliability and less maintenance need for the dewatering system.”
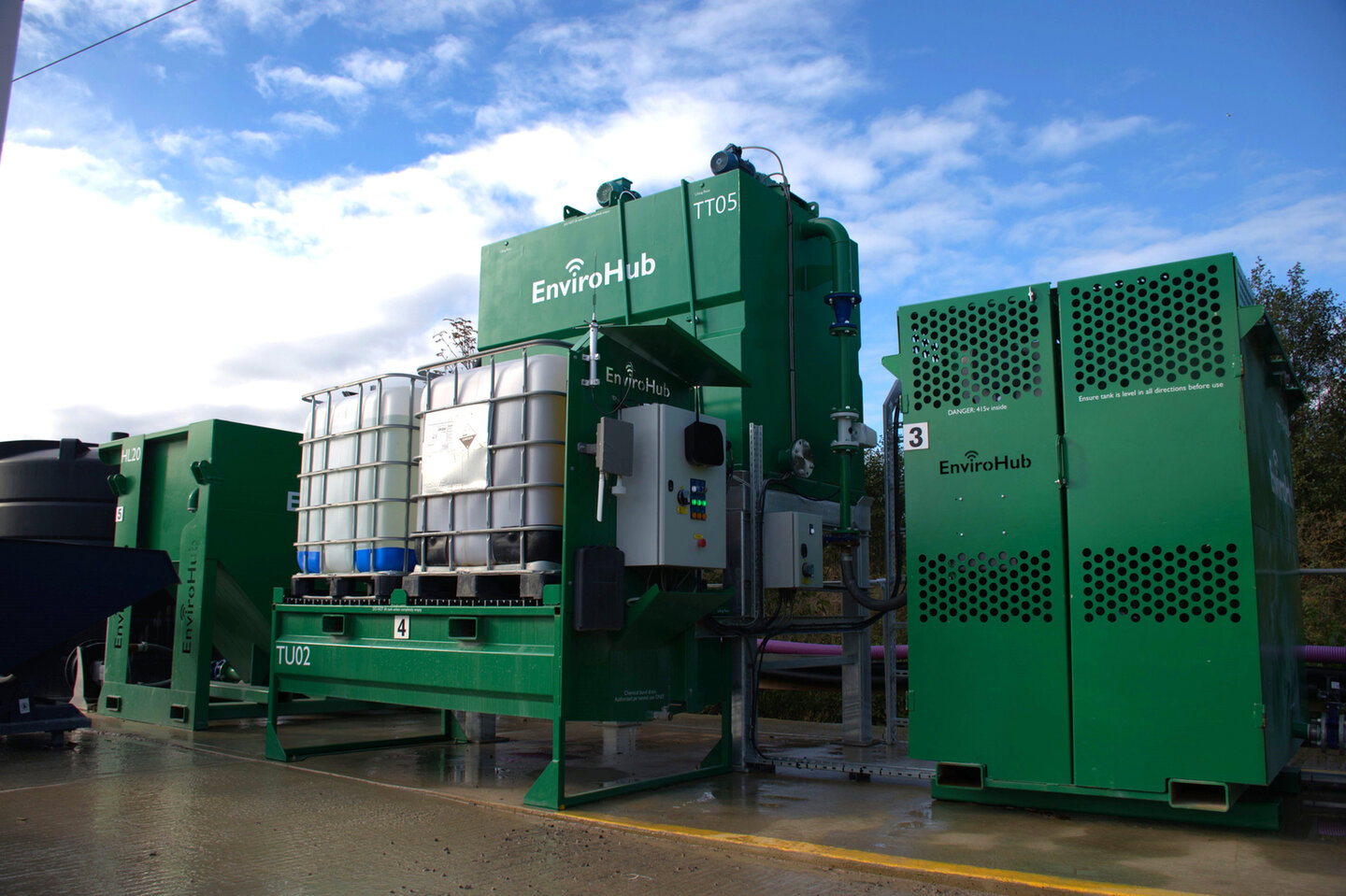
The EnviroHub Lamella tank, dosing unit, treatment tank and correction tank. Credit: Atlantic Pumps
This is an area where Smith and Atlantic Pumps are most proud of its offering. He says its EnviroHub unit has a direct impact by sustainably protecting the environment. Specifically designed for quarrying and construction, the system monitors and identifies any unsafe water and treats it before disposal. It also provides full data and reporting that helps sites ensure they are complying with local regulations and provides documented proof of the steps taken.
Recognising this is a growth area, Smith says the company will continue to focus on the monitoring space given the benefits it offers and as operators become increasingly comfortable with using electronic controls to improve outcomes.
The future of mining pump innovation
As mining operations evolve to address the growing demand for materials of the future, so too do pump OEMs and their product catalogues.
Highlighting the drivers that KSB, Atlantic Pumps and Weir have identified – declining ore grades, increased demand for metals and a greater focus on sustainability – Sutherland concludes: “As miners face new challenges and more constraints, OEMs… need to continue innovating and working with their customers to enable them to continue producing the minerals that will be required for the energy transition.”

Quinton Sutherland, divisional senior product manager for pumps at Weir
Smith echoes the view of Kohtanen, that progressively customers are looking for more tailored offerings rather than off-the-shelf solutions; but, he says, this is something that has the potential to prove more challenging as the need to be financially astute in decision-making continues to dominate.
“One of mining’s biggest problems is now fundraising,” he warns. Pointing to a “more risk averse commercial environment”, Smith says helping companies to cost-effectively trial processes to “prove to their finance partners that this is a sound investment” is important for OEMs to get on board with.
“For pumps, this means being able to support technologies at different scales.”