Company Insight
Sponsored by HINDSITE Industries
HINDSITE: Guided work instructions for an instant record of work
HINDSITE is being adopted rapidly by METS operations across Australia. With a new office now open in Brisbane to support its growth, we dig into how the Guided Work Instructions platform is poised to enhance consistency and reliability for mining nationwide.
Main image credit:
HINDSITE has been making waves across Australian mine sites over the past year and for good reason. The Brisbane-based company has turned the tide on being able to take any hands-on procedure, OEM manual process or mud map diagram and turn it into an easy-to-use digital workflow with an immediate record of work.
The company’s customers, including IMDEX, GroundProbe, Strata Worldwide and Hastings Deering, have seen unprecedented results in their operations. These range from halving the unavailability of critical safety systems to significantly increasing productivity throughput.
“The common refrain we hear from our mining equipment and technology customers is that they were snowed under and didn’t know where to start when it came to bringing skilled work processes into the 21st century”, reflects Doug Hastings, CEO and Co-founder of HINDSITE.
“We seem to have cracked the code with Guided Work Instructions. HINDSITE lets anyone play ball straight away.”
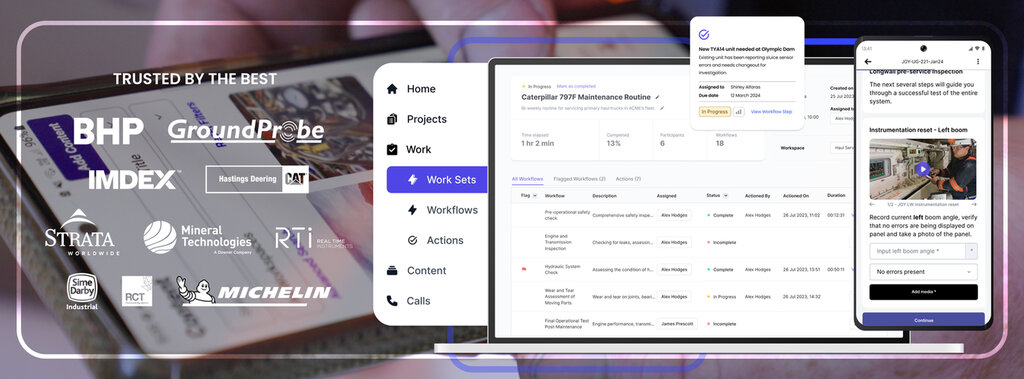
Mining Equipment, Technology and Services (METS) businesses are using HINDSITE across Australia for Guided Work Instructions.
The (not-so-humble) Workflow
The HINDSITE product is based on the simple idea of a step-by-step Workflow on a mobile device.
Replacing the dusty OEM manual, static inspection checklist or undocumented know-how passed down in training seminars or on the job, a Workflow guides a frontline worker through tasks, gathering user input data and providing an immediate report as a record of completion.
Co-founder and COO Liam Scanlan explains that his inspiration for HINDSITE came from his own lived experience. “I was on a mine site, undoing a bolt that turned out to be the wrong bolt. $40,000 later I knew I should have read the manual. But I hadn’t”.
The secret to HINDSITE workflows is that they don’t assume the person on the job is an expert.
Every step can be enriched with media such as bite-sized videos, imagery, and PDF content. This way, expert knowledge is passed down precisely when it’s needed, increasing memory retention.
HINDSITE Workflows themselves can be grouped and templated into Work Sets, providing confidence and evidentiary data to team leaders that tasks will be completed in a way that exceeds customer expectations.
Workflows across the product lifecycle
Mitch Rays, Field Service Supervisor for Pakka Jacks, says HINDSITE solves a few problems all at once. It can “combine our paperwork, documentation, our quality assurance as well as our procedures and boil that all into one Workflow. It’s magic”.
Hastings shares similar success stories: “We heard a customer say just last week that their junior technician in Western Australia was able to jump on a workflow at 2am and solve a problem independently in 43 seconds.”
To keep up with growth, HINDSITE expanded its Brisbane offices last month. METS businesses across the country are increasingly using HINDSITE across all stages of their product life cycles.
GroundProbe uses the platform to standardise assembly quality across their Australian and American manufacturing facilities. Mineral Technologies includes HINDSITE into their service and support package for Mobile Mining Unit sales.
IMDEX and Real-Time Instruments separately use HINDSITE to support workers in the field with self-service and around-the-clock troubleshooting and operation instructions.
Michelin uses HINDSITE for consistent scheduled maintenance of tyres. Strata Worldwide uses it to install and commission equipment into the South Australian copper province.
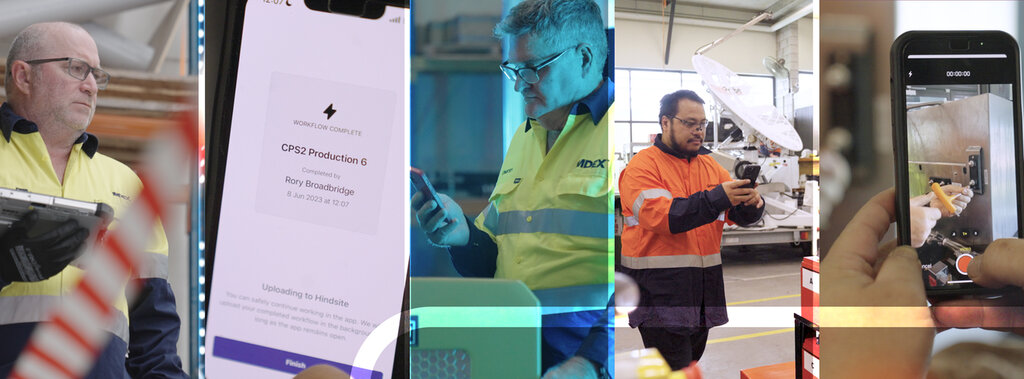
From the production line to routine maintenance, HINDSITE ensures all tasks are completed consistently to maintain safety and quality.
An immediate record of work
HINDSITE seeks to not only solve for inconsistent task execution in the field, but to expedite the outputs of that work back in the office.
“We’re ultimately improving the quality of relationships between METS businesses and their mine customers” says Hastings.
The app provides an immediate record of work in the form of a Workflow Report. If additional tasks are required beyond the procedure, they can also be managed in HINDSITE using follow-up actions. A HINDSITE workflow report:
- Reduces rework as evidence of work is captured in a standard way and it can be reviewed in real time
- Reduces time spent by frontline technicians building reports
- Reduces time spent by project managers chasing and managing records of work
- Allows leadership to trust the evidentiary data gathering process
- Provides leading indicators of the health of frontline work processes
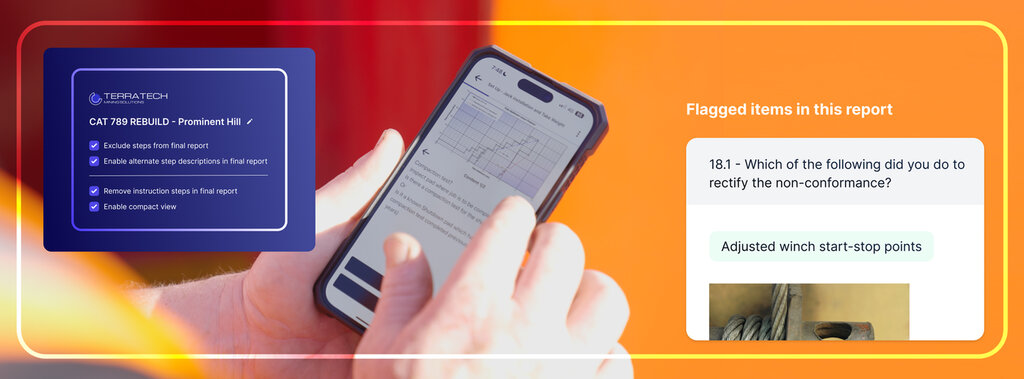
Every Workflow in HINDSITE generates an immediate completed report for sharing internally and with customers.
“More than just another checklist app, we’re letting managers and project leaders gain visibility into what is happening in their jobs in real-time. What’s more, they can share that information with their customer as soon as a job is complete”, explains Hastings.
A business model for scale
The end result of using HINDSITE is a business that approaches every task with a culture of consistency and continuous improvement. The cherry on top is having records to prove it to customers and improve for next time.
If you have a process or instruction set on hand and you would like to see what it would look like in HINDSITE, submit it to the team here and they will convert it for you.
At worst, you might get a little inspired. At best, you solve for inconsistent task execution and elevate your customer relationships.
Contact information
HINDSITE Industries
Tel.: +61 7 2100 4470
Email: sales@hindsiteind.com
Web: www.hindsiteind.com