Feature
Australian miners at the forefront of the robotics revolution
As robotic technology advances, Australian mining companies such as Rio Tinto and BHP are among the leaders in deploying automated systems to enhance operational efficiency and safety. Smruthi Nadig reports.
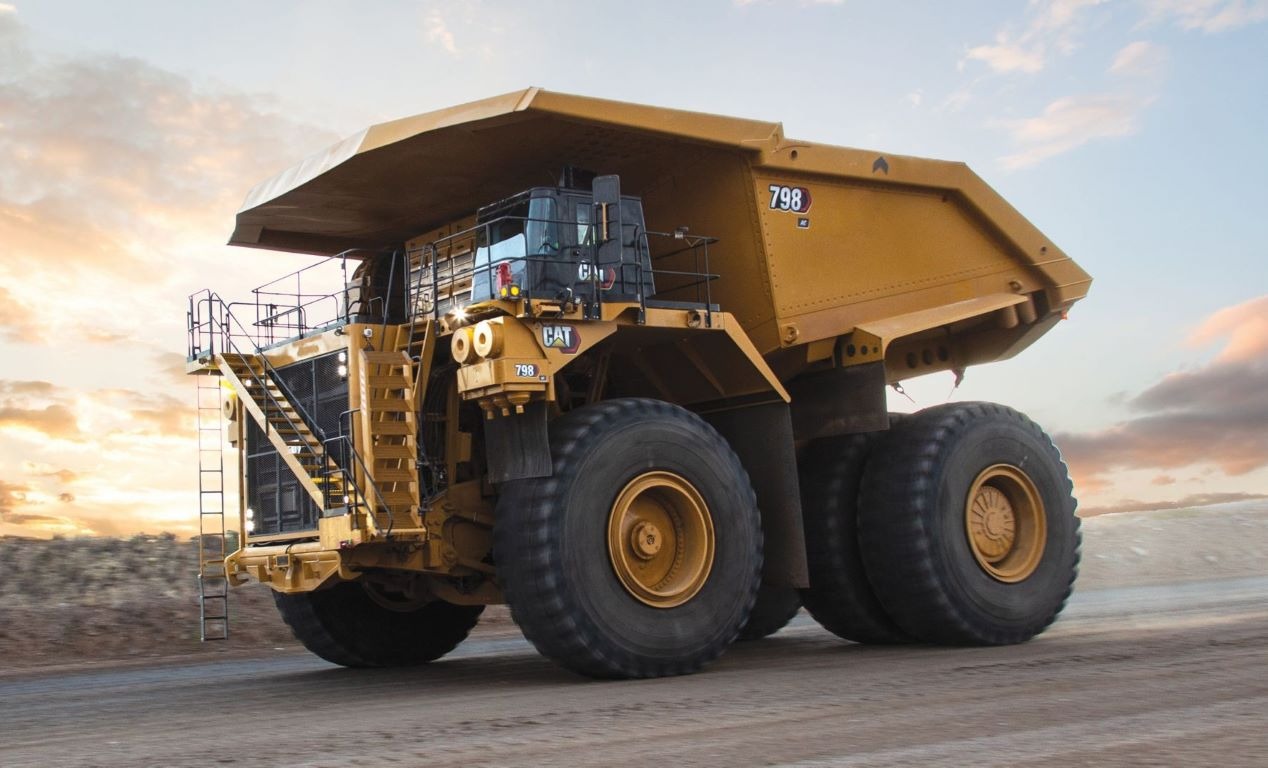
Mining trucks are a key are for robotic and autonomous technology. Credit: Caterpillar
Australia has a strong robotics industry that focuses on automation in both the manufacturing and agricultural sectors, which sets it apart from other robotics markets. GlobalData research indicates that 29% of robotics companies in Australia cater to the mining sector. Besides the robotics industry itself, the main industries served by robotics suppliers are metal and machinery, with 47% of suppliers serving these industries.
GlobalData’s recent report on robotics in mining reveals that the robotics industry was worth $63bn in 2022. By 2030, it will have grown at a compound annual growth rate (CAGR) of 17% to $218bn.
Sales of industrial robots amounted to $20.7bn in 2022, accounting for 33% of the total robotics market. By 2030, this segment is expected to be worth $45.1bn, representing a CAGR of 10% between 2022 and 2030, according to the report.
Mining companies deploy robotics across various parts of their operations, from surface mining to underground excavation and mineral processing.
How robotics can help to solve mining challenges
The mining industry is under pressure to reduce costs and improve efficiency and safety, and automation could provide one solution. Automating repetitive tasks reduces the risk of human error, and robots are accurate and dependable, ultimately increasing operational efficiency.
“Robots can address many of the main challenges faced by the mining sector,” says Martina Raveni, a thematic analyst at GlobalData. “Robotics and automation are improving safety in mines, and mine productivity, one of the main concerns within the industry, is significantly improved by robotics. Robotics plays a crucial role in various operations such as hauling, drilling, blasting and exploration.”
The mining sector has been transformed by the integration of robots such as drones, autonomous haulage systems and remote-controlled equipment. Drones are used to survey mining locations and acquire data on aspects like topography and the distribution of mineral layers, while remote-controlled machines are increasingly being used for tasks such as drilling and blasting.
Rio Tinto and BHP lead the way
Transportation is another area that can see significant benefits from the adoption of robotics.
Driver shift changes and product loading and unloading result in downtime for mining companies. In June 2019, Rio Tinto launched AutoHaul, a fully automated train system operating in the Pilbara region of Western Australia (WA), to address this issue.
The system consists of 50 crewless trains covering a 1,500km network, making it the world's largest robot. Each autonomous train comprises three locomotives and can transport around 28,000 tonnes of iron ore. The trains are monitored remotely from Perth.
According to GlobalData, Rio Tinto reported several operational benefits including increasing average speeds by 5–6% and removing two to three driver shift changes, cutting an hour from the average journey time.
However, the integration of robotic technology into mining operations also has its challenges. In February 2024, a self-driving iron ore train derailed 120km from Dampier Port in WA. The accident involved 38 wagons, but fortunately, no one was injured. In June 2023, a similar incident occurred, with 30 wagons derailing 20km from Dampier. The company managed to maintain shipments from port stockpiles until the situation was resolved, and operations resumed a week later.
Robotic and autonomous technology has also seen significant uptake in drilling and blasting.
“Australia is a leading country in the mining sector, and Australian companies deploy cutting-edge technologies in their operations,” says Raveni. “For example, BHP inaugurated its first autonomous drill at the Chilean Spence mine in 2022. The company has also rolled out autonomous drills across its WA iron ore operations. In June 2022, it reached the autonomous drilling milestone of more than 479,607 hours in operation, drilling more than 25 million metres.”
BHP, Caterpillar and Finning are working on a ten-year project to replace BHP’s fleet of more than 160 haul trucks at the Escondido mine.
Meanwhile, the most notable progress has been made in robotic and driverless mining vehicles.
A GlobalData report on the development of autonomous trucks in the global mining sector found that BHP currently has the largest number of autonomous trucks, totalling 367 as of July 2023. This number includes both autonomous-ready trucks and those already operating autonomously.
BHP, Caterpillar and Finning are working on a ten-year project to replace BHP’s fleet of more than 160 haul trucks at the Escondido mine. The introduction of 798AC trucks equipped with autonomous operation technology began in 2023. Additionally, BHP’s Spence mine in Chile is implementing an autonomous trucks project in collaboration with Komatsu. The mine has started converting and replacing 33 trucks in its fleet, with the first trucks operating autonomously by mid-2023.
The company reported several benefits from the adoption of autonomous trucks, including a 20% increase in productivity, a 20% reduction in operating costs and a 90% reduction in haul truck accidents.
“The mining sector in Australia has seen a substantial increase in investments aimed at digitalising and automating operations,” Raveni says.
“GlobalData’s latest mine-site technology adoption survey highlighted that robotics is one of the investment areas the industry is prioritising. Indeed, 48% of mines surveyed have invested considerably in or fully implemented drones. Surveying, mapping, monitoring and inspection were the most common uses for drones at the operating mines surveyed.”
The road ahead for robotics in mining
Miners operating in remote and harsh environments grapple with many challenges. Limited connectivity can make effective data analysis and location monitoring difficult, which can pose risks to worker and equipment safety. Mining companies also need to evaluate their impact on the environment and their compliance with regulations while striving to maintain high efficiency.
Then, there are the challenges posed by declining reserves, supply chain disruption and pressure to improve productivity while keeping down costs.
“New mineral deposit discoveries are declining, as is the ore grade. Therefore, identifying viable new mines and determining the economic feasibility of extracting a known resource is becoming increasingly difficult,” Raveni says. “This has led to a shift to more underground mining and remote deposits, implying longer haul distances and labour costs and, therefore, an increased need for digitalisation.”
Identifying viable new mines and determining the economic feasibility of extracting a known resource is becoming increasingly difficult.
As resource depletion necessitates the extraction of lower-grade deposits, more advanced and expensive exploration and extraction techniques will be required. The industry has also become more globalised and more susceptible to market fluctuations. Most recently, the mining sector has felt the impact of the Covid-19 pandemic, which has worsened supply chain disruptions and labour shortages.
As the demand for many minerals increases, mining companies must manage operational safety, productivity, cost savings and ESG performance. Robotic technologies can help address some of these, particularly in the areas of safety and efficiency.
The robotics industry is witnessing significant growth and diversification. With a strong focus on automation in mining, energy, construction and other non-manufacturing applications, the adoption of robotic and autonomous systems is reshaping operations across many sectors.
Companies like Rio Tinto and BHP are leading the way in Australia in deploying autonomous technologies in their mining operations. As these solutions become more widely adopted, equipment manufacturers and end users must continue to work together to ensure their safe and effective implementation.