Innovative mining.
optimised ore recovery.
Many hard rock mines have ore rich reserves, contained in unmined area's, commonly referred to as sterilised ore.
Some causes of sterilised ore could be dry filled stopes, unfilled stopes, narrow unstable pillars and low grade pillars. Basically the inability to access valuable ore deposits for removal.
Through unique and well proven methodologies pioneered by Minova our solutions can maximise the extraction of previously sterilised ore resources that support
- Increased revenue from extraction of additional mineral resources
- Cost effective usage of R.O.M waste rock material
- Providing structural elements of a known strength for mine life extension
- Improved management of HSE risk
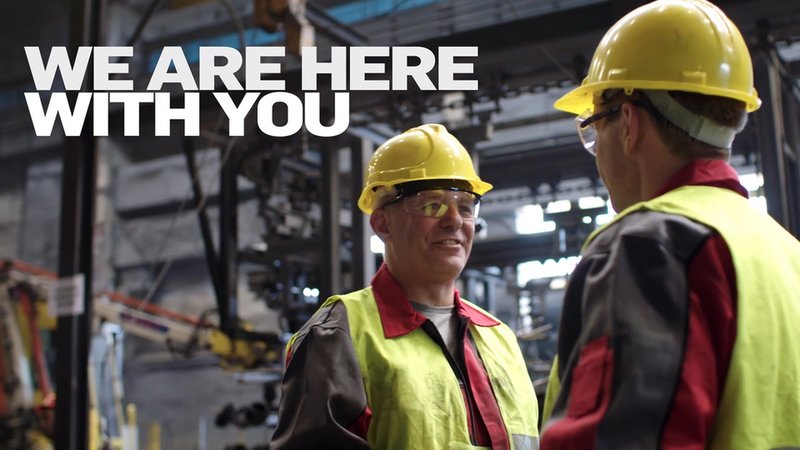
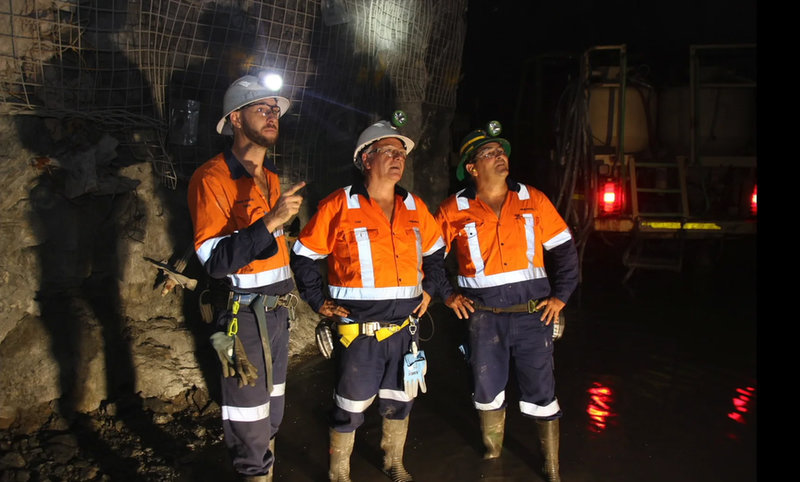
Who we have helped:
Round Oak Minerals
Newcrest Mining
Castlemaine Goldfields
Newmont
PHASE 1: PRE-WORK
Learn more about the pre-work required. See how we can help you!
Phase 2: Application
Learn more about the pre-work required. See how we can help you!
CASE STUDY
Read the Round Oak Case Study
Conference Paper
Read the abstract "Optimising the Recovery of Stopes at Bentley Mine"
Brochure
Download our brochure
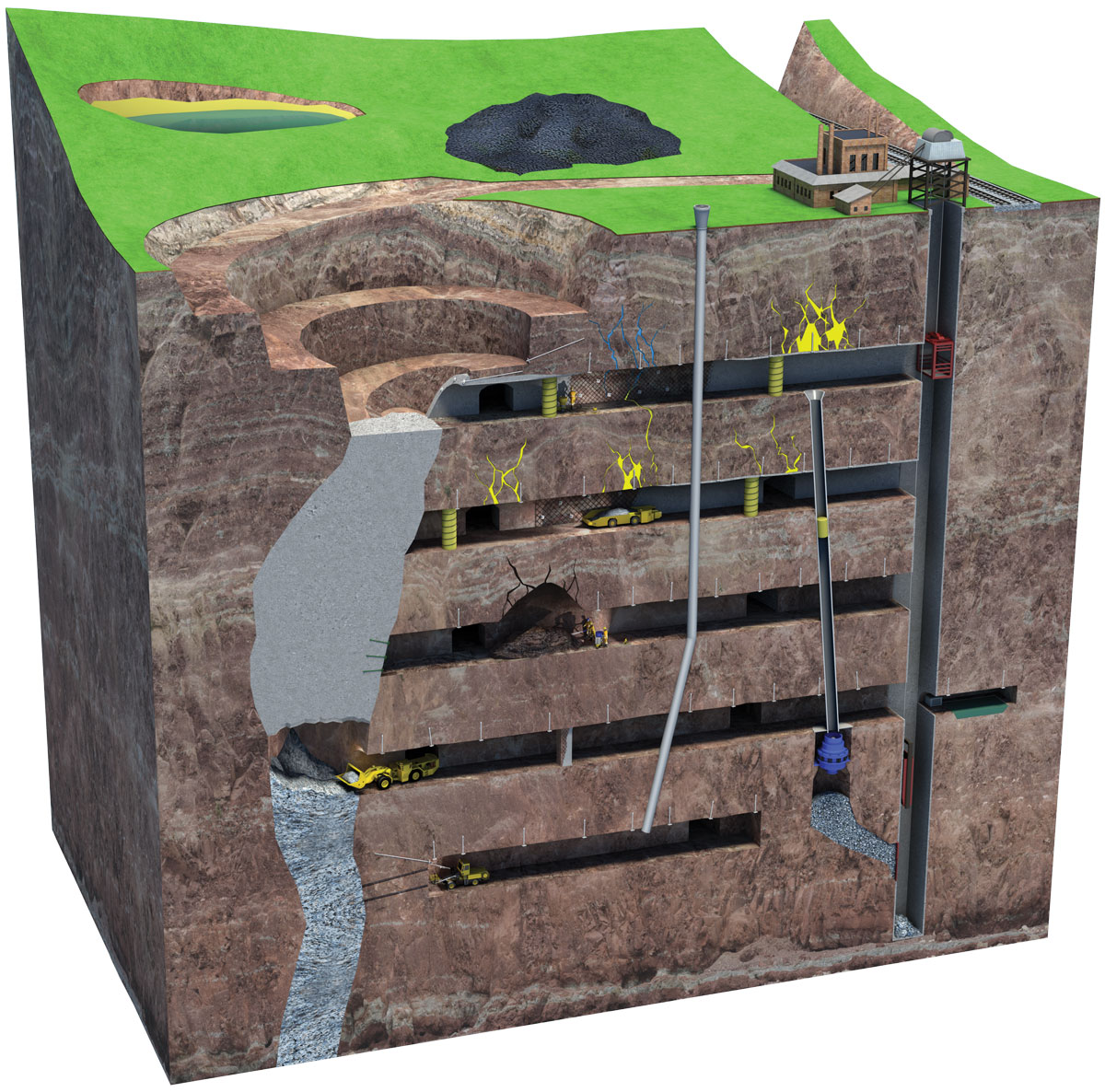
Click on the icons
1
2
3
4
1. Cavity & Backfilling
Increasing pressure from mining activity and variable geotechnical conditions can cause fractured ground, which if not supported, may lead to incidents of rock fall or roof collapse.
Learn more about cavity filling
High volume grouts
2. Ground Control
Ground control is fundamental to the integrity and safety of underground mining operations. Rock reinforcement methods vary and include point anchored bolts, friction bolts and grouted bolts. Minova offer multiple solutions for a wide range of bolts.
Not all resin bolts are the same.
Read our comparative information bulletin
3. Water control
Water ingress into an underground mine can represent a major risk if not recognised and rectified.
Learn more about our range of Injection Chemicals
4. Ore Recovery Optimisation
Many hard rock mines have sterilised rich ore left behind in vertical and horizontal pillars. With the placement of backfill adjacent to these resources, our solutions support safe and optimal ore recovery operations.
Contact Minova to find out how we can help you.
Minova solution
Read Round Oak Case Study
Innovative mining.
optimised ore recovery.
Many hard rock mines have ore rich reserves, contained in unmined area's, commonly referred to as sterilised ore.
Some causes of sterilised ore could be dry filled stopes, unfilled stopes, narrow unstable pillars and low grade pillars. Basically the inability to access valuable ore deposits for removal.
Through unique and well proven methodologies pioneered by Minova our solutions can maximise the extraction of previously sterilised ore resources that support
- Increased revenue from extraction of additional mineral resources
- Cost effective usage of R.O.M waste rock material
- Providing structural elements of a known strength for mine life extension
- Improved management of HSE risk
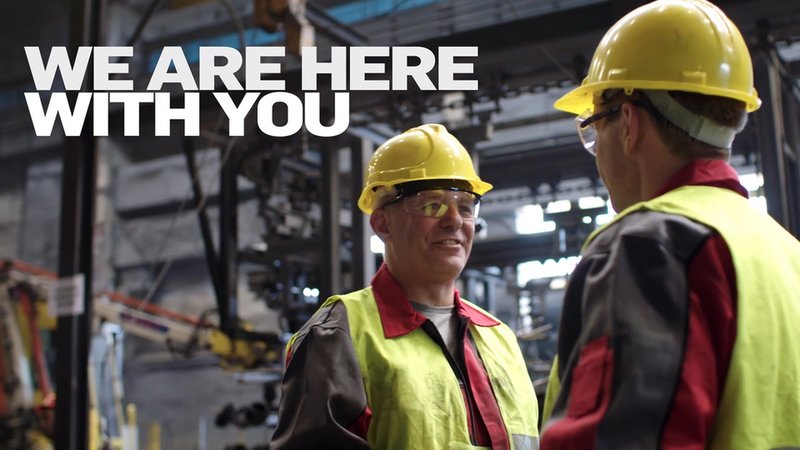
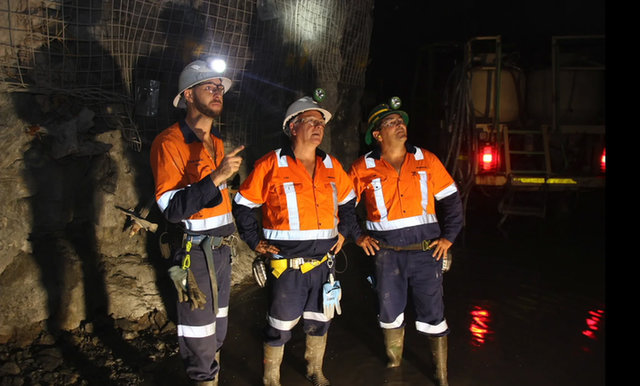
Who we have helped:
Round Oak Minerals
Newcrest Mining
Castlemaine Goldfields
Newmont
Phase 1: Pre-work
Learn more about the pre-work required. See how we can help you!
Phase 2: Application
Learn more about the pre-work required. See how we can help you!
Case Study
Read the Round Oak Case Study
Conference Paper
Read the abstract "Optimising the Recovery of Stopes at Bentley Mine"
Brochure
Download our brochure
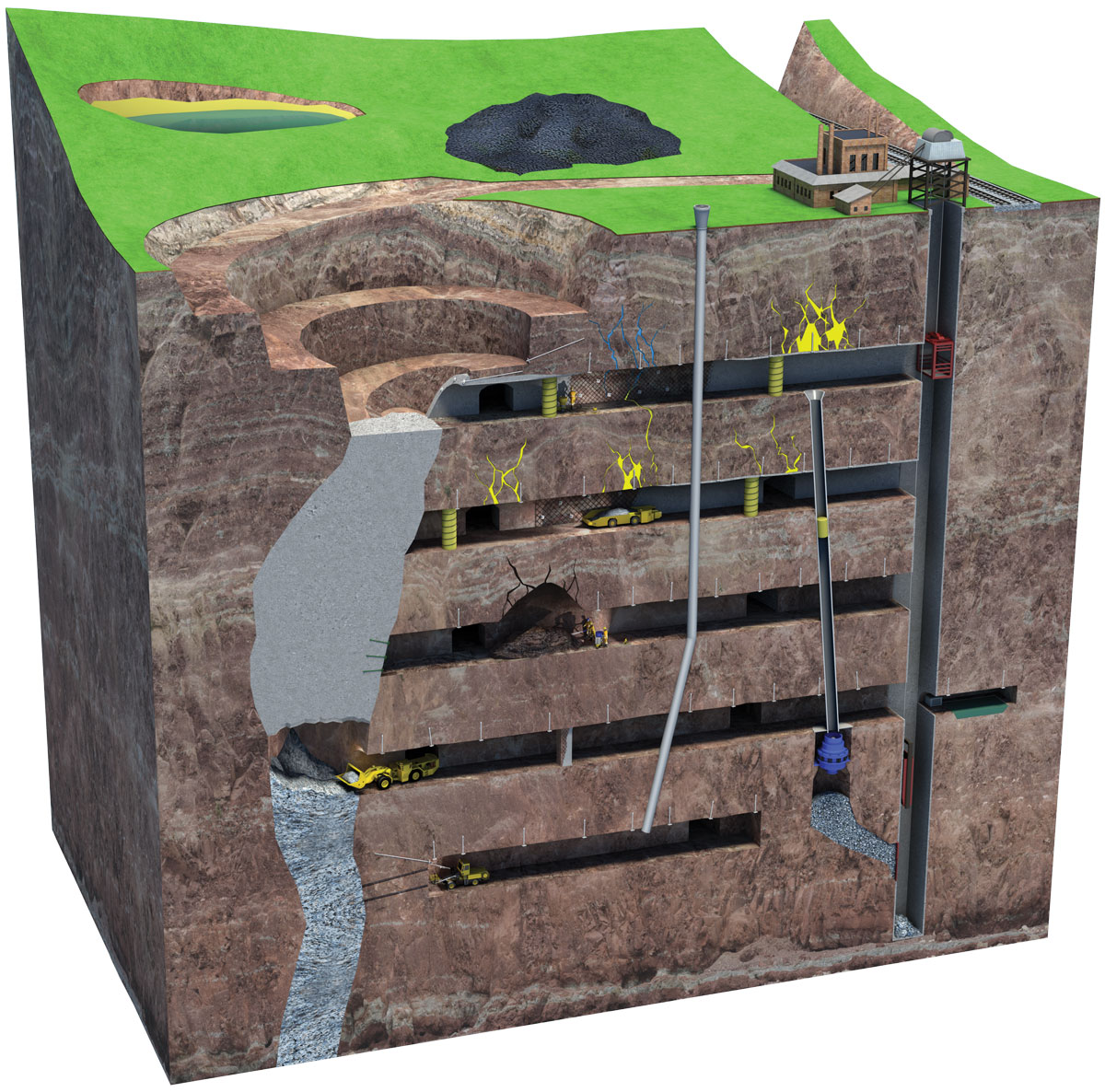
Click on the icons
1
2
3
4
1. Cavity & Backfilling
Increasing pressure from mining activity and variable geotechnical conditions can cause fractured ground, which if not supported, may lead to incidents of rock fall or roof collapse.
Learn more about cavity filling
High volume grouts
2. Ground Control
Ground control is fundamental to the integrity and safety of underground mining operations. Rock reinforcement methods vary and include point anchored bolts, friction bolts and grouted bolts. Minova offer multiple solutions for a wide range of bolts.
Not all resin bolts are the same.
Read our comparative information bulletin
3. Water control
Water ingress into an underground mine can represent a major risk if not recognised and rectified.
Learn more about our range of Injection Chemicals
4. Ore Recovery Optimisation
Many hard rock mines have sterilised rich ore left behind in vertical and horizontal pillars. With the placement of backfill adjacent to these resources, our solutions support safe and optimal ore recovery operations.
Contact Minova to find out how we can help you.
Minova solution
Read Round Oak Case Study
Innovative mining.
optimised ore recovery.
optimised ore recovery
Many hard rock mines have ore rich reserves, contained in unmined area's, commonly referred to as sterilised ore.
Some causes of sterilised ore could be dry filled stopes, unfilled stopes, narrow unstable pillars and low grade pillars. Basically the inability to access valuable ore deposits for removal.
Through unique and well proven methodologies pioneered by Minova our solutions can maximise the extraction of previously sterilised ore resources that support
- Increased revenue from extraction of additional mineral resources
- Cost effective usage of R.O.M waste rock material
- Providing structural elements of a known strength for mine life extension
- Improved management of HSE risk
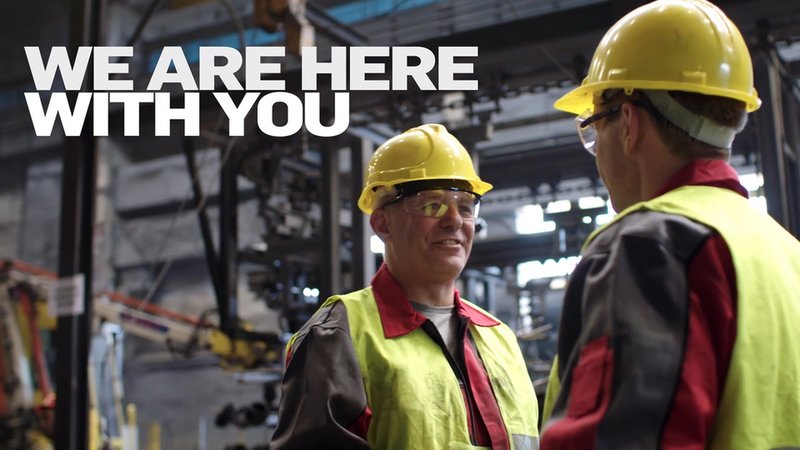
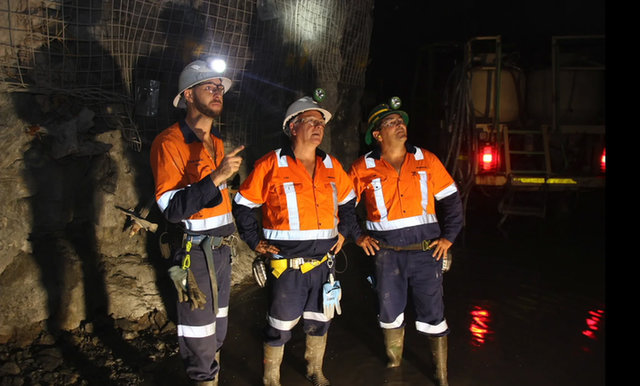
Who we have helped:
Round Oak Minerals
Newcrest Mining
Castlemaine Goldfields
Newmont
Phase 1: Pre-work
Learn more about the pre-work required. See how we can help you!
Phase 2: Application
Learn more about the pre-work required. See how we can help you!
Case Study
Read the Round Oak Case Study
Conference Paper
Read the abstract "Optimising the Recovery of Stopes at Bentley Mine"
Brochure
Download our brochure
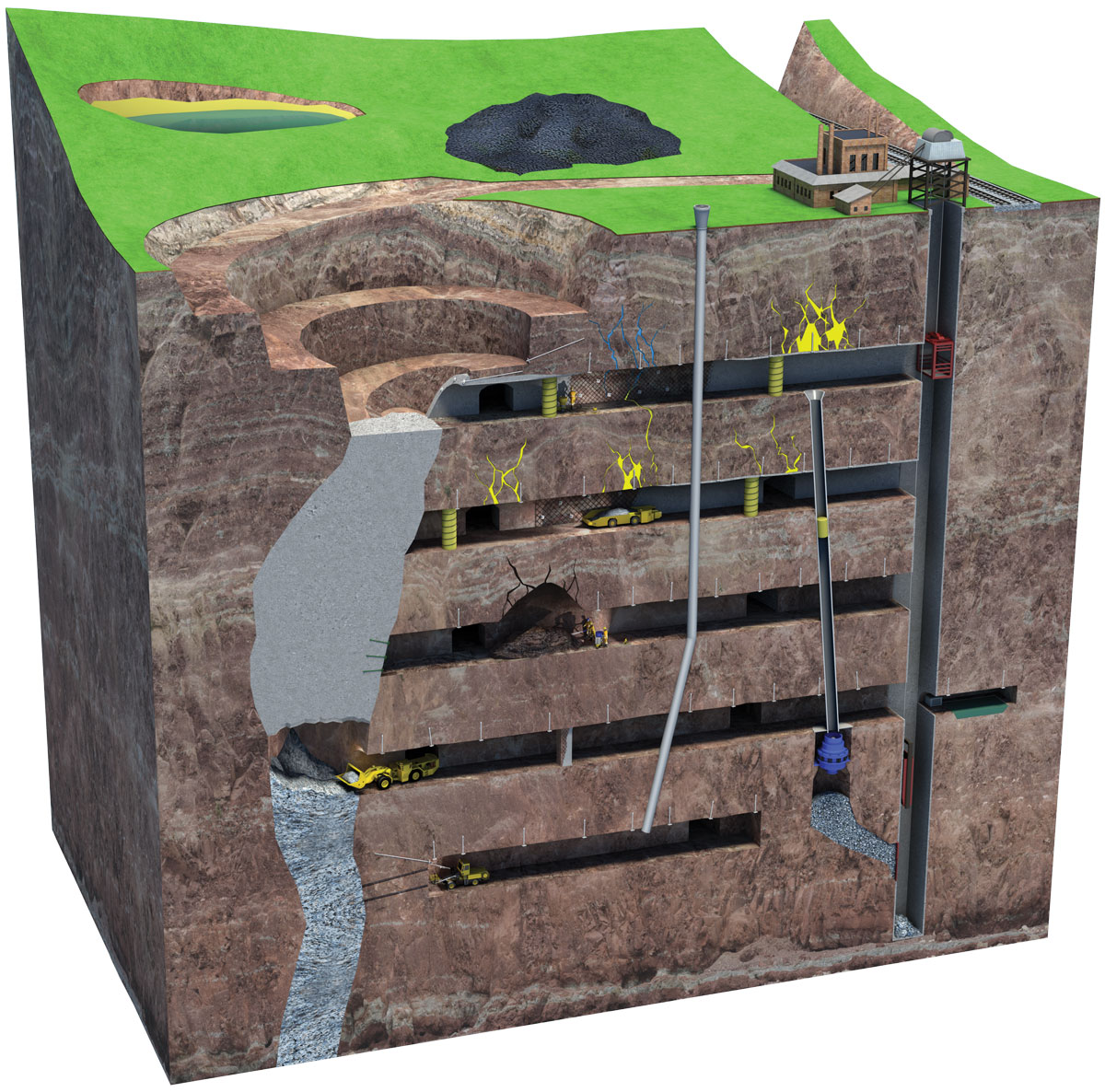
Click on the icons
1
2
3
4
1. Cavity & Backfilling
Increasing pressure from mining activity and variable geotechnical conditions can cause fractured ground, which if not supported, may lead to incidents of rock fall or roof collapse.
Learn more about cavity filling
High volume grouts
2. Ground Control
Ground control is fundamental to the integrity and safety of underground mining operations. Rock reinforcement methods vary and include point anchored bolts, friction bolts and grouted bolts. Minova offer multiple solutions for a wide range of bolts.
Not all resin bolts are the same.
Read our comparative information bulletin
3. Water control
Water ingress into an underground mine can represent a major risk if not recognised and rectified.
Learn more about our range of Injection Chemicals
4. Ore Recovery Optimisation
Many hard rock mines have sterilised rich ore left behind in vertical and horizontal pillars. With the placement of backfill adjacent to these resources, our solutions support safe and optimal ore recovery operations.
Contact Minova to find out how we can help you.
Minova solution
Read Round Oak Case Study
PHASE 1: Pre-Work
1. Identify the area of sterilised ore, the volume, grade and risk
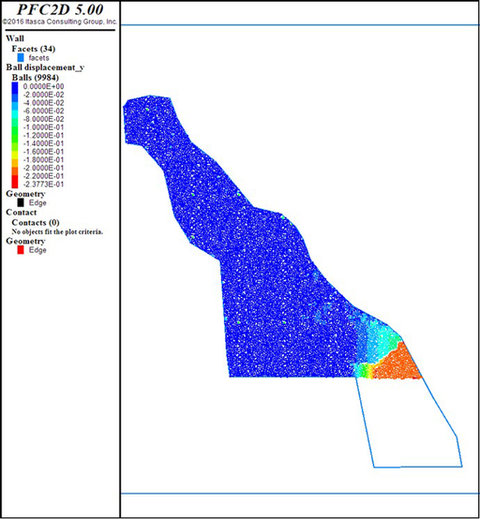
2. Numerical modelling to determine stability of surrounding area, thickness of consolidated fill required, determination of the UCS of the filler, void ratio and analysis of mine water
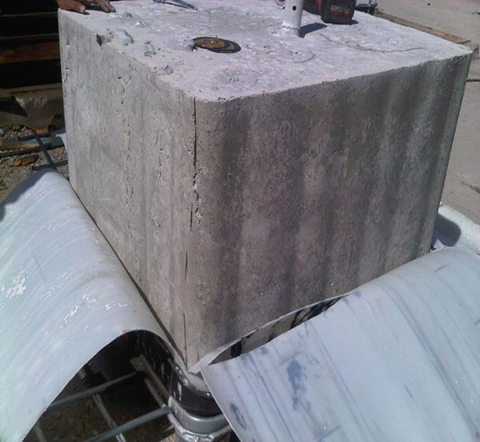
2. Numerical modelling to determine stability of surrounding area, thickness of consolidated fill required, determination of the UCS of the filler, void ratio and analysis of mine water
3. Rock In The Box Test to determine permeability of the fill
4. Site inspection
PHASE 2: Application
drilling and placement of grouting holes
setup of equipment
delivery of the stabilising grout
quality control testing
delivery of the stabilising grout
application of the grout



