Peter Dowd, professor of mining engineering. Image: University of Adelaide
Q&A | TECHNOLOGY
Inside the University of Adelaide’s A$12.5m mining research centre
The Australian government has announced A$12.5m in funding, from government reserves and industry organisations, to support a training centre at the University of Adelaide to educate miners and engineers in emerging technologies. JP Casey speaks to Peter Dowd, professor of mining engineering at the university’s School of Civil, Environmental and Mining Engineering about the funding, and how artificial intelligence and automation could impact the sector.


Peter Dowd, professor of mining engineering. Image: University of Adelaide
With artificial intelligence and automation technologies ever more in the press as the future of industry, it is perhaps easy to assume that adoption is a mere step away. However, while such technologies may offer numerous advantages to mining, those in the industry are not necessarily aware of these advantages or how to incorporate them into their systems and processes. The University of Adelaide’s new mining research is setting out to change that however, ensuring that the sector is properly prepared for emerging technologies and how they could change the future of mining.
More than half of the country’s coal mines are managed by pro-Russian separatist militia.Credit: DmyTo/Shutterstock.
JP Casey: Could you talk about the project’s aims, and how the adoption of new technology could have benefits for the mining industry?
Peter Dowd:
The training centre will deliver the enabling tools – advanced sensors, data analytics and artificial intelligence – for automated, integrated and optimised mining. Automating a mine requires all stages of the mining and processing system to be integrated so that intelligence across the value chain can be automatically generated, delivered and exploited.
The mining industry must be able to make real-time decisions if it is to apply the correct and most cost-effective parameters, or processes, at any point in the value chain and avoid the use of costly processes when they are not needed. Ubiquitous sensors, data analytics and artificial intelligence will bring step-change increases in productivity, based on network connectivity and high-speed computation in the Industrial Internet of Things.
The aim of this training centre is to demonstrate the benefits of, and deliver the tools for, integration to maximise productivity and reduce risk in the mining value chain through clever applications of integrated lean principles and, in so doing, train the next generation of scientists and engineers in the critical areas of sensors, data analytics and artificial intelligence for complex resources, a current knowledge priority for the mining industry.
Over what time frame do you expect to see these benefits realised?
The training centre will operate over the period 2020–2023. We expect significant benefits to be realised throughout the period and thereafter as the research delivers against each of the objectives and the translation partners develop the outcomes into industry-ready products and, in appropriate cases, commercialise outcomes.
You mentioned that Australia is in a “unique” position with regards to the global mining industry. Why is this?
The unique opportunity that Australia has is to master the Industrial Internet of Things in an industry – mining – in which it has the competitive advantages of the value and complexity of its mineral resources and of the high-level capability embedded in its mining equipment, technology and services and in its resource companies.
There is increasing pressure on mining operations to improve their performance with regards to health and safety and environmental footprint. Do you think these new technologies could improve either of these areas?
Definitely. The use of embedded and connected sensors together with real-time analysis of sensed data can be applied to safety, environmental monitoring and control and many other areas in mining operations.
The project is partially funded by the national government and research and industry organisations; how important was this funding to the project, and could it set a precedent for future industrial innovations?
The funding was critical for the project and, without it, the project could not be undertaken. The collaborative approach is a fundamental requirement for the award of this type of research grant. The Australian Research Council Industrial Transformation Training Centres scheme fosters close partnerships between university-based researchers and other research end-users to provide innovative PhD and post-doctoral training, for end-user focused research industries that are vital to Australia's future.
The project includes three universities (the University of Adelaide, the University of South Australia and Curtin University), two partner mining companies (BHP and Oz Minerals), 16 translation partner companies and five other organisations (participants that are not required to make cash or in-kind contributions). The partner organisations and the universities are required to make cash and/or in-kind contributions.
Are there any similar projects planned to build on the work of the training centre?
There is another complementary project, Unlocking Complex Resources through Lean Processing, which started last year. This is a research consortium funded by the State of South Australia through the Premier’s Research and Industry Fund (PRIF) Research Consortia Programme for the period 2018–2021. The total project award is A$4m from PRIF, A$6.14m from industry, [and] A$4.46m from university partners.
The project includes two research partners (the University of Adelaide and the University of South Australia), two end-user mining partners (BHP and Oz Minerals), 13 translation partner companies and four other organisations. The consortium will develop advanced technology to tailor the mining and processing options to specific characteristics of the mineral ore in real-time, an approach known as lean processing. The project takes an integrated systems approach to optimise the entire value chain from the in-situ resource to mining and processing, rather than individually optimising the components of the extraction system.
“Queensland’s resources sector provides one in every five dollars in the Queensland economy, sustains one in eight Queensland jobs, and supports more than 15,400 businesses and community organisations.”
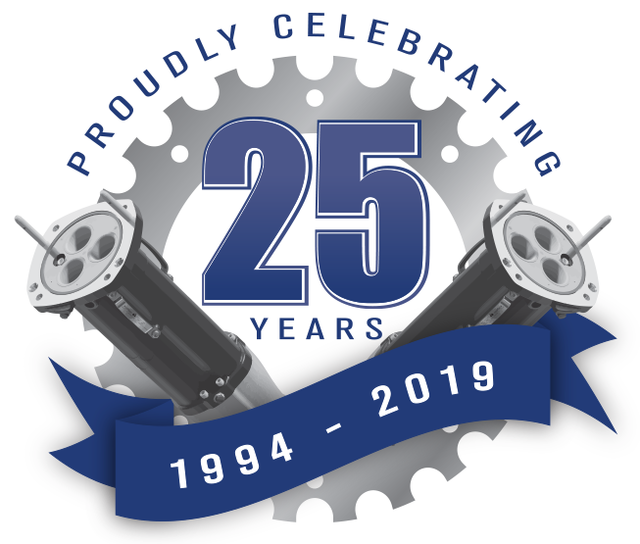
AusProof is celebrating 25 years of business in Australia in 2019.