BEVs expected to have the biggest impact on reducing emissions from mining operations
With leading mining companies pledging to significantly reduce greenhouse gas emissions and many targeting carbon neutrality by 2050, a switch from diesel-fuelled vehicles to battery-powered will be a critical step.
Many miners are already exploring the potential to electrify their mining fleets. This is particularly the case for underground mines, where tethered or battery-powered load, haul, dump vehicles (LHDs) are becoming more common. Not only do they reduce greenhouse gases, they can significantly reduce ventilation costs.
This reduction comes in a number of ways, including the elimination of diesel particulate matter and exhaust gases. Also, higher efficiency in the conversion from electric energy to wheel drives compared with diesel to wheel drives leads to less heat and therefore a lower ventilation requirement.
Other benefits include maintenance costs, with battery vehicles having 25% fewer parts compared with diesel propulsion systems, and less noise, vibration, and heat.
Majors adopt battery-electric vehicles
The use of battery-electric vehicles (BEVs) has been pioneered by companies such as Newmont, Kirkland Lake Gold, and Boliden, with majors such as Rio Tinto, BHP, and Vale all working towards larger fleets of electric vehicles.
In introducing BEVs at its Macassa Mine from 2013, Kirkland Lake Gold was an early-mover, supporting a reduction in greenhouse gas emissions at the mine of approximately 2,400t CO₂ equivalent/year compared to the use of only diesel equipment.
By 2019 the mine had extended its fleet to 24 battery-powered LHDs and nine haul trucks, with 80% of ore production at the mine being carried out by battery-electric machines.
The company has also introduced battery-powered equipment at its Taylor mine.
Newmont’s Borden gold mine in Canada, which began commercial production in late 2019, was the world’s first all-electric underground gold mine.
The switch eliminated 50% of the total greenhouse gas emissions on-site, or 5,000t of CO₂ per year, as well as saving 33,000MWh per year in electricity due to the need for 50% less ventilation than a baseline diesel underground mine.
More recently, on 5 May 2021, Ivanhoe Mines announced its upcoming Kamoa-Kakula mine would become the first net-zero carbon emitter among the top-tier copper mines through electrification of the mining fleet, either via electric batteries or hydrogen fuel cells.
The underground mine is due to begin production in June 2021, though a target date has not been indicated for achieving net-zero carbon emissions.
For BHP, emissions from fuel and distillate make up 42% of their operational emissions, with much of this from mobile equipment such as haul trucks.
In order to move towards net-zero diesel emissions, the company is adapting its fleet and has been trialling the use of light electric vehicles (LEVs) at various sites, including the Olympic Dam mine, converting diesel vehicles to run on lithium-ion batteries.
It has also been conducting trials of LEVs across mines in Queensland and Western Australia, the latest announcement in January 2021 being a trial with Toyota for an LEV at its Nickel West operations in Western Australia.
Developing battery-powered mining vehicles
For surface mines, the use of electric-powered mining trucks has been relatively limited. The sector has historically focused on the use of trolley-assist trucks, which are diesel-electric drive haul trucks that receive the power to run the wheel motors from catenary/overhead electric wire lines constructed on specified routes.
When running on external electricity they produce more power compared to a generator coupled with a diesel engine, which results in higher truck speeds. This means increased productivity per machine, lower fuel consumption, and increased engine life.
However, there have been recent developments in creating battery-powered mining vehicles. An early model was the Elektro Dumper, or eDumper, a 63-ton payload electric dump truck modelled on a Komatsu HB 605-7 and used at a quarry in Switzerland.
It has a regenerative braking system that recaptures the energy created by going downhill, refilling the battery’s charge for the next time the truck travels uphill.
In mid-2020, it was reported that BELAZ is developing a 90-ton class all-battery truck based on its 7558 base model.
In November 2020, it was announced that Nouveau Monde Graphite had been selected to join a consortium of companies in Canada, including Propulsion Québec, the Innovative Vehicle Institute, National Research Council of Canada, Adria Power Systems, Danat TM4, and Fournier & Fils, to work on a 40 ton electric-powered truck and fast-charging infrastructure.
More recently, in March 2021, Fortescue Metals Group signed an agreement with Williams Advanced Engineering (WAE) to build a zero-emission battery-electric haul truck for mining operations. The partners will design, build, and test a battery system, which will have the ability to regenerate power as the truck travels downhill.
The battery will be built at WAE’s facility in Grove, Oxfordshire, UK, and then shipped to Perth for integration into a 240 ton prototype haul truck. It will then be tested at Fortescue’s mining operations in the Pilbara, Western Australia.
Battery-powered vehicles’ impact on emissions
In a poll by Mining Technology between March and May 2021, 30% of the 496 respondents felt that the use of battery-powered vehicles would have the greatest impact on reducing emissions from mining operations over the next five years. This is compared with 16% expecting the greatest impact to come from hydrogen-powered vehicles and 21% from use of on-site renewable energy.
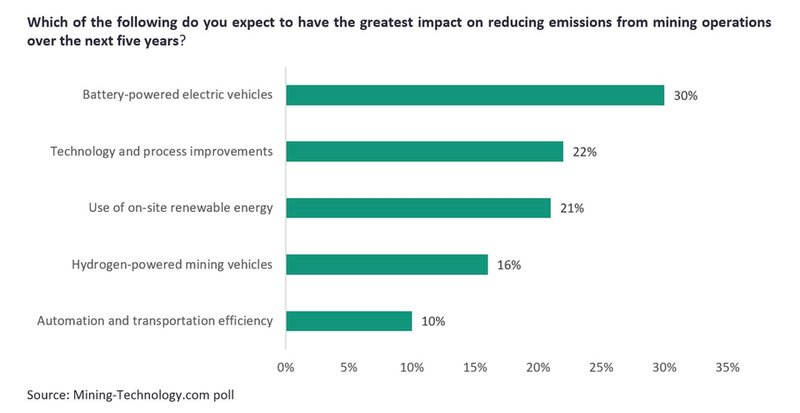
With regards to hydrogen, Anglo American is working with Engie to develop a hydrogen-based haul system, integrating hydrogen fuel cells and batteries into surface mining trucks.
Both the fuel cell and battery would be required to power the truck when it has a full payload and travelling uphill, otherwise the fuel cell can be used to propel the vehicle and charge the battery, and when going downhill the battery can be recharged.
Testing is being carried out at the Mogalakwena mine, where the company is installing photovoltaic solar panels to power electrolysers for hydrogen production (the electrolyser splits water into hydrogen and oxygen using electrical energy, generating hydrogen to fuel the truck).
Anglo American estimates that eliminating diesel consumption at its mines will reduce its greenhouse gas emissions by up to 14%.
Market Insight From