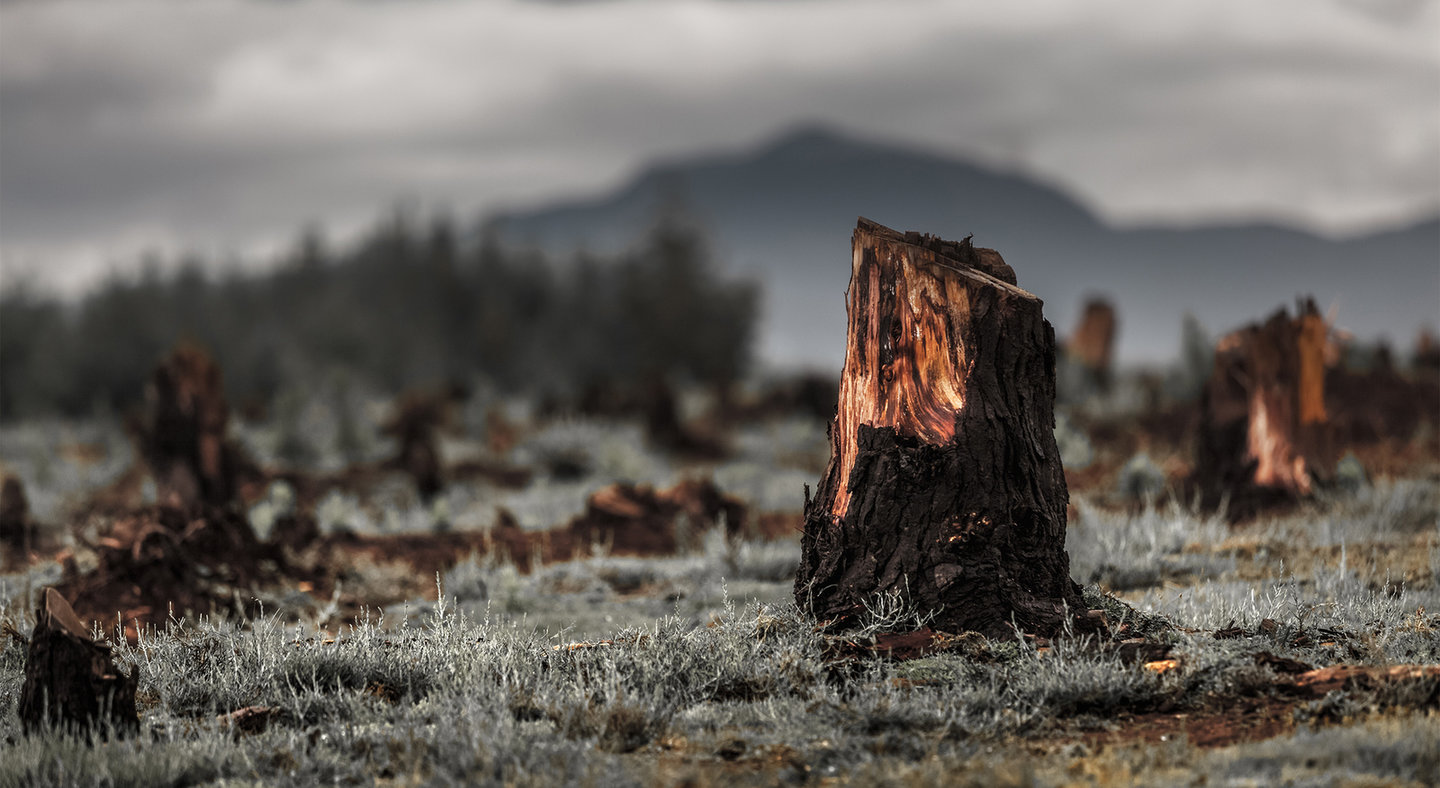
ENVIRONMENT
Mining and deforestation: the unheeded industry challenge?
Since 2014, the New York Declaration on Forests has aimed to do for deforestation what the Paris Agreement has since done for climate change. More than 200 endorsers aim to stop mining and other industries from damaging forests, jungles, and biodiversity. But in this time, the situation has only worsened. Matt Farmer asks: what more can miners do to stop deforestation?
T
he people behind the New York Declaration on Forests (NYDF) have kept an eye on global man-made deforestation. The declaration aimed to halve deforestation by 2020, and now aims to eliminate it by 2030. Most deforestation comes from agriculture, but the declaration’s third goal aims to protect forests from mining and other industries.
An analysis by the World Bank suggests that 44% of all operational mines lie in forests. This represents 1,539 mines, with another 1,826 in development or currently inactive. Mining activities have driven 7% of deforestation, according to a 2012 assessment.
A 2020 update by NYDF says extraction companies are “increasingly recognising their forest impacts”. However, report author Erin Matson told us: “This increase is unfortunately starting from a very low baseline, so the attention paid to deforestation by mining companies is not nearly sufficient yet.”
The report continues: “It is clear that important targets set by the declaration for this year have been missed. The outlook is also grim: forest loss has increased rather than halved since 2014, and success stories are a rare exception.
“Without dramatic shifts in economic development strategies - away from a reliance on extraction, exploitation, and consumption, and toward alternative pathways which value forests and people - the world will not meet its ambitious goals for sustainable development, climate, and forests.”
Where are the current deforestation problems in mining?
When picturing mining in forests, your first thought will likely go straight to the area with biggest issues. Brazil stands out as having many large-scale, pollution-intensive mines in its enormous tropical forest. While mines in Latin America generally see less impact on their forests than in Asia and Africa, Brazil stands out as an exception.
Destruction of the Amazon rainforest has sped up in recent years, as Brazilian President Jair Bolsonaro dismantles environmental protections. He has cut environmental protections, saying the Amazon “belongs to Brazil, not to the world”. This has allowed companies to move into previously inaccessible areas, and the pandemic seems likely to accelerate this.
Measures to mitigate negative impacts on forests, and people dependent on them, are often lukewarm at best.
The NYDF report states: “Measures to mitigate negative impacts on forests, and people dependent on them, are often lukewarm at best. Policies and institutions set up to protect lands and communities from environmental harms have been weakened in many forest countries, especially under cover of the Covid-19 crisis.”
Despite Brazil’s reliance on mining, the Covid-19 pandemic has fuelled backlash against the industry. The #MinersOutCovidOut campaign has petitioned the Brazilian government to expel illegal miners. Using legitimate mining infrastructure, “artisanal miners” have brought the pandemic into their otherwise isolated communities.
The disproportionate impact of “artisanal” mining on forests
Artisanal mining relies on its ability to meet demand without engaging with regulations. While ethical regulations focus on the supply side, Matson told a recent panel that: “Demand for minerals produced in forests continues to rise and the countries that consume these commodities have so far taken few steps to limit the impact of that demand.”
A 2012 study by consultancy Levin Sources and WWF found that illegal artisanal mines operate in more than two-thirds of protected forests. Since then, artisanal mining has almost doubled in scale.
Demand for minerals produced in forests continues to rise.
However, smaller mines generally cause less direct deforestation. Instead, these cause pollution to surrounding areas, degrading ecosystems and damaging biodiversity. One scientific paper found that artisanal mines often poison waterways with mercury, in turn killing trees and animals that rely on them. Another says that artisanal mines caused the loss of 100,000 hectares of forests between 1984 and 2017.
A 2016 Levin Sources study found that artisanal alluvial diamond mining disturbed 100 times more land per carat than industrial kimberlite mining. While places such as Ghana have used small-scale mining to encourage economic development, the lack of oversight leads to a disproportionate impact on the surrounding environment.

Mining in forests, and the consequences beyond the lease
Some minerals cause more issues than others. More than 60% of nickel, titanium, and aluminium mines lie in forested areas. However, gold, iron, and copper extraction bring the greatest volume of mining into forests.
The NYDF report urges miners to consider their impacts beyond just the site of the mine. For instance, exploration access roads cause direct logging, but also allow easier access deeper into forests. This increases access for rural communities, but also allows destructive agricultural practices, which are the leading cause of deforestation.
While this may seem tangential, a 2017 study in scientific journal Nature found that deforestation around mining leases was 12 times more prevalent than within them. This comes from development of airstrips, staff housing, and other developments directly stemming from projects. Examining mining leases in the Amazon, the study found that mining projects noticeably increased deforestation for 70km around them.
Biodiversity is declining at unprecedented rates.
Miners cannot control “slash and burn” agriculture, but political leaders can. As such, the NYDF report authors suggest approaching environmental issues from a broader perspective.
In remote forested areas, mining can lead to game hunting and monocultural farming. Along with deforestation, this in turn leads to poor biodiversity. As a result of practices like these, the International Council of Mining and Metals (ICMM) set up standards to encourage best practice.
ICMM COO Aidan Davy told us: “Biodiversity is declining at unprecedented rates, so a more strategic approach is required. We should question current practices relating to the allocation of concessions and licences within forest areas and call on governments to prohibit all development - including forestry, agribusiness, or infrastructure activity - in forest areas of greatest conservation value, coupled with stronger protective measures.”
// Main image: 3D System Model and Completed Installation. Credit: Deimos
What questions should mining companies ask to decrease their impact on forests?
NYDF report author Matson told us: “Comprehensive Environmental and Social Impact Assessments should be standard before exploration begins in any new site.
"The assessments need to cover not just the expected environmental impacts within the direct footprint of the mine site, but also the indirect impacts of access infrastructure. Then, the company can apply a mitigation hierarchy to address these impacts.”
In some ways, mitigation hierarchies act similar to a risk assessment. They encourage companies to eliminate unnecessary impacts at the planning stage, and to take remedial measures for unavoidable effects. The report emphasises: “Restoration and offsetting options should only be used as a last resort.”
Both Levin and the NYDF report also support industry bodies making and enforcing practice guidelines. ICMM’s Davy continued: “We need mining and metals companies across the industry to commit to higher standards of performance on biodiversity, and other environmental, social, and governance areas, which is the purpose of ICMM’s Mining Principles.
“These principles require our members to neither explore nor develop new mines in World Heritage sites, respect legally designated protected areas, and ensure that any new operations or changes to existing operations are compatible with the value for which such areas were designated.
We need mining and metals companies across the industry to commit to higher standards of performance on biodiversity.
”They also require companies to assess and address risks and impacts to biodiversity and ecosystem services by implementing the mitigation hierarchy, with the ambition of achieving no net loss to biodiversity.”
Matson continues: “The uptake of standards like these has been quite small and slow compared to the size of the sector. Separately, many sector-wide principles that aim to mainstream sustainable mining practices do not make specific mention of forests, so this is not just a gap at the individual company level.”
“The most important step toward solving this problem is recognising it and understanding its scale. For this, we need to drastically increase transparency around the impacts, sustainability commitments, and actions of companies.
“Companies need to measure and publicly report their forest impacts, adopting commitments and targets to reduce the impacts, and disclosing progress toward these targets on a regular basis. In 2019, CDP introduced a mining-specific module in their forests questionnaire for mining companies to disclose against, which would be a good place to start for any company interested in being part of the solution.”
// Main image: 3D System Model and Completed Installation. Credit: Deimos